Experiencing chatter in machining operations can be a major headache, causing extra time and cost to manufacturers.
Do you want to know how to prevent this issue?
It's time to gain an understanding of chatter in machining and find effective ways to reduce or avoid it.
In this guide, we discuss the causes of chatter in machining and recommend strategies for avoiding or reducing it. We also discuss best practices for setup and operation that should be followed to reduce the risk of chatter during any machining operation.
With this information, you will be better equipped to optimize your machine setups and ensure fast cycle times and high-quality parts with every operation.
What is Chatter in Machining?
The chatter in machining is a type of vibration or oscillation that normally occurs in milling, drilling or grinding operations. Machinists usually refer to chatter as "sensitive cutting" or “resonance." when it occurs, the machines produce a high-pitched wailing sound, and the chip strips generated from the tool are thick and unstable.
Chatter can result in poor surface finish, uneven cutting depths, and even nicked tooling. In severe cases, it can cause catastrophic failure of the machine itself.
Chatter is caused by an imbalance between the cutting forces pushing on the workpiece and the moments created by cutting forces measured at equal distances.
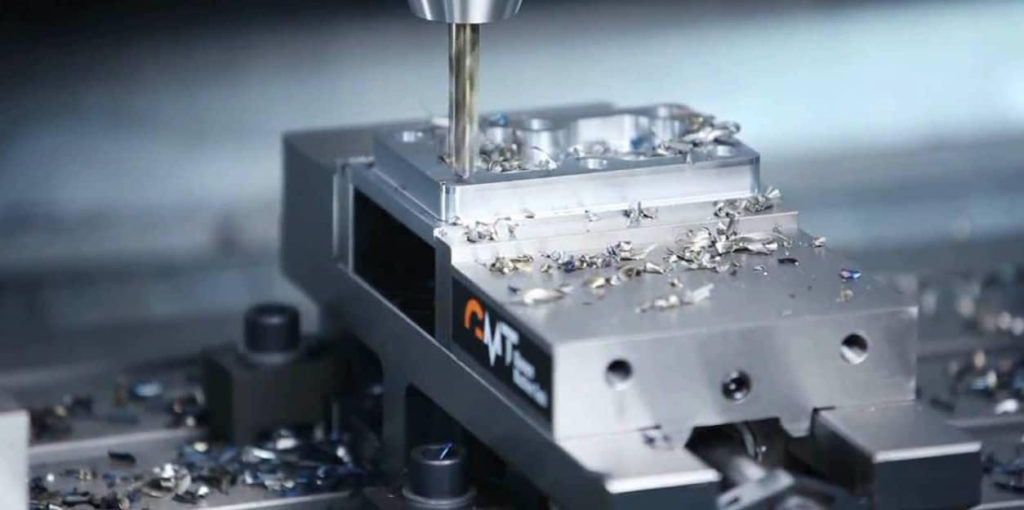
The energy created by this imbalance duplicates itself on a regular basis causing resonance waves that vibrate between those two points of inertia, resulting in a forced harmonic oscillation known as chatter.
The speed and intensity of this vibration depend on many factors, such as the type of material being machined, speed feed rate, degree of machine stiffness, and the compliance of the cutting tool used for manufacturing operations.
It is important for machinists to understand how to identify potential causes for chatter and how to mitigate it before catastrophic failure can occur.
Here are some common solutions often used to reduce or eliminate chatter in milling and drilling:
- Adjusting spindle RPMs
- Optimizing operating parameters
- Use sturdier setups with beefier tooling, such as stronger spindles on rigid frames
- Increasing the depth of cut or chip load
- Balancing cutting tools prior to installation
- Lubricating all moving parts appropriate for materials being machined
Types Of Chatter In Machining
In CNC machining, there are primarily two forms of chatter that you could experience. Some of them are as follows:
Tool Chatter
Typically, vibration occurs during cutting operations using CNC milling cutters. They start trimming, and as the vibration is transferred to the workpiece, they add different features. Because of this, the instrument and the workpiece start to slip against each other, which makes the chatter louder.
Workpiece Chatter
If you put the piece of work on the milling machine's worktable in the wrong way, it can sometimes cause offsets and vibrations. As a result, the thin wall of the workpiece may start to shake as it moves to the cutting tool.
It's important to keep in mind that some chatter is often hard to avoid. The surface of your workpiece could get scratched if the vibration while milling is more than 100µm. However, if you care about the quality of your output, you should probably think about doing something about the chatter between the tool and the workpiece.
Below, we'll go through some strategies for reducing chatter.
Causes of Chatter in Machining
The chatter in machining is a type of vibration that occurs during metal cutting operations, resulting in a poor surface finish and reduced tool life. While chatter can be difficult to detect because it’s unpredictable and very brief in duration, the right analysis and prevention techniques can help reduce or even eliminate it.
Chatter is generally caused by instability in the cutting process. This can arise from various factors, including tool wear or deflection from high feed rates or cutting forces, an imbalanced cutting edge or tooth form due to improper grinding angles or unequal flute length, insufficient coolant flow, incorrect workpiece clamping techniques, inadequate machine rigidity, and non-symmetrical material grinding conditions.

The tool’s chatter can further be affected by its rake angle, nose radius, and relief angle, as well as the composition of the workpiece material. Tool wear can also be a contributing factor to chatter and should not be ignored for too long since it violates the condition of stable machining operations.
If machining conditions remain unchanged for a long time after the first use of a new tool, then chatter may occur due to excessive wear on the tool’s surface that now has an unbalanced cutting edge or tooth form relative to before initial use.
It is therefore important to regularly check tools while they are being used and check them against accepted tolerances as outlined in various machining standards instructions, such as ISO 13399 Level 1A tool designation shape code guidelines.
Properly maintaining tooling is essential for avoiding false indications caused by changes in geometry overtime on the cutting edge that could otherwise lead to excess vibrations during machining operations, which may result in chatter occurring with each cut made on the workpiece material being processed.
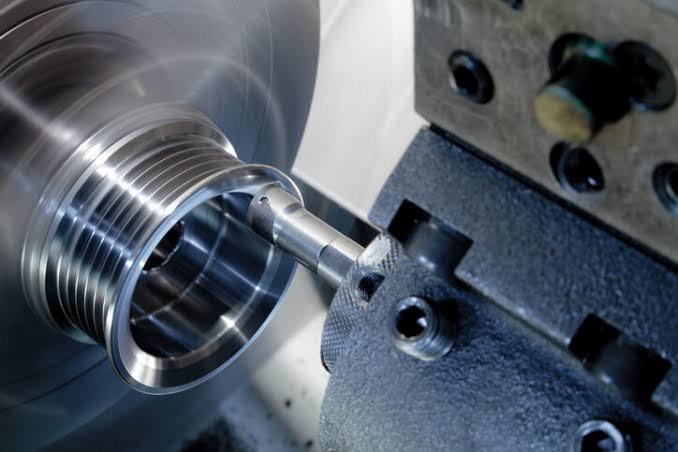
Effects of Chatter on Machining
Chatter is an undesirable and sometimes dangerous occurrence in machining which can result in an inferior surface finish, workpiece rejection, tool breakage, and increased machine noise. So what exactly is chatter, what causes it, and what can be done to eliminate it?
Chatter is an oscillation of the cutting tool across the material surface that results from various problem areas within the machining process. It occurs because of the dynamic nature of cutting forces acting on the tool bit, resulting from periodic interactions between the machine conditions and the geometry of the workpiece.
Common effects of chatter include:
- Misalignment between the cutting tool and workpiece.
- Poor spindle balance or disturbances to its rotation speed are caused by external factors such as air currents.
- Imperfections in the geometry of the tool, such as atypical rake angle or uniformity, can also lead to vibrations or deflection of the tool under high cutting forces.
There are several ways to reduce chatter during machining operations, which will discuss below.

Strategies to Avoid or Reduce Chatter in Machining
Chatter is a common and potentially destructive problem that can impact the machining process. Generally caused by an out-of-balance cutting tool, chatter produces an unwanted vibration in the workpiece and cutting tool during the cut. When chatter occurs, tool life and part quality can be negatively affected.
In order to reduce or eliminate chatter, several strategies may be employed, such as:
- Adjusting speed: By slowing down the spindle RPMs and decreasing the depth of cut may help to reduce chatter.
- Slowing down acceleration rates: Decreasing acceleration rates can help minimize vibrations when starting up a machining cycle and transitioning between passes on a different axis.
- Utilizing different cutting speeds or feeds: By using two different speeds or feeds on opposite sides of the tool, asynchronous motion is created, which helps to dampen out vibrations produced by other sources, such as drive motors or machine frame flexing.
- Employing balancing techniques for the tools themselves, such as gang nose RPM balancing techniques: This strategy reduces tool vibration by counteracting surface forces from unbalanced cutting tools – especially those with multiple blades in their composition.
- Considering other areas that may contribute to chatter, including collet rigidity, structural characteristics of machine components, improper angular alignment of spindles to XYZ axes, etc.: Much like findings contributing sources of machine noise in other industries (automotive manufacturing, for instance), reflecting on all aspects of the machine-tool design can often yield solutions previously unforeseen by machinists, operators and engineers alike!
- Regularly check machine alignment and ensure your spindle is effectively balanced: Inspect both spindle bearings to make sure they haven’t become overworked or prone to premature failure due to faulty lubrication or contaminant build-up.
- Additionally, pay attention to conditions outside of your workshop: Take appropriate steps towards reducing vibrations caused by harsh external temperatures, weather conditions, etc., as these can all lead to poor cutting stability on any lathe cutter or milling machine.
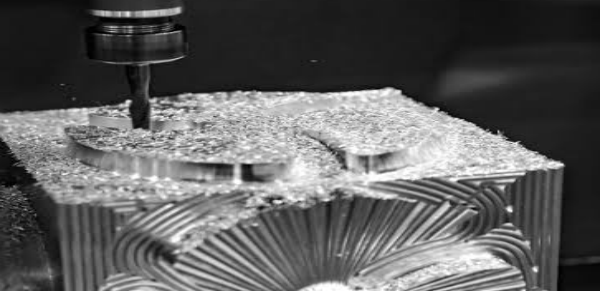
Tool Selection and Setup to Avoid or Reduce Chatter
One of the most important steps in setting up a machining operation is tool selection and setup. When it comes to reducing or eliminating chatter, the tool selection and setup can make a big difference. The cutting edge should be sharp, clean, of proper shape and size, properly hardened, and ground to suit the application.
The rake angles must be positive to ensure good chip flow. It is important to ensure that the tool has the correct helix angle if it is utilized for high-speed operations in order to have effective chip evacuation from between flutes.
Where feasible, an anti-vibration system should be adopted for dampening chatter vibrations due to the high speeds/feeds used during machining operations. Such an approach involves using “passive” vibration dampers such as molybdenum rubber instead of solid metal cutting tools or heavier materials, which are susceptible to vibrational frequencies.
Employees must also be instructed on proper machining techniques that can help reduce wheel/tool chatter while ensuring a safe work environment throughout each step of the process.
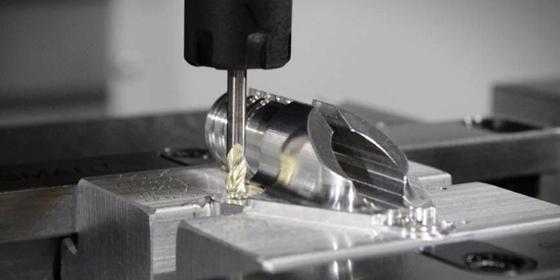
It is also important to consider machine dynamics when setting up an operation, such as mechanical tightness and looseness of machine parts, spindle movement characteristics, along with gib settings that determine moves for replacement of components or changeover between parts after completion of the machining cycle, called positioning accuracy.
In order to reduce vibrations and maintain uniformity during operations involving multiple-part processes for consistent models/prototype generation purposes.
Generally speaking, tightening screws will help in preventing excessive vibration during machining. This helps keep chatter under control; however, too much force applied may cause more harm than benefit. Thus, the correct amounts must be tested/ found with metal feeler gauges as required per workpiece dimensions before applying them directly onto spindles and other plastic bed structures within machines, respectively.
So, any form of deformation on beds doesn’t occur, causing issues while fitting into appropriate clamps and performing job roles related duties needed thereto, subsequently inducing damage to expensive metallic tool bits and the cutting geometry accordingly, leading towards unsatisfactory rejected end products created haphazardly.
The ultimate goal is to be able to:
- Create flawless parts every time with minimum downtime and lower scrap rates incurred.
- When necessary, questions come up that need to be answered quickly and per all standards and deadlines. On top of that, the question that needs to be answered quickly is customer satisfaction.
- Thus, maintaining a stellar reputation was kept proud, eventually deviating from product failure probabilities and thoroughly replacing them back.
- Also, maintaining previous benchmarked certainties carefully, frequently, and faithfully.
- Obtaining warranty coverage with assurance
- Steadily sending delectably gotten matchlessly beautifully.
- Executing the proper necessities demanded decently
- Ensuring success stories are fantastically constructed continuously.
Benefits of Avoiding or Reducing Chatter in Machining
Chatter sometimes referred to as "vibration," is an undesirable phenomenon that occurs in machining processes such as milling, drilling, and turning. It has many negative effects on the finished part, as it can cause surface finish problems due to tool deflection and lead to poor part accuracy due to chatter. Production output is also affected as productivity is reduced when chatter occurs. In extreme cases, the component may be scrapped completely due to chatter.
The benefits of reducing or avoiding chatter in machining processes are numerous. It allows for a smoother surface finish on components and improved part accuracy, resulting in more consistent product quality and greater customer satisfaction.
Additionally, it reduces tool deflection and decreases cycle times, which helps increase productivity and reduce overall costs associated with machining operations.
Further still, less wear on tools resists wear-related failure, while longer tool life yields less frequent tool replacement costs that can ultimately reduce downtime during periodic maintenance activities.
Overall, reducing or avoiding chatter in machining operations has both immediate advantages, such as improved productivity and cost savings. As such, it should be a priority for production teams striving for high-quality parts delivered at efficient cost points, which will eventually lead to higher customer satisfaction and efficiency gains across their operations.
Frequently Asked Questions (FAQs)
What are the causes of chatter in machining?
A variety of factors can contribute to chatter in machining, including the design of the tool, the cutting conditions, and the rigidity of the machine tool.
What are the consequences of chatter in machining?
The chatter that occurs during machining can have significant consequences, including a reduction in tool life, an increase in cycle time, and a reduction in component quality.
How can machine tool rigidity help prevent chatter in machining?
Chatter is less likely to occur on a machine tool with a higher degree of rigidity because it is better suited to bear the cutting forces created during the machining process.
How can cutting parameters help prevent chatter in machining?
In machining, minimizing chatter is best accomplished by adjusting cutting parameters such as feed rate, cutting speed, and depth of cut until they are optimal.
What are some active or passive vibration control techniques for reducing chatter in machining?
Modal analysis and the use of dampening materials are two examples of active and passive vibration control approaches that can be used to reduce chatter in machining. Both of these techniques can be applied either actively or passively.
How does chatter vary depending on the type of machining operation being performed? (h3)
Because the cutting rates involved in high-speed milling and turning operations are far higher than those involved in typical machining procedures, chatter can be an especially problematic aspect of these processes.
What are some best practices for avoiding or reducing chatter in machining? (h3)
Changing the cutting geometry, utilizing a machine tool with a higher degree of rigidity, optimizing the cutting parameters, and applying active or passive vibration control techniques are some of the best practices that can be used in machining to avoid or reduce chatter.
Conclusion
In summary, chatter in machining is caused by various vibrations that can occur during the cutting process and can have detrimental effects on productivity and precision. The most effective way to reduce or avoid chatter is to take steps to prevent it from occurring in the first place.
This may include:
- Selecting a sharp tool material with a low rake angle;
- Increasing tool rigidity by utilizing a more rigid tool holder and increasing spindle speed;
- Installing counterweights, dampening materials, and frequency-tuning devices along the machine tool rails
- Utilizing active control methods such as active vibration damping;
- Maintaining machine stability with proper maintenance and lubrication;
- Balancing workpiece weight with additional supports or fixtures;
- Using tools with multiple cutting edges or extended tip tools;
- Take advantage of modern CAM Software features that reduce unwanted disturbances while machining.
Adherence to these methods will result in an increase in productive time resulting from reduced vibration cutting.