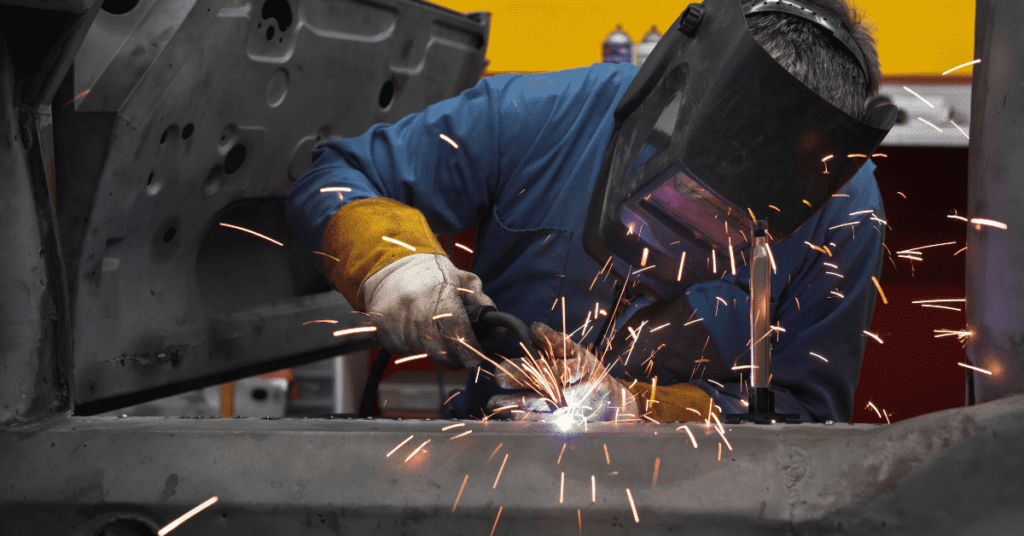
Welding is one of the most widely used mechanical processes that has existed for many years and continues to be widely used in industrial applications. There are many different types of welding, and the right one to use depends on the material's characteristics. Ductility, rigidity, temperature and wear resistance, and design structure of the workpiece are the factors that should be considered as per the project.
Further in this article, we will discuss one of the types of welding known as tack welding. So, what is tack welding? What are the appropriate materials for it? What is the strength of the welded parts? How does it work? Keep reading as we will cover all these technical aspects briefly in this article.
What is Tack Welding?
Tack welding is a pre-welding process of applying small weld beads on the workpiece throughout its length. The primary goal of tack welding is to keep the connecting components aligned for the final welding process. It facilitates welding by preventing workpieces from moving during the final welding process. Tack welding ensures that design alignments and sheet bonding distances are maintained until the final welding process.
It eliminates the use of fixtures and clamps and is ideal to be used for low-volume industrial production. The welding process creates a lot of internal stresses in sheet metals during heating and cooling. The tack welds can endure internal stresses of metal expansion and contraction during the final welding process and protect joint geometry.
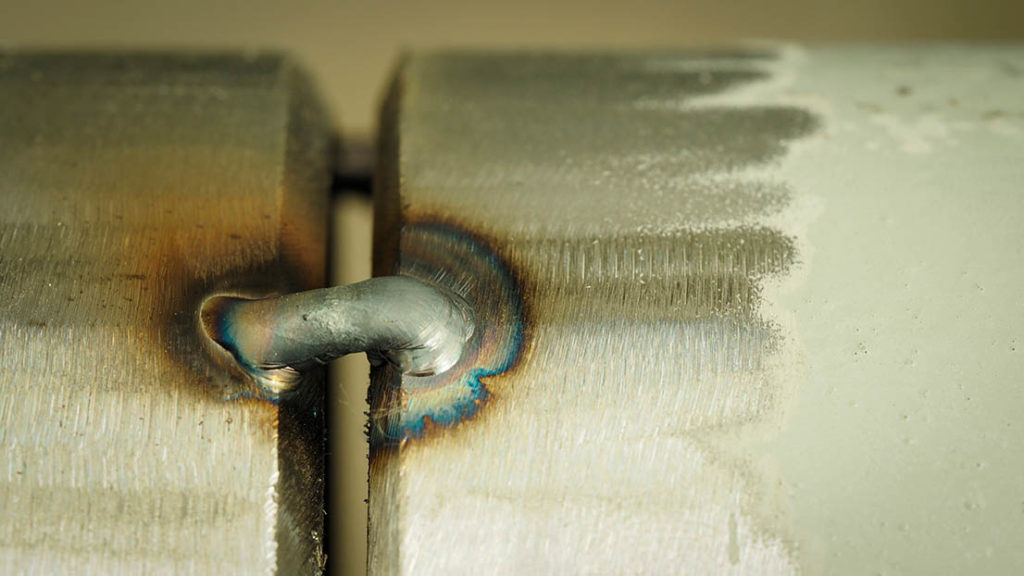
How Does Tack Welding Work?
Electrodes are used to join the sheet metals in tack welding. The working process of tack welding is similar to a simple welding process. But some technical points should be carefully observed. A high temperature and a short arc flame are recommended for tack beads. Usually, tack welds are 1/2 inches to 3/4 inches in length to keep the workpiece align. The more sensitive the material is, the smaller tack bids should be made. The tack welds are carefully applied to avoid heat distortion in sensitive materials.
The appropriate size of the tack weld is such that it perfectly incorporates the final weld. It should not large enough so that it causes discontinuity and significant stress points after the final weld.
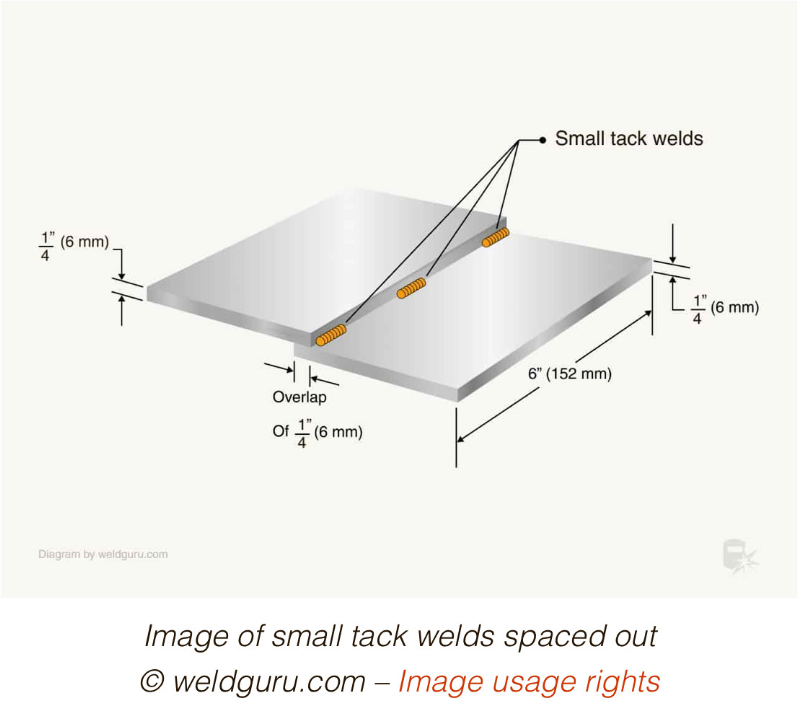
For example, a 1/2-inch-wide weld joint shouldn’t have 5/8-inch tack welds.
Materials Used in Tack Welding:
There are various types of materials used in tack welding. The ease of welding depends upon the type and thickness of the workpiece's material. The most suitable materials for tack welding are cast iron, brass, aluminum, stainless steel, titanium, and magnesium alloy.
The following technical parameters should be kept in mind before the Tack welding.
Internal stresses – the rapid heating and cooling of the material during the final weld, causes internal stress, which may break the tack weld beads and disturb the geometry.
Length of the joint – if you are welding a straight geometry, fewer tack welds are required, however for geometries like, sphere, curry, or an arc shape need a lot of tack joints.
Material thickness – Thin gauge sheets or sensitive materials require more tack welds, whereas thick sheets need fewer.
What Are the Types Of Tack Welding?
There are various types of tack writing recognized separately for the purposes and different scenarios. Following are the four most important and commonly used types of tack welding.
STANDARD TACK WELDS:
The primary purpose of Standard Tack Welds is to provide extra support to the final weld. They are intended to be consumed in the final weld. They are large enough so that they can hold the material weight and temperature effects. But not so large that they can’t match the final weld, a size balance must be maintained. For example, don’t tack ½ inch if you only need a ⅜ inch fillet weld.
This type of welding is utilized in MIG welding processes.

BRIDGE TACK WELDS:
Bridge tack welding is another generally used type of welding. Bridge tacks fill up the unnecessary gaps between the workpieces after they are tightly fit together by final welding. These unnecessary gaps are originally made due to blunders in cutting the materials.
Bridge tack welding does not penetrate the joint root. It is done by placing small tacks on each workpiece one after another so that the previous one cools in the meantime.
This type of welding is utilized in Flux-cored tacking or MIG and TIG welding processes.
HOT TACK WELDS:
Hot Tack welding is almost the same as bridge tack welding. Hot tacks fill gaps in joints between two components by depositing extra filler material and excess heat. The complete contact between two joined workpieces is necessary for which hot tacks are perfect.
The excessive heat causes contraction in the workpieces when they cool, and the gap between the components fills up. The only difference between bridge tack welding and hot tack welding is that the welder has to hit it with a sledgehammer after bridging the joint pieces.
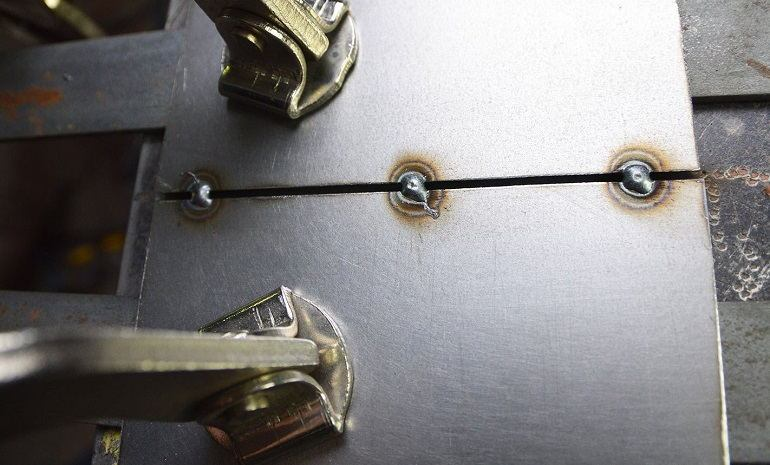
THERMIT TACK WELDS:
It is a unique type of tack welding in which different materials are mixed and a high-temperature reaction takes place. Thermit tack welding process involves the mixing of aluminum metal, iron oxide powder, and pure magnesium. The reaction occurs at a very high temperature of over 2000 degrees Celsius.
Forms of Tack Welding:
Just like various types of tack welding, there are also different forms of tack welding. Each form has a particular function to perform. There are Four common types of tacks:
- Square: used to join two parts at the right angle.
- Vertical: runs vertically from top to bottom between the workpieces.
- Right angle: tacks two workpieces perpendicularly at each other.
- The right-angle corner tacks two perpendicular workpieces making a T- shape.
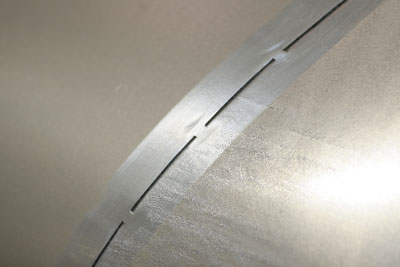
Ways to perform tack welding correctly:
It is essential to perform tack welding correctly because a minor defective tack weld can make the actual weld crack sensitive. These kinds of welds can harm people and construction as they can easily break off.
The following basic strategies are usually adopted to perform tack welding without any flaws:
- Know the direction and sequence of tack welds beforehand.
- Test the quality of the material of the metal piece with a scrapper.
- Ensure the workpieces are clean and have no debris.
- While tack welding large hem, start from the middle of workpieces and proceed toward the edges.
- Tack welding the workpieces in a sequence from one end causes shrinkage between the layers.
- Shrinkage causes the overlap between the layers and fills the gaps between workpieces.
- Give equal heat on both sides of the metal piece and use a one-second time frame.
- Do not try to move the metal until it cools completely.
PROS AND CONS OF TACK WELDING:
Tack welding also has its pros and cons like any other type of welding:
Pros of Tack Welding:
- Tack welding allows the manufacturers to examine their design before the final welding.
- It eradicates the use of fixtures such as magnets and clamps. It is beneficial to low-volume production jobs.
- Tack welds bear sufficient external and internal stresses during the final welding process and prevent distortion.
- It ensures adequate mechanical strength between the workpieces during final welding.
- Tack welding is cheap because it uses non-consumable wire rather than pricey filler materials.
- It stabilizes the joint between the workpieces without using any clamps.
- Welded components can be easily moved or separated if needed.
- As tack welds can be removed easily, they provide the manufacturers extra command over the production process. It helps them to prepare a perfect final product.
- Easy to use if you know the work well.
Cons of Tack Welding:
- It can create extra difficulty for the welder if the size of the welds is not manageable.
- It is difficult to balance a specific amount of heat on both metal pieces.
- It needs ample focus to prevent any accidental mistake in tack welding.
- Mistakenly made welds can cause damage to joint quality.
- Hot welds sometimes require a lot of filler metal to avoid slag inclusion in the gaps.
- It accelerates weld oxides accumulation in the gaps.
- Large-sized welds need to be ground which makes final welding more difficult.
- Tack welding causes quick heating and cooling that some materials unable to withstand.
- Tack welds need scrubbing after the welding process.
- Tack welds are relatively weak and have a short lifespan.
General FAQs:
Are Tack Welds strong?
Tack Welds are strong. Stronger tack welds are made using quality filler material and managing the number of tacks. Properly made tacks can endure large stresses without breakage.
Why do cracks occur in Tack welds?
The primary cause of cracking is improper welding by an inexperienced welder. Other causes of cracking include excessive heat and shrinkage during cooling.
Expert Suggestions:
Tack welding is not hard to do if you know the essential skills and have enough experience.
- Assure that the place of your tack welds and the heat input are evenly spread out and balanced. It would solve most of your tack welding problems.
- Also, ensure a balance between size and the number of tack welds.
Conclusion:
Tack welding is very advantageous to the manufacturing process, especially for maintaining quality, precision, and dimensional linearity. However, doing it wrongly may lead to massive damage. So, you always need expert engineers and a trustworthy company that ensure high quality.
Whether you need custom machining, rapid prototyping, or sheet metal fabrication work. With an advanced machining shop, modern welding facilities, and a perfect inspection process, we can provide you best quality and a smooth manufacturing experience all over the globe.
How to start? You just need to discuss your project details with our experienced staff to get a quick quote and lead time for the project.