Vacuum chambers are integral to numerous scientific, medical, and industrial applications, necessitating extremely high standards of accuracy and reliability. Proper post-processing is crucial in ensuring these standards are met by enhancing the physical and chemical properties of the chambers. This comprehensive guide explores the sophisticated post-processing steps such as cleaning, heat treatments, and surface treatments that are essential for crafting top-quality vacuum chambers.
Cleaning Processes
Initial Cleaning: Immediately after their construction, vacuum chambers contain residual particles and contaminants from the manufacturing process. Initial cleaning involves detailed manual wiping and using compressed air or vacuum systems to remove loose debris, which is critical for preventing initial contamination.
Chemical Cleaning: Following physical debris removal, chemical cleaning targets oily residues and chemicals left on the surface. Using specially formulated solvents, this step involves multiple rinses and possibly the application of aggressive agents like acids or bases, depending on the chamber material and specific contaminants involved. This ensures a pristine surface, free of potential contaminants that could degrade the vacuum's performance.
Ultrasonic Cleaning: For exceptionally high standards, particularly in chambers with intricate designs or hard-to-reach areas, ultrasonic cleaning is employed. This method utilizes high-frequency sound waves in a liquid medium to create cavitation bubbles that agitate and lift even the most stubborn contaminants from the chamber surface.
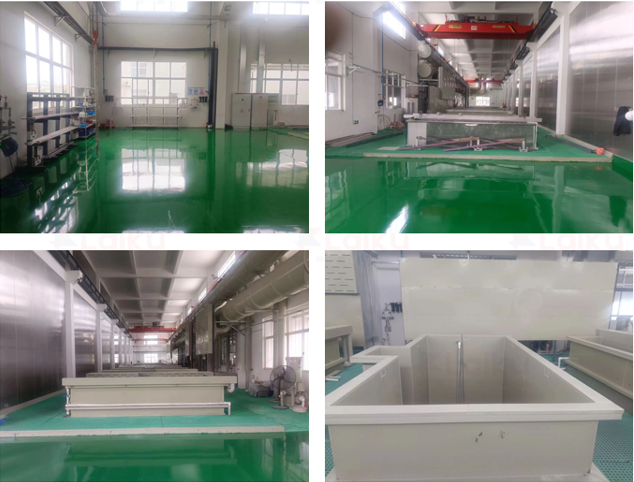
Heat Treatments and Stress Relieving
Purpose and Benefits: Residual stresses introduced during the manufacturing process can cause material deformation or failure. Heat treatments are vital for relieving these stresses and enhancing the material properties, such as toughness and ductility, which are critical for the structural integrity of vacuum chambers.
Common Techniques:
- Annealing: This process involves heating the chamber material to a specified temperature, holding it at that temperature to allow transformation, and then slowly cooling it. This reduces hardness and enhances ductility, making the material less prone to cracking.
- Tempering: Applied typically after hardening, tempering involves reheating the material to a lower temperature to decrease brittleness and increase toughness, balancing the mechanical properties for optimal performance.
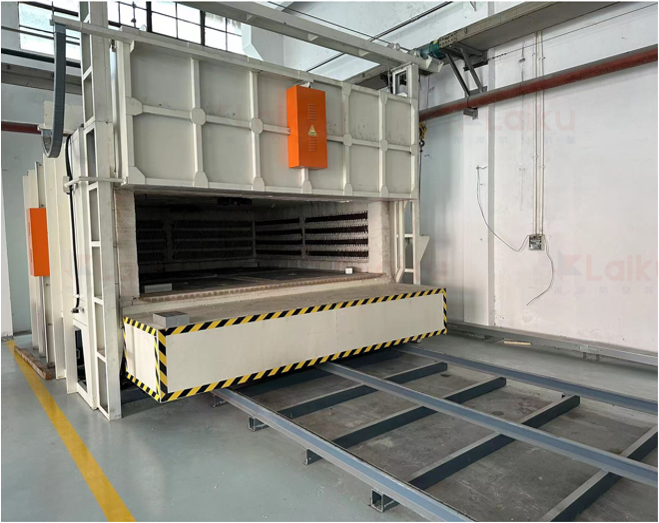
Surface Treatment Techniques
Mechanical Polishing: This process involves physically smoothing the surface of the chamber using abrasive materials. It's essential for achieving a mirror-like surface finish, reducing surface roughness, and minimizing particle adhesion which is crucial for vacuum integrity and performance.
Electropolishing: As an electrochemical process, electropolishing enhances the chemical and corrosion resistance of the surfaces. It selectively removes material from the surface, smoothing microscopic peaks and valleys, and providing a uniform, lustrous appearance.
Sandblasting: This method involves blasting the chamber surface with abrasive material under high pressure. Sandblasting not only cleans the surface but also roughens it up slightly, which can be beneficial for subsequent coating processes by providing better adhesion for coatings.
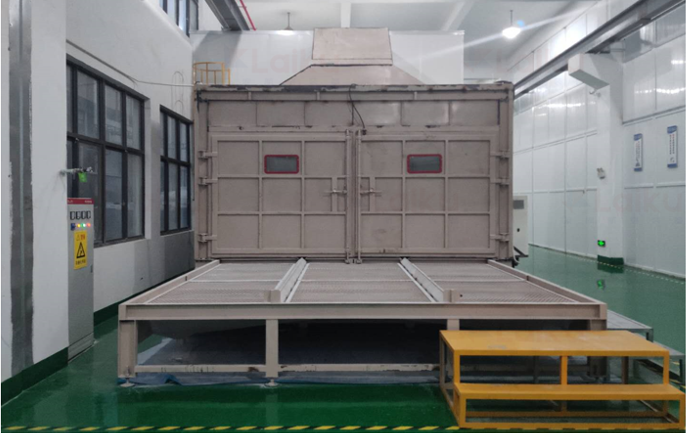
Coating Applications: Various advanced coatings, such as Physical Vapor Deposition (PVD) and Chemical Vapor Deposition (CVD), are employed to deposit thin films of materials on the chamber surfaces. These coatings serve multiple purposes: they enhance the hardness, reduce outgassing, and can significantly improve the chamber's resistance to environmental and chemical attacks.
Ensuring Compliance and Standards
Inspection and Verification: Post-processing steps are meticulously monitored and inspected using advanced measurement and testing techniques. This ensures that every chamber meets the stringent cleanliness and surface integrity standards required for high-performance vacuum applications.
Standards and Protocols: The entire post-processing sequence adheres strictly to international quality and safety standards, such as ISO and ASTM, which prescribe specific methods and criteria for evaluating the efficacy of each post-processing technique.
Case Studies
Several industrial reports and academic studies underscore the effectiveness of these post-processing techniques. For example, a study in a semiconductor production facility demonstrated that implementing a combination of ultrasonic cleaning and advanced heat treatments reduced operational downtimes and improved yield rates by enhancing vacuum performance.
Conclusion
Through detailed cleaning, precise heat treatments, and meticulous surface treatments, the post-processing of vacuum chambers ensures they meet the exacting requirements necessary for their intended applications. This not only enhances their performance but also extends their operational lifespan, thereby providing greater value and reliability for users.