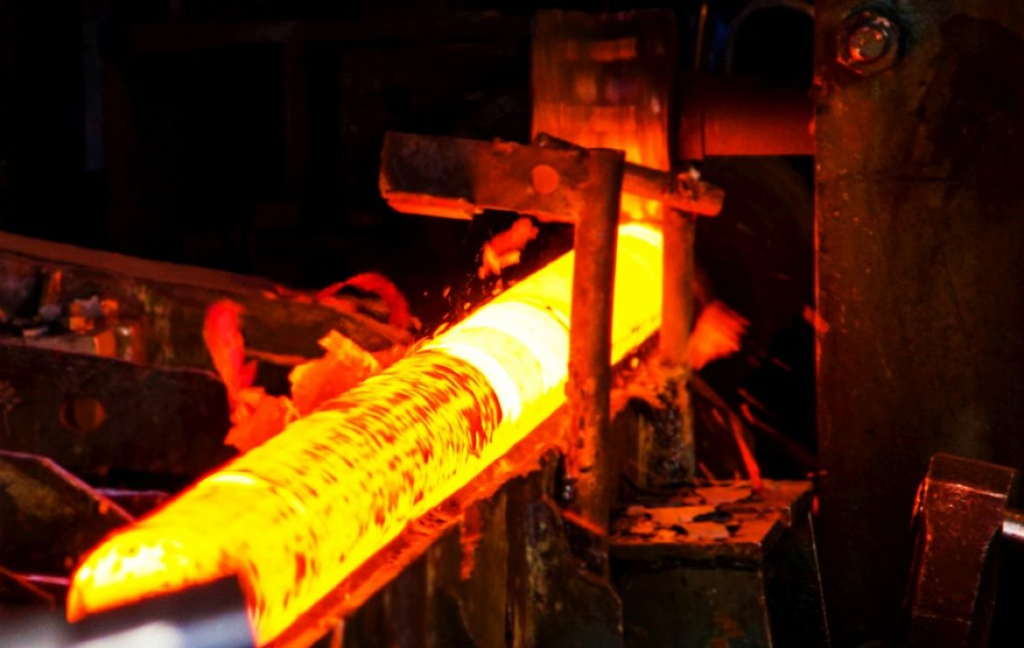
Blacksmiths employed heat to form metals for wagon components, horseshoes, and other items many years ago. The metal was immediately cooled once it was shaped into the correct shape. This frequently resulted in the metal becoming much tougher and less brittle. Heat treatment of metals is a fundamental procedure. Modern metalworking and machining methods are more precise and sophisticated than ever before.
Metals can be shaped using a variety of ways for a variety of reasons. The way metals react to precision machining is altered by heat treatment procedures. Metals can be heat treated to change a variety of characteristics. Hardness, strength, formability, elasticity, machinability, and other qualities are among them.
When these processes are rigorously followed, metals of various standards with astonishingly specific physical and chemical properties can be produced.
What is Heat Treatment?
It is, in fact, a necessary aspect of the production process. This is due to the fact that heat treatment allows a metal object to be upgraded so that it can resist more wear and tear. It is the process of heating a metal or alloy by heating and cooling it to a specific temperature.
Heat treatment can be defined as the heating and cooling of metals in general. The heat treatment method, on the other hand, is more precise. The shape of the working metal is maintained during the heating and cooling cycles.
The material's structural and physical qualities change during this process to serve the desired function. It's also possible that it's for more metalwork. Heat treatment of steel or metals is crucial in many phases of the manufacturing process.
A range of industries, including airplanes, automobiles, hardware (such as saws and axes), computers, spacecraft, the military, and the oil and gas industry, use heat treatment extensively.
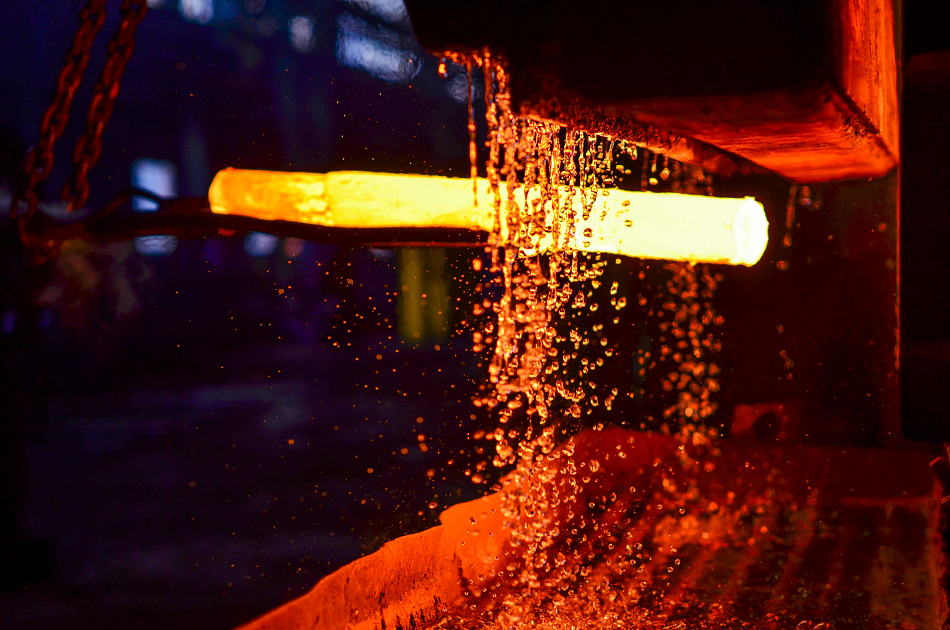
How Does It Work
The material's structural and physical qualities change during this process to serve the desired function. It's also possible that it's for more metalwork. Heat treatment of steel or metals is crucial in many phases of the manufacturing process.
It's a technique for altering the characteristics of a metal or alloy at various stages of production. Heat treatment can be used to make a material stronger, harder, more durable, or more ductile, depending on the material's requirements.
A range of industries, including airplanes, automobiles, hardware (such as saws and axes), computers, spacecraft, the military, and the oil and gas industry, use heat treatment extensively.
The metal's outcome is also influenced by the cooling process following the soak time. To ensure that the metal reaches the intended result, it might be quenched rapidly or cooled slowly in the furnace. In order to get the desired qualities in a metal or alloy, the soak temperature, soak time, cooling temperature, and cooling duration must all be combined.
What properties are changed depends on when the metal is heat-treated during the manufacturing process, and some metals may be treated multiple times.
It's difficult to figure out what temperatures to heat and cool metals at, as well as how long each step of the process should take for a certain metal or alloy. As a consequence, metallurgists (also known as material scientists) study the effects of heat on metals and alloys and provide precise instructions on how to carry out these procedures correctly. This data is used by manufacturers to guarantee that their metal components have the necessary properties at the end of the manufacturing process.
What Are The Types Of Heat Treatment?
Every heat treatment method, as previously said, involves heating and cooling. The four major heat treatment types will be discussed in this section. You'll also learn about their specific machining applications.
Hardening
Hardening is the process of heating a metal to a certain temperature. This is the temperature at which the metal's constituent constituents dissolve into the solution. The metal's crystal lattice structure may have flaws that provide a source of plasticity. Heat treatment aids in the correction of these flaws.
It accomplishes this by introducing the metal into a fine particle solution. This helps to reinforce the metal's structure. The metal is quenched as soon as possible once it has been thoroughly heated to the desired temperature. Quenching aids in the trapping of particles in the solution by the metal. In other situations, experts may add impurities to the alloy to boost its strength even more.
The goal of hardening is to increase the metal's strength. At the same time, it reduces ductility and makes the metal more brittle. As a result, tempering the metal after the hardening process will be beneficial.
Tempering
It's another heat treatment method for improving steel's tensile strength. Iron-based alloys are typically hard, although they are frequently too brittle for several uses. Tempering a metal helps to change its hardness, brittleness, and ductility. This is done to make the machining process go more smoothly.
Heating occurs at a temperature below the critical threshold in this situation. Brittleness is reduced, and hardness is maintained at lower temperatures. Hardening causes hardness, which can be reduced by tempering. You can use this method to give your metal new physical qualities. As a result, tempering should frequently occur after hardening during heat treatment.
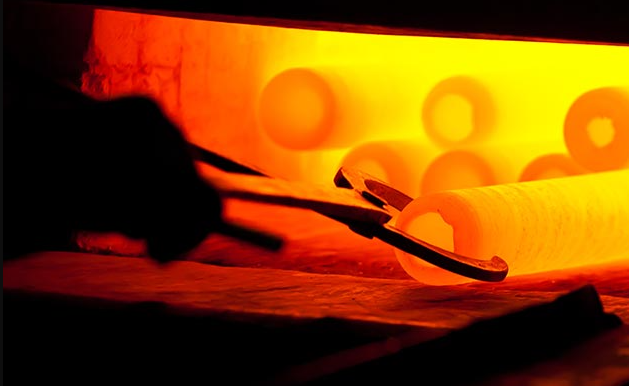
Annealing
Steel, aluminum, copper, silver, and brass are all appropriate for this technique. The metal is heated to a certain temperature during annealing. The metal is then held at that temperature for a period of time in order to convert it. After that, the air is cooled.
For silver, copper, and brass, cooling can happen slowly or quickly. However, for successful annealing, steel must be cooled gradually. Hardening is the polar opposite of annealing. It reduces the hardness of the metal while enhancing its ductility. As a result, working on the metal becomes much easier. It's also an excellent technique for repairing corroded metal. It also aids in the relief of internal stresses in metals.
Normalizing
Another type of annealing is normalizing. The metal material is heated to 200°F in this scenario, which is higher than annealing. The technician maintains the critical temperature of the metal until transformation happens. After heating, this heat treatment technique necessitates air cooling.
Austenitic grains become smaller as a result of this process. The use of air chilling aids in the refinement of ferritic grains. It serves to eliminate any internal stress in metals. Metal failure can be caused by internal tensions. As a result, normalizing the metal is critical. Hardening can then ensure that production operations are successful.
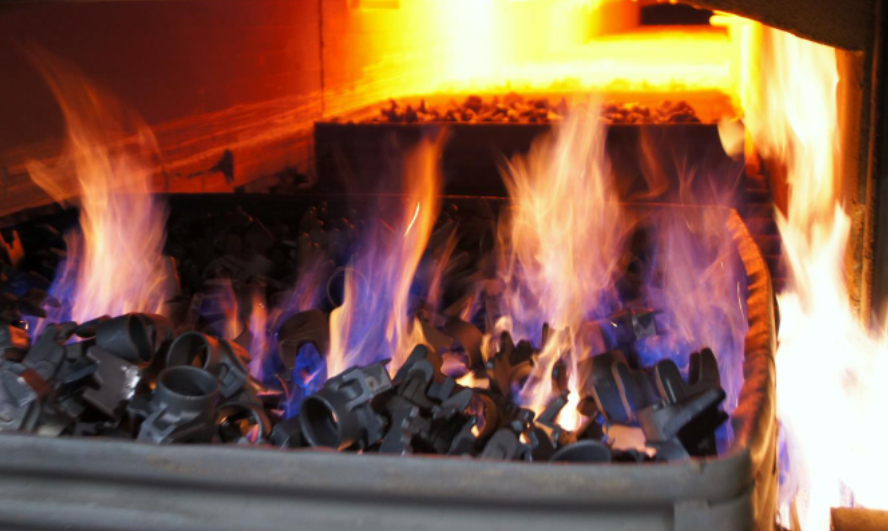
Heat Treatment Process Steps
Heat treatment is the process of heating a metal, keeping it at that temperature for a period of time, and then cooling it down. The mechanical characteristics of the metal item will vary during the process. This is because the metal's microstructure is altered by the high temperature. And a material's microstructure has a big impact on its mechanical characteristics.
Heating
The microstructure of alloys changes during heat treatment, as we've already covered. The heating is done in accordance with a predetermined thermal profile.
When heated, an alloy can exist in one of three states. It could be a mechanical mixing, a solid solution, or a hybrid of the two.
A mechanical mixture is similar to a concrete mixture in which cement is used to hold sand and gravel together. Separate particles of sand and gravel can still be seen. The base metal holds the mechanical mixture together in metal alloys.
In a solid solution, on the other hand, all of the components are homogeneously blended. This means they can't be distinguished from one another even under a microscope.
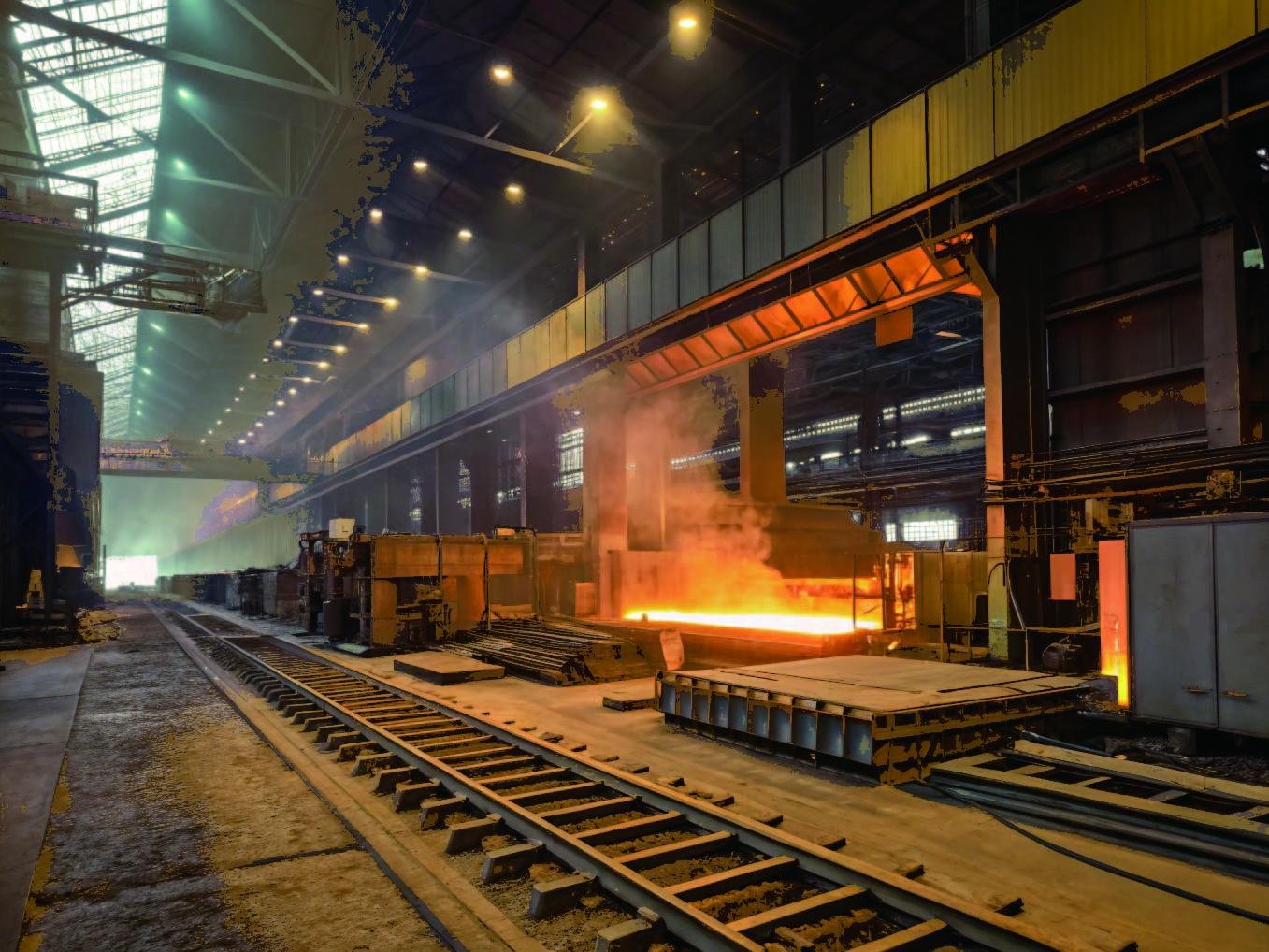
Holding
The metal is held at the desired temperature throughout the holding or soaking step. The length of time it takes is determined by the criteria.
Case hardening, for example, only necessitates structural changes to the metal's surface in order to improve surface hardness. Other approaches, on the other hand, require uniform qualities. The holding period is longer in this scenario.
The soaking time is also determined by the type of material used and the size of the component. When uniform qualities are desired, larger components require more time. The core of a large part just takes longer to achieve the requisite temperature.
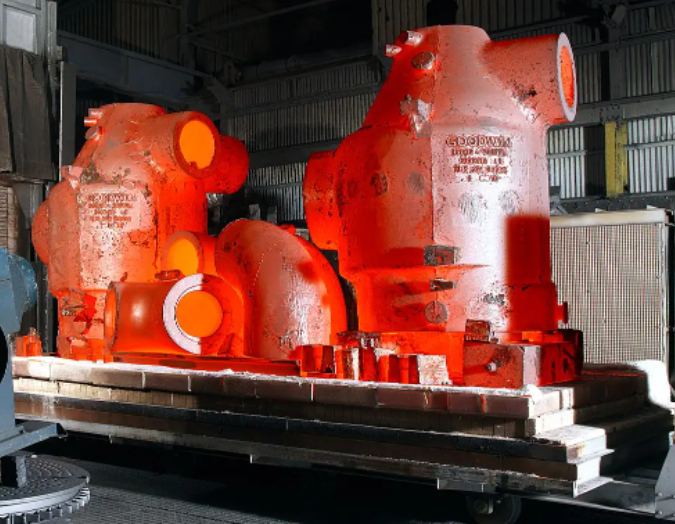
Cooling
After the soaking stage, the metal must be cooled according to the manufacturer's instructions. Structure modifications occur during this period as well. Depending on numerous conditions, a solid solution may remain the same after cooling, or it may partially or entirely transform into a mechanical mixture.
The rate of cooling is controlled by various media such as brine, water, oil, or forced air. The cooling media listed above are listed in decreasing order of effective cooling rate. Brine is the fastest in absorbing heat, whereas air is the slowest.
Furnaces can be used in the cooling process as well. When delayed cooling is required, the regulated atmosphere provides for high precision.
Benefits of Heat Treatment of Metals
There may be nothing like metal parts for gadgets and equipment without heat treatment of metals. Even if they did exist, they would not function properly. Non-ferrous metal parts, for example, would be too weak for a variety of applications.
Heat treatment is used to strengthen metals and alloys such as steel and aluminum. Many of these metals are used in airplanes, automobiles, computers, and other devices. Metals with considerable enhanced strength are used in these items. To provide proper safety and greater performance, this is necessary.
Shear strength is the most important mechanical parameter that changes following heat treatment. Tensile strength and toughness are two others. Heat-treated metals are often stronger and last longer. As a result, there will be no need to repair costly metal parts on a regular basis.
Machines run more efficiently and cost-effectively when heat-treated metal parts are used. Furthermore, even for the most demanding applications, the product will be far more efficient. Additionally, some applications may necessitate the use of exceptionally hard metals. It's possible that the applications will require sharply defined edges.
- Increases the material's ductility, making it more flexible.
- It imparts to the metal wear-resistant qualities.
- Stresses are relieved, making it easier to mill or weld the item.
- Brittleness is improved.
- Can help a metal's electrical and magnetic characteristics.
What Metals Are Suitable For Heat Treatment?
Heat treatment can be done on copper, magnesium, aluminum, nickel, brass, and titanium alloys, as well as ferrous metals.
Steels of various grades make up about 80% of heat-treated metals. Cast iron, stainless steel, and various grades of tool steel are ferrous metals that can be heat treated.
On ferrous metals, processes such as hardening, annealing, normalizing, stress relieving, case hardening, nitriding, and tempering are commonly used.
Heat treatment procedures for copper and copper alloys include annealing, aging, and quenching.
Heat treatment procedures like annealing, solution heat treating, and natural and artificial aging are all possible with aluminum. Aluminum heat treatment is a precise procedure. The scope of the process must be defined, and it must be closely monitored at each stage to ensure that the required qualities are achieved.
Conclusion
Metals can benefit from heat treatment to improve their mechanical characteristics. It can increase a metal's electrical and magnetic characteristics in addition to its physical features. This improves the part's compatibility with other materials even more.
As you've seen, there are several heat treatment procedures that can help you improve your products. However, in order to achieve the required results, you must hire the best people to work on your project. Kunshan Baichuan is a manufacturer with 25 years of experience in the machining industry, and we have the most professional team to serve you.
Obviously, not all materials are suitable for heat treatment methods. Similarly, each approach will not necessarily benefit a single material. To obtain the desired effect, each material should be studied separately. The initial point is to use phase diagrams and accessible knowledge of the effects of the aforementioned strategies.