Introduction
Aluminum is a reactive metal by nature, yet it is also a passive metal. Trachomas and holes will develop on the surface of aluminum machining processing components after sandblasting and oxidation, which will negatively impact the product's surface texture. This is a common issue in the sector, which has a significant influence on clients and significantly damages their brands and delivery schedules.
Reasons for formation of Trachoma and Holes
Cutting fluid
During the machining process, the cutting fluid has high heat dissipation and lubricating effects. Cutting fluids often include some alkaline ingredients. Occasionally, this salt-containing component will erode the aluminum's surface, producing sand holes. As a result, the cutting fluid has to be more water-rich, have its PH level controlled, and protect the surface of the aluminum pieces being machined.
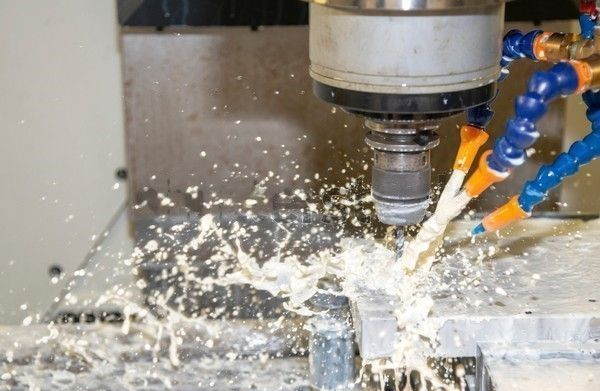
Storage environment
The surface of aluminum components that have undergone machining processing must have sand holes on it if they are stored in an environment with high levels of acid and salt for more than a week, such as the environment of an electroplating plant or an oxidation plant itself.
An aluminum pressure casting component made of aluminum alloy is called an aluminum pressure cast. The heated liquid aluminum or aluminum alloy was injected into the feed port of the die casting machine for die casting, cast aluminum component or aluminum parts machining processing, creating a mold, which is typically referred to as aluminum die casting. such as aluminum die castings, die-cast aluminum components, die-cast aluminum, aluminum die castings, and aluminum alloy die castings.
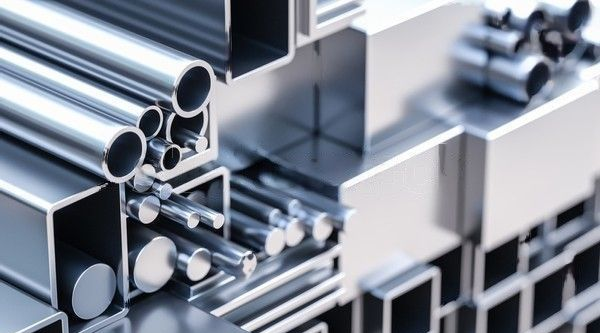
aluminum rods and billets storage
Pitting corrosion
Pitting corrosion is a surface corrosion process of aluminum metal characterized by tiny holes (pits) on the surface. Usually, these pits have little impact on the product's strength. Instead, it is a cosmetic problem, but if surface appeal is important, it may result in failure.
Pitting corrosion, which is caused by the presence of chloride anions, often happens in areas where salt is abundant in the environment. Pitting corrosion can also be partially brought on by sulfate salts. Alkaline and acidic salts cause the worst cases of pitting corrosion to occur.
For pitting corrosion to take place, the potential of the alloy must be higher than the potential of the electrolyte (salt solution). Pitting corrosion is preceded by the presence of surface flaws at grain boundaries and second-phase particles.

Intergranular corrosion
When it comes to aluminum, the grain boundary is electrochemically distinct from the alloy microstructure. An electrochemical potential is created as a result of this, and an electron exchange occurs.
Intergranular corrosion can take many different forms depending on metallic structures and thermochemical processes. A variety of aluminum alloys include it to varying degrees as well. The 6xxx series alloys, for example, are comparatively less prone to this kind of aluminum corrosion.
For various alloy systems, the anodic route will change. The grain boundary is portrayed as a continuous route in the 5xxx series, as opposed to the 2xxx series, where it appears as a thin band on each side of the grain boundary.
Similar to pitting corrosion, intergranular corrosion also starts in a pit. Insensitive grain boundaries are where it spreads the fastest, though.
Exfoliation corrosion
Intergranular corrosion with a specific characteristic known as exfoliation corrosion is a phenomenon that occurs in directionally marked aluminum alloys. Products made from aluminum that have gone through hot or cold rolling procedures are the ones where this is most noticeable.
It appears in the microstructure at long grain boundaries. Exfoliation is a word used to describe how the corrosion product seems to be rising off the material surface because it is more voluminous.
This kind of aluminum corrosion causes the product to become stressed as it grows above the surface and in both directions. As a result, the wedging motion first occurs at the product's surface before spreading throughout the majority of it. The material becomes more brittle due to severe delamination. Pitting, peeling, and blistering are examples of the effects of surface deterioration.
Due to their highly directed grain structures, the 2xxx, 5xxx, and 7xxx series are especially susceptible to exfoliation corrosion. As a result, intergranular corrosion is far more likely to affect grain boundaries.
By applying heat treatment techniques to disperse the precipitates, the susceptibility to exfoliation corrosion can be altered.

Deposition corrosion
When a foreign metal is deposited on the surface of aluminum, deposition corrosion takes place, which causes severe localized corrosion.
Consider a copper tube that is being filled with water. Copper ions are absorbed by the water as it passes through. This solution contains copper ions at this time. These copper ions are added to the aluminum surface or vessel when this solution comes into contact with it.
If the ions are lower in the electrochemical or galvanic series, they will create a modest galvanic cell that will erode the aluminum by pitting. The severity of the corrosion increases with the difference between aluminum and the deposited ion in the galvanic series.
It is known that significant corrosion can occur on the surface of aluminum at even a concentration of 1 ppm copper ion solution.
Heavy metals are the metals that have the potential to deposit corrosion on aluminum. Lead, copper, mercury, tin, and nickel are a few significant heavy metals.
Compared to alkaline solutions, the corrosion brought on by this technique is more evident in acidic solutions. This is due to the fact that these ions are poorly soluble in alkaline solutions.
SCC
A kind of intergranular corrosion known as stress corrosion cracking (SCC) has the potential to completely destroy aluminum components.
To cause this corrosion, three requirements must be met. A vulnerable alloy is the first of them. The likelihood of SCC varies across aluminum alloys. Stress corrosion cracking occurs more frequently in alloys with high yield strengths.
The second need requires a moist or humid service environment. Existence of tensile tension in the material is the third need. The crack's initial formation and subsequent spread throughout the metal are caused by this tensile stress.
SCC procedures come in two varieties. The first type of cracking is called intergranular stress corrosion cracking (IGSCC), and it spreads along the grain boundary. The second kind, transgranular stress corrosion cracking (TGSCC), is where the crack moves across the grain bodies rather than along the boundaries.
Prevention Methods
- To assure the quality of degassing and refining aluminum alloys, choose a good refining agent, lower the gas concentration in the aluminum water, drain the liquid level, and avoid allowing gas to enter the gas mold.
- Select an efficient release agent. When die-casting, the chosen release agent shouldn't produce any gas and should work well in terms of release;
- Make sure the mold exhaust is clear and unblocked, and that it is clear so that the gas inside the mold can be entirely released. In particular, the exhaust channel has to be cleared after the aluminum liquid has totally polymerized.
- To avoid air entrainment, adjust the die-casting settings and fill speed should not be too quick.
- Emphasize the use of core-pulling cooling in mold design and machining processing design for aluminum components to mitigate the negative effects of excessive wall difference.
- Where air holes frequently emerge, the mold and design need to be changed.
- Remember to examine the quality as the sand core is created rigorously in accordance with the procedure.
- Sand core dimensions are identical to those of the outer mold.
- Timely cleanup of the ink.
- Avoid rubbing the ladle on the sand core.
- When lowering the sand core, blow out the sand in the mold cavity.
Conclusion
It's crucial to comprehend surface flaws and their origins in aluminum-machining components to guarantee part quality. There is still a lot to learn, so it is advisable to collaborate with a specialist in aluminum CNC MACHINING. With premium materials, qualified workers, and state-of-the-art procedures, CNC milling China provides the best customized CNC services.
We tackle your assignment with the intention of supplying the highest caliber work. Additionally, our machinists keep a close eye on the procedure. As a result, we may eliminate wasteful procedures and just employ top-notch methods. Get a quotation right now by uploading your design file.