People all throughout the world are now able to live modern lives because of mass manufacturing. The requirement to produce goods swiftly in large quantities won't go away any time soon, yet the traditional production environment is not appropriate for the high-mix, low-volume production of complicated items. This is especially true for some plastic and mechanical components that demand sizable tooling investments.
Daily production management face conflicting key performance indicators. Such as high delivery precision, short lead time, and maximum resource utilization is a very difficult task in a high-mix and low-volume (HMLV) manufacturing environment. Where demand fluctuation is the norm rather than the exception. Even unreliable supplier performance could make things worse.
In this situation what should be the best alternative solution? How can we compete with the rising demand for products? Well, CNC machine shop application for high mix low volume (HMLV) and batch order production is best suitable for demand fluctuations.
In mass production, a lot of material waste produce throughout of production process. Thus, Lean manufacturing is attainable using aluminum CNC milling services in HMLV and batch order production.
CNC machining automation and flexible production are other features that make CNC milling precision best suitable for HMLV and batch order production.
Now we discuss in this blog in detail how are aluminum CNC milling services changing HMLV and batch order production? What are important things to know about CNC aluminum milling services? So, let's get started.

Photo by Daniel Smyth on Unsplash
The factors that Demand High Mix low Volume and Batch Order Productions
Make-to-order manufacturing, also known as high-mix, low-volume (HMLV) production, is the process of producing a wide range of goods in modest numbers. This kind of production is frequently used to manage and produce complex, one-of-a-kind products that must meet strict quality standards.
Manufacturing HMLV necessitates frequent adjustments to positions, supplies, and equipment. Operators working in HMLV environments must continually adjust the schedule of operations and materials due to the restricted number of production lines.
Here are the number of factors that demand high mix low volume production using CNC milling precision services.
- Improved product customization
- Increased customer responsiveness
- Reduce expenses because there is less inventory in storage.
Improved product customization
Allowing clients to customize a product in accordance with their needs and preferences is referred to as product customization. Add-ons, unique features, templates, and design flexibility all qualify as various types of customizing.
So, CNC precision milling Delivering personalized customer experiences to diverse user segments requires the customization of products. It is essential for developing client loyalty and raising client satisfaction.
Increased customer responsiveness
Understand your potential customers. Increasing customer responsiveness is figuring out which channels your customers prefer. Using CNC precision milling services, you may increase your customer's responsiveness to what changes he required and what adaption needs to adopt.
Reduce expenses because there is less inventory in storage
Keeping inventory levels low is a frequent logistics and inventory goal for businesses. Costs and management are involved with an inventory. Companies usually strive to strike a balance between having just enough inventory to meet short-term and current demand and not having a surplus. Therefore, CNC precision milling services are compatible to meet the demands in a short time.
Batch Production
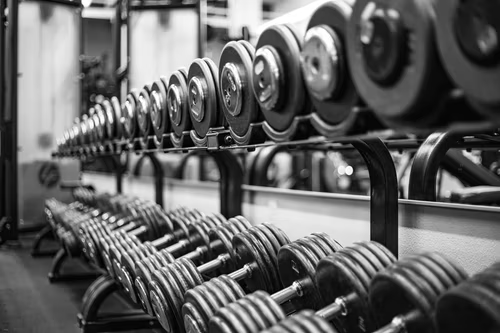
Photo by Luis Reyes on Unsplash
Batch production is a manufacturing process in which related or identical products are manufactured in groups for various-sized production runs. The process enables the mass production of goods, from automobile doors to children's toys, with minor to significant product modifications.
In order to create the intended result, each batch only passes through one stage of the production process. It is a crucial solution that is employed by companies of all sizes in numerous industries.
There could be variations across batches, such as products made in various sizes, colors, and styles. This variation can be updated as the production process shifts from one batch style to another if a product has to be modified.
The following factors lead to the creation of batch orders manually or during master planning:
- When there is not enough inventory, they are produced to fill sales order demand.
- They are produced to help with demand planning.
- To meet unusual demands, they are manually generated by authorized workers.
When producing in lower quantities, this kind of manufacturing is advised because it can cut production lead times and waste. Due to mass production of that batch, manufacturers can often produce these things at relatively low prices even though they are not continuously produced, allowing them to demand higher prices for their goods.
This manufacturing technique allows for a limited number of each sort of product to be produced at once. It is distinguished by the production of a small number of items that are made on a regular basis and stored in warehouses as finished goods awaiting sales.
Thus, aluminum milling services factories have enough potential to fulfill all HMLV and batch order production in a short time. So, Customers can get rid of expenses of inventory.
Things to consider for Selecting CNC Precision Milling Tool
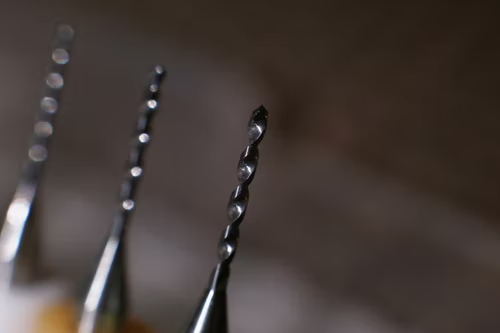
Photo by Marcus Urbenz on Unsplash
What are the requirements for a rapid prototyping CNC milling tool?
That seems easy, right?
It is clear-cut what you want a tool to do. Many engineers in CNC machine shops find it difficult to decide which tool to use to ensure that the job is done correctly. Of course, choosing a cutting tool for a prototype CNC milling isn't only about how well the tool performs.
There are some factors that are focused on while choosing any kind of CNC precision milling tool.
These factors or requirements are mentioned below
- simple to install or modify
- solid stiffness
- strong durability
- superior accuracy
When choosing a CNC machine shop tool, engineers should take the following factors into account. How thoroughly you comprehend the various aspects that might have an impact on the work you are doing will determine whether you make the proper choice.
The choice of machine tools is mostly a subjective decision that must take into account a wide range of variables. When choosing CNC precision milling tools, it's important to take into account elements like production capacity, equipment cost, and serviceability. Other elements that could be important or unimportant
An analysis of the following factors should be done to determine which of these classes the need for aluminum CNC milling services falls into
(a) the quantity of product needed and how long it will take;
(b) method of machining and required tolerances and finish;
(c) possibility of a change in product design;
(d) cost of production;
(e) when delivery is required.
Lean Manufacturing using Aluminum CNC Milling services
First of all, when we discuss lean manufacturing, we are referring to increasing a CNC machine shop's output by reducing waste generated throughout the production process. This system is based on the finest practices.
Firstly, Toyota used in their product line in the 20th century, where their major objective was to get rid of waste. The method grew so popular that manufacturing industries all around the world have adopted it.
The five foundational pillars of lean are value, value stream, flow, pull, and perfection, according to Womack and Jones.
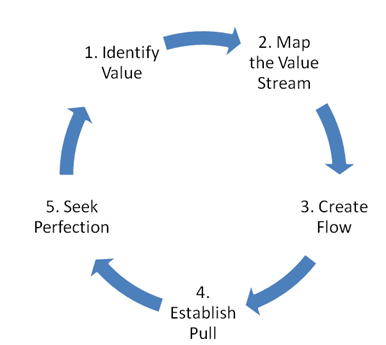
Value
Value is always determined by the needs of the client for a particular product. For example, when will the product be manufactured and delivered? How much does it cost? What other crucial conditions or demands must be fulfilled?
stream of values
The next phase is mapping the "value stream," or all the activities and procedures required in getting a given product from raw materials and delivering the final product to the consumer, after the value (end goal) has been established. Finding solutions to reduce inefficient stages is the aim after identifying each step that does not add value.
Flow
Make sure the value-creating stages take place in a precise order to ensure that the product or service flows smoothly to the client.
Pull
As a result, "just in time" manufacturing and delivery become significantly simpler. This implies that the client can "pull" the item from you as required (often in weeks, instead of months).
Perfection
A process is not truly lean, according to lean experts, until it has gone through value-stream mapping at least half a dozen times.
Industry experts have identified eight key kinds of industrial wastes via the method's evolution since its creation. These are defects, overproduction, waiting, underutilization of talent, transportation, excess inventory, motion waste, and excessive processing. These all defects can be abbreviated as “DOWNTIME”.
Lean manufacturing can be obtained while using aluminum CNC milling services. But, there are certain factors that should be considered such as those below
Production Done Just-In-Time (JIT)
JIT is made possible by wise resource allocation and scheduling. The absence of raw materials to work on is a major factor in the unnecessary waiting in CNC Machine shops. Planners devise the best strategies for the inflow, processing, and outflow of various resources in order to avoid this happening.
Initiatives for continuous improvement
The maintenance of the CNC machine shop's best practices comes last. Long-term, the aluminum CNC milling services factories that are able to offer the highest-quality parts with dependable delivery promises are those that consistently enhance their processes.
Logical plant layout
Plant layout is one of the most important considerations in a CNC machine shop in order to prevent the extra waste brought on by excessive transportation. Examples of such situations include placing raw material racks close to the blanking processes, setting up the machines so that the item can be transported quickly to the machining operation, and positioning the finishing equipment close to the packaging area.
Utilizing Machining Parameters and Processes Wisely
To maximize the use of the CNC precision milling, the material, and the toolings, manufacturing engineers carefully design their parameters (such as feed rate, cutting speed, depth of cut, etc.). Designing the optimum parameters for various machining processes is crucial in addition to the parameters. By adopting these steps, wastes associated with flaws, motion, and excessive processing will be reduced.
The efficiency of Tooling at its Highest (tooling selection)
The effectiveness of the tooling used in a CNC machine shop is crucial because it has the power to make or break the quality of the items that any CNC machine produces. The appropriate tool selection is crucial for ensuring high cutting quality, which will reduce defective components caused by inefficient tool use.
CNC Automation for HMLV and batch Order production
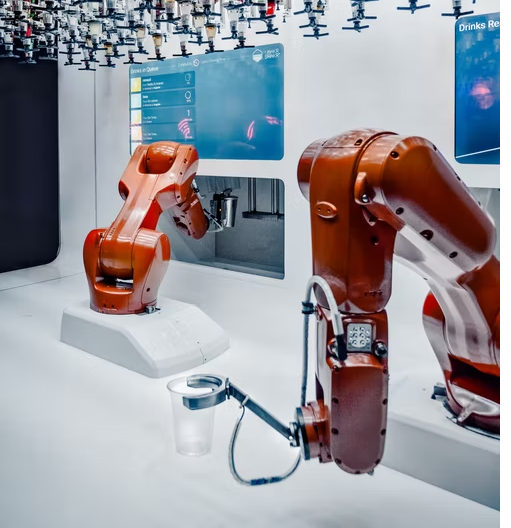
Photo by David Levêque on Unsplash
How does automation work? Automation is the process when robotized labor replaces some of the manual labor needed to complete a task in a manufacturing environment. A good example of this is coupling a robot cell to a CNC machine.
According to our experience, the most typical misperception about automating CNC machines is that one's company has too few units per year to support automation. Surprisingly few manufacturers are aware of the immense potential adaptable automation solutions offer in high-mix, low-volume production, also known as variable batch production.
It is characterized by one to several thousand single workpiece annual volumes.
Most manufacturers understand the necessity and benefits of automation in the context of mass manufacturing.
In mass production, workpieces are uniform, cycle times are frequently brief, and production rarely experiences unforeseen changes, such as urgent orders that must bypass queues. For instance, the manufacturing of auto sector parts mostly falls within this group. 'Transfer-line' automation, which permits incredibly efficient manufacturing operations in a steady environment, is often used to manage production.
The process of batch production involves producing an item's components in stages on multiple machines to make various batches of the final product. Because of the dependability, accuracy, and speed of CNC-based manufacturing, using them for batch production helps expedite the workflow.
Flexible Manufacturing
Today, flexibility means creating high-quality, unique items that are fairly priced and easily supplied to clients. Machine flexibility is the simplicity with which a machine can carry out different tasks.
A production system with a CNC milling precision tool or machining center and a material transportation device makes up the flexible manufacturing system. The machine can handle a variety of operations without halting thanks to the system's automatic control by an electronic computer.
A production technique called a flexible manufacturing system (FMS) is made to quickly adjust to changes in the type and volume of the product being manufactured. A variety of parts can be manufactured by machines and automated systems, which can also adapt to changing production levels.
Today's FMS tendency is toward compact variations of the conventional FMS known as flexible manufacturing cells (FMC).
Today, a flexible cell consists of two or more CNC machines, and a flexible manufacturing system consists of two or more cells.
To handle any family of parts for which it has been designed and built, a Flexible Manufacturing System (FMS) is composed of a number of machine tools as well as part and tool handling devices like robots.
More enterprises are choosing adaptable solutions for their manufacturing facilities. If you decide to do so, you can gain numerous advantages similar to these manufacturers.
A flexible manufacturing system offers an affordable method to raise shop floor efficiency and consistently deliver high-quality components on schedule. Additionally, it enables High Mix - Low Volume production by enabling the fabrication of a wide variety of parts using a CNC machine shop in small quantities, ranging from single parts through small and medium batches to series productions.
The benefit of CNC Machine
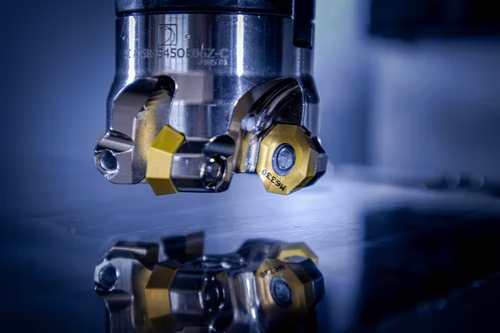
Photo by Daniel Smyth on Unsplash
The precision of the aluminum CNC milling services assures a constant level of product quality. Compared to manual machining, the procedure is more precise and may be repeatedly performed in the same way.
enhanced output velocity and effectiveness. The automated technique, which uses computers to manage the machinery, boosts manufacturing efficiency and quality. Since machines don't get tired or need breaks, they are more productive than manual machining.
Safety is one of the key benefits for CNC machine shop workers.
CNC machines run behind a guard or even a closed, transparent safety door, making them far safer to use than manually driven machines. It is more economical to use a CNC machining service. One operator is needed for each machine in traditional machining.
A well-maintained CNC precision milling machine will cut precisely as instructed after being programmed, resulting in a quick and reliable run of high-quality work. The machine will produce that part consistently after a good outcome has been achieved.
The end user gains a number of benefits from the usage of a CNC machine shop
few processes are needed to make parts, leading to excellent efficiency.
- The procedure is repeatable in the same way and is more accurate than manual machining.
- permits the extremely exact creation of intricate forms.
- Operates with sophisticated CAD software to generate outputs and perform numerous tasks that cannot be duplicated manually.
- The operator is not exposed to safety issues with fully automated systems.
The Bottom Line
Flexibility and adaptability are fundamental in CNC precision milling services in today's complex and uncertain manufacturing environment.
Part manufacturers can expand their markets to serve their customers who need more complex parts created quickly with the proper setup involving multi-axis machines, automatic workpiece changers (AWCs), and automatic tool changers (ATCs). Both High Mix - Low Volume (HMLV) and Batch Order productions benefit greatly from such set-ups.
A lot of product waste in mass production whereas, using aluminum CNC milling services will enable lean production. The five foundational pillars of lean are value, value stream, flow, pull, and perfection. These pillars create another value in CNC milling precision services for HMLV and batch order production.