Ever wonder how, in harsh environments, vacuum chambers manage to remain strong and intact? How can we ensure these vital parts withstand extreme heat, stress, and pressure? Heat treatment is a crucial phase that holds the key to the solution. Then why is heat treatment so important for the post-processing of vacuum chambers, and what does it entail?
Heat treatment is the process of heating and cooling metals or alloys to change their mechanical and physical characteristics without changing their shape. his process is revolutionary when it comes to vacuum chambers. As a result, the chambers are more durable, tough, and able to function under challenging conditions. It also strengthens the materials and reduces internal tensions. We'll explore the topic of heat treatment in this article and learn how important it is to vacuum chamber post-processing.
1. Purpose of Heat Treatment in Vacuum Chambers
Why is this procedure so important for producing these intricate systems? Vacuum chambers work under harsh conditions with tremendous pressure, very high temperatures, and demands of airtight seals that push materials to their limits. These problems are solved by heat treatment, which improves the mechanical qualities of the materials used in their creation.
Heat treatment increases the material's strength, hardness, and resistance to corrosion and wear by precisely regulating the heating and cooling cycles. Additionally, under operating stress, internal strains that may lead to warping or breaking are eliminated. This procedure guarantees the vacuum chambers' structural integrity and long-term performance. The heat treatment gives these chambers the durability they need to endure harsh vacuum application conditions. The following are some of the main goals of heat treatment:
- Enhancing Mechanical Properties: Heat treatment can improve a metal's toughness, ductility, hardness, and strength. For example, quenching and tempering can greatly improve the hardness of steel, increasing its suitability for a wider range of uses.
- Combating Residual Stresses: Materials may accumulate residual stresses during manufacturing operations such as casting, machining, and welding, which could cause warping or failure. By assisting in the release of these tensions, heat treatment ensures dimensional stability.
- Microstructure Refinement: Heat treatment can encourage materials to undergo desired microstructural alterations. Annealing, for instance, promotes grain development, which increases ductility and decreases brittleness.
- Get Equipped for More Processing: Heat treatment can facilitate the handling of materials in later stages of production. For instance, annealing metal softens it and facilitates shaping or forming.
2. Types of Heat Treatment Processes
Vacuum chamber material qualities are improved by a variety of heat treatment techniques, each with a distinct function based on the intended result. Let us examine a few prevalent types:
Annealing:
The heat treatment procedure known as annealing entails heating the metal to a predetermined temperature and gradually cooling it inside the furnace. This process makes the material softer, more malleable, and experiences less internal stress. Annealing is a critical step in vacuum chamber technology that increases the material's fatigue resistance and workability.
Tempering:
It is necessary to temper after quenching to lessen the brittleness that is created by rapid cooling. Following a brief period of reheating, the metal is gradually cooled. For vacuum chambers to function consistently without becoming overly brittle, a balance between toughness and hardness must be achieved by this technique.
Normalizing:
The process of normalizing involves heating the material above its critical temperature and letting it cool in the air. The mechanical characteristics of the metal are enhanced and its grain structure is refined with this treatment. Normalizing a vacuum chamber increases its resistance to high-pressure situations by ensuring structural consistency.
Quenching:
When a metal is quenched, it is quickly cooled by submerging it in a quenching media like water, oil, or air. The material's strength and hardness are increased by this treatment. Although quenching might make the metal more brittle if tempering isn't done afterward, it's frequently employed in vacuum chambers to attain the high strength required to withstand extreme pressures.
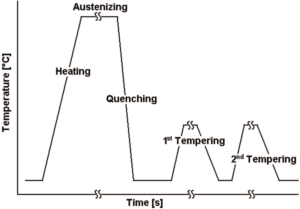
vacuum heat treatment
A specialized procedure known as vacuum heat treatment involves heating and cooling materials in a regulated vacuum setting. This improves material purity and guarantees a clean surface finish by getting rid of oxidation and contaminants. This procedure is especially advantageous for vacuum chambers because it upholds the strict requirements necessary for the chambers to operate efficiently under extremely high vacuums. Parts that require improved mechanical characteristics, cleanliness, and precision are best produced using this process.
3. Common Materials and Their Heat Treatment Processes
When discussing heat treatment processes for common materials, it's essential to understand that each material has its unique characteristics that dictate the type of heat treatment it undergoes. Here’s an outline covering common materials and their heat treatment processes:
1. Steel
Different heat treatments are done to steel to satisfy different needs, depending on whether the steel is carbon steel, alloy steel, or stainless steel. The following justifies the usage of these procedures:
- To make steel softer and more ductile, annealing involves heating it to a precise temperature and then gradually cooling it down.
- Quenching: Quickly cooling a heated material's temperature (in water, oil, or air) to solidify it.
- Tempering is the process of slowly cooling and reheating quenched steel to make it more resilient.
- To improve strength and refine grain structure, normalizing involves heating steel to a temperature greater than annealing and allowing it to cool in the air.
- Low-carbon steel can be carburized, or its surface hardened, by adding carbon.
Aluminium:
Here are the methods for heating of Aluminum;
- Aluminum alloys are heated to dissolve solutes and then quenched to produce a supersaturated solid solution. This process is known as solution heat treatment.
- Aging (Precipitation Hardening): Solution-treated alloys are heated to lower temperatures to cause solute elements to precipitate and fortify the material.
- Aluminum is softened and made more formable through the low-temperature annealing process.
Titanium:
Here are the methods for heating
- Stress Relieving: To relieve internal tensions, titanium can be heated below the transition temperature.
- Annealing: Heat is applied during annealing to increase toughness, machinability, and ductility.
- Solution-Treating and Ageing: This process of aging and dissolving alloying elements at high temperatures to precipitate the solutes strengthens titanium.
Copper and Copper Alloys
Here is the Procedures for Heat Treatment
- Annealing is the process of heating copper to make it softer, more electrically conductive, and more formable.
- Stress-relieving: It is conducted at lower temperatures to remove internal strains without changing the mechanical characteristics of the material.
- Age hardening, also known as precipitation hardening, is the process of heating copper alloys to a particular temperature and then allowing them to cool slowly.
4. Key Parameters in Heat Treatment
The ultimate qualities of a vacuum chamber are determined by essential heat treatment parameters. These consist of:
Temperature control and its importance
The microstructure and mechanical properties of the material are immediately impacted by temperature, making temperature control essential in heat treatment. The material will experience the appropriate phase changes that affect its hardness, strength, and durability if the exact temperature is maintained.
Time Duration
When it comes to giving the material enough time to reach the desired temperature consistently, the duration of heating is a crucial factor. A too-extended heating time might lead to grain expansion, which weakens the material, or an insufficient phase change.
Cooling Techniques
The rate at which heat is extracted shapes the ultimate qualities of the material and is determined by cooling techniques including air cooling, quenching, or oil cooling. While slower cooling techniques, such as air cooling, produce softer, more ductile structures, quenching produces greater hardness through rapid cooling.
Atmosphere Control
During heat treatment, oxidation, and contamination are avoided by the environment (vacuum, inert gas, or regulated gases). Sustaining surface integrity requires controlled environments, particularly for delicate materials that undergo high-temperature reactions with moisture or oxygen.
5. Challenges in Heat Treatment for Vacuum Chambers
Vacuum chamber heat treatment involves several difficulties that could influence the procedure and ultimate product quality, such as:
Warping and Distortion During Heat Treatment
Uneven heating or cooling during the heat treatment process can cause deformation and warping in vacuum chambers, which are commonly composed of materials like stainless steel. The structure may deform as a result of temperature expansion and contraction, which could compromise the accuracy of the dimensions. This problem is solved by using stress-relieving techniques both before and after heat treatment, as well as by maintaining consistent heating and accurate temperature control.
Risks of Contamination and Countermeasures
One of the main problems with vacuum chamber heat treatment is contamination, especially from oil, grease, or other residues. Under extreme heat, these impurities may evaporate, weakening the substance or resulting in unintended reactions. Before heat treatment, the chamber and its components should be thoroughly cleaned. Another preventive step is to use a vacuum or controlled environment (such as argon) to reduce contamination from outside sources.
Surface Oxidation Problems and Solutions
When a material is heated to a high temperature and exposed to air, oxidation may occur. This can cause unwanted scale formation on the material's surface and reduce its functionality. Vacuum chambers are frequently treated in inert or reducing atmospheres, or under vacuum conditions to minimize exposure to oxygen, and to minimize oxidation. Moreover, protective layers like aluminum or nickel surface coatings can be placed before heat treatment.
Surface Oxidation Due to the atmosphere
6. Benefits of Heat Treatment for Vacuum Chamber Performance
Heat treatment contributes to longer service life and more effective operation under high vacuum settings by optimizing the material's characteristics. What are the advantages of using this heat treatment in the post-processing of a vacuum chamber? It is explained in detail below. Let’s begin.
- Enhanced Strength
It increases durability and tensile strength, prolonging the service life of the chamber.
- Resilience against Corrosion
It raises the corrosion resistance in reactive circumstances.
- Relieving Stress
Minimizes warping or breaking during utilization by reducing residual stresses.
- Surface Hardness:
Carburizing or nitriding are two surface hardening procedures that increase wear resistance.
- Increased Vacuum Integrity
It ensures consistent vacuum performance by sealing porosities and minimizing flaws.
- A Higher Stage of Thermal Stability
improves resilience to heat cycling and keeps functioning at different temperatures.
- Reliable Performance
It ensures consistent material qualities, resulting in long-term dependable operation.
- Lower Upkeep Expenses
More durable materials reduce the need for replacements and repairs more frequently, which lowers total maintenance costs.
- Enhanced Manufacturing
It is possible to increase machinability with heat treatment, making it simpler to process intricate designs.
7. Quality Control and Testing After Heat Treatment
Vacuum chamber performance, longevity, and structural integrity must all be validated by quality control and post-heat treatment testing. Important tests include the following:
1. Dimensional Verification:
The vacuum chamber's structural integrity and performance are contingent upon quality control and post-heat treatment testing. Verifies that following heat treatment, the chamber keeps all necessary dimensions and tolerances, preventing distortion.
2. Hardness Testing:
This technique verifies that a material has reached the required strength and hardness for operation in a machine.
3. Non-Destructive Testing (NDT):
Techniques like dye penetrant testing and ultrasonic testing find surface flaws or internal fissures brought on by heat treatment. It is imperative to do comprehensive surface inspections following heat treatment to detect any potential cracks, warping, or distortions.
4. Examining for Variations in Mechanical Properties
Assessing mechanical characteristics after treatment is essential. This comprises impact, tensile, and hardness tests to evaluate alterations in toughness, ductility, and strength. These tests verify that the intended characteristics have been attained and that the chamber satisfies predetermined performance requirements.
5. Microstructure Examination:
Assessment of the material's grain structure microstructurally to make sure there are no undesired defects, that phase change is occurring properly, and that the material is uniform.
9. Application of Heat Treatment in post-processing of vacuum chamber
Heat treatment is a crucial step in the post-processing of vacuum chambers to ensure dependability and improve material performance. Among the important applications are:
- Stress Relief: Reduces the possibility of distortion or breaking under operating vacuum pressures by minimizing residual stresses from welding and machining.
- Degassing: Minimises outgassing during operation to ensure optimal vacuum performance by eliminating trapped gases and impurities from the material.
- Strength and Hardness Improvement:By improving the material's strength and hardness through processes like annealing and solution treatment, the chamber is made more resilient to mechanical wear.
- Fatigue Resistance: Increases the material's capacity to tolerate cyclic loading and lowers the risk of fatigue failure in chambers that are repeatedly subjected to mechanical loads.
- Enhanced Thermal Conductivity: Some heat treatments make materials more thermally conductible, which is useful for vacuum chambers employed for applications where effective heat dissipation is required.
9. Future Trends in Heat Treatment
Environmental sustainability, accuracy, and efficiency are the primary objectives of heat treatment's future developments. A few significant trends are as follows:
Advance Materials
The increasing usage of high-performance materials—like composites and advanced alloys—will spur the development of heat treatment techniques that are specifically suited to their special qualities.
Automation and Digitisation
The use of Industry 4.0 technologies, such as machine learning and the Internet of Things, will improve heat treatment process monitoring and control, resulting in increased accuracy and efficiency.
Green Practices
The adoption of eco-friendly materials and techniques to lower carbon footprints, along with the development of more energy-efficient heat treatment procedures, are all results of growing environmental concerns.
Integration of Additive Manufacturing
Heat treatment will be essential in the post-processing of the vacuum chamber step as additive manufacturing develops pace to enhance the mechanical characteristics of 3D-printed components.
Adaptable Heat Treatment Products
More specialized heat treatment solutions will be possible due to developments in simulation and modeling, which will optimize procedures for particular materials and applications.
Better Techniques for Quality Assurance
Enhancing the quality control of heat-treated components through the use of modern imaging techniques and non-destructive testing (NDT) will guarantee improved performance and dependability.
Conclusion
In vacuum chamber post-processing, heat treatment is essential because it greatly increases material strength, wear resistance, and overall performance. Precisely regulating the temperature, cooling, and environment, may improve the vacuum chambers' longevity and dependability, making them compliant with the stringent demands of contemporary businesses.
In the future, the field of heat treatment is changing because of promising developments in material science, automation, and sustainability. How will this procedure be affected by emerging technologies like nanotechnology and additive manufacturing? Is it possible to achieve maximum efficiency while also being environmentally conscious? These queries highlight the fascinating possibilities for heat treatment advancements in the future.