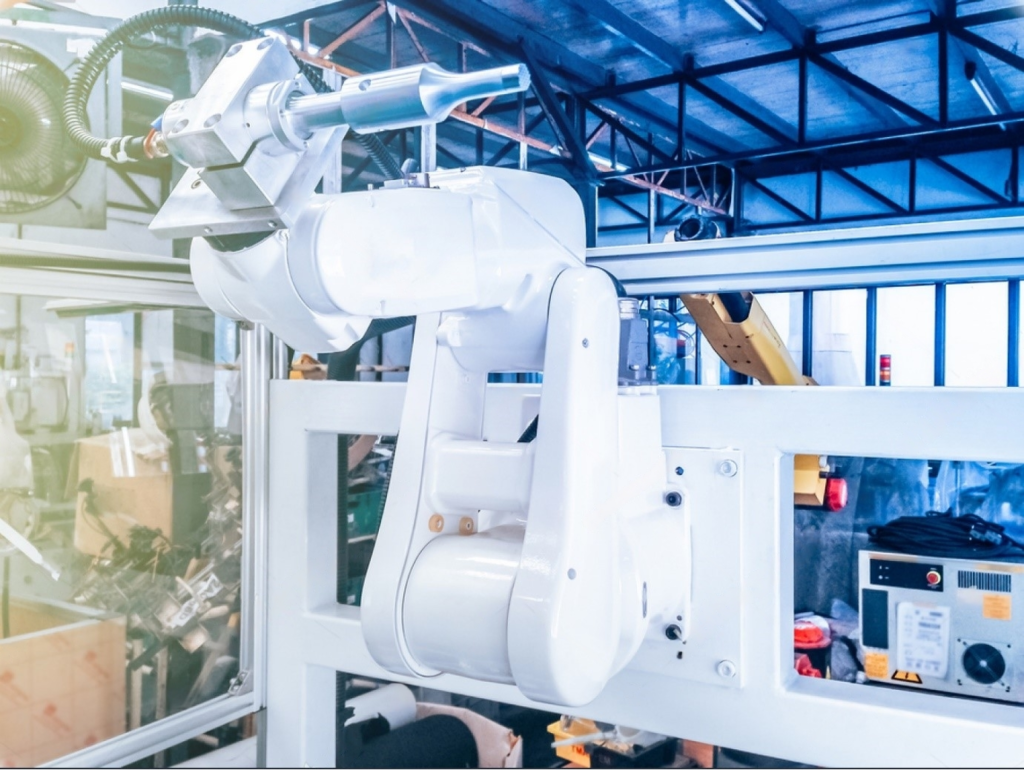
Ultrasonic welding (USW) is a solid-state welding process where two components are joined by applying high-frequency oscillatory shear stresses while under modest clamping force. This procedure, which is frequently employed in lap welding (as shown in Fig. below), breaks off surface coatings and permits close contact between the components, forming a strong metallurgical bond. Heat is produced at the interface by friction and plastic deformation, but the temperatures stay much below the melting point, negating the need for shielding gasses, fluxes, or filler metals.
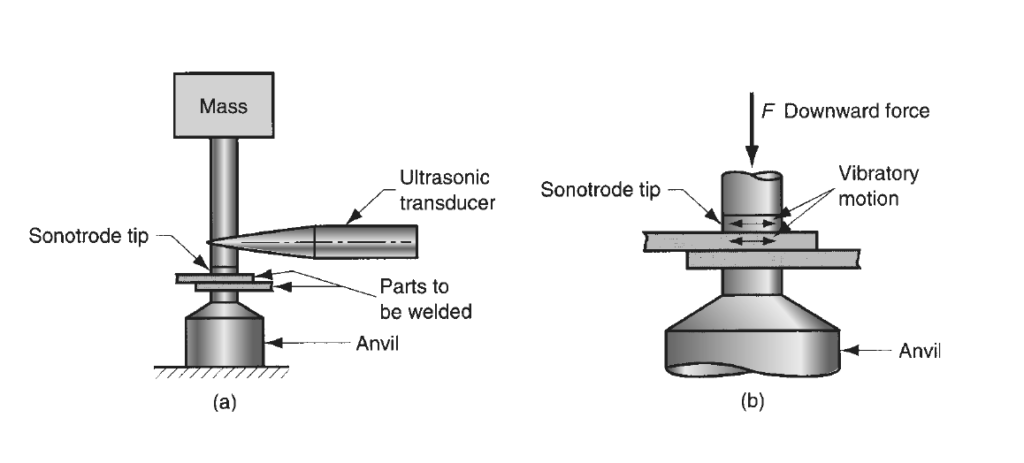
In USW, a sonotrode that is attached to an ultrasonic transducer transmits the oscillatory motion to the upper workpiece. This device transforms electrical energy into high-frequency vibratory motion, with amplitudes of 0.018 to 0.13 mm (0.0007–0.005 inches), and a frequency range of commonly 15 to 75 kHz. The surfaces are not significantly plastically deformed since the clamping pressures utilized are substantially lower than in cold welding. Welding times are typically shorter than a second.
Copper and aluminum are among the softer materials that ultrasonic welding works best on. Harder materials erode the sonotrode more quickly. The best workpieces are small, usually less than 3 mm (1/8 inch) in welding thickness. Soldering is not required when using this technology for wire terminations and splicing in the electrical and electronics sectors. Additionally, it is employed in the welding of solar panel tubes to sheets, the assembly of small parts, and the assembly of aluminum sheet-metal panels.
Welding Process
The following describes the general operation of the ultrasonic welding process:
-Material Preparation: Place the plastic components on the welding stack of the machine in a lap joint configuration.
-Production of High-Frequency Electricity: Standard electricity (50–60 Hz) is transformed into high-frequency electricity (20–40 kHz) by the generator.
-Conversion to Ultrasonic: The vibrations are amplified by the booster after the transducer converts the high-frequency electricity into ultrasonic waves.
-Welding: Ultrasonic vibrations are directed onto the assembled parts by the welding horn, also known as a sonotrode. The press is used by the operator to provide pressure. The operator extracts the welded components and retracts the horn after welding.
Ultrasonic welding machine components
Ultrasonic welding machines are made up of different parts, each with a specific function. Here are some key parts found in all types of ultrasonic welding machines:
Generator
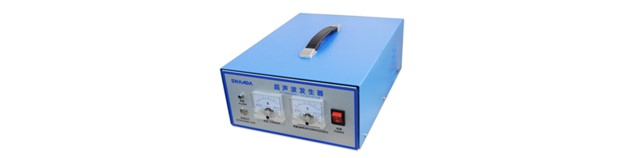
The generator converts electrical power into the required high frequency and voltage at a resonant frequency. A microprocessor that manages the welding cycle and enables essential communication via the user interface is also a part of it.
Machine Press
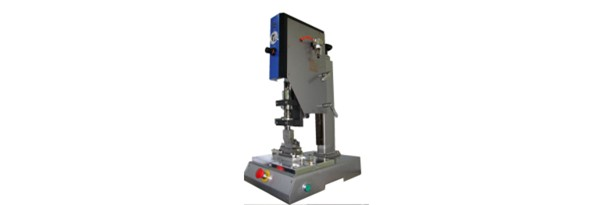
The machine press secures the welding assembly and applies the necessary force to maintain the joint. It is equipped with a pressure gauge and regulator, enabling the operator to adjust the force applied to the system.
Welding Stack
The transducer, booster, and welding horn are all part of the welding stack and are fixed to the press in the middle of the booster. The ultrasonic vibrations are produced by this assembly, and in order to guarantee excellent welded seams, their frequency must nearly match that of the generator.
Transducer
A transducer, sometimes referred to as a converter, converts electrical energy with a high frequency into mechanical vibrations. It is made up of many ceramic piezoelectric discs sandwiched between two titanium blocks. In addition, a thin electrode made of metal is positioned in between the piezoelectric discs.
Booster
The booster has two main purposes. It delivers the vibrations to the welding horn after amplifying them through contraction and expansion. It also serves as a foundation for the welding stack on the welding press.
Welding Horn

A welding horn, typically made of aluminum or titanium, transmits vibration to the welded part. Although aluminum works well in low-volume applications, it wears rapidly. In order to counter this, the majority of welding horns include hardened tips, which improve performance and longevity under heavy usage.
Support Tooling
Support tooling acts as the foundation of the machine by supporting its lower component while it is being welded. In order to provide stability and accuracy, it is made to fit the workpieces' curves.
Welding parameters
Ultrasonic welding is a highly effective method of joining materials, usually metals or polymers, by using high-frequency vibrations. The force applied perpendicular to the vibration direction, vibration amplitude, and vibration duration are the three main technological factors that affect the effectiveness and quality of ultrasonic welding. Comprehending and managing these variables is essential to attaining ideal welds.
Vibration Duration
The time that ultrasonic vibrations are applied to the materials to be connected is known as the vibration duration or weld time. This length is typically less than one second for the majority of welding operations. Nonetheless, if a weld requires more energy, the vibration length needs to be raised while maintaining the same values for the other parameters. The following formula determines the energy required for a welding cycle:

where �� is the energy in joules, �� is the power in watts, F is the force in newtons, �� is the amplitude in micrometers, �� is the frequency in hertz, and �� is the cycle time in seconds.
Vibration Amplitude
The longitudinal extension and contraction of the welding tool are measured by the ultrasonic vibrations' amplitude, which varies between 5 and 35 micrometers. This is an important amplitude because it matches the welding surface's friction distance. It takes less time to input the same amount of energy when the amplitude is increased because more power is needed to keep the vibration going. Amplitude profiling or stepping, as it is called, is made possible by the state-of-the-art ultrasonic equipment during the welding cycle. Since it strengthens the bond and avoids tool trapping, this method is very helpful for welding alloys like aluminum.
Force Perpendicular to the Vibration Direction
A key factor in the ultrasonic welding process is the force applied perpendicular to the vibration direction. The required mechanical stress on the welding zone is created by this force, which is produced by a pneumatic cylinder. The following describes the performance criteria for vibration creation and maintenance:

where Smh is the cross-sectional area of the pneumatic cylinder in square meters, pℓ is the compressed air pressure in pascals, and η is the mechanical efficiency. As the pressure increases, the mechanical load increases, requiring more power to sustain the vibration.
Process variants
In ultrasonic spot welding, the oscillating motion is transmitted from the overlapped inserts to the thinner materials (ranging from 0.005 to 3 mm). The sonotrode, applying force to compress the pieces, creates a welded bond that vibrates with the workpiece. It's crucial that there is relative movement between the workpieces, not between the sonotrode and the upper workpiece. This method can connect sheets or wires of varying material qualities. Ultrasonic welding, a form of continuous spot welding, produces welded joints between overlapping thin sheets positioned between the sonotrode and the anvil. During the process, three vibration units provide alternating motion around the axis of the tubular sonotrode, forming a seam of consistent size and shape with its tubular front surface.
Types of Ultrasonic Welding
Both metals and polymers, which have different material compatibilities are frequently joined via ultrasonic welding.
Ultrasonic Plastic Welding: For thermoplastics like polyester, ABS, and polycarbonate, ultrasonic plastic welding is the best method. Properties like hardness and moisture content should be taken into account. But it isn't appropriate for plastic polymers like polyamide and PVC.
Ultrasonic Metal Welding: This technique is effective for joining metals, including alloys made of copper, silver, brass, nickel, gold, and aluminum. This method works best with thin, small-diameter metals, which makes it ideal for sensitive uses.
Advantages of Ultrasonic Welding
Because ultrasonic welding uses indirect heating techniques, it improves aesthetics without sacrificing functionality, setting it apart from conventional sheet metal welding and non-welding methods. These are its main benefits:
Speed: High-frequency ultrasonic vibrations produced by ultrasonic welding swiftly weld suitable pieces, ensuring a quick production process. Short turnaround times and high throughput are the results of this.
High Level of Safety: Less operational risk is created by the indirect heat application. The welded connections and surrounding materials are shielded from damage by the localized and fast dissipation of the heat generated.
Reliability: The machinery is dependable and has few malfunctions and failures. Automation further minimizes operational and human error, saves operating expenses, and enhances the quality of welded joints.
Suitable for Dissimilar Materials: Another important aspect of plastic welding is that this procedure works well for joining disparate materials together. When joining dissimilar plastics, ultrasonic welding does not need the development of molecular bonds, in contrast to other plastic welding techniques.
Disadvantages of Ultrasonic Welding
There are a number of disadvantages to ultrasonic welding. It is inappropriate for hard and moisture-containing plastics, to start with. This method has trouble with thermoplastics with high moisture content and strong polymers like polypropylene. Furthermore, the transducer's limited range of 100-150 mm means that it is unable to weld pieces with joints greater than 150 mm. Part size is another constraint. The fact that melting thick materials takes a lot of energy makes them troublesome as well.
The expensive initial outlay is yet another major disadvantage. For organizations, ultrasonic welding equipment requires a significant financial investment due to their high cost, which rises with automation. Additionally, this method is limited to lap joints, which are formed of sections that overlap one another on a level surface. Other joint types, such as corner, butt, tee, and edge joints, shouldn't use it. When choosing whether ultrasonic welding is the best technique for your application, keep in mind that these drawbacks limit its versatility in comparison to other welding techniques.
Applications of Ultrasonic Welding
Ultrasonic welding is a valuable technique that finds uses in a wide range of industries, particularly in the fabrication of consumer and industrial goods. It's utilized to make vital medical supplies like anesthesia filters, blood and gas filters, and face masks. This method is perfect for medical devices since it guarantees low-cost, high-quality joints in parts composed of different medical polymers, like ABS and polyethylene.
To create components like instrument panels, door panels, and steering wheels, the car industry uses ultrasonic welding to fuse plastic. In addition to its low capital costs, automation, quick cycle times, and flexibility, the process is preferred because it uses indirect heat, which does not cause damage to the workpiece.
Because of its accuracy, speed, and high-quality joints, ultrasonic welding also helps the aircraft sector.
In the same way, the electronics sector uses ultrasonic welding to join wires and put together electric motors, capacitors, storage media, and delicate circuits. Because of its accuracy and dependability, it is perfect for creating tiny, complex electrical components.
References
Groover, M.P., 2010. Fundamentals of Modern Manufacturing: Materials, Processes, and Systems. 4th ed. Hoboken, NJ: John Wiley & Sons, Inc.