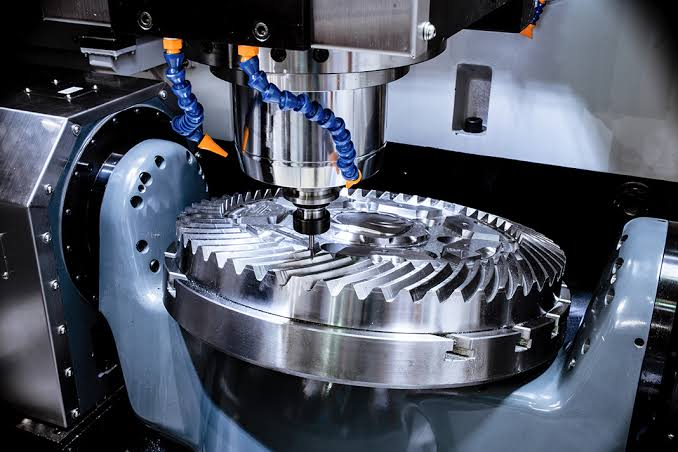
Over the past 150 years, as technology has developed in many different directions, the exact definition of the word "machining" has evolved. Initially, for the most part, people worked by hand, utilizing techniques like hand-forging and filing metal, as well as, carving wood.
But, in this era, there is strong competition and a broad spectrum of complexity in product demand. The industry has had to implement new machining optimization procedures due to material, size, complex design, and finish factors. These tactics involve implementing new technology, improving process flexibility and efficiency, and even altering the organizational structure.''
Modern production has substituted outdated machinery such as hammers, chisels,s and shaping machines with computer numerical control (CNC) systems. If you are an industrial person, a product creator with new ideas, who turns public demand into reality then you know precision technology isn't just an option – it's a necessity.
Now, buckle up your seats, as this blog is the ticket for you on a rollercoaster ride, in which we will uncover a detail on what is CNC machining, how CNC Machining is different from other machining techniques, and how it works. Do you think it going to be boring? Exactly No! Don’t worry! It will not be a historical lecture instead you will learn interesting information on how CNC Machining is ruling in every product manufacturing industry.
So, Are you ready for this ride? Let’s delve deep into it.
1. Introduction to CNC Machining
Computerized Numerical Control is referred to as CNC. It's a computerized control manufacturing process where production equipment moves according to preprogrammed software and code. The use of computers for design is known as computer-aided design or CAD. In CNC, CAD/CAM integration is used to design and manufacture the product.
G-code is a unique kind of code used to operate CNC machine equipment. To make a product with the necessary shape and size, components are automatically programmed to work following the sequence of events established by the user.
2. How Was CNC Developed?
The first "data systems" for machines were imagined by John T. Parsons, vice president of the Parsons Corporation's Aircraft Division one of the top producers of mechanical parts at the time. He got in touch with MIT's Servomechanisms Laboratory Professor Gordon S. Brown in the spring of 1949. NCs began to evolve in a modern manner in 1948 or 1949.
The United States Air Force was an important stakeholder in this advancement since it wanted machines for the aircraft industry that could produce complicated parts more quickly, cheaply, and accurately than with traditional methods. Therefore, the Air Force funded research into the viability of automated contour-cutting machines. The MIT Servomechanisms Laboratory and the John Parsons Company led the development of the first milling machine experimental models, which were tested in a few companies by 1951.

Photo by Sven Daniel on Unsplash
3. How Is CNC Machining Operated?
The computer transfers the data from the input and output, evaluates it on the device or in memory, examines the sensor readings, and then comes back to the computer to assess the readings from the sensors and the input till the lowest error rate is achieved, leading to the greatest level of precision and high excellence. In CNC machining the MCU works as the heart of CNC machine. The basic layout of the working principle is shown below.

The CNC machining process contains multiple essential components that operate together seamlessly. The CNC system's MCU (Machine Control Unit) receives the part program first. The MCU processes all of the data. Then, using the prepared program, it creates exact motion orders and sends them to the drive system.
Components of CNC system
Here are the following components of a CNC machine.
(i) Input Devices:
These units are in charge of feeding the CNC machine's part design. Three types of device input are frequently utilized: computers connected via RS-232-C protocol, magnetic tape readers, and punch tape readers.
(ii) Machine Control Unit (MCU)
The CNC machine's Machine Control Unit (MCU) is its brain; it controls every aspect of the machine. It can read and decode coded instructions, produce axis motion commands through linear, circular, and helical interpolation, feed these instructions to amplifier circuits that operate the axis processes, get feedback signals indicating the velocity and position for each drive axis, and perform auxiliary control functions like coolant or spindle on or off and tool changes, among other things.
(iii) Machine Tool:
Machine tools use some kind of tool to perform machining or cutting. The CNC machine tool has a spindle for speed and position control and a slide table. Z-axis control is applied to the spindle, and X and Y-axis control is applied to the machine table.
(iv) Driving System:
Drive motors, ball lead screws, and amplifier circuits make up the driving system. The amplifier circuits receive inputs from the MCU for each axis, such as position and speed, and then augment or boost the control signals to activate the drive motors. The machine table is positioned by the actuated drive motors rotating the ball lead screw in turn.
(v) Feedback System:
Transducers are used in this system to function as sensors and measurement tools. It constantly keeps track of the cutting tool's position and speed at all times. After receiving signals from these transducers, the MCU creates control signals to fix speed and position errors by comparing the reference and feedback signals.
(vi) Display Unit:
CNC machine projects, commands, and other relevant data are shown on a monitor that serves as a display unit.
4. What Are the Types of CNC Machines?
CNC machines are efficient because of their exceptional precision when handling various kinds of materials. Digital control machines have demonstrated their effectiveness in handling thick materials and their ability to quickly penetrate them, in contrast to other types of machinery. Several kinds of CNC machines have been developed as a result of this versatility: CNC machines can be categorized based on the work function of CNC machines, and the number of axes.
a)CNC Router
In addition to cutting sheet metal, plastic, and wood, CNC routers also provide three-dimensional axes for manufacturing complex and large-scale items. furthermore used to cut various materials along a route. The CNC router's form is shown in the Figure below.

b) Water Jet Cutting
This cold-cut method, which is used in CNC machines and does not contaminate the environment, cuts over any sort of soft or hard material, including ceramics, glass, and metal, by pumping water through the material. The water jet cutting form is shown in the figure below.

c) 3D printers
One of the most recent techniques for manufacturing is three-dimensional printing, which involves creating a product on a computer, having it printed using a 3D printer, and then fabricating it in a realistic and tactile manner. The 3D printers are shaped like stacks of material, and the printing process involves building layers of material on top of each other to create the desired product.

d) Milling Machine
This kind of CNC machine cuts various materials from produced materials by using rotary cutters. The form of the milling machine is represented by a Figure when it was operating by hand.

e) Plasma Cutters
This kind of CNC machine uses plasma to split steel and other materials, and plasma scissors are used for cutting the material.

Electric Discharge Machine
To cut conductive materials, one uses Electrical Discharge Machines or EDMs. An electrical arc is produced in EDM when a cutting head close to the material emits electrical pulses. The arc here creates a cut after melting and removing the material at the necessary location.
Laser Cutting
A laser beam is utilized for cutting materials. There is no restriction on what materials can be cut using laser cutting—unlike plasma cutting. By modifying the laser's specifications, beams of light can penetrate any material.

Other CNC Machines Based on their Axis of Motion
Here is the other list of CNC machines categorized based on the axis of motion. There are several CNC machines, each with unique uses and characteristics. The most fundamental kind is the 3-axis CNC milling machine, which has three dimensions of linear movement: X, Y, and Z. In contrast, the 4-axis CNC milling machine allows for the cutting of four sides of a product with just one fixture setup by adding a rotational axis (A axis) to the X, Y, and Z movements. The 5-axis CNC milling machine, which has two extra rotating axes (B and C axes), is the most sophisticated kind. The most complex and costly form of CNC milling machine is the 7-axis model, which offers more features for quicker production and more seamless operations.
5. How CNC Machining Process?
Turning raw resources into finished product is the process of manufacturing. Generally speaking, manufacturing is an intricate procedure involving a wide range of tools and techniques. This kind of automated machining technique uses computer numerical control technology to shape an object or a part. There are the following number of steps to consider while doing CNC machining.
A. Pre-Processing/product design
The initial stage in the manufacturing process is to create a design for the product. The mechanical design of a product is important before it is manufactured because it establishes the tolerances that the product must fulfill to be regarded as appropriate. There are following software is used for this purpose.
1. Designing the part in CAD software
CAD software is used to make sketches of the geometric shapes that need to be made in all dimensions and, if needed, transform them from two dimensions to three. The design of an item is essential before it is manufactured because it establishes the product tolerances for manufacturing. Once the design is complete, it is exported to code languages so that CAM can read it.

2. Creating toolpaths in CAM software
Mathematical models/GCODE representing two-D or three-D geometrical models are further transferred to CAM software on a computer. There are three possible formats for this mathematical model: wireframe, surface, or solid. Creating a toolpath involves choosing the machining approach, cutting equipment, and machining settings are all part of this process. Below is the process diagram of the CAM software.

B. Setup
The setup part involves material, tool selection, and choosing work-holding devices and fixtures. It is very crucial in ensuring the CNC machining process's accuracy and quality. Therefore, several factors need to be considered before running a CNC program.
1. Loading materials and tools
It includes choosing the right material and tool for the CNC machining. There is a vast range of materials available that apply to CNC machining. Choose any material that fulfills your requirements in strength, quality, and durability, and most importantly it should be cost-effective as well. For CNC machines, the tools need to be highly interchangeable, very stiff, and quickly changing to minimize non-cutting time.
Tool Selection and Operation Setup
In this section, we choose the appropriate cutting tool according to workpiece selection such as diamond tools are selected for hard materials. Tools are used to cut/ design a material in the desired shape. Three primary material types are utilized for cutting tools: ceramic, tungsten carbide, and high-speed steel. It is crucial to provide careful consideration to the selection and use of CNC machine tooling, namely tool holders. We set up the tool in-CNC machine properly to avoid its wearability. In the operation setup, the input is used to control system parameters such as spindle speed, feed rate, tolerance, and coolant on/off.
2. Securing the workpiece on the machine
Fixture and work holding devices are used to ensure the workpiece sample isn’t misplaced from its original position so that all pieces produced using the fixture will remain replaceable and compatible. This process avoids the uncertain breakage of the sample, and the tool during the process.
C. Machining Operations
The CNC machine tool equipment carries out operations by attaining linear sliding and turning movements. When the user commands the system to move the cutting tool along the x and y axes, the system will react accordingly.
1. Running the CNC program
Initially, Conduct a dry run (devoid of any cutting material) to confirm that the tool's actions, trajectories, and sequences are accurate. Make sure there are no unanticipated motions or crashes. The cutting tool's axis or cutting tool reaches the desired position following the program. Every control system is designed to keep the device from automating until the return to zero is carried out.
2. Monitoring and adjusting parameters
Make a proper adjustment of required parameters during CNC machining like feed rate, and spindle speed. Make sure to monitor the initial CNC cut carefully to avoid any damage. If anything unexpected failure happens it can be managed carefully. Continuous monitor the CNC machining process to verify the dimensions and tolerance.
D. Post-Processing
Post-processing includes ensuring the final quality inspection and removing excess material or deburring and finishing the material. After the machining process check the product quality, surface finish, and required dimensions. If there is any kind of roughness found on the product surface deburr it. Use surface treatments such as anodizing, coating, or polishing the product if needed.
6. Surface Finish
Following CNC machining, surface finish is a crucial factor that influences the machined parts' functioning, appearance, and performance. Surface finishes are used to modify the look, the degree of hardness, resistance to chemical attack, and texture of components that are processed. Here are the most common surface finishes.
1. Polishing
It employs buffing tools and abrasive substances to create a mirror-like surface that improves appearance and lowers friction.
2. Bead Blasting
It involves blasting the surface with fine abrasive particles to create a uniform, matte texture. It is the perfect method for getting rid of tool marks and producing a consistent appearance
3. Anodizing
It deposits a thin layer of oxide coating on aluminum parts to improve chemical and corrosion resistance.
4. Plating
To improve durability against wear, electrical conductivity, and corrosion resistance, a very thin film of metal (such as nickel or chrome) is applied to the surface.
5. Powder coating
This method creates a consistent, superior surface by applying an electrostatically charged powder and heating it to cure, resulting in a long-lasting, beautiful finish.
7. What Are The Most Common Machining Processes?
The machining process involves employing machines that can perform tasks such as lathes, milling machines, scrap machines, and others to carry out facing, roughing, finishing, cutting, slashing forms, and other operations to create workpieces following the intended design. Here are some machining processes that are commonly used in CNC machining.
CNC Turning
CNC turning is a machining process that is most frequently employed to shape workpieces with a cylindrical shape. But, it might also be used for raw materials with square or hexagonal shapes.

CNC Milling
This machining technique is utilized to shape/ cut product material in a diverse range of shapes and sizes as compared to turning. One of the most widely used kinds of CNC machining procedures is CNC milling. In reality, a lot of expert machine shops frequently switch between the CNC machining and CNC milling processes. Two applications for CNC milling that are most commonly utilized are face and peripheral milling.
Drilling
A rotating cutting tool is used in the CNC drilling process to create round holes in the sample. Usually, the holes are designed to take machine screws or bolts for installation needs. Nevertheless, they may be employed for aesthetic reasons as well using different kinds of drill bits as displayed below.

Boring
Internal machining of a hollow workpiece or in a hole previously created by drilling or other methods. Dimensional errors may result from the boring bar's deflection.

Broaching
Several teeth are used in broaching to machine flat surfaces, gear teeth, holes, and keyholes on the inside or outside. The broach tool is inserted into the workpiece by pushing or pulling.

8. Materials Selection for CNC machining
The choice of material is based on the requirement of the finished product. CNC machining offers a vast variety of materials, you may choose any kind of material according to your requirements. But choosing the right material is very essential to get great output. Therefore, you must have some knowledge about what kind of material you are going to choose for your project. So, a common distinction between the materials commonly used in CNC machining is elaborated on below
Metals & Alloys
The main materials that are utilized for CNC are metals and metal alloys. Metal can be utilized for low-to-medium volume manufacturing as well as for the fabrication of prototypes and unique singular parts. The following is a broad category of materials that are utilized in CNC part manufacturing:
❖ Ferrous Materials.
These types of materials are renowned for having remarkable magnetic, strength, hardness, and durability characteristics. Although iron makes up the majority of ferrous materials, it also frequently includes different proportions of carbon and other components. Ferrous materials are used due to their high machinability, and strength properties. The most common ferrous materials are steel, grey cast iron, and carbon alloy
❖ Non-Ferrous Material
Conversely, nonferrous materials don't have a substantial iron content. Rather, they are usually made of different alloys and metals like brass, copper, aluminum, and aluminum. Nonferrous materials are renowned for having superior electrical conductivity, resistance to corrosion, and lightweight nature.
Aluminium:
Aluminum is an abundant material utilized for CNC machining. It is just because aluminum is a very malleable metal, and machining is very simple and easy. The material is readily available in numerous varieties for a variety of applications and boasts a favorable strength-to-weight ratio.
Copper
Copper is mostly used in CNC due to its machineability and strength. It provides high precision and long-lasting parts in a variety of sectors.
Brass
It offers excellent machinability and mechanical properties in CNC machining allowing for high precision. It has an attractive appearance for various industry applications.
Alloys
Alloys combine desirable properties of material for machining for specialized applications. Its physical and chemical properties make it suitable for high-performance applications. It may include
- Carbon alloy
- Stainless steel
- Brass
Polymers & composite
Polymers and composites are utilized in CNC machining due to their strength-to-weight ratio, high resilience, and durability. Composite materials have better qualities than traditional materials, thus they are now essential to CNC machining. However it can be challenging to produce effective machining results if you overlook crucial factors like choosing the right plastic type, the optimal machining technique, keeping an effective surface polish, and avoiding frequent faults. Nylon, Acrylic, fiberglass, and metal matrix composite (MMC) are examples of materials.
Ceramics
Ceramics can be machined by CNC to create parts and products with a distinctive texture and look. Despite ceramic pieces manufactured in a kiln, those made with a CNC machine also exhibit outstanding flexural persistence. Now, CNC machining is very popular in the ceramic product manufacturing industry.
Glass
CNC machining is currently pushing the limits of using glass and other optical materials for desired product creation, despite CNC being used for decades to manufacture only metal, alloys, and plastic parts.
Other Materials are Graphite, Wood
Wood may be easily machined by CNC machines using end mills and router bits as it has a soft nature. Machining and polishing graphite can be difficult, particularly if you are ill-prepared for a combo of peculiar and abrasive qualities.
9. Design Guidelines
Additionally, you need to be competent to machine the item effectively and economically.
The process framework known as design for manufacturability (DFM) aids in combining the design of a product with its manufacturing process. DFM is essential to production and impacts all aspects of manufacturing, including costs and schedules, operational effectiveness, and part quality. The following are the most typical design factors for CNC machining:

Photo by Kelly Sikkema on Unsplash
Machine Frame and Structure:
To reduce vibrations and deflections during machining, make sure the frame is sturdy and rigid. Materials such as cast iron or welded steel material can be used to accomplish this.
Precision and Accuracy:
Use high-quality linear actuators, guides, and bearings to achieve a high order of accuracy and precision in manufacturing.
Drive System
Choose the right motors (servo or stepper) depending on the torque, speed, and accuracy needed. For applications requiring great precision, servo motors are recommended.
Spindle Design
To manage the variety of materials and cutting tasks that the machine is designed to perform, choose a spindle with the right degree of speed and force.
a. Principles for CNC Manufacturing Design
Design principles are essential rules that aid in producing items that are both physically appealing and useful. One of the biggest obstacles encountered while developing a part for CNC machining is the lack of nationwide industry standards. The capabilities of CNC machines and tools are always being enhanced by manufacturers, pushing the boundaries of that which is attainable. There are some basic principles in design as mentioned below.
- Employ standard thread pitches and hole diameters.
- Set the tolerances that can be accomplished with a CNC machine. Excessively tight tolerances can raise expenses without necessarily improving the part's quality.
- Stay away from sharp internal corners. Use rounds or fillets that have a radius that is at least half the diameter of the cutting tool.
- Blind holes should not be deeper than four times the width.
- Arrange the primary elements of your design using one of the six fundamental directions. This will facilitate the part's machining by the CNC machine.
- Make sure that cutting instruments can access every feature on the part. Refrain from designing anything with overhangs or deep voids that are hard to manufacture.
b. Design limitations for CNC machining
- Parts having interior undercuts cannot be machined by CNC machines.
- Very thin-walled items are not machinable by CNC machines. There is a different minimum wall thickness that depends on the machine and the material being processed.
- Very complicated geometries might not be able to be machined without specialized tools, such as 5-axis CNC machines, or they might require numerous setups.
- The machining of intricate internal geometries or deep cavities may be hampered by limited tool range.
- Cutting tools have to be replaced frequently due to their limited lifespan, which might disrupt production. Tool breakage can result in downtime and higher expenses, particularly when cutting hard materials or intricate geometries.
- Certain materials might be difficult and expensive to manufacture, particularly extremely hard metals.
10. Suggestions to Cut Costs on Your CNC Machining Job
There are various ways to reduce the cost of a CNC machining project, all of which concentrate on optimum design, materials, workflow, and overall effectiveness. These are some recommendations to assist in cutting costs:
1. Design for Manufacturability (DFM) optimisation
To cut down on machining complexity and time, create parts with simpler geometry. Be careful of complex elements that call for several setups or special equipment.
2. Selection of Materials
Select efficient materials that are more widely available and easier to process. In comparison to harder metals, it might be less expensive to process softer materials like aluminum or some plastics.
3. High Batch Production
Larger batches can be machined at a reduced cost per part by reducing setup intervals and distributing expenses over a larger number of pieces.
4. Quick Tooling and Setup
To cut the expense of specialized tools, use standard tooling. Make sure the tools can be used for a variety of tasks. Reduce setup time by designing fixtures and pieces. To improve tool paths, cut down on machining time, and increase tool life, employ advanced CAM software.
5. Minimise Tight Tolerances:
Define tight tolerances only when they are essential to functioning. Lower machining time and expenses can be achieved by using looser tolerances.
6. Constant Enrichment
To find opportunities for improvement, evaluate and assess machining processes regularly. To reduce waste and boost productivity, apply lean production concepts.
11. What Sets CNC Machining Apart from Other Machining Techniques?
Numerous significant characteristics and benefits set CNC (Computer Numerical Control) machining apart from other machining methods. Several characteristics distinguish CNC machining, including the following:
Automation and precision
CNC machines are managed by computer programs (G-code) unlike manual machines which allow for highly accurate and repeatable machining operations. CNC machining produces parts with precise tolerances and reliable quality. Production becomes more accurate and consistent as a result of automation, which lowers the possibility of human error.
Flexibility and Complexity:
Complex geometries and shapes that would be difficult or impossible to accomplish using manual machining processes can be handled by CNC machines. The 4 or 5 axes allow for the execution of complex cuts and processing through a variety of angles without requiring that the workpiece be moved.
Versatility:
The usage of CNC machining can reduce the need for several machines and setups by performing multiple operations, such as milling, turning, drilling, and tapping, on a variety of materials, including metals, plastics, wood, and composites.
Customization and Prototyping:
Rapid prototyping is ideally suited for CNC machining, which enables short lead times from design to finished product.
Comparison with Other Machining Methods:
Manual Machining:
In contrast to labor-intensive and operator-dependent manual machining, CNC machining provides more accuracy, consistency, and automation, hence mitigating errors and labor costs.
3D Printing:
While 3D printing allows for intricate, lightweight constructions and quick prototyping, CNC machining provides superior material qualities, surface quality, and accuracy for finished products. For smaller volumes, CNC machining usually entails higher costs and design limitations.
Laser Cutting:
While laser cutting can be used to quickly and precisely cut thin materials. However, CNC machining provides more flexibility in terms of material categories as well as the capacity to carry out turning, drilling, and milling operations.
12. Overview of the CNC Machining Industry
Three Technological Advances Waves
The CNC demand growth can be categorized into three phases/ waves.

Undoubtedly, the 1950s and 1960s saw the arrival of numerical controls for machine tools, which was the first wave. Over seven years, from 1959 to 1965, shipments rose by 40% on average.
The need for numerical controls in microcomputers during the 1970s and 80s led to the second wave of this technology. Between 1978 and 1984, sales of NC machines increased dramatically by roughly 30 to 40% a year.
Demand did not significantly rise after 1967 until twelve years later when substantial quantities of CNC machines became available. These devices were significantly more adaptable and had additional functionalities. Up to now, there has been a third wave of technological adoption.
According to a Fortune analysis, the CNC machining market is anticipated to be valued at more than $140 billion by 2029. The development of EV vehicles, automation, the usage of CNC in the manufacturing of medical and arts, and the rising demand for semiconductors and renewable energy will be the main drivers of this rate of expansion.
13. Is it Difficult to Operate CNC Machines?
The level of knowledge and expertise needed to operate a CNC machine can vary, making it either easy or difficult. CNC machines are easy to use and require little training for small parts and basic operations. Learning about CAD design, G-code programming, material characteristics, and process optimization is a big part of being a professional and streamlining the production process.
While learning the fundamentals of CNC machining is not difficult, there are a lot of online tutorials available to learn, just invest some time in learning and you can become a pro of this continuous and complex process.
14. Advantages of CNC Machining
The industry is the lifeline of each developing nation. Production will increase as these machines become more precise and efficient in their operations. Here are some benefits of CNC machining.
- It is easy to make any change in the product design.
- The program is simple to review and correct.
- Less time is required for data input and faster output production.
- Offers superior precision in part manufacture;
- Reduces production time as compared to conventional machinery.
- Cutting the cost of production because of continuous production.
15. Limitations and Challenges in the CNC Machining Industry
While there isn't a flawless innovation in the world, but, good inventions have benefits that outweigh drawbacks.
The downsides of CNC
- The machine's expensive price.
- To operate these kinds of machinery, operators need to have the best possible training.
- The scarcity of experts in maintaining these kinds of machinery. The availability of specialized tools to operate the machine remotely and continuously.
16. Applications of CNC Machining
Computer numerical control, or NC, equipment is extensively utilized in many different industries because of its accuracy, effectiveness, and adaptability. The following are some important uses of CNC machines:
Automotive Industry:
Engine parts including pistons, engine blocks, and cylinder heads are produced with extreme precision using CNC machines. The production of parts like shock absorbers, suspension arms, and chassis frames frequently involves the use of CNC machining.
Aerospace industry:
Landing gear components, fuselage frames, and wing spars are among the crucial structural parts made by CNC machines for aircraft. Parts of the engine: turbine blades, casings, and other parts are machined with extreme precision.
Vacuum Chamber:
Accurate machining of intricate geometries in vacuum chamber components is made possible by CNC technology, which is essential for preserving hermetic seals. Manufacturers attain the constant tolerances and surface finishes necessary for vacuum integrity and performance by utilizing CNC machining. Production efficiency is maximized by CNC automation, making it possible to fabricate vacuum chambers at a reasonable cost with little chance of operator error.

Robotic industry:
Precision parts for robot limbs, like joints, links, and end effectors, are made by CNC machines. CNC manufactures components for various electric, hydraulic, and pneumatic actuator types utilized in robotic systems. These are vital for advancement in the rapidly expanding and inventive automation industry.

Photo by Possessed Photography on Unsplash
Medical and Dental Industry:
CNC machines are used in the production of orthopedic implants, dental implants, and custom prosthetic limbs. Finely machined surgical equipment and tools.
Defence and Military:
Ammunition, other defense-related equipment, and gun parts are produced using CNC machining. Tanks and armored personnel carriers are among the military vehicles for which parts are produced.
Art and Sculptures:
CNC machines are used by sculptors and artists to produce massive sculptures and complex designs from a variety of materials.
Renewable Energy:
Blade and hub precision machining is a common practice for wind turbine parts. Frames and mounts for solar panels are manufactured by employing a CNC Machine.
17. Future Trends of CNC Machining
The drive for increased efficiency and precision, shifting industrial demands, and technical improvements will all influence future trends in CNC (Computer Numerical Control) machining. Look at the following important trends:
1. Automation and Industry 4.0 Integration
CNC machine integration into "smart factories," which allows for continuous information sharing and decision-making through communication with other equipment and systems.
2. AI and Machine Learning Development
Enhancing the lifespan of machines and decreasing downtime by employing AI to forecast when maintenance is needed for machinery. It maximizes the efficiency of energy, speed, and precision in machining operations.
3. Additive Manufacturing Integration
Combining additive manufacturing (3D printing) and CNC machining to create hybrid machines that can do subtractive and additive tasks.
4. High-tech software and modeling
To model and optimize operations before actual machining, digital replicas of CNC machines and processes are created.
5. Sustainability and Energy Efficiency:
Creating CNC equipment and procedures with the least amount of waste and energy usage.
The Bottom Line:
Since its invention, CNC (Computer Numerical Control) machining has undergone tremendous development and is now a fundamental aspect of current manufacturing. By automating the control of machine tools through computers, this technology transforms the production process and improves accuracy, reproducibility, and efficiency. As sectors continue to develop and incorporate new technologies. Incredibly, CNC machines are used to create the joints, linkages, and end effectors of robot limbs. Artificial intelligence is continuously reviving the CNC machining sector.
The most important aspect, you don’t need to worry about CNC machines to create any product design, instead you may avail the opportunity of a CNC machine shop just like BaiChuann CNC Machine where you may get any kind of assistance in product design and prototype production. So why are you waiting for? Just contact us and get a quote.