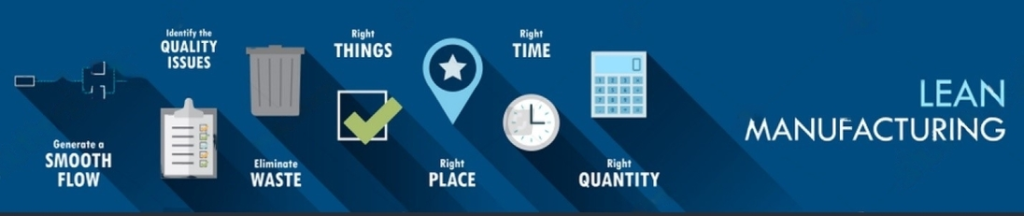
Introduction
Lean manufacturing, rooted in principles established by Japanese automaker Toyota, is a transformative approach aiming to slash waste in product development and manufacturing. The core objectives—eliminating overburden (Muri), inconsistency (Mura), and waste (Muda)—underpin a Just-in-Time (JIT) system. JIT encapsulates the ethos of producing only "what is needed, when it is needed, and in the amount needed," fostering efficiency and error reduction. Contrary to misconceptions, waste elimination in lean manufacturing isn't about workforce cuts but about sustainable value delivery to customers. It enhances lead times, boosts product quality, and trims operational costs, ensuring long-term competitiveness. As manufacturing evolves, lean principles serve as a compass, driving continuous improvement, streamlining processes, and embracing innovative technologies to deliver quality products swiftly and cost-effectively.
How Lean Manufacturing Works
By locating and removing waste, lean manufacturing seeks to improve quality, shorten production times, and save expenses. There are two main strategies: the traditional waste-focused strategy and the 'Toyota Way,' which prioritizes process optimization over waste reduction. The Toyota Way does not directly target individual wastes; instead, it takes a comprehensive, system-wide approach that encourages lean thinking throughout a company. It makes operational frameworks simpler to aid in comprehension and administration. 'Senpai and Kohai' (Senior and Junior) mentorship is also included in the method to foster lean thinking throughout the corporate hierarchy.
Key concepts like automation, continuous improvement, adaptability, load leveling, flawless first-time production or service quality, production flow and visual control, pull processing, supplier connections, and waste reduction are shared by both techniques despite their different methodologies. Processes are streamlined via automation, and improvements are guaranteed by continual improvement. Adaptability to shifting needs is made possible by flexibility, while resource consumption is maximized via load leveling. Prioritizing flawless quality from the start reduces errors, while visual control and production flow improve operational transparency. Pull processing helps to match output to real demand, and good working connections with suppliers promote cooperation. Either way, the goal of lean manufacturing is to maximize productivity and quality throughout the whole company.
Five Principles of Lean Manufacturing
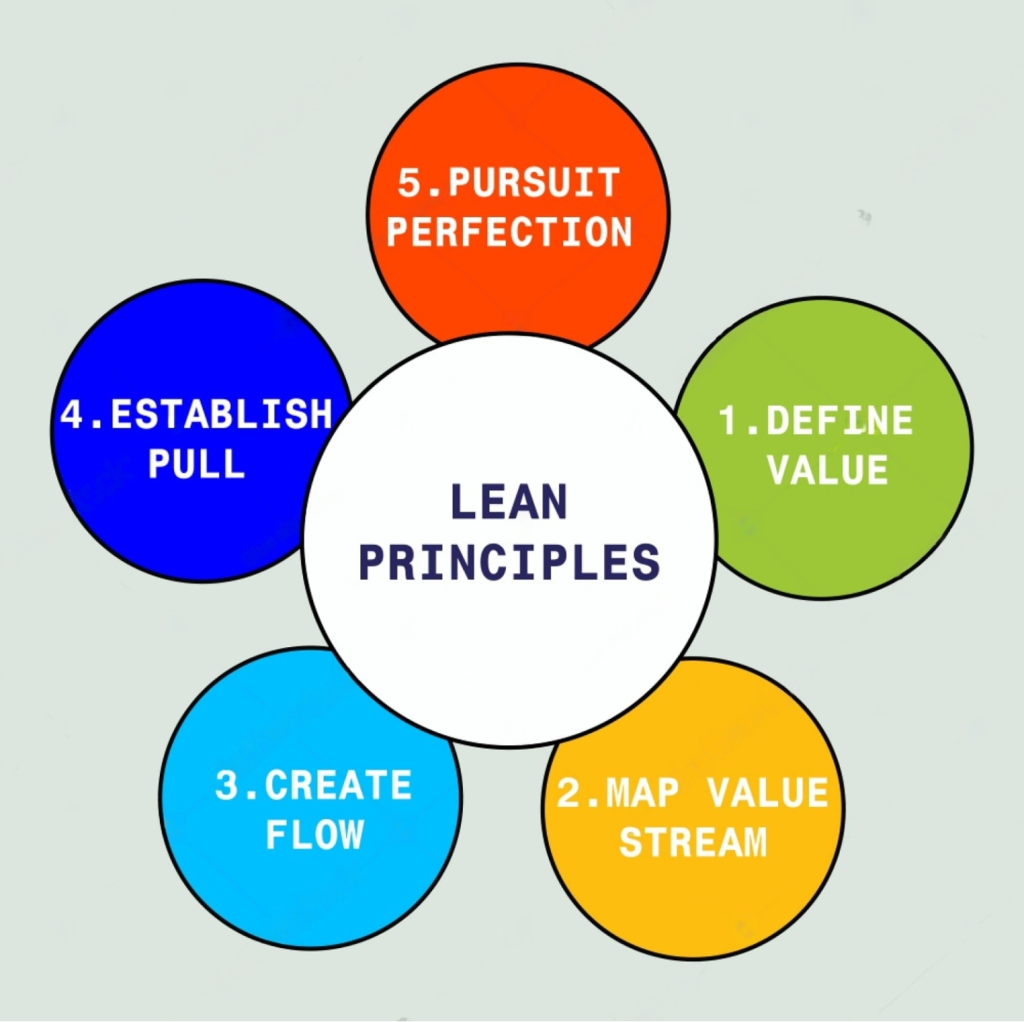
Five Principles of Lean (Reference)
Lean Manufacturing emphasizes five key principles to optimize production systems:
Customer Value Creation
In Lean Manufacturing, the primary focus is on efficiently creating customer value. The initial step involves identifying crucial product features through customer preferences. By aligning production with customer needs, the emphasis is on eliminating non-essential components, streamlining processes to enhance value, and ensuring that the final product resonates with customer expectations.
Value Stream Mapping
The lean approach defines the value stream as the sequence of steps adding value to the customer throughout manufacturing. Visualizing this process through a value stream map enables managers to pinpoint inefficiencies, minimize waste, and identify avenues for improvement. This visual aid provides insights into the entire production journey, aiding in the optimization of the manufacturing process.
Flow Creation
Lean Manufacturing advocates continuous process improvement, addressing issues such as suboptimal facility layouts. Improving the flow of the value stream involves eliminating bottlenecks and barriers that impede efficiency. A streamlined process ensures a smoother production flow, enhancing overall productivity and responsiveness to customer demands.
Pull System Implementation
The pull system, integral to Lean Manufacturing, dictates initiating new work only in response to customer demand. This approach eliminates wasteful activities like excess inventory storage and unnecessary transportation. By aligning production with demand, the pull system supports a just-in-time production model, reducing waste and increasing efficiency.
Continuous Improvement (Kaizen)
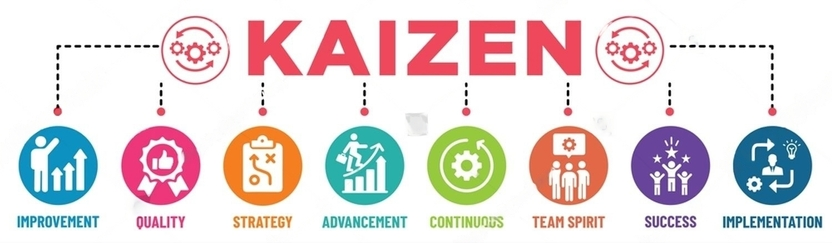
Kaizen, synonymous with continuous improvement, involves making incremental changes to enhance processes over time. In Lean Manufacturing, Kaizen enables businesses to identify and address issues systematically, maximizing customer value while minimizing waste. Through small, ongoing improvements, organizations cultivate a culture of continuous enhancement and problem-solving.
Toyota, a pioneer in Lean Manufacturing, employs a mentorship methodology called Senpai and Kohai (senior and junior). This approach instills lean thinking throughout the organizational structure, fostering a ground-up commitment to efficiency and waste reduction. In summary, Lean Manufacturing's principles, rooted in customer-centricity and continuous improvement, offer a framework for businesses to streamline operations and enhance overall production efficiency.
Types of Waste in Lean Manufacturing
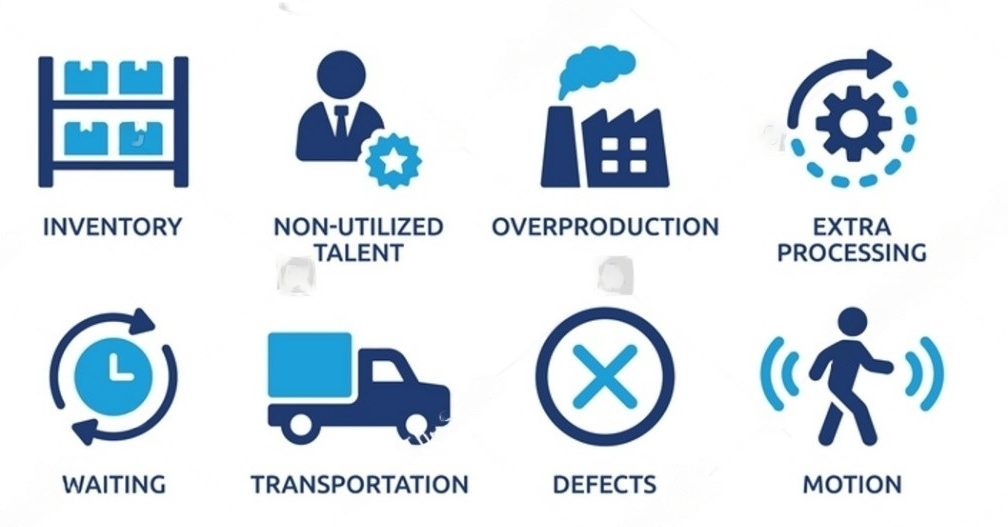
Lean manufacturing places a strong emphasis on cutting waste to increase productivity and provide consumers with value. Gaining an understanding of the eight categories of waste is essential for streamlining operations and enhancing overall company performance.
Defects
Visible and expensive defects lead to items that don't satisfy requirements, which delays delivery and annoys customers. Reworking faulty products costs money since it takes time and resources. Reducing financial losses and preserving customer happiness depend on effective defect management.
Overproduction
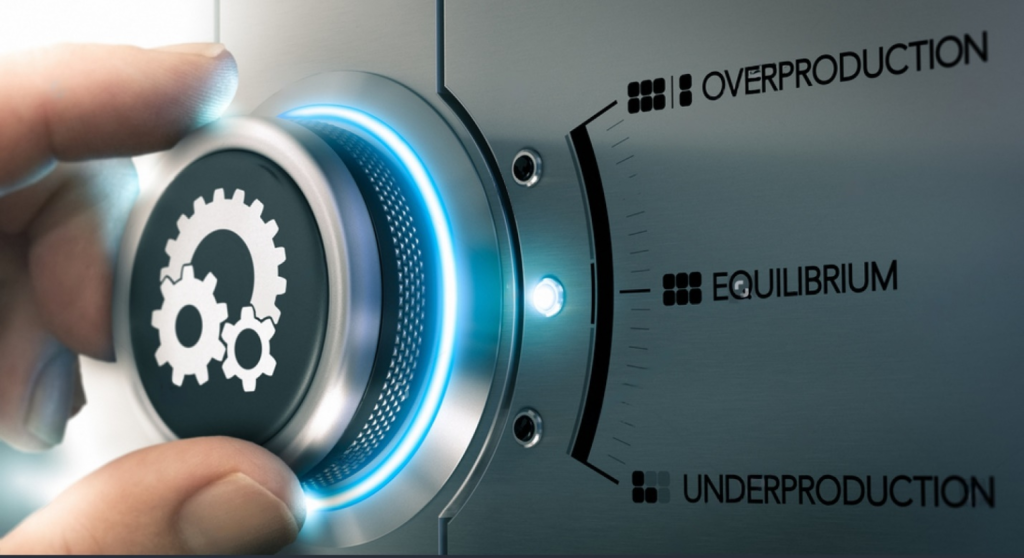
When production exceeds consumer demand, extra inventory is created, storage costs are incurred, and possible product deterioration occurs. Takt time, or the pace at which supply meets demand, can be tracked to help match supply to real demand and avoid overproduction and related expenses.
Waiting
When a consumer or product is ready for the next phase but the process that follows isn't ready, waiting occurs. This lowers consumer satisfaction and can cause delays in several industries, including manufacturing and healthcare. Reducing waiting waste requires accurate time measurement and process design modifications.
Non-utilized Talent
A major source of non-utilized talent waste is the disregard for the abilities and potential of employees. Workforce efficiency is hampered by ineffective teamwork, inadequate training, communication gaps, and pointless administrative activities. The best use of staff talent is ensured by addressing these problems with appropriate training and participation in process enhancements.
Transportation
Transportation waste is a result of the movement of commodities between places without contributing value to the final product. Ineffective transportation systems raise expenses, use more energy, and may even cause product harm. As demonstrated by Toyota's methodology, placing production facilities close to suppliers reduces transportation waste and boosts total productivity.
Inventory
When goods are kept on hand while they wait to be sold, inventory waste happens similarly to overproduction. Physical costs are associated with having too much inventory, and this can result in higher storage costs. By avoiding overproduction and inventory waste, just-in-time production helps to maintain a balance between procurement and consumer demand.
Motion
Motion waste is the unnecessarily moving of personnel, equipment, or other non-value-adding objects. It is a sign of a deviation from lean manufacturing practices. Time is lost as a result of poorly planned work areas and inefficient placement of materials or equipment. Eliminating motion waste and increasing overall efficiency are two benefits of adopting the 5S lean manufacturing concept.
Extra Processing
Overprocessing, also referred to as "extra processing," is the addition of work that is not essential and results in the waste of time, materials, and equipment wear. As a result, resources are diverted from jobs that bring value, decreasing process efficiency overall. Process simplification and attention to detail reduce unnecessary processing and increase output in general.
Advantages and Disadvantages of Lean Manufacturing
Advantages
Saves Money and Time: The most apparent benefit of lean manufacturing is cost reduction. Regardless of size or output, organizations may gain from more efficient processes, resource allocation, production, and storage. In addition to enabling shorter lead times and faster product delivery to clients, time-saving measures may also result in cost savings by creating a more efficient staff.
Enhanced client Satisfaction may be achieved by providing a better product or service to a client at an affordable price. This is critical to the success of your organization since contented clients are more likely to use your goods or services again or refer others to you.
Eco-friendly: You may save money on energy and gasoline by cutting down on wasteful operations and wasting less time and resources. Both this and the deployment of more energy-efficient equipment, which may also result in cost savings, have clear environmental benefits.
Disadvantages
Employee Safety and Wellbeing Concerns: Critics argue that lean manufacturing may neglect employee safety and well-being by overly focusing on waste reduction. The intense pressure to adhere to streamlined procedures might overlook the toll on employees, reminiscent of outdated 19th-century management techniques.
Potential Hindrance to Future Development: The inherent focus on waste reduction may lead management to cut areas considered non-essential to the current strategy. However, these aspects may be vital to a company's legacy and future development, potentially hindering long-term growth. Lean manufacturing can create a myopic emphasis on the present at the expense of future considerations.
Challenges in Standardization: Critics contend that lean manufacturing, being more of a cultural approach than a rigid method, lacks a standardized production model. This perception may undermine the credibility of lean as a robust and well-defined technique.
Best Lean Manufacturing Tools
Lean manufacturing relies on various tools to streamline processes and enhance efficiency. Among the best tools in this approach are Kanban, Kaizen, Value Stream Mapping, 5S Management, and Plan-Do-Check-Act (PDCA).
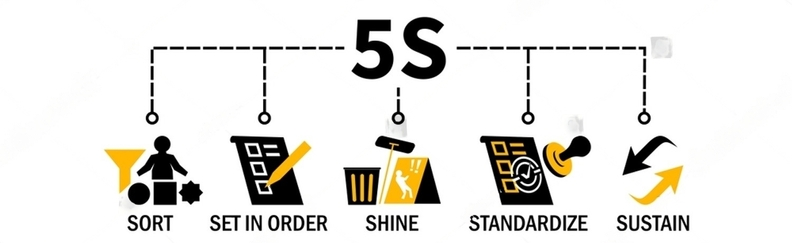
5S Management (Reference)
Kanban, whether in digital or physical form, serves as a signal for small-batch production, optimizing resource utilization. Kaizen, a tool for continuous improvement, encourages small daily changes across all levels of an organization.
Value Stream Mapping is a versatile tool that analyzes and improves material and information flow throughout the entire product or service lifecycle. Meanwhile, 5S Management, encompassing sort, set in order, shine, standardize, and sustain, is a productivity tool that enhances efficiency by making abnormalities visible.
PDCA is a fundamental lean management tool promoting continuous improvement. It involves planning specific goals, executing the necessary tasks, evaluating outcomes, and adjusting as needed.
In addition to these core tools, various methodologies contribute to the implementation of lean management. Control Charts monitor workflows, Kanban Boards visualize processes, and 5S offers a methodology for workplace organization. Multi-process handling, Error Proofing (Poka-Yoke), Rank Order Clustering, Single-Point Scheduling, Single-Minute Exchange of Die (SMED), and Total Productive Maintenance further refine manufacturing processes.
Moreover, Work Cell Redesign optimizes the layout for improved workflow. These tools collectively create an effective lean management system. They encompass aspects like workflow visualization, workplace organization, error prevention, and continuous improvement, contributing to enhanced productivity and overall operational excellence.
Practical Lean Manufacturing Tips for Machine Shops
Embracing lean manufacturing in machine shops is not just about adopting specific practices; it's a dynamic philosophy requiring a profound understanding of its principles. Womack and Jones highlight the critical distinction between those who merely copy practices and those who grasp the fundamental principles underpinning the entire lean system, emphasizing the latter's success.
To cultivate a lean approach, view it as an ongoing journey necessitating continual assessment and adjustment. A lean toolbox of methods can simplify management systems, but remember, lean is more a philosophy than a rigid set of procedures. Here are four actionable steps to shape an effective lean project management system tailored for machine shops:
Craft a Streamlined Manufacturing System:
Break down your operations into simple, composite parts for easier monitoring and waste elimination. Simplifying processes enhances visibility, making improvements more manageable. This step aligns with the essence of lean thinking—efficiency through simplicity.
Constantly Pursue Improvement:
Empower staff at all levels to actively seek better ways of doing things. Encourage an honest evaluation of procedures, pinpointing areas ripe for improvement. Tailor these enhancements to your specific machine shop processes for maximum effectiveness. The more precise and relevant the improvements, the more impactful the results.
Implement Ongoing Design Improvements:
Identifying improvements is just the beginning; they must be seamlessly integrated into your designs, procedures, and processes. Opt for incremental changes, supported by measurable metrics. Practical application is key—ensure that enhancements translate into tangible, day-to-day improvements.
Secure Staff Buy-In:
Success in the first three steps hinges on garnering the support of your staff. Lean principles encompass the entire business, necessitating management's understanding of the genuine issues at hand. Employee resistance can impede progress, making it crucial to involve them in the lean journey. Establish a 'lean plan' for collaborative decision-making, where teams contribute feedback, and management decides on changes. Coach employees at all levels to impart the knowledge needed for a collective and successful lean implementation.
Conclusion
To sum up, lean manufacturing—which has its roots in the Toyota Production System—prioritizes waste removal to increase productivity and value for customers. Value, Value Stream, Flow, Pull, and Perfection—the five pillars of lean manufacturing—allow companies to reduce waste in a variety of ways, including overproduction and faults. Stressing a straightforward design and getting staff cooperation may maximize outcomes, resulting in lower costs, better quality, and more customer satisfaction in a competitive market, including methods like Kaizen and Kanban to promote continual development.