Blind hole engineering and fabrication are two closely linked disciplines that were essential in creating many modern products. Dealing with blind holes is one of the difficulties engineers and machinists encounter. Blind holes are holes that don't completely penetrate the material; instead, they halt just short of getting to the other side. To ensure that the blind hole terminates at the desired depth within the material, blind holes need to be machined with more accuracy.
They are frequently employed in production processes for several functions, including tapping threads, producing cavities for inserts or rivets, or simply serving as the starting point for drilled holes. These holes can present several difficulties during the process of production. In this article, we will examine what blind holes are, why they are used, and how they are made. So, Let’s begin.
Blind Holes VS Thru Holes
Blind holes are cavities that are drilled, bored, or milled into a material but do not penetrate to the full length. This indicates that the hole does not escape through the other side, but rather terminates at a specific depth within the material. Blind holes are frequently used in manufacturing for several purposes, including to make a surface for fasteners or a recess for a component to fit into.
When making a through hole is not possible or preferable, blind holes are frequently used. For instance, making a through a hole in a material with narrow walls could weaken the structure, whereas a blind hole can fulfill the required function without endangering the strength of the material.
It is crucial to keep in mind that when creating blind holes, additional care may need to be taken to ensure proper alignment and depth as well as to avoid the buildup of debris or chips that could impair the hole's functionality.
A "thru hole" is a hole that is fully drilled through a material or component in manufacturing and engineering. This indicates that the hole penetrates the complete thickness of the substance or component and then exits through the other side.
Thru holes are frequently used in a variety of uses, including the passage of electrical components through circuit boards, bolts, and screws through metalwork, and dowels and pegs through woodworking.
Through holes, which pierce a substance entirely, are frequently confused with blind holes. Because they can be drilled directly into the material, holes are usually simpler to make than blind holes.
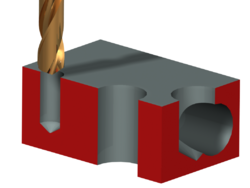
Blind holes (left) Thru-hole (middle) interrupted (right) Photo by Handwiki.org
How Blind Holes Engineering is Essential in Machining
For several reasons, blind holes are crucial in machining:
Tolerances: accurate dimensions and tolerances are crucial when milling a component. Because the bottom of the hole is a set reference point, a blind hole is simpler to accurately machine than a through-the-hole. To check that the hole is within the required tolerance, the machinist can measure the depth of the hole.
Threaded Holes: Since threads are only necessary on a part of the hole, blind holes are frequently used for threaded holes. In a bolted joint, for instance, the bolt may only need to thread into a portion of the hole and the leftover space may be left unfilled.
Blind holes can also be used to enhance a part's aesthetic appeal. Since the bottom of the hole will be obvious, a through hole might not appear as tidy as a blind hole.
Strength: A blind hole occasionally offers more power than a through hole. This is so that the material can distribute the load over a bigger surface area at the bottom of the hole, which reduces the likelihood that it will break under strain. Overall, blind holes are a crucial tool in machining because they increase the final product's precision, flexibility, and strength.
Why Are Blind Holes Used?
Blind holes are employed in manufacturing for several purposes. Giving fasteners, like screws or bolts, a surface to adhere to is one typical use. A safe attachment point can be made by drilling a blind hole into the substance, which can then be threaded with the fastener and tightened. This is frequently used in situations where a flush surface is wanted or where the fastener needs to be hidden from view.
Blind holes are frequently used to make recesses that components can slide into. For instance, a blind hole can be made to provide an exact fit for a component that needs to be inserted into a larger assembly. By doing so, you can help ensure that the component is firmly fixed and won't move or change while it's being used.
Blind holes can be utilized for aesthetic reasons as well. A decorative component can be pressed into a blind hole that has been made just slightly smaller than it, holding it in position without the use of additional fasteners or adhesives. This may produce a visually pleasing appearance that is neat and streamlined.
How is Blind Hole created?
Drilling, boring, and milling are just a few of the machining processes that can be used to create blind holes. The precise method will be determined by the material that is being machined, and the size, depth, and accuracy requirements of the finished hole.
One of the most popular techniques for making blind holes is drilling. By removing material from the object with a drill bit, a hole that penetrates the material to a specific depth is made. The drill bit is stopped before it penetrates the opposing surface of the material to produce a blind hole. This can be done by meticulously measuring the depth of the hole as it is being drilled or by using a depth stop on the drilling machine.
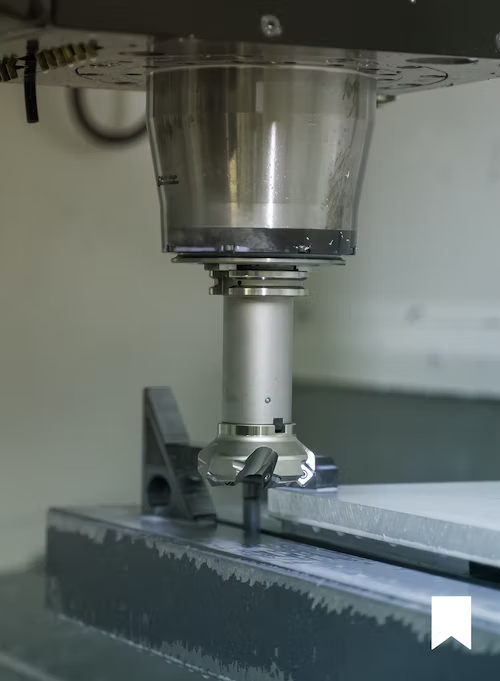
Another typical technique for producing blind holes is boring. Boring is the process of making a new hole or enlarging an existing hole in a workpiece using a single-point cutting instrument. As the cutting tool can be altered to produce holes of different sizes and depths, boring can be used to accurately make blind holes.
The third technique for making blind holes is milling. In milling, the material is taken out of the workpiece using a rotating cutting instrument. Different milling machines, such as vertical milling machines, horizontal milling machines, and multi-axis milling machines, can be used to accomplish this. Blind holes with intricate curves can be made using milling.
Depth of a Blind Hole
Depending on the particular application and design requirements, a blind hole's depth can change. The thickness of the material being machined and the intended depth of the recessed feature, in general, define the depth of a blind hole.
For instance, the depth of the hole should be adequate to fit the length of the screw or bolt is used if a blind hole is being used to create a threaded hole. The hole's depth should be adequate to accomplish the desired depth of the pocket if the blind hole is being used to make one.
It's crucial to remember that a blind hole's depth shouldn't be greater than the material's thickness. If the hole is too deep, the material's integrity may be compromised, weakening the framework or component. To ensure that blind holes are machined to the proper depth for a particular purpose, engineers and machinists should always refer to the design specifications.

What is the Blind Hole Symbol?
The GD&T doesn't have a symbol for a blind hole. It will be essential to the diameter and depth specification—or the quantity of material still present for a blind hole.
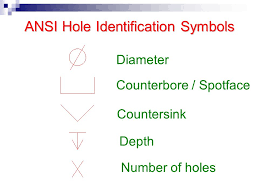
Blind Hole Example
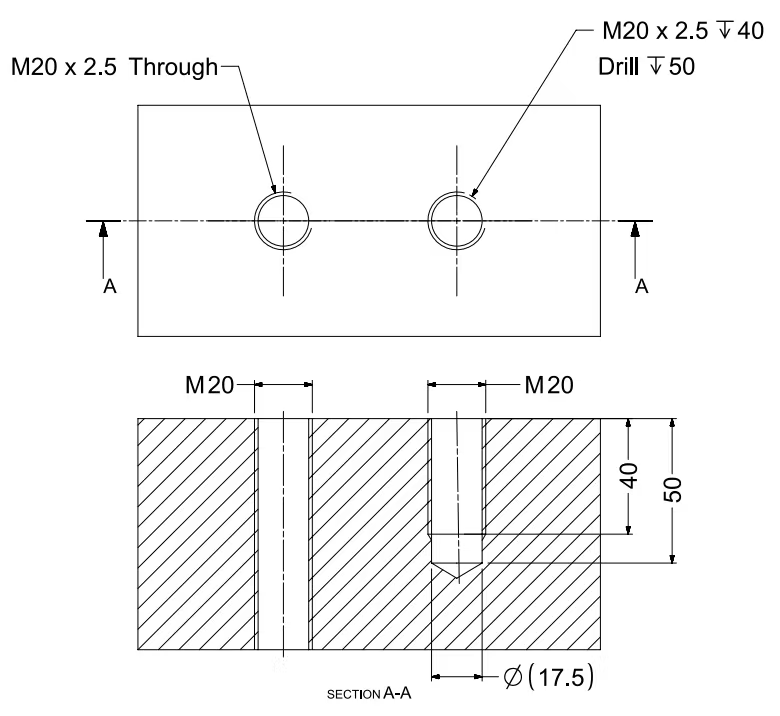
tapped-hole drawing with a symbol for blind holes
The marking "M20 x 2.5" designates the thread pitch and fastener size. The thread tap depth is denoted by the downward-pointing arrow symbol (↧), and the last number denotes the overall hole depth.
What Tools Are Used for Blind Holes?
Drills, taps, and specialized equipment like countersinks, counterbores, and spot facers are frequently used to make blind holes. The particular drilling equipment chosen for blind holes will rely on the size, depth, and kind of material being drilled.
The initial hole in the material is made using drills. A twist drill, which has a pointed head and numerous spiral flutes that help remove the material as the drill rotates, is frequently used for blind holes. The drill bit must be the right dimension for the hole being made.
A tap can be utilized for cutting threads into the opening after it has been drilled. A tap is a specialized tool used to rotate the tool while exerting pressure on the substance to cut threads. It's critical to select the appropriate tap for the hole being made because taps come in a variety of sizes and thread pitches.
In some instances, a recess may be made around the hole's entrance using countersinks and counterbores. This can guarantee that bolts or screws are flush with the material's surface. To make a flat area at the hole's bottom, spot facers can also be used.
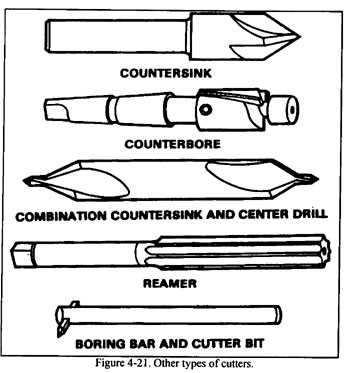
Tips to Get Ideal Blind Hole
Blind holes are a type of hole that doesn't go all across the substance. Although creating the ideal blind hole can be difficult, the following tips can be helpful:
- Use the proper drill bit: When drilling a material, it's critical to select a drill bit that is the appropriate size and style. For precise, clean holes, Brad point or Forstner bits are excellent choices.
- Use a drill press instead of a handheld drill: If at all feasible, use a drill press. You will have greater control and accuracy over the piercing process as a result.
- Mark the depth: Before you begin drilling, use a piece of tape or a marker to indicate the depth of the cavity on the drill bit. This will assist you in preventing through-hole drilling and cutting too deeply.
- Drill a pilot hole first: For holes with a bigger diameter, it's frequently beneficial to do so. This will guarantee a straight hole and aid in guiding the bigger drill bit.
- Use cutting lubricant when drilling through metal to lubricate the bit and keep it from overheating. Additionally, it will result in a cleaner wound.
- Create a blind hole slowly: It's crucial to take your time and create a blind hole slowly. This will guarantee a precise, clean hole and help keep the bit from straying.
- After drilling the opening, clean it out with a vacuum or compressed air to remove any dust or debris.
Blind Hole Application in Machining Industry
In the machining sector, blind holes are frequently used for several purposes. Among the most popular applications are:
Tapping: Blind holes are frequently used when threads need to be tapped into a variety of materials. The blind hole enables the tap to begin in the material without passing all the way through, potentially minimizing distortion or harm.
Counterboring: Blind holes can also be used for purposes involving counterboring. Counterboring entails making a cavity at the apex of an existing hole that is bigger in diameter. This can be used to create an indentation so that the head of a bolt or nut sits flush with the material's surface.
Spotfacing involves creating a flat surface at the bottom of a cavity and can be done with blind holes. This can be used to give a washer or other component a flat area to rest against.
Dowel holes: These holes are also possible to make using blind holes. Two pieces of material can be accurately located and aligned using dowel holes.
Cooling Holes: Blind holes are frequently used to make cooling passages in components, such as engine blocks or turbine blades. These channels may aid in heat dissipation and efficiency enhancement.
Blind Hole Risk and Solution
Blind holes have many uses, but they also carry some special dangers. These consist of Debris, chips, and other materials that may collect in the bottom of a blind hole, trapping them there. Because of this, threaded holes may not be accurate, and chips may conflict with the tooling during machining.
Thread stripping: If the tap or other instrument used to make the thread bottoms out in the hole, blind holes used for threading may become problematic. If the tool keeps turning, it may strip the thread or suffer other damage, necessitating expensive repairs or scrapped components.
Corrosion: Blind holes can accumulate moisture, which over time may cause corrosion and substance deterioration.
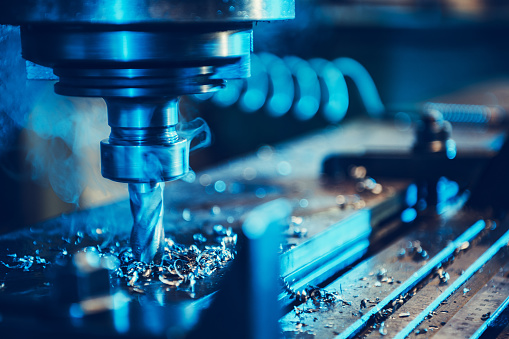
Solution for Blind Holes
Engineers and machinists can use several strategies to lessen the dangers posed by blind openings. These consist of:
Cleaning: It's crucial to routinely clean blind holes with compressed air, solvents, or other cleaning techniques to prevent material buildup. By doing this, you can help prevent chips and other debris from affecting the precision of threaded openings or creating problems with the tooling used for machining.
Threading methods: Engineers and machinists can use specialized tapping methods, such as bottoming taps or roll taps, to avoid thread stripping in blind holes. These tools are made to make threads in openings that are blind without harming the thread or the tool.
Coating: Engineers can use specialized coatings and treatments to shield the material from moisture and other corrosive factors to stop corrosion in blind holes. These coatings could be anodizing, chromate conversion coatings, or other surface treatments that separate the substance from the environment in a protective manner.
What Are Some Other Kinds of Holes Used in Machining?
Numerous different kinds of holes are frequently employed in manufacturing and processing, including:
Countersink holes: Conical-shaped countersunk holes are used to make it possible for screws or bolts to rest flush with the surface of a material.
Counterbore holes: To provide a larger surface area for the fastener head to bear against, counterbore holes, which are cylindrical in shape, are used to enable bolts or screws to sit inside the material.
Tapered holes: To accommodate parts that must fit closely or to permit simple insertion or removal, holes are sometimes designed to have a gradually changing diameter, either increasing or decreasing.
Blind holes are those that are only partially drilled through the material and do not extend to the opposite side.
Thru Holes: Holes that are fully drilled through a material, from one side to the other, are referred to as through holes.
Reamed holes: To increase precision and surface finish, these holes were first drilled, and then their diameter was precisely determined using a reamer.
Spot-faced holes: Holes that have been threaded with a tap make it possible to quickly screw screws or bolts into the substance.
Counter-Drilled Holes: To make it simpler to enter a tool or component, counter-drilled holes are holes that have been drilled to a larger diameter at the entrance of a blind hole.
Stepped Holes: Stepped holes enable the use of parts of various sizes because they have several sections with varying diameters.

Conclusion
Blind holes are a frequent design element in engineering and machining. Drilling, boring, and milling are just a few of the machining processes that can be used to create blind holes. In the machining sector, blind holes are frequently used for tapping, counterboring, cool holes, and dowel holes.
Although creating the ideal blind hole can be difficult, you may follow the above-mentioned tips to get a perfect blind hole. Moreover, Blind hole engineering also presents some special risks that can affect the final product's quality and safety. Engineers and machinists can create accurate, dependable parts that meet the highest standards of quality and performance by understanding the risks connected with blind holes and applying the appropriate solutions. This blog was helpful for you? Do you have any questions just let us know by commenting below?