Welcome to the world of CNC machining!
If you're familiar with the process, you know how complex and nuanced it can be. Today we’re going to focus on a common problem that plagues many machinists: tool bumping. We'll analyze what causes this issue and provide practical solutions for overcoming it.
This article aims to identify and analyze the different causes of tool bumping and their associated consequences. The objective of this blog is to bring about awareness among operators about potential hazards and provide guidelines to help prevent such incidents from occurring.
This post also looks at various approaches used by various companies in order to mitigate the risk associated with tool bumping and thereby provide safer work conditions.
So get your tools ready, and let's dive into the exciting world of CNC machining troubleshooting!
Overview of CNC Machining Center
Computer Numerical Control, or CNC, machining centers allow the automation of specific processes in the manufacturing industry. Using a CAM (Computer-Aided Manufacturing) program to control machine parameters such as feed rate, spindle speed, and tool paths on a computer numerical control (CNC) machine provides operators with greater repeatability and accuracy than manual operations.

The ability to automate these processes also results in less wasted material, improved surface finishes, and reduced cycle times. CNC machining centers work with materials ranging from hardened steel to composite plastics, depending on the setup of the machine.
To perform cutting or shaping operations on these materials, machinists use a variety of tools such as drills, end mills, and taps. Due to the close proximity of the cutting tools and material being cut, these machines are susceptible to tool bumping - i.e., when the spindle makes contact with the material or an outside object during operation, causing damage to both parties involved.
To prevent such occurrences, it is important for operators and maintenance engineers to understand what causes tool bumping in CNC machines and how it can be avoided.
What is Tool Bumping?
Tool bumping is an issue that affects CNC mills and lathes, particularly those with large spindle heights and long tool sticks. Tool bumping occurs when a tool makes contact with either an element of the workpiece or the environment. This leads to scrap parts, tool damage, and higher production costs.
Tool bumping is a common cutting issue in CNC machining centers. This problem affects the quality of the machined part and decreases efficiency while increasing costs.
Common causes of tool bumping include tooltip ground unevenly, incorrect cutting parameters or conditions, wrong tool selection, improper machine setup, excessive feed rate, and lack of machine maintenance, among others.
Causes of Tool Bumping in CNC Machining Centers
Some of the causes are minor, while others require careful attention and direction. Below are presented reasons why this happens and ways to prevent it.
So let’s dig in:
Incorrect Spindle Speed
The most common cause of tool bumping in CNC machining centers is incorrect spindle speed. Incorrect spindle speeds, either too high or too low, can cause the tool to come into contact with the workpiece before the spindle has reached its optimal cutting speed.
Inadequate Chip Break-out
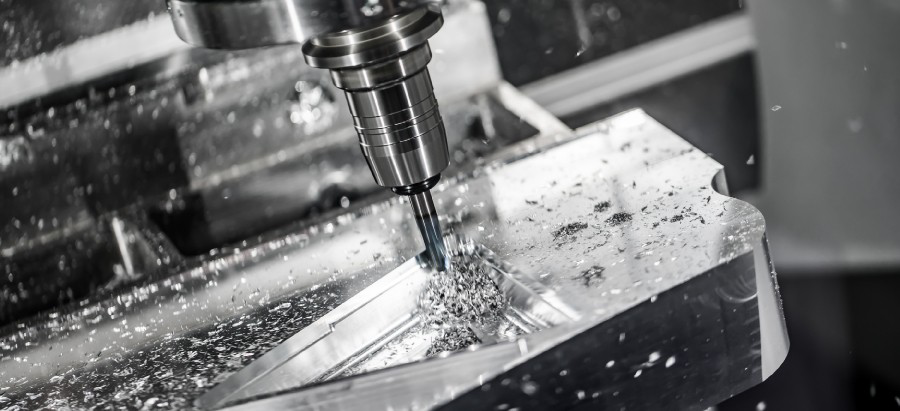
Improper chip breaking can result in a poor surface finish. CNC machine downtime to remove the chips periodically, and higher temperatures at the cutting edge cause tool bumping. Continuous chips are, therefore, not desirable.
To overcome this, you’ve to change the chip or don’t remove the chip periodically, which makes the chip bend.
Wrong Type of Cutting Tool
Tool bumping might suffer if the incorrect cutting tool is used. Edges or corners of the material may be rough, there may be visible cutter traces, there may be raised marks, or there may be signs of burning. This inaccuracy could result in significant tool wear.
Tool bluntness or an incorrect feed speed ratio are two common causes of poor material finishing. Incorrect tool dimensions in terms of size, quality, or compatibility with the material may also be to blame.
Fixing this issue requires picking the appropriate method and environment for processing the given substance.
Programming Errors
Inadequate programming is another frequent issue that causes tool bumping. CNC computers operate every piece of CNC machinery, and poor programming lowers the quality of the manufactured component. It could be because the controller doesn't understand G and M codes well enough.
To fix these problems, fresh operators must be instructed on how to program CNC machines. New operators should be given user manuals and training on motion sequencing and machine operation by machine suppliers or experienced shop floor operators.
CNC Machine Tool Overheating
CNC machining is constantly being used to fulfill the massive order volume. This causes the machine tools to overheat and break down.
The CNC machine can get hotter at over 150 degrees Fahrenheit while running for extended periods of time. It decreases the value of the tool, the precision of the CNC machine, and the longevity of the machine itself.
It's important to keep the machine free of dirt, soil, and other debris on a regular basis to avoid this problem. Clean up any cutting fluids and metal shavings on a regular schedule.
Improper Maintenance
Improper maintenance on the machining center is also a factor that contributes to tool bumping. Lack of regular maintenance on the machine, such as cleaning and lubrication, can lead to wear and tear on the parts of the machine, resulting in irregular performance, which further complicates the process of obtaining optimal results without bumping.
This can be avoided if operators strictly adhere to the machine tools' prescribed maintenance schedule. They should also routinely inspect the airflow and coolant levels (such as with air filters) to guarantee the continuity of operations.
Automatic Tool Changer Problems
When using a CNC machine tool, the automatic tool changer can occasionally give you trouble. To fix this, one must become familiar with each stage of the tool-changing procedure and determine where the breakdown occurred.
First, make that the base, tool holder, gripper arm, support arm, and tool magazines are all in good operating order. Alternately, check the swiveling mechanism as well as the mechanical action of the arm to ensure that it is functioning correctly. Additionally, make sure to keep coolant and chips out of the automatic tool changer and tool holders.
Wrong CNC Machine Tool Partner
Last but not least, selecting a reliable CNC machine tool partner is essential for minimizing breakdowns and mistakes. Incorrect use of a machine tool can have significant consequences for your business.
To overcome this problem, team up with a reputable CNC machine tool supplier that offers a full suite of services following the sale, including in-depth training and servicing.
Machine Vibration/ Chatter
The life of the tool, CNC machine longevity, and machined component quality are all negatively impacted by vibrations that occur while the machine is in operation. The noise it makes will alert you to its presence, which can be rather intense at any time.
In order to fix the problem, you must determine whether the chatter is coming from the workpiece or the tool. To prevent the machining process from resonating with the material's frequency, you can alter the RPM used in the process.
Inappropriate Tool Holder
Please take note that while operating machining centers with spindle speeds in excess of 8,000 rpm, the use of balanced tool holders is mandatory. If your manufactured part isn't properly stabilized, the first thing anyone will notice is vibration marks. The bearings in your spindle will eventually fail, and your tool life will suffer as a result.
In addition to the above-mentioned causes, other problems occur that cause tool bumping in the CNC machining center. Including dull or blunt cutting tools, damaged turbine blades or wheel guards, and an incorrect feed rate.
Additionally, improper installation of cutting tools, tightening torque, etc., result in loose clamping force and cause vibration during machining. This leads to poor surface finish but more frequently results in premature breakage of cutting tools due to poor clamp force setting values.

Impact of Tool Bumping on CNC Machining Centers
The impact of tool bumping can have far-reaching consequences for both productivity and quality in CNC machining centers. Tool grinding time will increase due to the shortening of the life span resulting from wear on the cutting edge caused by bumping incidents.
Furthermore, chips produced by interrupting cuts can cause micro-cracks on surfaces resulting in poor surface finish and damage to both tools and parts which will result in cancellation costs for nonconformance pieces and consequent financial losses to enterprises engaged in CNC machining operations.
To reduce or eliminate the impact of tool bumping on CNC machining operations, certain preventive measures could be implemented, including setting correct parameters that fit each particular application based on guidelines provided by manufacturers.
Correct selection of tools considering the material type and geometry being cut are also considered. Also, proper calibration between spindle motor speed, feed rate, proper maintenance procedure as well as frequent monitoring during operation using testing programs reduces the bumping of the tool.
So any issues arising can be quickly identified before they become more serious problems. Taking these precautionary steps appropriately could personify good practices leading towards improved operational efficiency at CNC facilities across the industrial sector.
Prevention of Tool Bumping in CNC Machining Centers
Preventing tool bumping in CNC machining centers is important for ensuring higher accuracy and efficient production. Poorly managed machine operations can lead to tool bumping, which can be extremely time-consuming and costly to fix.
To reduce the risk of tool bumping, it is important to observe good practices and preventive maintenance measures when using CNC machining centers.
One way to prevent tool bumping is by ensuring that all cutting tools are appropriately secured, fastened, and balanced. This means that machines must be set up with properly tightened clamps, bolts, sleeves, and other components that attach tools to the spindle or turntable.
Tool holders should also be checked regularly for wear and tear before any operation starts. Furthermore, cutting tools must be properly lubricated according to the manufacturer's instructions so that they rotate smoothly during operation.

Aside from mechanical maintenance of machines' components and cutting tools, a stable workpiece setup is also critical in preventing tool bumping in CNC machining centers. Like with any other machine operations, setting up workpieces accurately on the machine table is essential for better accuracy of output product dimensions and shapes.
An improperly secured workpiece can result in unexpected, unintended movements of the workpiece during a CNC milling operation that might cause collet locking devices or other components’ clamping mechanisms to slip off from securing a grinding wheel or an end mill.
Another way to prevent tool bumping errors in CNC machining centers is by choosing appropriate feeds and speeds for each machining operation. According to recommended cutting conditions specified by manufacturers as well as following best practices used among industry professionals alike.
Since poor feeds and speeds often lead to unstable cutting conditions where tools can suddenly move due to amplified vibrations. Cutting forces may be too much for an attachment arm to handle, causing the grinding wheel or end mill to fall off. This makes the surface finish less accurate. So, you need to avoid this.
Uncontrolled runouts suddenly appear even after a production process's completion phase has been reached or cause permanent damage by undergoing certain key parts when being inspected by technical staff and then waiting for the right time before using such parts again, unless they need more repairs that put safety at risk.
The early intervention occurred if precautions weren't taken, resulting in improper technical handling. Keeping a huge audience's attention while examining how things went wrong due to unavoidable distractions tests their capacity to remain composed. The most important thing is to stop using traditional replication protocols and put interest ahead of technology.
Some Other Common Tool Bumping Solutions
To address the tool bumping issue, several solutions exist for working around or minimizing tool bumping in CNC machining centers.
- One solution is to create a process float leaving some extra time in between machining operations which gives some time for the tool’s vibration to die down before it engages with the part again.
- Another strategy is designing fixtures carefully so that there are as few obstructions adjacent to the cutting area as possible; this will reduce the chances of a tool collision when loading and unloading parts from the bed of a CNC mill.

- Furthermore, cutting chamber designs can adjust their height to servo-position their spindles precisely so that they’re always at an optimal distance from their fixtures throughout an operation.
- Regular maintenance can help limit the effects of wear on contact surfaces like spindles and gears, which can lead to increased vibration and, thus, increased likelihood of tool bumping errors.
- Additionally, setting appropriate cutting speeds for different materials also goes a long way toward reducing problems caused by vibrations from suddenly changing material properties mid-operation.
- Finally, ensuring that tools are long enough for each procedure (but not too long) will also help restrict unnecessary movement, which often contributes to poor precision outcomes on CNC machines because it affects spindle stability or chip clearance height significantly during operation cycles.
Frequently Asked Questions (FAQs)
What are the common problems with CNC machines?
There are 5 common problems that occur with CNC machines:
- Chucks And Fixtures
- Overheating
- Operator Training
- Power Supply Issues
- Wrong Tools Or Settings
Which of the following is the cause of faults in machine tools?
These are the cause of industrial machine failure, including
- Bearing failure
- Metal fatigue
- Corrosion
- Misalignment
- General surface degradation.
What causes CNC chatter?
Chatter can occur when there is either too little, too much, or too much fluctuation. Chatter can develop if too many flutes are involved in the cut on a CNC milling machine. You can lessen the resonance vibrations brought on the chip load by using end mills with fewer flutes or variable pitch.
What are the factors affecting the tooling for CNC machines?
There are a wide variety of possible tool configurations for a CNC machine. For example, when our engineer chooses tools, he or she mostly thinks about the following five things:
- The instrument in use
- The substance in use
- The total quantity of machined components
- What the customer needs
- Technical details on the instrument being employed
What are the 4 modes of failure?
There are four failure mechanisms for mechanical devices
- Corrosion
- Erosion
- Fatigue
- Overload
Although the aforementioned failure mechanisms can be found in nature, the particular operating environment of an item may or may not have them.
Conclusion
Overall, tool bumping in CNC machining centers is mainly caused by a variety of factors. These include the improper use of sensor less vector software and the implementation of program errors.
Other potential causes are linked to incorrect setup and configuration, insufficient lubrication, and an over-travel style design. In order to minimize tool bumping in CNC machining centers, operators should practice proper usage techniques and employ error-checking routines in their production programs. Ensure that all settings are accurate to the task at hand and properly lubricate parts.
Additionally, it may be beneficial to choose a design with limited travel. By implementing a comprehensive approach towards preventing tool bumping on CNC machining centers, many companies will be able to improve the longevity of their machines and reduce unnecessary costs associated with such damages.
Now you’re ready to analyze the tool bumping issues, and you can also fix them!