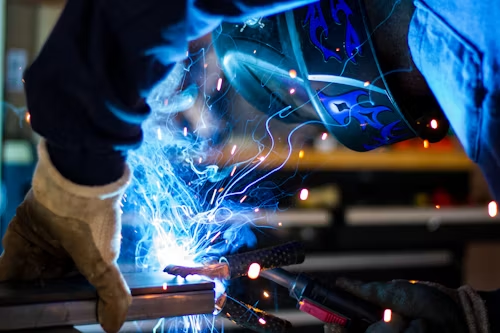
Photo by Rob Lambert on Unsplash
Laser beam welding (LBW) is an inventive technique in fusion welding. An intense laser beam is directed towards the desired gap, providing the heat needed to melt, fill the edges, and complete the joining operation. Noticeably, the LBW's apparatus and functioning differ from traditional fusion welding techniques. The laser beam's focused heat source makes it possible to weld precisely and effectively, producing welds that are frequently of excellent quality and little deformation.
Brief overview of the process
Laser Beam Welding (LBW) is a type of welding in which materials, usually metals or thermoplastics, are joined together using a highly focused laser beam. A laser beam is targeted on the joint area of the materials that need to be welded as part of the LBW process.
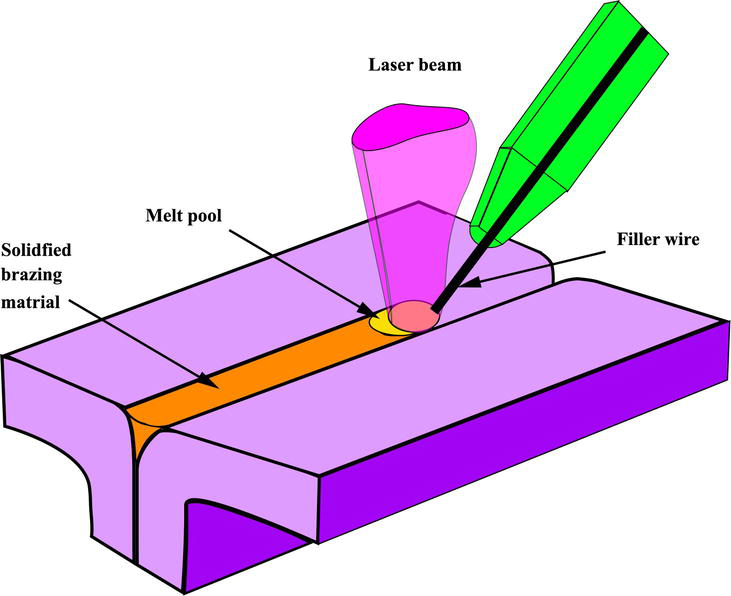
The intense laser light melts the substance, creating a molten puddle. The molten pool solidifies as the laser beam passes over the joint, producing a robust weld. LBW can be carried out in various ways, including conduction welding, which transfers heat via the surface, and keyhole welding, which allows the laser to pierce the material deeply.
Key characteristics distinguishing LBW from other welding techniques
Control and accuracy: LBW provides remarkable control and accuracy, enabling complex welds on small components or intricate geometries. Accurate and reliable welding is guaranteed by the great degree of influence over the laser beam's properties, including power and intensity.
Speed and Efficiency: LBW is suited for high-volume production since it can weld at high speeds. The concentrated heat source decreases heat-affected zone reduction and post-weld processing requirements.
Versatility: LBW is suitable for various joint configurations and a broad spectrum of materials, including dissimilar metals. It's also perfect for welding delicate or sensitive components because of its non-contact nature.
Quality and Strength: LBW normally produces strong welds that are free of flaws like porosity or cracking. Additionally, the procedure reduces residual stresses and deformation in the welded components.
B. Historical Background
The first laser was created in 1960 by Theodore Maiman, marking the beginning of the development of laser technology in the middle of the 20th century. This innovation paved the way for the use of lasers in a variety of industries, including welding. Although the primary use of early lasers was in science and research, it soon became clear that they might also be utilized in industry.
- Evolution of LBW in industrial applications
The 1970s witnessed a rise in the usage of lasers for welding as innovations in laser technology made the procedure more effective and feasible. Early uses of LBW were in the aerospace and automotive sectors when it was essential to have welds with great precision and strength. Electronics, medical devices, and power generation are just a few of the industries that LBW has grown into throughout the years.
Major Significant Stages in the Development of LBW include:
1963: The first reported application of laser welding took place in 1963 when steel sheets were butted together using a pulsed ruby laser.
1965: Laser systems were created in 1965 to be utilized for certain applications that could not be fulfilled at the time by traditional technologies, such as welding vacuum tube interiors and electronic circuits.
1970: High-power CO2 lasers were introduced in the 1970s, allowing for quicker and deeper welding speeds.
1980s: Better beam quality and adaptability were provided by the development of solid-state lasers, such as Nd lasers.
1990s: Improvements in fiber optics and other laser beam delivery methods allowed for more accessibility and flexibility in welding applications.
2000s: The development of fiber and diode lasers with better brightness, which offer more power and efficiency for industrial LBW applications.
II. Principles of Laser Beam Welding
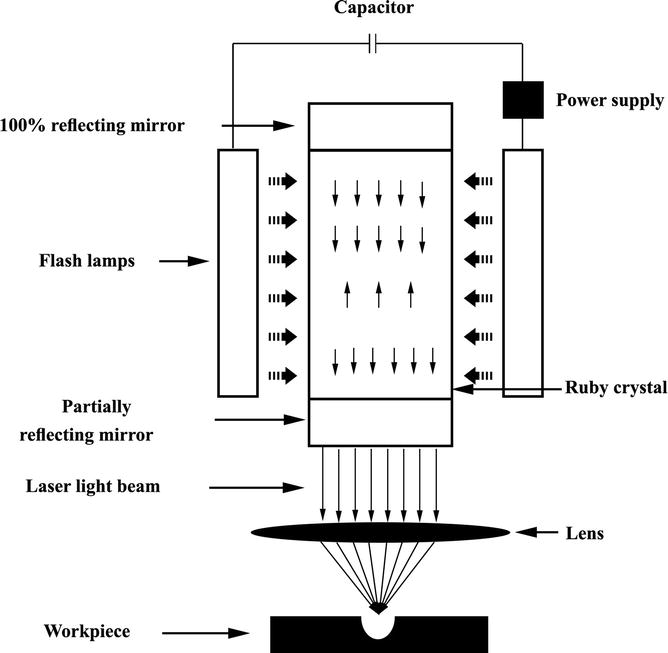
Laser beam welding, or LBW, focuses a concentrated light beam into a tiny area and releases a lot of energy there to ensure precise and efficient material joining. A method used in LBW is called stimulated emission, which involves first excitation of the electrons in a medium (such as a gas, liquid, or solid) to a higher energy state and then instantaneous release of the electrons.
Types of Laser
In welding, a variety of laser types are used, each with unique properties:
CO2 lasers: Known for their tremendous power and capacity to fuse thick materials, these operate by using carbon dioxide gas. They are perfect for both metals and non-metals since they emit infrared light.
Fibre Lasers: These lasers use rare-earth element-doped optical fibers. They are especially well-suited for precision welding of delicate components and provide excellent beam quality and efficiency.
Nd Lasers: These lasers produce near-infrared light by doping a crystal of yttrium aluminum garnet with neodymium. They are adaptable and ideal for a range of materials and applications since they can operate in both pulsed and continuous modes.
Diode Laser: When an electric current flows through semiconductor materials, diode lasers emit laser light. Layers of p-type and n-type semiconductor materials that form a junction make up the active medium. At this junction, electrons and holes recombine to release photons, which produce laser light.
B. Mechanism of Welding
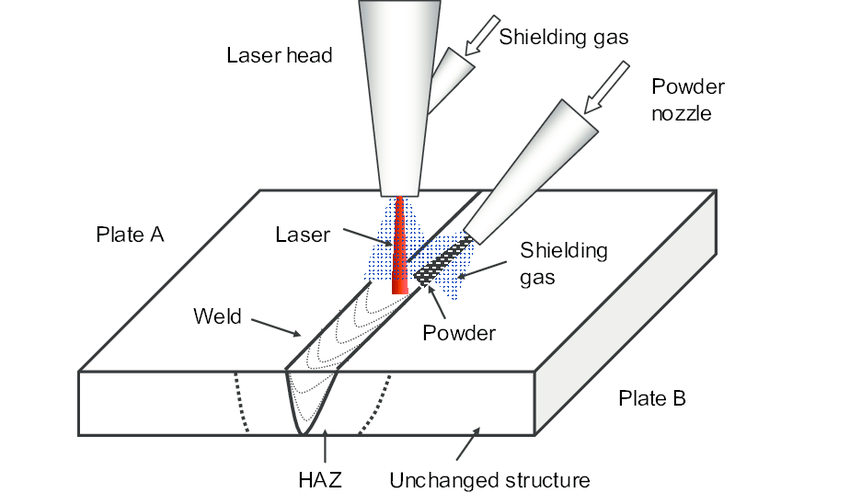
In laser beam welding (LBW), the material and laser beam interact during the welding process. The material melts and forms a pool of weld when the laser beam is directed onto its surface, quickly heating the localized area. Heat production results from the material's absorption of energy, and heat generation is a crucial step in the fusion process. The material undergoes phase transitions from solid to liquid due to this heat, and then solidifies again as it cools, resulting in a strong weld junction.
Types of Laser Beam Welding(LBW)
There are three main forms of laser beam welding (LBW) depending on how they operate:
Keyhole Mode Welding:
Using a high power density, the laser beam forms a tiny, deep hollow in the material, known as a "keyhole" in keyhole mode welding. As the laser moves, it leaves behind a fused seam, and vapor pressure stabilizes the keyhole. High-speed applications and deep penetration welding are perfect for this mode.
Conduction Mode Welding:
This mode is commonly employed for shallow connections to produce a wide and shallow weld because it transfers less energy per unit area (about 0.5 MW/cm2). The laser beam creates a deeper, wider weld pool in the conduction mode of welding. Heat conduction is the mechanism that drives the melting of the material and is mainly absorbed by the surface. For applications needing a smooth surface finish and thin materials, this mode is appropriate.
Conduction/ Penetration Welding:
In comparison to the conduction state, this mode has a higher penetration rate and occurs at a medium energy density per unit area (about 1 MW/cm2). The keyhole in this instance has a shallow penetration and a distinctive aspect ratio (depth/width) of approximately 1. For different spot and seam welding applications, this mode is virtually exclusively used with pulsed Nd: YAG lasers.
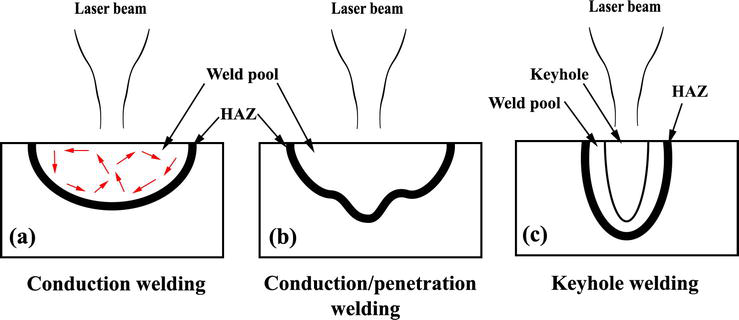
Equipment and Setup
A. Components of LBW System
There are the following basic components of the LBW system which are described below.
Laser source
A high-energy beam needed for welding is produced by the laser source, which is the brains behind the LBW system. Notable varieties comprise CO2 lasers, fiber lasers, and Nd lasers, each providing distinct benefits concerning power, efficiency, and compatibility with various materials.
Beam delivery system
Systems for guiding laser beams from sources to workpieces are called beam delivery systems. Accurate direction and focus of the beam are maintained by the use of mirrors, lenses, and optical fibers. Ensuring constant welding quality requires proper alignment and maintenance of the beam delivery system.
Workpiece positioning system
Accurate workpiece location is necessary for laser welding to be successful. Automated stages, robotic arms, or CNC machines that can precisely move the workpiece by the welding path that is set into the system are frequently used in this type of technology.
Monitoring and control systems
These are used to guarantee the best possible welding conditions and quality. These systems may comprise cameras, sensors, and software that monitor and modify in real-time to maintain consistent welding performance based on characteristics including beam power, focus, and alignment.
B. Setup Procedures
There is following setup procedure to follow for laser beam welding.
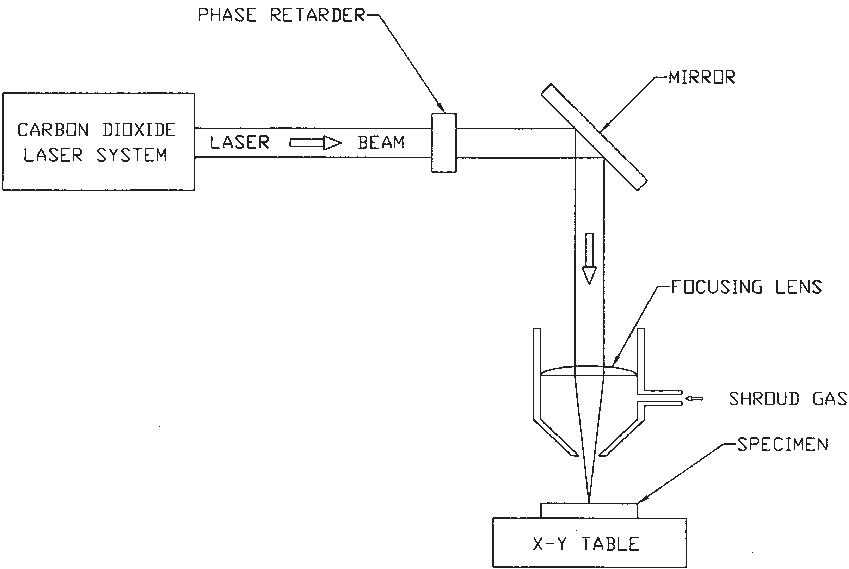
Laser welding set-up Schematic diagram
Preparing the workpiece
The workpiece must be properly prepared. To prevent pollutants like oils, oxides, or dust from interfering with the welding process, the surfaces must be cleaned. To improve the weld quality, it could occasionally be required to pre-heat or add a coating. It also takes proper fixturing to keep the workpiece firmly in place.
Aligning the laser
To achieve the necessary weld quality, the laser beam must be precisely aligned with the part to be welded. This can entail utilizing alignment tools and modifying the beam delivery mechanism.
Safety precautions
To shield operators from laser risks, safety precautions must be put in place. This entails making sure the laser area is appropriately designated and enclosed, as well as utilizing the correct personal protective equipment (PPE) and safety interlocks.
IV. Difference of Laser and Electron Beam Welding
The precision and effectiveness of laser and electron beam welding make them extremely popular advanced welding techniques across many sectors. Both techniques use high-energy beams to fuse materials together, although their benefits, uses, and procedures are very different.
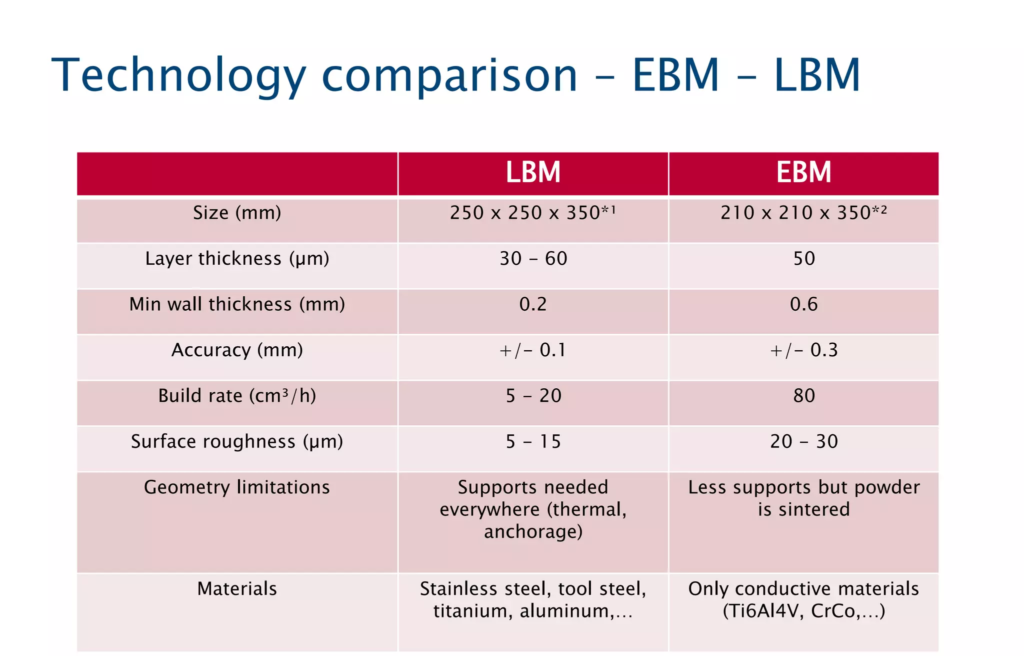
Laser Beam Welding:
A laser beam with a high degree of concentration is used in laser welding to melt and fuse materials. This method is renowned for its accuracy and capacity to produce strong, clear welds with little deformation.
The fact that laser welding may be done outside in a controlled environment makes it useful for a range of industries, including the production of automobiles, aircraft, and medical devices. One of the main benefits of laser welding is its exceptional precision in joining small, sensitive parts, which makes it perfect for micro-welding purposes.
Electron Beam Welding:
In contrast, electron beam welding creates heat and melts the materials being welded using a concentrated, high-velocity electron beam. This is a more complicated and expensive method than laser welding because it needs a vacuum atmosphere to keep the electrons from scattering.
Nonetheless, deep penetration welding with negligible contamination is made possible by the vacuum atmosphere, producing incredibly high-quality welds. Thick materials are well suited for electron beam welding. Its application includes those in the nuclear, aerospace, and power generation industries, where weld quality is crucial. They are best suited for electron beam welding.
Important Features
Environment: While electron beam welding needs a vacuum, laser welding can be done outside.
Depth of Penetration: Deeper penetration is made possible by electron beam welding, which qualifies it for thicker materials.
Precision: Laser welding has a great degree of precision, making it perfect for small and sensitive parts.
Cost: Because laser welding requires less setup and running equipment, it is typically more economical.
V. Which Important Factors Determine a Laser Weld's Quality?

Photo by Museums Victoria on Unsplash
Numerous significant elements impact the quality of a laser weld. Here are a few important things to remember:
1. Power:
The laser's power must be sufficient to pierce the materials that are being fused. Weak welds can result from insufficient power, while excessive melting or vaporization might be caused by insufficient power.
2. Composition of Material :
The weldability of the materials is influenced by their chemical composition. Depending on the alloy and metal, different laser settings may be needed. Thicker Materials require more power and distinct focus settings than those that are thinner.
3. Welding Speed
The heat input and cooling rate are dependent on how quickly the laser travels along the weld path. For thicker materials, slower speeds could be required, while higher speeds can minimize heat input and distortion.
4. Spot Size:
Smaller spot sizes lead to increased energy densities, which make deep, accurate wells possible. The ideal spot size for the laser should be determined by the thickness of the material and your preferred weld pattern.
5. Shielding Gas:
To protect the weld from air contamination, gases like nitrogen, argon, or helium are utilized. The shielding gas flow rate needs to be sufficient to shield the weld pool without disturbing it.
6. Joint Design:
The geometry of the joint must be appropriate for laser welding. Butt, lap, and fillet joints are examples of common geometries. Joints that are neat, aligned, and fitted correctly promote better fusion and lower the possibility of cracks.
7. Cooling Rate:
Weld microstructure is impacted by the cooling rate. Higher strength and a finer microstructure can be achieved by rapid cooling, but a coarser structure may be the outcome of slower cooling.
8. Post Heat Treatment:
Weld mechanical characteristics can be enhanced and stresses relieved by post-weld heat treatments.
VI . What Effect Does Laser Speed Have on Laser Welding Quality?
Some parameters impact the quality of laser welding when there is a change in laser speed. Let’s discuss it in more detail here.
1. Heat Source
There is less heat input and a smaller heat-affected zone (HAZ) when the laser moves rapidly. As a result, there is less chance of thermal distortion and flaws like warping and cracking. Higher heat input from slower speeds may end up in a larger HAZ. This can raise the danger of heat distortion and other flaws, but it may also improve penetration in thicker materials.
2. Penetration of Weld
Shallower weld penetration may be the outcome of higher laser travel speeds. This works well for thin materials or applications that don't need deep penetration. Deeper penetration is possible because slower speeds give the laser more time to interact with the substance. In this way, thicker materials can be welded better.
3. Weld Bead Profile:
The weld bead becomes thinner and more concentrated as it travels faster. For precise welding and producing fine seams, this can be helpful. Weld beads that are wider are produced at slower rates, which may be required to fill in spaces or reinforce joints. On the other hand, this may potentially result in an excessive accumulation of material and possible overflow.
4. Rate of Cooling:
Quicker welding speeds lead to faster cooling rates, this may improve the weld metal's morphology and boost its strength and hardness. A coarser microstructure may materialize as a result of slower speeds allowing for more gradual cooling. While the weld's toughness and ductility may increase, the hardness may decrease.
5. Defect Generation
Fast welding can lessen the chance of flaws like porosity and cracking since there is less time for heat stresses and gas entrapment to occur. Prolonged exposure to heat can lead to flaws such as oxidation, porosity, and cracking. Delays in welding speed can exacerbate this danger.
6. Surface Finish:
Since there is less time for the molten material to flow and generate imperfections, faster welding rates frequently produce a smoother surface finish. Weld ripples and possible oxidation marks may be more noticeable on a surface finish that is rougher due to slower motion.
7. Compatibility of Materials
Variations in the speed of the laser cause distinct reactions in different materials. For example, steel can be welded successfully at faster speeds, whereas reflective materials like aluminum could require slower speeds to obtain appropriate penetration.
8. Production Effectiveness
Cutting cycle durations and accelerating the laser welding speed can greatly improve production efficiency. Whereas slower speeds have the potential to enhance some aspects of weld quality, they can also raise expenses and reduce production efficiency.
VII. What Types of Materials Can Be Laser Welded?
A high-precision technique called laser welding can be used to fuse different materials with amazing strength and accuracy. This technology offers several benefits over conventional welding techniques. The following is a list of materials that can be successfully laser welded:
Metals:
Laser welding is very suitable for metals, it is widely used in a variety of industries, including aerospace and automotive. Crucial metals consist of:
Steel: Lasers are frequently used to weld carbon and stainless steel. Precise control is provided by the process, which is essential for thin-sheet and high-strength applications.
Aluminum:
Aluminum has low weight. So, It may be laser-welded to create robust joints with little distortion from heat.
Titanium: Titanium has a high strength-to-weight ratio and resistance to corrosion. Frequently laser-welded for vital aeronautical and medical applications.
Alloys based on nickel: The laser's ability to accurately control heat input is beneficial for these materials, which are frequently utilized in high-temperature situations.
Polymers:
In addition to working with metals, laser welding is also useful with some polymers, which are being utilized more and more in a variety of industries. To create a firm bond, this procedure includes melting the plastics:
Polycarbonate (PC): PC can be laser-welded to create high-strength joints. PC is recognized for its durability and optical clarity.
Polypropylene (PP): It is a common thermoplastic that may be laser welded; it is frequently utilized in consumer products and automotive parts.
Acrylic: For applications needing both strength and clarity, acrylic can be laser-welded due to its optical transparency.
Composite Materials:
Composite materials, which consist of two or more distinct materials, can also be laser welded, however because of their heterogeneous character, the procedure is more difficult:
Fiber-Reinforced Composites (FRCs): These materials are frequently utilized in the automotive and aerospace industries, but maintaining the integrity of the reinforcing fibers requires exact laser control.
Metal Matrix Composites (MMC): These composites take advantage of laser welding's capacity to manage several material properties within a single joint by combining metals with ceramic or polymer matrix.
Glass
The glass must be precisely controlled when being welded with a laser to ensure that there is no thermal stress or fracture during the melting process. For strong and clear optics applications this method may be employed.
Silica Glass: It is frequently used in optical and electrical applications. To guarantee strength and optical clarity, silica glass can be laser-welded.
Borosilicate Glass: Borosilicate glass, which is used in science and industry, is fused with lasers to create strong joints because of its remarkable temperature resilience.
Ceramics:
Conventional Ceramics: Alumina and zirconia are two materials that can be laser welded to form strong links, but because ceramics are brittle, this procedure needs to be done carefully.
Advanced Ceramics: High-tech applications include sophisticated ceramics, which can be laser welded for applications like electronics and medical devices that need precise joins and exceptional endurance.
VIII . Is Laser Welding a Faster Technique Than Other Welding Techniques?
The high processing speed, automation possibilities, and effectiveness in reducing prep and post-weld processing time make laser welding generally faster than many traditional welding procedures. For industries where precision and great productivity are essential, these benefits make it a desirable choice.
High Processing Speed: When compared to traditional welding techniques like TIG (Tungsten Inert Gas) and MIG (Metal Inert Gas) welding, laser welding can generate greater welding speeds. Rapid material melting and joining are made possible by the high energy density of the laser beam.
Minimal Preparation: Laser welding frequently requires little surface preparation, in contrast to other techniques that could call for thorough cleaning, beveling, or pre-heating.
Single-Pass Welding: laser welding frequently completes joins in a single pass, even for thick materials. The cycle time is greatly shortened as a result.
IX. Which Safety Measures Are Crucial When Using Laser Welding Equipment?
Several important safety precautions need to be followed when utilizing laser welding equipment to protect both the area around it and the operators:
Protective Eyewear: To shield their eyes from dangerous laser radiation, operators must put on safety glasses or goggles designed specifically for use with lasers.
Laser Enclosure: To avoid unintentionally coming into contact with laser beams, enclose the area used for laser welding. To keep the laser radiation contained, use the proper drapes or barriers.
Ventilation: To remove hazardous gases and fumes produced during the welding process, make sure that there are adequate ventilation or fume extraction devices in place.
Warning Signs: Make sure that any possible hazards and the presence of laser equipment are marked with warning signs.
Equipment for personal protection (PPE): To guard against burns, sparks, and other physical risks, use the proper personal protective equipment (PPE), such as gloves, aprons, and face shields.
Frequent Maintenance: To guarantee the laser welding equipment is operating safely and effectively, perform routine maintenance and safety inspections.
Laser Classification: Recognise the laser class that is being used and adhere to the particular safety precautions that go along with it.
Operators can reduce the dangers involved with laser welding and preserve a safe working environment by adhering to these safety precautions.
X. Advances in Laser Beam Welding Technology
Here are some current advances in laser beam welding. We will explore each one step by step.
Technological Developments in Laser Beam Welding
A. Development of Laser Source:
- Improvements in Laser Sources: High-power lasers that can deliver more energy efficiently have been developed as a result of recent improvements, enabling deeper and faster welds.
- Developments in Fibre Laser Technology: Compared to other laser types, fiber lasers offer more precision and require less maintenance due to their better energy efficiency and beam quality.
B. Automation and Robotics:
To improve accuracy, repeatability, and productivity in automated production processes, laser beam welding systems are being more and more combined with robotic arms and CNC machines.
C. Hybrid Welding:
This welding approach integrates laser beam welding (LBW) with other welding processes, such as MIG or TIG welding, providing the advantages of both procedures, including enhanced adaptability, decreased flaws, and greater weld durability.
D. Simulation and Modeling:
Improvements in computational modeling make it possible to create predictive models that replicate the performance and quality of welds, improving process planning and optimization.
XI. Is Laser Beam Welding More Expensive Than Other Welding Techniques?
Although it can be more expensive than other welding methods, laser beam welding (LBW) can be more cost-effective in certain situations. Due to the sophisticated technology and accuracy required, laser welding equipment has a hefty initial investment. Comparing laser welding to more conventional techniques like MIG or TIG welding, the initial outlay is much higher due to the high cost of laser welding equipment and maintenance.
Nevertheless, LBW has several benefits that eventually outweigh these expenses. It offers great control and precision, resulting in little distortion and a reduction in the amount of post-weld processing needed. This effectiveness can speed up production and lower labor expenses. Moreover, productivity can be increased by using laser welding to join a variety of materials and thicknesses, frequently in a single pass.
XII. Advantages of Laser Beam Welding
For certain applications, Laser Beam Welding (LBW) is the preferable method because of its multiple benefits. Some of its advantages are mentioned below.
Excellent Control and Precision
With laser beam welding, heat input may be precisely controlled, resulting in less deformation and a small heat-affected zone (HAZ). High-quality welding in complex and sensitive components is made possible by this accuracy.
Rapidity and Effectiveness
Comparing the approach to conventional methods, higher welding speeds are possible in this process. So, It is also ideally suited for automation, which raises productivity and lowers labor expenses.
Flexibility:
Metals, polymers, ceramics, and other materials can all be joined together using a laser beam welding machine. It is a flexible option for a range of industries since it works particularly well for intricate geometries and delicate parts.
Welding quality:
The welds created by laser beam welding have a gorgeous polish and are robust and dependable. As a result, less intensive post-processing is required, saving time and money.
No-Contact Process:
The LBW procedure minimizes wear and tear on equipment and lowers maintenance expenses because it is a non-contact method.
XIII. Limitations and Challenges
The drawbacks and difficulties associated with laser beam welding
High Launch Expenses
Considering the expense of setup and equipment, laser beam welding requires a large initial investment. However, upkeep and repairs require trained personnel, which might result in significant maintenance and operational costs.
Technical Requirement:
High-tech equipment and technical expertise are required for the procedure since it needs exact control and alignment. In addition, if porosity and cracking are not well controlled, there is a chance for flaws.
Considerations for the Material
It can be difficult to laser weld some materials. It might be challenging to weld materials with high thermal conductivity or high reflection efficiently. The procedure is made more difficult by the requirement for proper joint fit-up and preparation for successful welding.
Safety Precautions:
There are serious safety concerns associated with high-power lasers, including the possibility of burns and eye injury. It is crucial to have appropriate safety procedures and protective gear to reduce these dangers. Laser welding can produce vapors and fumes that need sufficient ventilation to guarantee a safe working environment.
Operator Expertise:
To produce the best outcomes, proficient operators are needed to handle the complex equipment and adjust the welding parameters.
XIV. Applications of Laser Beam Welding
1. Automotive Industry:
The automobile industry uses a lot of laser beam welding to assemble different car parts, like body panels and structural components. The method is perfect for combining lightweight materials, such as aluminum and high-strength steels, which are being utilized more and more to increase safety and fuel economy.
2. Aerospace Industry:
Laser welding is used in the aerospace industry because of its accuracy in joining crucial fuselage and structural components. It is also utilized in high-performance engine and turbine parts, where the accuracy and robustness of the welds are essential to the efficiency and safety of operation.
3. Electronics:
In the electronics industry, laser welding is used for micro-welding, which allows for the exact connecting of small components and circuits. For electrical gadgets to function properly and be dependable, this is crucial.
4. Medical Device Manufacturing:
Laser welding is a common process in the medical device industry for the fabrication and assembly of implants and medical devices. Producing high-quality, biocompatible devices depends on the process's cleanliness and precision.
5. General Manufacturing
In general manufacturing, laser beam welding is also used to create tools, machinery, and consumer goods. It is a useful instrument for making a variety of things with high precision and little post-processing because of its efficiency and adaptability.
6. Mold Repair and Fabrication
Damaged or worn molds can be fixed with laser welding. Because of its extreme precision, material may be applied precisely where it is needed to restore the mold to its former shape without damaging the vicinity. It is possible to create mold-complex geometries that are challenging to do with conventional welding techniques.
Conclusion:
A wide range of materials may be welded with great precision and speed due to the highly developed and adaptable laser beam welding process. It is perfect for intricate and fragile components due to its precise control, which produces little distortion and a small heat-affected zone.
Although there are certain initial expenditures, technical requirements, and material limits, the advantages in terms of weld quality and efficiency frequently outweigh these disadvantages.
In sectors where high performance and dependability are essential, such as the automotive, aerospace, electronics, medical device, and mold fabrication industries, laser beam welding is extremely beneficial.
Do you have any thoughts to share about this blog? Let us know by commenting below.