Introduction
The industrial revolution is one of the rapid transitions in technological advancements that we are experiencing as the Centuries change. The benefit is that we get to enjoy the excellent pros that come with it.
Innovations are upgraded almost every fortnight, all to build technology solutions and improve the effectiveness of those already in existence.
Technology in Machining
Like in other aspects of life, technology has prompted the emergence of different techniques to perform tasks including in the industrial sector.
CNC machining is one such reliable innovation employed in industrial machining.
It stands for Computer Numerical Control machining.
Machining involves processes for subtractive manufacturing to build the desired output/workpiece.
Machining processes include drilling, cutting, turning, and milling using specialized equipment.
As the name suggests, CNC machining is widely based on the use of intelligent technologies and computerized technology to build custom-designed parts.
Unlike manual machining, CNC systems are automated, hence offering speed, higher production rates, and precision.
Several operations can be accomplished with CNC machining, including milling, drilling, boring, cutting, and lathe applications.
Let us explore one of the trends in intelligent machining; gantry machining.
What is Gantry Machining?
Gantry machining is a type of machining method which, based on its structure, uses an overhead spanning (bridge-like) framework and is designed for multi-axis operations.
Like we saw earlier, the goal is achieving effectiveness and efficiency in building a quality and unique workpiece or desired end-product.
CNC gantry machines, therefore, utilize the gantry design involving detail-oriented procedures to achieve output through machining processes of drilling, cutting, turning, and milling.
Types of CNC Machining Centres
Machining centers can be classified as either vertical, horizontal, or gantry types based on the structure. The significant difference between the three types is the orientation of the spindle.
For the horizontal machining centers, the blade-mounted spindle machine workpieces horizontally. This type can allow for machining on four surfaces of a workpiece when a four-axis machining center is used. The orientation also allows chips to fall to the ground, thus preventing the accumulation of chips on the workpiece or having them dig into the blade.
In the vertical type, the blade-mounted spindle machines workpieces vertically, enabling triaxial machining on a workpiece.
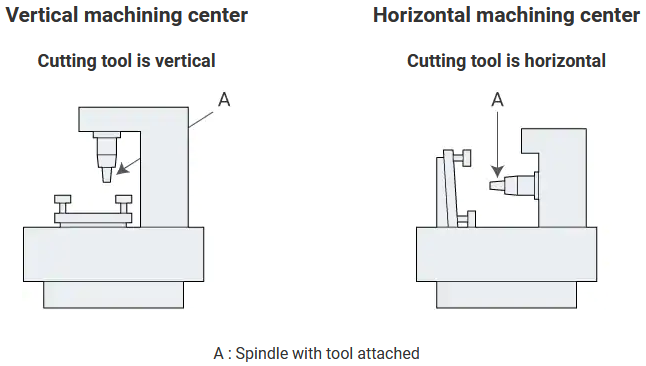
Figure 1: Comparison between horizontal and vertical machining centers
Gantry-type Machining Centres
The gantry system is more complex than the conventional vertical and horizontal types. The overhead bridge-like structure in the gantry machining system holds the spindle, which is mounted on the ceiling of the framework then facing downwards. It makes it possible to machine large workpieces in five different axes to obtain precision.
CNC gantry-type machining centers comprise the main body, which is usually equipped with some key but optional accessories. These include tool magazine, power tool turret, CMM (coordinate measuring machine), ATC (automatic tool changer), and a multi-axis worktable, to name a few.
The cycle time of the CNC gantry-type machining center is shortened by a significant range due to a power turret.
In the current industrial era, the CNC gantry type machining center is primarily used in several industries that require strict machining accuracy.
Gantry Type Machines
The gantry design is well featured in machining tools to perform different types of operations.
Some specialized equipment that employs computerized technologies for high duty-cycles processes relies on the gantry for smooth operations.
The commonly used gantry-type machines available in the modern-day industry include:
-Gantry type Milling Machine
- Gantry type Cutting Machine
Let us discuss in detail and understand how some of these gantry-type machines operate.
Gantry type Milling Machine
Milling is a machining operation in which a rotating tool with multiple cutting edges is moved slowly relative to the material to generate the required texture and geometry, either a plane or straight surface. The feed and cutting speed achieve relative motion during the process. During milling, the direction of feed motion and the tool's axis of rotation form a perfect 900.
There are two forms of milling: face and peripheral milling.
The gantry milling machine, also known as gantry milling, consists of a gantry frame and a long horizontal bed (working bench). The surface of a workpiece can be machined simultaneously with multiple milling cutters using this machine. The machine is suited for large workpieces required in batches and mass production. They are also used to process unique parts and space surfaces.
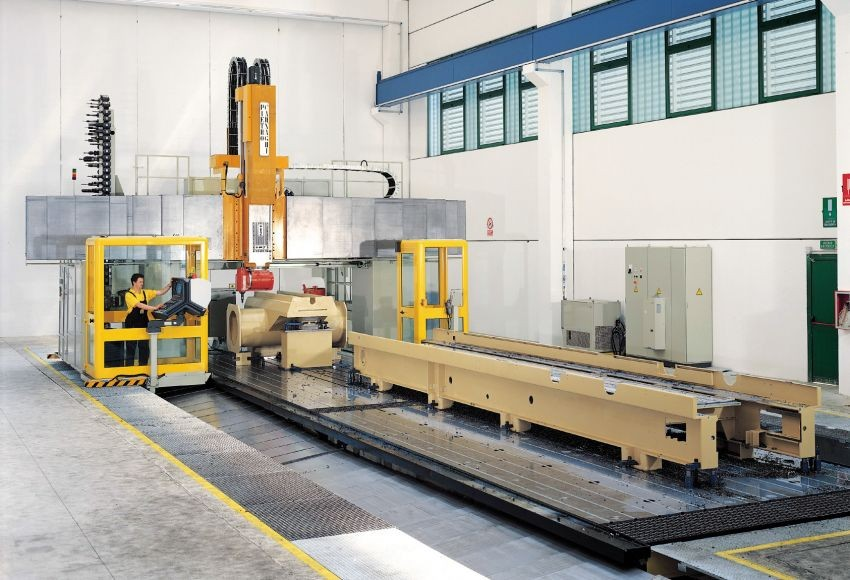
Figure 2: A operator controlling a Gantry milling machine
Key Features of the Gantry milling machine
It is an innovative technical solution whose design comprises an assembly of massive structures, with the movable portal sustained by hydrostatic guideways.
Some of its available features include:
- high-quality Meehanite cast iron structural parts to make it more robust
-machine milling head with cross ribs to improve overall processing stability and rigidity
-strengthened gantry pillar with ribs to improve cutting rigidity
-thickened structural base to increase stability and avoid vibrations
- guideways distributed on the front and top of the beam
- high precision roller screws to improve the machine accuracy and transmission rigidity
- high rigidity belt spindle
- High-speed automatic tool changer
- Auto chip conveyor
- 3 axis precision protective cover
- CNC controls to control the three-dimensional space milling process
Like a majority of equipment, the gantry machine is customizable, and various accessories for milling operations accompany the structure. The floor plate length, for instance, is modular and can be defined based on the customer's needs. An additional turning table may be included to meet some machining requirements.

Figure 3: TAICNC's Gantry Milling Machine
Operating Concept of Gantry milling machine
Machines from different manufacturers use varying working mechanisms for the ultimate operation of the equipment. Workpieces are usually mounted on the table and fed to the machine longitudinally.
The frame has a column and top beam, which can be moved up and down along the guide rails. The machine can have one or two milling heads, each with vertical spindles on the beam for lateral movement along with the beam guides. A horizontal spindle can also be mounted to provide for lifting movement along with the column guide.
In that case, several surfaces can be machined at the same time.
One example of operation mechanisms is machines that allow operation with a pendulum concept. In this case, it has two separate areas on the floor table; one protected machining area with portable enclosures and one area to set up the part that is accessible with bridges along with the guideway covers. This allows flexibility that essentially validates the machine's capability for mass production.
Some of the variants of the gantry machines can perform combined operations. These include:
Gantry boring and milling machine
As the name suggests, it can perform both boring and milling operations. The top beam is equipped with two heads: a milling and a boring milling head. The sleeve or ram has a motion adjustment device and can be used for axial motorized feed.
Gantry drilling and milling machine
Depending on the desired operation, a drilling or milling cutter can be loaded on the powerhead. It has X, Y, and Z-axis guide rails to enhance movement in the three-dimensional space. The gantry carriage is clamped onto the X-axis rail, the Z-axis guide rail is mounted on the gantry, and the y-axis guide rail is mounted on the beam.
Classification of gantry type milling machine
These can be categorized as follows
- By capability
It can be classified as either medium, light, or heavy /super heavy gantry milling.
- By form
Whether or not the gantry is moving, these can be categorized as the bridge-type/ a mobile gantry type or a gantry fixed table mobile type. A majority of the milling machines are usually the fixed type.
The bridge-type gantry milling's unique features are a small footprint and a large carrying capacity. The gantry can run up to 20 meters, making it possible to machine heavy and long workpieces easily.
Based on the beam movement on the column, we have a subclass with two types: fixed beam, the moving beam type, and the overhead type, which is a beam moving on the elevated bed.
- By system
This category is based on the operation and control system and is classified into CNC and the ordinary type.
One button conversion type is also existent in the market and its more practical and flexible. In other words, they are digital intelligent gantry milling with ordinary milling and CNC milling.
Performance characteristics
The gantry milling machine offers all-around performance on three-axis, high efficiency, and convenient operation.
However, the specific performance characteristics vary depending on the technology used for the different models from different manufacturers.
Let’s take a case of the SK series three-axis CNC gantry milling. Its performance characteristics include:
- It adopts a three-axis CNC system that is programmable and can also be operated manually using the expansion panel in the actual machining process.
- The milling head on the side is equipped with a V5 gantry milling head containing an independent lubrication device. It adopts a frequency control system, and an ordinary reducer drives the lifting.
- The vertical milling head has a TX400 heavy-duty gantry head and a rigid double rectangular guide rail.
- The horizontal bed is advanced and retracted, and the vertical milling head has a Taiwan ball screw driven by a servo motor.
- It has a synchronous wheel and a timing belt.
- Has specialized beam lifting safety interlocking device to ensure the repeatability of the machine tool.
- Hand-held electronic handwheel unit to ensure ease of setting the three-axis tool.
- The station standard cycloid pump group has a standardized lubrication mechanism with a low failure rate.
- The milling head has a mounted ball screw, a motor drive, and a pneumatic broach device for machine automation.
Gantry type Cutting Machine
It is a machine with a gantry/ bridge-like design equipped to move cutting torches on both the X and Y-axis. The gantry forms the X-axis, while the gantry's rail moves in the Y-axis.
When both axes are motorized, and motion in each is coordinated simultaneously, the cutting torch can be moved in any pattern to cut large and thick steel plates.
The X-axis rails/ guiding systems support the equipment mounted on it and provide accurate motion of the machine. The rails on the X-axis tend to be larger than those on the Y-axis, which only carry the cutting tool and small carriage.
The equipment may have either one or many tool carriages, depending on the model and manufacturer. There can be one motor for each carriage, or they can all be driven by one motor in the Y-axis when they are all connected.
The common cutting technologies applied in the industry are plasma and oxy-fuel cutting.

Figure 4: Example of a Gantry type CNC cutting machine
Height Adjustment System in Gantry Cutting Machines
To ensure a high-quality cut, an accurate distance should be maintained between the cutting nozzle and the steel plate, which is the workpiece. Maintaining stability of the separation distance or the height of the cutting torch throughout machining may be challenging to be manually achieved. This is because the workpiece's flatness or straightness may not be constant, or the cutting environment may be unsuitable.
The height required for the desired cut varies for different materials, thicknesses, and conditions. It is, therefore, an element the requires to be closely monitored and controlled for quality output. Gantry plasma cutting machines are designed to control this height automatically.
Key Features of the Gantry CNC cutting machine
- It supports remote control systems and nesting software.
- Has hybrid servo motor to ensure precision in sharp angle cutting quality
- The track length can be adjusted accordingly to suit the different requirements
- It can be equipped with a fume extractor
- Has the optical height adjustment controls for plasma application
- Rigid support structure for the rail mounting can be customized on need basis
Pros of the gantry type Cutting machine
- Operation is quick and easy.
- Given an adjustable cutting torch feature, the machine design offers control keys to regulate movement. The system has safety parameters making operation very efficient and convenient for the operator.
- Durable and professional design.
The material of the keys and buttons is rigid and crystal hence very clear to see. Therefore, the operator cannot misinterpret the control keys due to rubbed-off stickers and labels on the buttons. The host body adopts color technologies that are durable and build the aesthetic of the equipment.
- Rigidity and stability of the machine
The component materials used to build the machine are of high quality. For instance, the horizontal rails are made of precision cold-pull guide plates, the vertical guide rails are made of precision-processed rails (heavy rails), and the deceleration devices are imported precision gear reducers for same-way or mirror cutting.
- Simplicity in graphics programming
The graphics for the cutting are pretty straightforward as some of the applications require a direct input of the programming codes. It is easy for an ordinary operator to acquire the skills through simple training.
- Easy operating mode
The screens remind various operating methods; hence any keen operator can efficiently run the process.
- Higher reliability design
- It has a simple maintenance requirement
There is a working status indicator light on each module; hence any fault in the system can easily be pointed out and necessary action taken. The modular design directs the lamp replacement modules hence convenience in maintenance.
- Simple bulk cutting function
Cutting machines can implement automatic sorting of graphics. Operators only need to input the programming codes then the orientation of cutting quantity and mass continuous automatic cutting can be realized.
Applications of Gantry type Cutting machines
It is widely used in machine manufacturing, bridge construction, shipbuilding, power industries, pressure vessels, construction machinery, mining machinery, power, steel, and other industries.
How to avoid errors in machining
Precision testing of the machine tools is a sure way of ensuring obvious errors are avoided during machining.
Errors during machining result in distortion of the desired shape or quality of the workpieces. They vary from one machine tool to another. Common errors include straightness errors, tilt errors, misalignment of workpieces, and repetitive positioning errors.
What affects the machining accuracy of workpieces in machine tools?
- Geometrical form error of the tool and its misalignment on the machine.
- Misalignment of the workpiece on the work table during machining.
- Machining principle’ error of the machine tool.
- Vibration, deformation, and wear of the machine tool and the workpiece system during the cutting process.
How to identify reliable manufacturers
Given the increasing demand for efficient technologies, manufacturers have increased. It may be challenging to differentiate the legit manufacturers from the fake ones. Reliable manufacturers are those in legal possession of legitimate technology and are certified for compliance with international quality standards.
It helps to do background research on the capability and features of the equipment in question and conduct a comparative analysis of what different manufacturers are offering.
Conclusion
A combination of CNC machining and gantry design system is a sophisticated yet efficient technology employed to ensure accuracy, precision, and consistency in the output of the machining process. For quality cuts on complex workpieces and in large quantities within a short time, you need not look any further; gantry machining is the way to go!