The manufacturing world faces constant pressure to produce complex parts faster, with tighter tolerances and fewer defects. Traditional manual machining simply can't keep up with these demands, leaving businesses struggling to compete in precision-driven markets.
CNC machining solves these challenges by using computer-controlled automation to transform digital designs into physical components with exceptional accuracy. Modern CNC systems can repeatedly produce identical parts with tolerances as tight as ±0.001mm, eliminating human error while dramatically increasing production efficiency.
A CNC machine creating a precision component
After working in custom manufacturing for over a decade, I've seen firsthand how CNC technology has revolutionized production capabilities. Our factory in Kunshan has evolved from basic machining to advanced multi-axis operations that serve industries from automotive to aerospace. Let me walk you through how this remarkable technology works and why it matters for modern manufacturing.
What are the essential components of a CNC machining system?
Every day, I watch as customers struggle to understand what makes our machines different from conventional equipment. Without the right components working together, precision parts remain impossible to produce consistently.
A complete CNC machining system consists of five critical elements that work in harmony: the machine controller (computer), input devices, machine tool, driving system, and feedback devices. The controller acts as the brain, interpreting programmed instructions and coordinating all mechanical movements through precision motors that position tools with incredible accuracy.
Components of a modern CNC system
Key Components of CNC Systems
The heart of any CNC system is its control unit - essentially an industrial computer with specialized software that interprets G-code instructions. This controller communicates with motion control systems that precisely position the cutting tools relative to the workpiece. Our factory utilizes Fanuc and Siemens controllers, which offer exceptional reliability and programming flexibility.
The machine structure provides the stability and rigidity needed for precision cutting. High-quality machines feature cast iron or polymer concrete bases that absorb vibration, along with linear guides and ball screws that ensure smooth, accurate movement. I recently invested in a machine with hydrostatic bearings that virtually eliminates friction in the guideways, allowing for surface finishes measured in single-digit microns.
The tooling system is equally important, comprising tool holders, cutting tools, and automatic tool changers. Modern machines can house 30+ tools and switch between them in seconds. We've found ceramic-coated carbide tools provide the optimal balance between tool life and cutting performance for most applications.
Finally, feedback devices like rotary encoders and linear scales continuously monitor position, sending real-time data to the controller to maintain accuracy. When manufacturing vacuum chambers for semiconductor clients, these closed-loop systems help us achieve the ±0.005mm tolerances required for critical sealing surfaces.
How does the CNC programming process translate designs into physical parts?
Many clients come to us with brilliant designs but don't understand the critical gap between CAD files and finished products. This knowledge gap often leads to unrealistic expectations about timelines and capabilities.
The CNC programming process follows a systematic workflow: design creation (CAD), machining strategy development (CAM), post-processing to generate machine-specific code, verification through simulation, and finally, execution on the machine. This digital thread ensures that the physical output precisely matches the original design intent.
Programming process for CNC machining
From Digital Design to Physical Reality
The journey begins with the design phase, typically using software like SolidWorks, AutoCAD, or Fusion 360. We work closely with clients to optimize their designs for manufacturability, sometimes suggesting minor changes that can dramatically reduce machining time or improve part quality. For instance, adding a small internal radius to corners reduces tool wear and prevents stress concentration in the finished part.
Once the design is finalized, we import it into Computer-Aided Manufacturing (CAM) software like Mastercam or HSMWorks. This is where the real magic happens - our programmers create machining strategies by defining tool paths, cutting parameters, and operation sequences. For complex components like impellers for marine applications, we might program 3-5 axis simultaneous movements that follow the contoured surfaces precisely.
The CAM system generates G-code - the universal language of CNC machines - which contains all positioning commands, feed rates, spindle speeds, and tool changes. Before any actual cutting occurs, we verify the program through simulation software that detects potential collisions or errors. I've seen this step save countless hours and expensive materials by catching programming issues before they reach the shop floor.
During actual machining, our operators monitor the process, making micro-adjustments when necessary to account for tool wear or material variations. For critical aerospace components, we perform in-process measurement using touch probes that automatically compensate for deviations, ensuring the final dimensions meet exact specifications.
Which industries benefit most from custom CNC machining services?
Business owners often wonder if investing in custom-machined parts will truly deliver value for their specific industry. This uncertainty can delay critical product improvements or innovations.
CNC machining serves diverse sectors, but provides exceptional value in aerospace (requiring lightweight, high-strength components), medical (needing biocompatible, sterilizable parts), automotive (demanding reliable, precise components for safety systems), and semiconductor manufacturing (requiring ultra-clean vacuum chambers and fixtures).
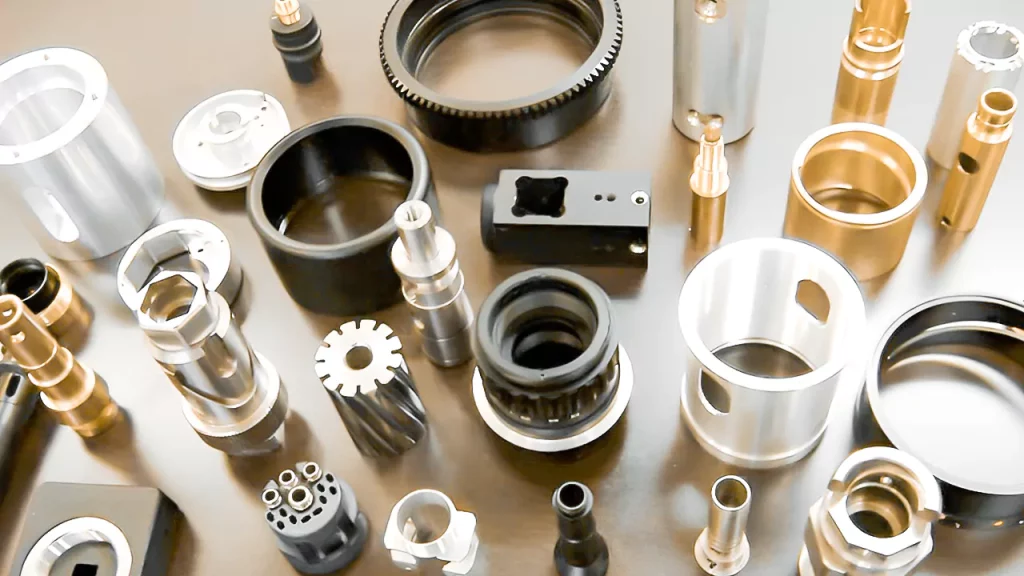
Custom CNC parts for multiple industries
High-Value Applications Across Industries
The aerospace sector represents one of our most demanding client bases. These customers require components machined from exotic alloys like titanium and Inconel, often with complex geometries that optimize weight while maintaining structural integrity. We recently produced mounting brackets for satellite systems that needed to withstand extreme temperature fluctuations while maintaining precise alignment - a perfect application for our 5-axis machines that can create complex geometries in a single setup.
Medical device manufacturers rely on our services for surgical instruments, implant components, and diagnostic equipment parts. The requirements here focus on biocompatibility, surface finish, and absolute reliability. We maintain special protocols for these jobs, including dedicated tools and rigorous cleaning procedures to prevent cross-contamination. One notable project involved creating titanium bone plates with complex contoured surfaces that required simultaneous 5-axis machining.
The semiconductor industry presents unique challenges with its demand for vacuum chambers and components with exceptional cleanliness and dimensional stability. These parts often require machining to tolerances of ±0.005mm or better, with surface finishes that ensure proper vacuum sealing. Our climate-controlled inspection room allows us to verify these critical dimensions regardless of ambient temperature variations in the factory.
Automotive applications span from prototype development to production tooling and specialized components. We've produced everything from custom engine components for racing teams to precision fixtures for assembly operations. The combination of tight tolerances, durability requirements, and cost constraints makes these projects particularly interesting from an engineering perspective.
Why is CNC machining preferred for high-precision metal and plastic components?
Companies struggle with choosing between various manufacturing methods, often wasting resources on processes that aren't optimized for their specific requirements or production volumes.
CNC machining excels where precision, material properties, and design complexity intersect. Unlike casting or molding, CNC creates parts directly from solid material blocks, preserving material integrity while achieving exceptional dimensional accuracy and surface finish without the need for expensive tooling.
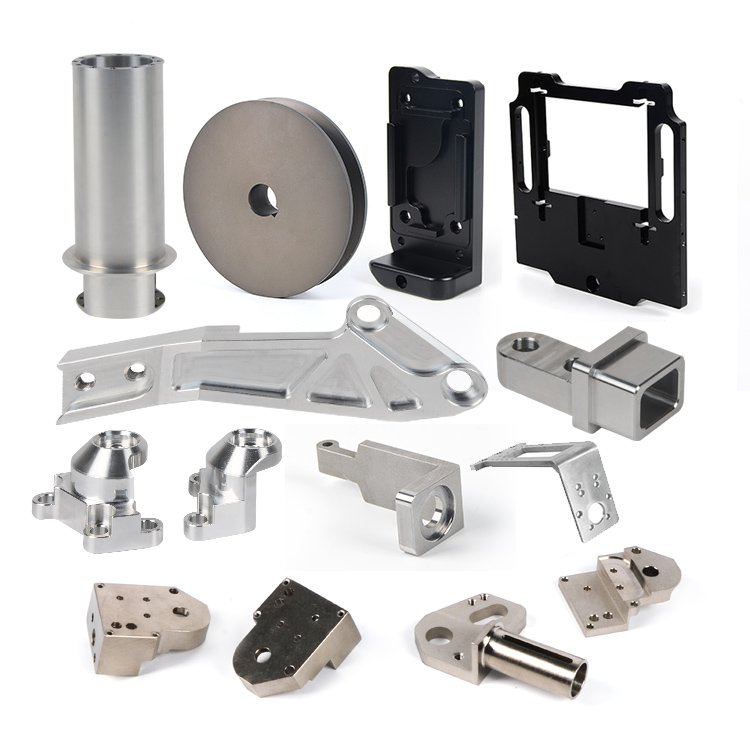
High-precision CNC-machined part
Unmatched Precision and Material Versatility
The dimensional accuracy achievable through CNC machining simply cannot be matched by most other manufacturing processes. Modern CNC centers regularly maintain tolerances of ±0.01mm, with specialized machines capable of micro-precision down to ±0.001mm. This level of precision is critical for components like injection mold cavities, where even minor dimensional variations can affect the final product's quality.
Material versatility represents another significant advantage. Our shop regularly machines everything from common aluminum alloys and stainless steels to specialized materials like Hastelloy, medical-grade titanium, engineering plastics like PEEK, and even machinable ceramics. Each material requires specific cutting parameters, tool selections, and handling procedures - expertise we've developed through years of diverse projects.
CNC machining also excels at creating complex geometries that would be impossible with conventional manufacturing methods. Features like undercuts, internal channels, and precisely positioned holes can be machined directly into the workpiece. For instance, we recently produced a hydraulic manifold block for an industrial client with over 30 intersecting internal passages - a component that would be impossible to create using casting or molding processes.
Surface finish quality presents another compelling advantage. CNC processes can achieve surface roughness measurements down to Ra 0.1μm with the right tooling and parameters. This level of finish is essential for components like sealing surfaces in vacuum chambers or bearing seats in precision mechanical assemblies. We've invested in diamond-tipped finishing tools specifically for applications requiring mirror-like surface characteristics.
The ability to transition directly from prototype to production using the same process and equipment offers significant time and cost advantages. Unlike processes requiring expensive tooling or molds, CNC machining allows for economical production of small to medium quantities without sacrificing quality or precision.
How can businesses determine if CNC machining is cost-effective for their production needs?
Procurement teams and engineers often struggle to evaluate the true cost-effectiveness of CNC machining compared to other manufacturing methods, potentially missing opportunities for significant savings.
Determining CNC machining's cost-effectiveness requires analyzing part complexity, material requirements, production volume, tolerance needs, and lifecycle considerations. While initial per-part costs may exceed molding or casting for high volumes, the elimination of tooling investments and the ability to make design changes without penalty often provides better overall value.
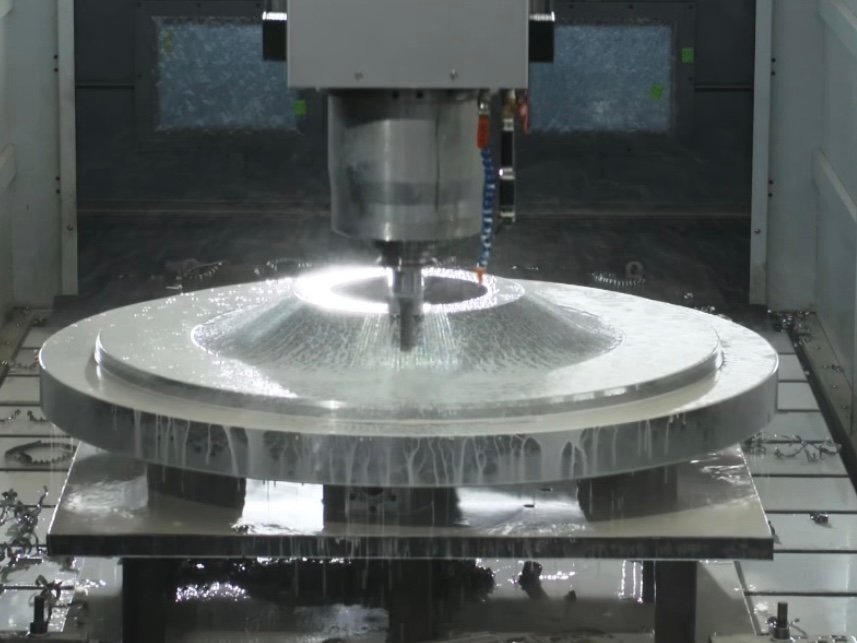
Evaluating the cost-effectiveness of CNC machining
Making Smart Manufacturing Decisions
Production volume stands as the most significant factor in cost analysis. For quantities below 500-1000 pieces (depending on part complexity), CNC machining typically proves more economical than processes requiring expensive tooling investments. I recall working with a client who initially wanted to injection mold a component with projected annual volumes of 2,000 units. After calculating the mold cost ($25,000+) against our CNC pricing, they discovered machining would break even at year three while allowing design flexibility as their product evolved.
Material selection dramatically impacts the cost equation. CNC machining excels with materials that are difficult to cast or mold, like high-performance alloys or specialized plastics. One aerospace client needed components in a specific aluminum-lithium alloy that couldn't be reliably cast, making CNC machining the only viable option despite their relatively high production volumes.
Part complexity creates another important consideration. Geometries requiring multiple setups or specialized tooling increase machining costs, while these same features might add little incremental cost in molding processes once the tool is created. Our quoting system analyzes features like deep pockets, tight tolerance holes, and thin walls to identify potential cost drivers.
Production Factor | Favors CNC Machining | Favors Alternative Processes |
---|---|---|
Volume | Under 1,000 pieces | Over 10,000 pieces |
Complexity | Moderate complexity with precision features | Very simple OR extremely complex geometries |
Material | Specialized/difficult materials | Common materials with standard properties |
Timeline | Urgent needs (days/weeks) | Extended timelines (months) |
Design Status | Evolving/likely to change | Finalized and stable |
Lifecycle considerations often tip the scales toward CNC machining. For products with expected design iterations or customization requirements, the flexibility to modify digital files without tooling changes provides significant value. We've supported clients through multiple design generations without the "tooling penalty" they would face with other processes.
For businesses unsure about the best manufacturing approach, we recommend a hybrid strategy: use CNC machining for initial production and market testing, then transition to alternative processes if volumes justify the tooling investment. This approach minimizes upfront capital while preserving long-term cost optimization opportunities.
Conclusion
CNC machining transforms digital designs into physical reality with unmatched precision and versatility. By understanding the technology's capabilities and applications, businesses can make informed decisions that balance quality, cost, and production needs for optimal manufacturing outcomes.