Explosive welding is a solid-state welding process, that joins two dissimilar metals together by using an explosive charge. The goal of this technique is to create a high-velocity collision that forces the metals to fuse at the molecular level, unlike standard welding, which frequently relies on heat. Often stronger than the original materials, the end product is a strong, long-lasting bond.
A History of Evaluation:
The origins of explosive welding can be traced back to the mid-1900s when scientists started experimenting with non-traditional techniques for joining metal. The development of explosive welding began following World War II. However, its origins can be traced back to World War I. The technique, which was first created for military use, has since been improved and modified for civilian use. It is particularly useful in sectors of the economy where traditional welding techniques are inadequate.
Significance and Application in Emerging Industries
Explosive welding is becoming more and more popular in a variety of industries, including oil and gas and aerospace. For engineers and designers, it offers new possibilities because of its unparalleled precision and strength in joining incompatible metals, such as steel, and aluminum. For the creation of high-performance, composite materials, explosive welding provides a flexible and dependable alternative as industries push the envelope of what is feasible.

Does explosive welding represent the way forward for welding? This novel technique may completely change our understanding of material joining in the twenty-first century as we learn more about its advantages, workings, and practical uses.
2. Basic Principle of Explosive Welding:
Explosive welding is a very precise and regulated technique for combining metals. This technology is a very promising breakthrough in the welding industry, and its basic principles can be explored to see why. Let's examine the operation of explosive welding, its main elements, and the intriguing bond-forming mechanism that distinguishes it from conventional procedures.
2.1 The Workings of Explosive Welding
The basic principle of explosive welding is to accelerate a metal plate, called the flyer plate, in the direction of another metal surface, called the base plate, using a high-energy explosive charge. Without melting the materials, a solid-state link is formed between the two metals as a result of the explosion's tremendous pressure. A clean, strong joint with distinct metallurgical characteristics is produced by this method, usually more powerful than base metal.

2.2 Crucial Elements:
In explosive welding, there are three primary parts: Detonator, Base Plate, and Flyer
The metallic plate known as the "Flyer Plate" is moving quickly in the direction of the base plate. To achieve the appropriate bonding quality, the flyer plate's material and thickness are critical.
The base plate, to which the flyer plate is connected, is a stationary metal surface. The qualities of the base plate affect the welded joint's final features.
Explosive: Carefully chosen both in type and quantity, the explosive substance produces the required force for bonding without causing any material degradation.
2.3 Bond Formation Mechanism:
In explosive welding, the tremendous pressure and metallurgical interaction at the two metals' interface are the main causes of bond formation. Depending on the material and technique, the connecting components are positioned towards one another at an angle of 1 to 15 degrees, and they are primed with an explosive layer above.

Atoms from both plates can combine at the interface where a small layer of metal plasticizes as the flyer plate and base plate collide. This process produces the wavy, vortex-like pattern at the bond line that is typical of explosive welds, along with the high impact velocity. This design strengthens the joint's mechanical strength and increases its resistance to corrosion and wear.
3. Types of Explosive Welding
Let's examine the four primary forms of explosive welding, each of which has unique properties and uses.
3.1 parallel Plate Fusion
Placing two metal plates parallel to one another with a tiny space between them is known as parallel plate welding. An explosive charge is applied to the upper plate, and when it explodes, the shock wave rapidly presses the plates together. A metallurgical link is formed and the surfaces are cleaned by the quick collision that causes a jetting action at the contact.

Heat exchangers and other big components are frequently manufactured using this technology, which is perfect for producing huge, flat bonded regions. Stronger than the parent metals in many cases, the resultant bond is extraordinarily robust.
3.2 Welding Angular Plates
The metal plates are stacked at an angle instead of parallel when using angular plate welding. A more intricate bonding interface is produced when the explosive charge detonates in a way that pulls the plates together not just along one axis but also at an angle. The metals collide as a result of the detonation, creating an undulating or wavy bonding surface.

The angled arrangement of the components makes this approach especially helpful for joining metals with various thicknesses or characteristics since it provides greater control over the bonding process. It's frequently employed in situations when a solid, long-lasting bond is required without the need for further welding
3.3 Welding of Tubes to Tubes Plates
Tube-to-tube welding is used in heat exchangers, boilers, and condensers, plate welding is a specialized type of explosive welding that joins tubes to plates. This method involves inserting the tube into a plate hole and surrounding or completely encasing the tube with an explosive charge. The tube swells and solidifies its link with the plate upon detonation.
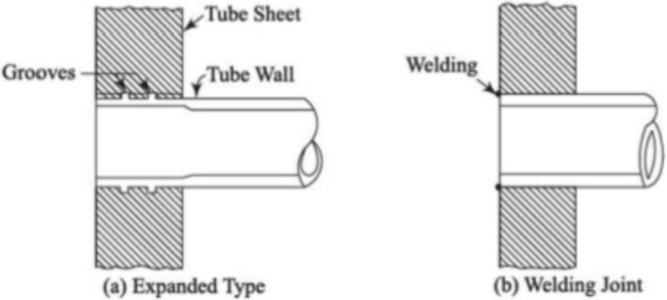
This method works well for applications involving fluids or gases under high pressure because it guarantees a tight, leak-proof seal. It also makes it possible to combine different metals, which increases the design and material selection's adaptability.
3.4 Detonating cladding
In explosive cladding, two distinct metals are bonded together to create a composite material with improved qualities. This method involves covering a thicker base metal with a thin sheet of one metal (the cladding). The cladding metal is then subjected to extreme pressure when an explosive charge is detonated on it.
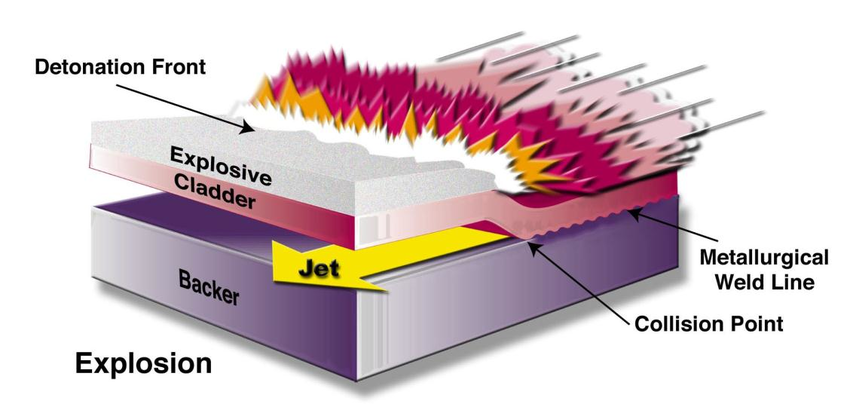
By joining the strengths of the base metal with the corrosion resistance of the cladding material, the resulting bond combines the qualities of both metals. This method is commonly employed in sectors like chemical processing and oil refining that need materials with certain combinations of qualities.
4. Techniques of Explosive Welding
Explosive welding is a flexible procedure that can be carried out with a variety of techniques, each designed for certain materials and applications. The weld's properties and quality can be greatly impacted by the procedure used. Let's examine some of the main techniques for explosive welding, demonstrating their uses, benefits, and drawbacks.
4.1 Contact Technique
In Contact Technique, the explosive charge is placed directly on the metal plates that need to be welded. The explosion presses the closely spaced, frequently slightly apart plates together, forging a link between them. This method works well for both parallel and angular plate welding setups and is frequently used to join big, flat surfaces.
4.2 Stand-Off Technique
The Stand-Off Technique involves positioning the explosive charge a specific distance away from the metal plates, which are spaced apart by a gap called the stand-off distance. A shock wave is created by the explosion and passes through the standoff distance before hitting the plates. When bonding a thin layer of one metal to a thicker substrate, this technique is frequently utilized in cladding applications.
4.3 Underwater Explosive Welding
A unique technique called underwater explosive welding involves welding underwater. The submerged components can be joined together since the explosive charge detonates in an aquatic environment. This method is frequently applied to the upkeep and repair of offshore platforms, pipelines, and maritime constructions.
4.4 Vacuum Explosive Welding
The welding process is carried out in a vacuum chamber when using vacuum explosive welding. A cleaner and more controlled welding environment is made possible by the lack of air and other pollutants. In high-tech sectors where contamination can have a major impact on the quality of the weld, such as electronics and aerospace, this technique is frequently utilized to combine metals.
4.5 Explosive Welding with Pre-Heating
Heating the metal surfaces in advance of the explosive welding process is known as "explosive welding with pre-heating." By lowering heat gradients and tensions during the welding process, preheating enhances the bond's quality. When combining metals with noticeably different melting points or rates of thermal expansion, this method is especially helpful.
5. Materials Used in Explosive Welding
To fuse two or more distinct metals or alloys, explosive welding uses high-energy explosives. To achieve a strong and long-lasting weld, material selection is crucial. In general with further subdivisions, the materials are categorized as metals and alloys.
- 5.1 Metals and Alloys
- 5.1.1 Ferrous Metals
Iron is the primary element in ferrous metals. Common ferrous metals used in explosive welding include:
Carbon steel: It is used extensively, because of its strength and adaptability.
Stainless steel: It is well-known for being resistant to corrosion, which makes it perfect for use in chemical and maritime applications.
Alloy steel: It is utilized in high-stress applications and provides better mechanical qualities.
- 5.1.2 Non-Ferrous Metals
Iron is absent from non-ferrous metals, utilized for their unique qualities like resistance to corrosion and lightweight. The following are typical non-ferrous metals:
Aluminum: The aerospace and automotive industries frequently employ aluminum and its alloys because they are lightweight and corrosion-resistant.
Copper: Utilised in heat exchanger and electrical applications, copper and copper alloys have excellent thermal and electrical conductivity.
Titanium: It is a material with a high strength-to-weight ratio and resistance to corrosion that is utilized in maritime, aviation, and medical fields.
Nickel: Utilized in the chemical processing and aerospace industries, nickel and nickel alloys resist high temperatures and corrosion.
- 5.1.3 Metal Composites
Materials made of two or more different metals or alloys are known as metal composites. They combine the desired qualities of various materials, such as strength and resistance to corrosion, using explosive welding. Consider:
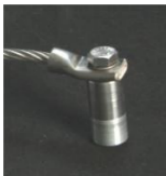
Bimetallic sheets: These are frequently used in electrical applications. They are layers of various metals linked together.
Clad metals: These are composed of a base metal that has a layer of a different metal on top that offers a mix of qualities including structural integrity and resistance to corrosion.
- 5.2 Selection Criteria for Flyer and Base Plates
The base plate and flyer plate in explosive welding need to be carefully chosen depending on several factors, including:
Compatibility: For a solid bond to form without unwanted intermetallic compounds or reactions, the materials must be metallurgically compatible.
Mechanical Characteristics: To prevent excessive wear or failure under stress, the mechanical characteristics, such as ductility, strength, and hardness, should be compatible.
Thermal Properties: It is important to take into account the materials' coefficients of thermal expansion, particularly if the welded component will be subjected to temperature fluctuations.
Corrosion Resistance: Since hostile environments may aggravate corrosion, the materials chosen should provide the appropriate amount of corrosion resistance.
Thickness and Density: The welding process, including the number of explosives used and the final qualities of the weld, is influenced by the thickness and density of the flyer and base plates.
Expense and Accessibility: In large-scale applications, the cost and availability of the materials can play a major role.
6. Detailed Process Steps
- 6.1 Preparation of Surfaces
- Cleaning: To get rid of any impurities like oxides, filth, or oil, the surfaces that need to be welded are carefully cleaned. Chemical cleansers, mechanical abrasion, and other techniques can be used for this purpose.
- Surface Roughening: To improve the bonding process, the surfaces may be roughened to a particular texture. This enhances the mechanical interaction between the metals and helps to increase surface area.
- Alignment: To guarantee consistency and high-quality welding, the plates or parts are carefully aligned.
- 6.2 Assembly of Components
- Component Placement: The parts that need to be welded are arranged in the desired way. Usually, this entails placing the flyer plate (the upper plate) above the base plate.
- Buffer or Stand-off Gap: The flyer and base plates are kept apart by a buffer or gap. This gap plays a critical role in the bonding process by enabling the flyer plate to speed toward the base plate during the explosion.
- Assisting Frameworks: To stop any unintentional movement during the explosive detonation, the assembly is stabilized and fastened

A Detailed process set-up (a,b), Explosion welding(c), Final explosive welded plate (d)
- 6.3 Explosive Placement and Shaping
- Selecting Explosive Material: The metals being joined and the intended weld qualities are taken into consideration when selecting the type and quantity of explosive material.
- Explosive Forming: The explosives are placed over the flyer plate and given a specific shape. Since they dictate the direction and strength of the force applied, the explosive charge's shape and arrangement are crucial.
- Detonation Control: To regulate the timing and order of the explosion, detonators, also known as initiation devices, are positioned at particular sites.
- 6.4 Detonation and Bonding Process
- Explosion: When the explosive detonates, a high-pressure shock wave is created that pushes the flyer plate in the direction of the base plate.
- Bonding Mechanism: A jetting action is produced at the interface when the flyer plate and base plate collide due to the high-pressure impact. In addition to cleaning the surface, this jetting process forges a metallurgical link between the metals.
- Wave Formation: Explosive welding is characterized by the "wave structure," or wavy pattern that frequently appears at the interface between the two metals. The mechanical strength of the connection is strengthened by this structure.
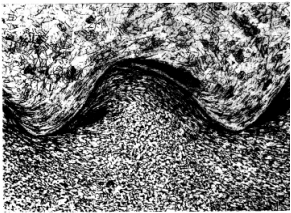
Microstructure of steel/steel wavy interface of explosive welding
- 6.5 Post-Weld Inspection and Testing
Explosive welding post-weld inspection includes multiple quality testing methods which involve visual inspection for surface imperfections, mechanical testing for strength and ductility, and ultrasonic and radiographic testing for internal problems. These procedures guarantee the structural integrity and quality of the weld.
7. Factors Influencing the Explosive Welding Process
Explosive welding is a complicated process that requires careful control over several variables to produce a high-quality weld. These variables are as follows:
- 7.1 Properties of Explosives
Detonation Velocity: The welding process is impacted by the explosive wave's speed of travel. Increased energy produced by higher detonation velocities can strengthen the link between the components but also increase material damage.
Energy Output: The force exerted on the metals is influenced by the explosive's total energy release. It ought to be enough to form a solid binding without causing any harm to the plates.
Explosive Type: The energies, velocities, and sensitivities of various explosives differ. The process efficiency and safety are impacted by the selection of explosive
7.2 Plate Material Characteristics (Thickness, Hardness, Density)
Density: The materials' reaction to the explosive force depends on their density. Denser materials may take more energy to establish effective bonding.
Hardness: The materials' ability to withstand stress can have an impact on the way waves form and how well bonds are formed. Harder materials could be more difficult to bond and might need other factors to be carefully adjusted.
Thickness: The necessary explosive energy and the standoff distance are determined by the thickness of the plates. More explosive strength might be required to achieve bonding on thicker plates.
- 7.3 Explosive Loading Ratio
The mass of the explosive divided by the mass of the flyer plate is known as the loading ratio. The ideal loading ratio guarantees that there is enough energy to make a connection without subjecting the materials to undue distortion or harm.
- 7.4 Stand-off Distance
The flyer and base plate gap are essential for regulating the impact's angle and velocity. While an improper stand-off distance might result in weak bonds or material failure, the optimum distance guarantees appropriate jetting and bonding.
- 7.5 Angle of Impact
The jet formation and wave pattern at the interface are influenced by the angle at which the flyer plate collides with the base plate. A homogenous and robust connection can only be achieved at the right angle. Small angles of impact are usually favored for efficient bonding and jetting.
-7.6 Environmental Conditions (Temperature, Humidity)
Temperature: High temperatures can have an impact on the explosive's and the materials' welding qualities. The materials may get brittle at low temperatures and soften at high ones.
Humidity: Surface cleanliness and the explosive's performance can both be impacted by environmental moisture. The quality of the weld may be compromised by oxidation or contamination brought on by excessive humidity.
- 7.7 Surface Preparation and Cleanliness
To achieve a strong connection, surfaces must be free of oxides, oils, and other pollutants. Impurities may hinder appropriate bonding and jetting, resulting in poor quality or feeble welds.
Surface Roughness: The mechanical interlocking and bond quality are influenced by the roughness of the surfaces. By expanding the contact area, a surface that has been appropriately prepped and appropriately roughened can improve bonding.
8. Advantages of Explosive Welding
Explosive welding is a popular technique for combining metals, especially those that are challenging to weld with other methods since it has many benefits. The main benefits are as follows:
- 8.1 Strong Metallurgical Bond
- The metallurgical bond between the metals is reinforced by the explosive welding process. A strong and long-lasting joint results from the high-pressure impact-induced plastic deformation at the interface.
- The bond is further strengthened by the distinctive wave pattern created at the weld interface improves the mechanical interlocking between the metals.
- 8.2 Ability to Join Dissimilar Metals
- Dissimilar metals such as aluminum and steel or titanium and copper are only two examples of widely diverse metals that can be joined via explosive welding. Applications requiring electrical conductivity, corrosion resistance, or other unique qualities will find this especially helpful.
- Compatibility with Non-typical Materials: While conventional welding methods have difficulties when bonding metals to non-metallic materials like ceramics or composites, this process can also be employed to achieve this goal.
- 8.3 Minimal Thermal Effects
- Cold Welding Process: In contrast to traditional welding techniques, explosive welding is a solid-state procedure carried out at room temperature or slightly below it. It follows that the materials are not receiving a lot of heat.
- Diminished Thermal Distortion: The absence of appreciable heat generation inhibits thermal distortion and lowers the possibility of changing the characteristics of the material. This is especially important for heat-sensitive materials or those that need exact dimensional control.
- Exclusion of Heat Affect Zone: Minimal Heating Prevents the Formation of a Heat-Affected Zone (HAZ). A HAZ could weaken or change the qualities of the material. This welding technique prevents it from happening.
- 8.4 High Production Efficiency
- Quick Process: The explosive welding process is extremely quick, taking only a few seconds to finish. This is useful in high-production settings when efficiency is paramount.
- Large Area Bonding: Well suited for creating large components or clad plates, this technique joins vast surface areas in a single operation.
- Minimal Post-Weld Processing: The technique requires minimal heating or melting, thus it doesn't require a lot of post-weld heat treatments or machining, which saves money and time on manufacturing.
9. Limitations and Challenges
- 9.1 Safety Concerns and Handling of Explosives
- Dangerous Materials: Using explosives carries several intrinsic safety concerns, such as the possibility of unintentional detonations that could result in fatalities or severe injuries.
- Strict Safety Procedures: Tight safety procedures and specialized facilities are needed while handling and storing explosives. Operating expenses and complexity may rise as a result.
- Specialized Training: Operators need to get extensive training in the handling of explosives, safety protocols, and the unique needs of explosive welding operations.
- 9.2 Limitations in Material Thickness and Size
- Limitations on Thickness: Although explosive welding is a versatile technique for joining a variety of materials, it is feasible to attach plates only to a certain thickness. Overly thick materials might need a lot of explosive charges, which would make handling difficult and unsafe.
- Size and Geometry Restrictions: Flat or mildly curved surfaces work best for this method. This process can be difficult to use when welding complex forms or intricate geometries, hence its use is limited to specific designs or parts.
- 9.3 Control of Bonding Quality and Consistency
- The variation of bond quality: The process of bond quality is extremely sensitive to changes in explosive charge, stand-off distance, and other characteristics, making it difficult to achieve consistent bond quality. Incomplete or weak bonding can result from minor variations.
- Challenges with Inspection: The ability to find minute flaws or inconsistent welds in non-destructive testing techniques may be limited. It can be expensive and time-consuming to implement the required strict inspection and testing methods.
- 9.4 Environmental and Regulatory Issues
- Impact on the Environment: The use of explosives can harm the environment, including noise pollution, issues with air quality, and possible degradation from hazardous leftovers.
- Regulatory Compliance: There are strict rules governing the usage, storage, and disposal of explosives in explosive welding operations. It can be difficult to comply with these requirements and may require a large amount of administrative work.
- Limited Facilities: Because explosive welding is a specialized procedure and has specific regulations to follow, there aren't many facilities that can handle it. For businesses looking to utilize explosive welding, this might limit access and raise prices.
10. Applications of Explosive Welding
Explosive welding is used in a variety of industries when it's necessary to fuse dissimilar materials, especially when traditional welding techniques are inappropriate or not feasible.
- 10.1 Aerospace and Defense
- Explosive welding is frequently used in aerospace applications to combine incompatible metals like titanium and aluminum, which are lightweight and strong. This process creates lightweight structures.
- Rocket casings and Heat Exchangers: Accurately joining high-performance materials is essential in the production of heat exchangers and other components for rockets and missiles.
- 10.2 Oil and Gas Industry
- Manufacturing of Clad Pipes: For protection against corrosive conditions, pipes are clad with materials that resist corrosion, such as nickel alloys or stainless steel, using explosive welding.
- Offshore Platforms: It is utilized in the building of offshore oil platforms, where the ability of materials to survive strong marine conditions and corrosion is a prerequisite.

Titanium Clad Pressure vessel
- 10.3 Chemical Processing
- Corrosion-Resistant Linings: To create tanks and vessels that can withstand extremely corrosive chemicals, corrosion-resistant metals are bonded to structural substrates using explosive welding.
- Heat Exchangers: This method is used to produce heat exchangers that have the best possible thermal conductivity and chemical corrosion resistance, which improves process safety and efficiency.
- 10.4 Power Generation
- Turbine Components: When fabricating turbine blades and other parts requiring the use of materials with high strength and resistance to corrosion, explosive welding is employed.

- Renewable Energy: It's also used when building renewable energy systems, like solar panels and wind turbines, which call for strong, lightweight materials.
- 10.5 Marine and Shipbuilding
- Ship Hulls and Superstructures: Lightweight materials like aluminum are bonded to steel via explosive welding, which lowers the total weight of ships without compromising structural integrity.
- Submarine Components:
While explosive welding can produce metallurgical junctions between extremely different metals with sufficient corrosion resistance, it is commonly used in the marine and shipbuilding industries.
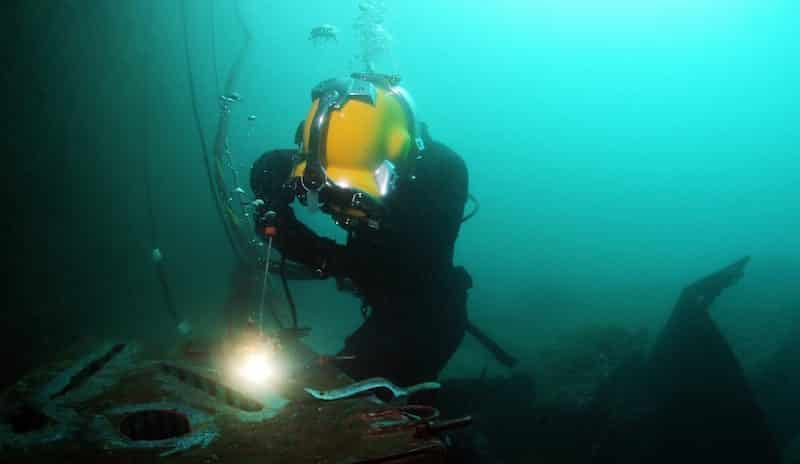
Underwater Explosive welding of submarine components
- 10.6 Medical and Healthcare
- Medical equipment: To ensure the safety and dependability of medical equipment, such as implants and surgical instruments, biocompatible materials are joined via explosive welding.
- Diagnostic Equipment: Accurate and dependable component bonding is essential in the manufacturing of diagnostic equipment, which also uses it.
11. Recent Developments and Innovations
- 11.1 Advances in Explosive Formulations and Technologies
- Nanomaterial Additives: To improve control over the detonation characteristics, it has been investigated to incorporate nanoparticles into explosives. These additives can change the behavior of the explosive, enabling better weld quality and more accurate energy delivery.
- Digital Detonation Control: Advances in detonation technology have led to the development of digital control systems, which enable more accurate timing and explosion sequencing. This lowers the possibility of flaws and produces more consistent bonding.
- 11.2 Integration with Other Welding Techniques
- Hybrid Welding Procedures: Scientists are investigating hybrid welding processes that fuse laser or friction stir welding with explosive welding. By combining the benefits of several procedures, these hybrid methods can increase the variety of materials that can be joined together and produce better joint qualities.
- Post-Weld Heat Treatment: By combining post-weld heat treatments with explosive welding, the welded joint's qualities can be improved. By combining these two methods, the microstructure can be improved and residual stresses can be released, creating stronger and longer-lasting connections.
- 11.3 Emerging Applications and Research
- Applications in Aerospace and Automotive: Current research centers on using explosive welding to fuse innovative materials, like composites and high-strength alloys, in the aerospace and automotive industries. These applications seek to preserve durability and safety standards while lowering weight and enhancing performance.
- Bi-Metllic structure in construction: Explosive welding is being investigated for the creation of bi-metallic structures in the construction sector, such as steel-aluminum composite panels. These structures are appropriate for contemporary architectural designs because they have better strength-to-weight ratios and corrosion resistance.
12. Quality Control and Testing Methods
Post-weld testing for explosive welding involves multiple tests such as optical, ultrasonic, and radiographic inspections to check for faults and guarantee bond integrity.
- 12.1 Non-Destructive Testing (NDT) Techniques
1. Ultrasonic Testing (UT):
Principle: Measures thickness, assesses bond quality, and uses high-frequency sound waves to find internal faults.
Application: Good for locating weld faults such as voids, inclusions, and delaminations.
2. Radiographic Testing (RT):
Principle: The basic process is to create an image of the welded joint's internal structure using X-rays or gamma radiation.
Application: Helps identify internal defects and discontinuities by giving a picture of the weld integrity.
3. A dye-penetrating microscope (DPI):
Principle: The basic idea is to apply a dye to the surface, let it get into any surface-breaking defects, and then use a developer to extract the dye from the defects.
Application: Effective in identifying surface flaws such as porosity and fractures.
4. Magnetic Particle Inspection(MPI):
Principle: The method detects discontinuities at the surface and near the surface by using ferromagnetic particles and magnetic fields.
Application: Excellent for locating inclusions, seams, and fissures in ferromagnetic materials.
5. Eddy Current Examinations (ECTs):
Principle: Surface and subsurface fault detection using electromagnetic induction.
Application: Optimal for assessing thin materials and identifying changes in conductivity and surface fissures.
- 12.2 Mechanical Testing (Shear, Tensile, Hardness)
1. Shear Testing:
Principle: The welded joint's resistance to shear forces is measured.
Application: Establishes the bond's shear strength, which is essential for determining how well the joint can tolerate applied stresses.
2. Tensile Testing:
Principle: The welded junction is pulled apart until its tensile strength and ductility are no longer measured.
Application: Assesses the welded joint's overall strength and elongation characteristics to determine how well it will hold up to tensile loads.
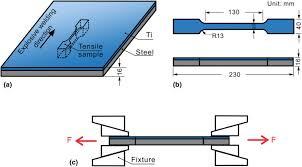
3. Hardness Testing:
Principle: Employ indentation techniques to measure the hardness of the welded area and the foundation materials.
Application: Evaluate how resistant the welded connection is to wear and distortion, offering information about the material's characteristics after welding.
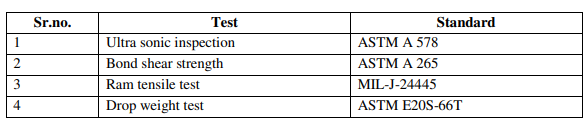
- 12.3 Metallurgical Analysis
1. Microscopic Analysis:
Principle: includes cutting a cross-sectional sample of the weld and microscopically analyzing it.
Application: Shows the weld's microstructure, including the grain structure, wave pattern, and any impurities or flaws.
2. Scanning Electron Microscopy (SEM).
Principle: High-resolution pictures of the weld surface and its microstructure are created by focusing an electron beam.
Application: Offers comprehensive data regarding the weld interface, encompassing the type of bonding and any minuscule imperfections.

SEM image of the explosive welded interface of Ti/Fe
3. Energy Dispersive X-ray Spectroscopy (EDS):
Principle: EDS examines the elemental makeup of the weld region in conjunction with SEM.
Application: Determines the dispersion of various elements at the interface between the weld and the material, which might reveal information about the bond's quality and potential contradictions.
13.1 A Case Study of Aerospace and Defence
Jointing Titanium and Steel for Aerospace Components:
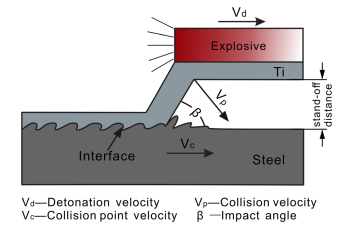
Explosive Welding of Dissimilar material(Ti/Steel)
Background:
Steel's longevity and affordability combined with titanium's small weight and great strength make joining titanium to steel necessary in the aerospace sector.
Problem:
Due to titanium and steel's dissimilar thermal characteristics and propensity to generate brittle intermetallic compounds, conventional welding procedures frequently fail to provide a reliable bond between the two materials.
Solution and Result:
Process of Explosive Welding: Steel and titanium plates were welded using a controlled explosive charge. By avoiding the production of brittle phases, the high-velocity collision formed a strong, metallurgical bond without requiring a large amount of heat input.
Outcomes:
The final bimetallic joints demonstrated superior mechanical qualities, satisfying the demanding specifications of aircraft uses. Due to its success, explosive welding is now used to produce essential aerospace components, which reduce weight and increase performance.
14. Explosive welding VS Traditional welding Difference
Conventional and explosive welding methods have special qualities, benefits, and drawbacks. Below is a contrast between the two:
Process:
Explosive welding is a technique that joins metals together without producing a lot of heat.
Conventional Welding: Melts and joins metals using heat and occasionally pressure. Compatibility of Materials:
Explosive welding is the best method for combining different metals without creating brittle intermetallic complexes.
Conventional welding: It can combine different metals, but may encounter difficulties due to varying melting points and rates of thermal expansion.
Joint attributes:
Strong metallurgical bonding with little deformation and heat-affected zone (HAZ) are the hallmarks of explosive welding.
Conventional Welding: Vary in intensity; considerable heat-related hazards and possible deformation.
Applications:
Explosive Welding: Ideal for cladding, big plates, and surfaces that are flat or gently curved.
Conventional Welding: Adaptable to many different sizes, forms, and intricate geometries.
15. Future Prospects and Trends
It is the only method that can create strong bindings between materials that are not compatible, explosive welding will only become more important in the future.
More Utilization in Aerospace and Defence:
- Rising demand for materials that are strong and lightweight.
- Improved military vehicles and aircraft performance using superior material bonding.
Development In Material Integration:
- Creation of novel bonding methods for a larger variety of materials.
- Enhanced compatibility between metals that expand at varying rates of heat.
Improved Operations Management:
- Enhanced command of explosive charges and explosion sequences.
- Optimized welding settings by the use of sophisticated calculations and modeling.
Improvements in the Environment and Safety:
- Production of safer and more ecologically friendly explosive substances.
- Improved equipment and safety procedures for operators.
The incorporation of additive manufacturing
- Possibility of building intricate structures made of multiple materials.
- Rise in hybrid manufacturing technologies that combine additive manufacturing and explosive welding.
Conclusion:
To sum up, explosive welding is a strong and versatile welding technology that overcomes the drawbacks of conventional welding methods. Its capacity to create durable, dependable joins between different materials, together with continuous advancements and growing uses, places it at the forefront of manufacturing and material joining technology.
Explosive welding is a cornerstone of contemporary engineering methods, contributing to developments across a wide range of industries thanks to its extensive benefits and promising future. Did you find this blog helpful? Let us know by commenting below.