Introduction
Injection molding flash represents a flaw arising from the escape of molten plastic outside the mold during the injection process, leading to solidification. This issue not only diminishes the overall quality of the molded component but also poses a risk to the integrity of the mold itself. Consequently, understanding the origins of flashing, implementing effective remedies, and adopting preventive measures becomes crucial. This article comprehensively explores the nuances of plastic injection molding flash, equipping you with the knowledge to rectify or circumvent this particular defect.
What is Injection Molding Flash?

Injection Molding Flash (Reference)
Flash" denotes the presence of delicate plastic residues along the periphery of molded plastic components. This imperfection arises when liquid plastic escapes the mold cavity, subsequently cooling and solidifying alongside the main component to form an unintended tab, flap, or analogous projection. Typically, flash manifests in areas such as sealing faces, parting lines, ejectors, or venting channels.
In comparison to other potential flaws in the injection molding process, flash might not appear particularly severe. Admittedly, the plastic remains unaffected and can often be rectified by trimming. However, it's crucial to recognize that the removal of flash necessitates additional time and labor, which may not have been initially factored into the project budget. Moreover, excessive trimming and flash removal can introduce inconsistencies between parts and deviate from the intended design accuracy.
Causes of Injection Molding Flash
Injection molding flash can occur due to a variety of reasons, often stemming from multiple factors. It is essential to address these issues comprehensively, as they can manifest during different stages of the injection molding process. Here, we explore the primary causes of injection molding flash and when they typically arise.
Parting Line Mismatches
Parting line mismatches, a major contributor to flashing, often result from environmental contaminants such as dust or debris that keep the mold open. This allows excess material to leak out, causing a flash defect. Mold flaws can exacerbate this issue, particularly in older, worn-out tooling prone to leakages over time. Even with a flawless mold, improper clamping pressure or highly intricate shapes can lead to flashing.

Improper Venting
In the intricate process of injection molding, maintaining optimal temperature, pressure, and air pocket conditions is crucial. Trapped air bubbles can significantly impact a part's mechanical properties. Vents play a vital role in ensuring the smooth operation of these components, and any issues can lead to various defects, including flashing.
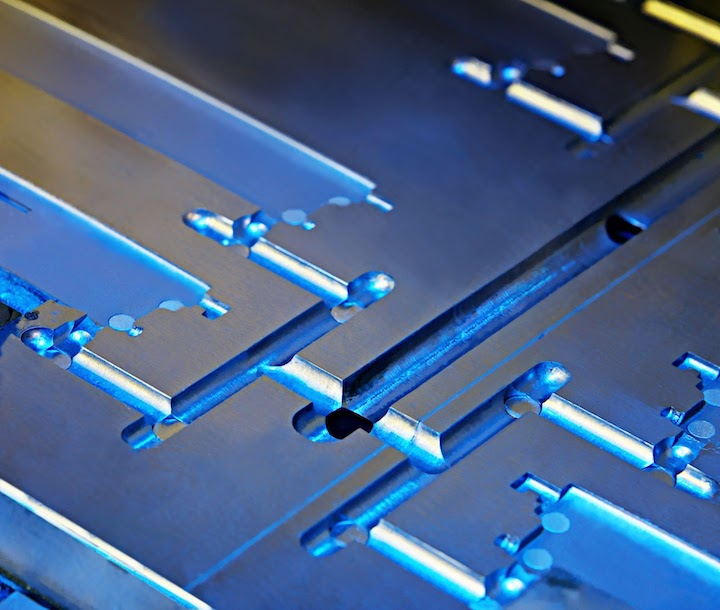
Low Clamping Pressure
Flash can occur during both the packing and holding processes. In these phases, precise clamping pressure is essential. Incorrect clamping force can disrupt the parting line, allowing liquid material to escape and cause flashing. Adequate clamping pressure is crucial for maintaining equilibrium during cooling, preventing defects in the final product.
Sprue Bushing Issues
Sprue bushings, responsible for transferring molten plastics into the cavity, can deteriorate over time. As they lose support to withstand injection pressure, defects in injection molded parts become more common, with flashing being a prevalent issue.
Viscosity
The property of viscosity, influencing the flow of molten plastic, plays a central role in injection molding. Lower viscosity increases the likelihood of molten liquid flowing out of the mold shape, resulting in flash defects. Viscosity is affected by temperature, material properties, pressure, and speed.
Barrel and Nozzle Temperature
Apart from pressure, barrel and nozzle temperature directly impact viscosity. Higher temperatures reduce viscosity, making the fluid more prone to leaking and increasing the chances of injection molding flash.
Over Fill
Overfilling the molten plastic in an injection molding setup can lead to increased injection pressure, surpassing clamping pressure and causing leakages. Care must be taken while adjusting feed settings to prevent incomplete parts due to short shots in injection molding.
High Pressure
High pressure is a significant factor that can elevate the probability of flash defects. Basic physics dictates that increased pressure results in higher temperature and flow characteristics in a closed environment. This heightened pressure, coupled with increased viscosity, can lead to various defects, including flashing.
Over Packing
Design complexities and intricate mold pathways can create flash defects in injection molded parts. In narrow fields, limited molten liquid can solidify and block the flow, creating localized pressure within the mold. This can result in flash defects and other issues, such as warpage and non-uniform density.
Addressing Flashing Issues Holistically
To mitigate flashing problems, it's crucial to address issues at every stage of the injection molding process. This includes maintaining a clean environment to prevent parting line mismatches, ensuring proper venting to avoid defects, and monitoring clamping pressure during packing and holding phases. Regular maintenance of sprue bushings is essential to prevent deterioration and defects. Additionally, controlling viscosity through temperature management and avoiding overfilling are key strategies to reduce the chances of flash defects.
Effective Ways to Control Flash
During the production process, injection molding flash can be a frequent problem that affects the end product's quality and appearance. To guarantee a more seamless production process and better final products, there are several efficient techniques to manage and prevent flash.
- Utilizing Hot Air for Flash
ResolutionUsing hot air to combat tiny and thin flashes in injection molding can be a rapid and effective fix. Melting the flashback into the plastic surface is the process used in this procedure. Remember that hot air can be used as a backup deflashing technique for coarse flashes following mechanical removal.
2. Adopt a Cryogenic Flashing Method
Cryogenic deflashing emerges as the most potent remedy for addressing flashing issues in injection molding. This technique involves subjecting the part to liquid nitrogen, facilitating easy removal of flash. Notably, the process maintains the finish of the parts. Despite its efficacy, it's worth noting that commercially available cryogenic deflashing machines come with a considerable price tag.
3. Select Handheld Deflashing
Using instruments like blades, scissors, or grinders, manual deflashing is a flexible technique that removes injection mold flash at the parting line. Depending on the expertise of the operator, this approach works with nearly all technical materials and guarantees high-quality outputs. Moreover, it makes it possible to quickly check the deflashing procedure.
4. Exercise Caution When Using Open Flames
Deflashing using an open flame is a viable option in some situations. It is important to exercise caution though, since this technique may change the surface of the material, which might reduce its aesthetic value and make post-processing alternatives more difficult, such as painting.
Taking Preventive Measures to Avoid Flash in Injection Molding
Preventing flash completely is a more effective method than treating it after it arises. The following preventative steps might help avoid injection mold flash:
- Give mold maintenance and cleaning priority.
Injection molding flash may be avoided by regularly cleaning and maintaining molds. To make sure mold surfaces are clear of debris, use compressed air, clean cloths, and mold cleaners. Remove any impurities carefully before the molding process to prevent the mold from closing all the way.
2. Utilize Sufficient Clamp Tonnage
Securing the appropriate clamp tonnage is crucial to a fruitful molding procedure. But be careful not to use too much force since this might harm the mold as well as the finished product. Flash and other possible problems can be avoided by using the proper clamp tonnage.
3. Manufacturability-focused design (DFM)

Designing parts with manufacturability in mind is a proactive approach to eliminate flash in injection molding. Emphasizing simplicity and effectiveness in features, especially concerning the parting line, can significantly mitigate the risk of flash occurrence. DFM analysis, facilitated by specialized software tools, aids in simulating results, predicting issues, and optimizing designs for flawless injection molding.
4. Select Molds Without Flash (for Sensitive Applications)
Every mold surface that comes into contact with the plastic during the injection molding process should have draft angles added to it to guarantee a mold configuration free of unwanted flashes. This method reduces the amount of flash produced while guaranteeing a quick ejection of the molded item from the mold.
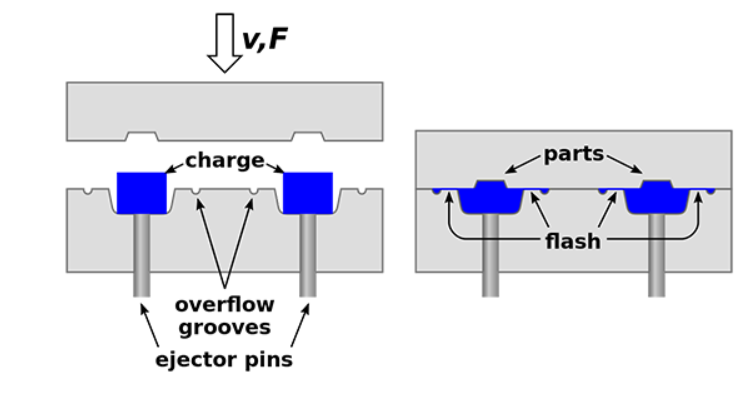
flash-free mold design (Reference)
Using a flash-free mold is a great option for situations where cost is not a major factor and aesthetics and functionality are of utmost importance. Even though it's pricey, it ensures products are free of defects and is particularly useful for delicate applications.
5. Regulate Injection Rate to Diminish Flash
Flash control depends on process variable management done well. Experts begin by reducing the injection rate since it has a direct impact on temperature, pressure, and viscosity—all of which can lead to the occurrence of flash.
Conclusion
Finally, keeping molded components intact and manufacturing processes efficient requires dealing with the complexity of injection molding flash. To effectively troubleshoot, it is necessary to understand the many reasons, which might range from viscosity problems to parting line mismatches. Hot air, cryogenic, and manual deflashing are some of the methods that may be used to solve flashing issues during production. Nevertheless, the most effective way to avoid flash-related problems is to prioritize preventative measures such as mold maintenance, correct clamp tonnage, design with manufacturability in mind, molds that do not contain flash, and regulated injection rates. Manufacturers may improve the injection molding process and ensure cost-effectiveness and high-quality final products by proactively regulating these aspects.