Mirror polishing is an important activity in many different industries such as manufacturing, automotive, and optics. This process involves reducing surface flaws, which increases reflectivity and improves the surface quality, aesthetics, and functionality of the object. Actually, the grading system from A0 to A3 is a classification of different levels of mirror finishes, with A0 being the highest grade. In this blog, we will clarify the mirror finish polishing grades in detail, as well as their techniques, comparisons, and outcome factors, so that you can make informed choices. So, it's wise not to skip!
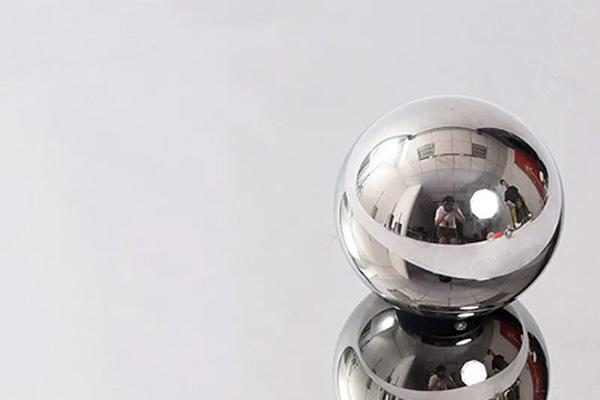
Figure 1: Mirror polishing
1) Overview of Mirror Polishing Grades
There are different mirror polishing grades like A0, A1, A2, and A3. Let’s discuss each one by one.
i) A0 (Optical-Grade Mirror Finish)
The A0 grade is the highest described finish in mirror polishing. It features an ultra-smooth and exceptionally reflective surface that shows no signs of being spoiled. This grade is crucial in the fields of optics, medical devices, and luxury brands, where accuracy and detail work are of utmost importance. Achieving an A0 finish requires a very detailed multi-step polishing process to produce a perfect mirror effect.

Figure 2: Different polishing grades
- Key Features:
- The surface is remarkably flawless and undamaged.
- Involves the application of high-volume polishing with ultra-fine abrasives.
- The good thing is that it achieves a surface roughness as low as Ra 0.008 µm.
- Provides superior light reflectivity, crucial for optical applications.
- As it is a sophisticated work, it demands significant time and expertise to achieve the desired finish.
ii) A1 (High-Precision Mirror Finish)
With A1 having a slightly lower polish than A0, the A1 grade has a high reflectivity which aids the grade in having minimal imperfections. It is mostly used in the aerospace and automotive industries, as well as in high-precision molds where smooth surface appearance is a key factor.
- Key Features:
- High reflectivity with a few fractures or blemishes.
- Achieved through the use of fine abrasives and great emphasis on polishing.
- It attains a surface roughness of around Ra 0.016 µm.
- Balances top-quality finish with minimum processing time compared to A0.
- Offers excellent durability for components subjected to high stress.
iii) A2 (Standard Mirror Finish)
Highly polished, the surface reflects light. Speaking generally, this mirror finish may be used where minor surface imperfections are not an issue. A2 grade is widely used in business sectors as there is a margin of minor scratches in large-scale productions. Grade A2 is commonplace in general engineering, decorative pieces, and ordinary parts in the automotive industry. For an A2 grade, a micrometre polishing technique makes use of moderate abrasives so that polishing is cost-effective while maintaining value in quality.
- Key Features:
- Used for general manufacturing and decorative purposes.
- A2 grade achieves a surface roughness of approximately Ra 0.032 µm.
- The good thing is that it is more cost-effective due to reduced processing time.
- Provides a satisfactory aesthetic for non-critical applications.
iv) A3 (Basic Mirror Finish)
A3 is the basic level of polishing type. As a result, there are scratches and unsightly blemishes at the surface which give low reflectivity. A3 mirrors are mostly used for construction equipment and parts of industrial machinery. So, no wonder that the machinery used to create an A3 finish is of low quality and is rough in nature. A broad range of buffing and polishing dressers are used with basic methods to achieve an A3 grade.
- Key Features:
- Coarse abrasives and low-cost basic polishers are used.
- Results in a surface roughness around Ra 0.063 µm.
- As it is the lowest quality grade, it is obvious that it offers the most economical polishing options.
2) Polishing Techniques for Each Grade
The polish technique for every grade varies and so does the amount of abrasives and methods to achieve the desired finish. Below is a detail of how each grade is polished:
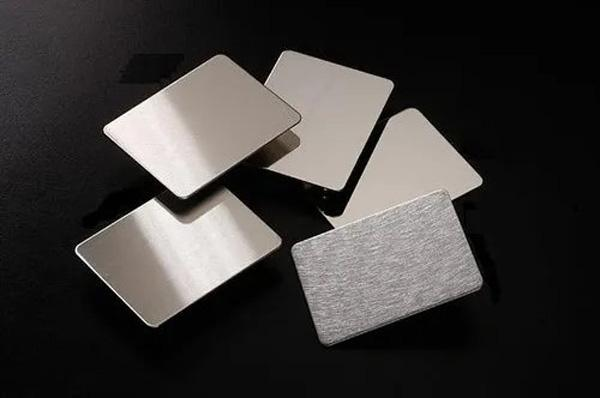
Figure 3: Polishing techniques making a grade difference
a) A0: Multi-polishing using Fine Abrasives and Diamond Pastes
A0 grade polishing is done in steps, where the grade polishing is completed in fine steps. The first step uses abrasives in order to refine ‘rough’ surfaces. The surface is then polished using diamond pastes to provide an ultra-smooth and reflective finish. Such techniques are prevalent in high-end precision tools and optical components.
b) A1: High-precision polish with Fine Abrasives
A1 polishing step uses finer abrasives with a set base to increase surface gloss. Care needs to be taken while doing A1 polishing to prevent scratches on the surface. This method is common for molds, lenses, and other surfaces that require a high degree of clarity.
c) A2: Standard Buffing and Polishing
A2 polishing encompasses simple standard buffing with moderate abrasive forces. It provides a clean and shiny surface but does not reach the gloss levels of A1 and A0 grades. Such a Polish technique is common for general manufacturing and decorations.
d) A3: Polishing With Coarse Abrasives
This stage of polishing is aimed at refining rough edges with the help of coarse abrasives. The process eliminates larger flaws, but a glossy finish is not achieved. This procedure is suitable for pieces that do not require a high-end sheen.
Every level of polishing has a specific target, and the level of shininess and smoothness for every task is distinct. Generally, we can say that to achieve the desired objective, abrasives and approach must be correct.
3) Comparison of Mirror Polishing Grades
Grade | Reflectivity | Surface Smoothness | Common Applications |
A0 | Ultra-High | Flawless, no imperfections | Optical lenses, medical devices, high-end products |
A1 | High | Very smooth, minimal imperfections | Aerospace, automotive, precision tools |
A2 | Moderate | Acceptable minor imperfections | Decorative elements, standard engineering |
A3 | Low | Visible imperfections | Construction materials, machinery parts |
4) Factors Influencing Polishing Outcomes
There are a lot of factors that can impact your polishing results, for example;
- Material being polished: Literally, this is a significant determinant of the polish’s effects. Stainless steel, aluminium and glass will all have specific needs regarding polishing. Stainless steel uses abrasives of high quality to obtain an immaculate finish, but aluminium is softer and more easily scratched. Glass is brittle and requires gentle polishing approaches to avoid surface marks.

Figure 4: Factors affecting polishing results
- Quality of Polishing Equipment and Abrasives: The quality of the finish is determined by the diamond pastes, buffing wheels, and polishing compounds used. In contrast, poor abrasives result in rough surfaces, stains, and a lack of gloss. For dependable, long-term results, the right tools and chemicals must be selected.
- Operator Skill and Polishing Duration: Proficient technicians know how to apply appropriate pressure, adjust the speed of polishing, and use the right tools. If done too fast, the surface will be left unfinished, while a slow pace will increase smoothness and polish. Undoubtedly, the level of detail determines how good the results will be.
- Environmental Factors: The workspace temperature, humidity, and clutter affect the quality of polishing. Clarity will be compromised due to micro-scratches caused by dirt. For consistent, high-quality finishes, there should be minimal noise in the controlled environment.
5) Selecting the Right Polishing Grade
When determining the mirror polishing finish to use, ensure to consider the following pointers for optimal results and efficiency in cost; these pointers cover grades A0 to A3.
- Application Needs: Establish what your application precisely requires. For medical instruments, for example, an A0 finish would be needed since such devices have to have high levels of clarity. In the same breath, construction materials and certain machinery parts do not require much attention to detail, hence they can adequately serve their purpose with an A3 finish.
- Surface Quality Requirements: Identify the level of surface finishing needed. A0 offers a polishing grade ideal for optical applications as it has no imperfections, while A3 offers a basic polishing finish where some defects are visible. Depending on the application, ensure that the required level of finishing surface accuracy is chosen.
- Material in Question: The material being polished influences the achievable finish. Harder materials may require more intensive polishing processes to reach higher grades, while increasing time and cost. Ensure the selected grade is feasible for your material.
- Financial Limitations: Pricing: A0 will be more expensive than A2 and A3 since these grades do not require extensive polishing and therefore serve as a more cost-efficient option.
- Industry Standards: Some industries, such as automotive and aerospace, have set requirements for surface finishes such as an A1 finish, which is a noted surface finish and at the same time cost-effective.
- Durability Requirements: Always consider the working conditions of the component, as the applications may vary. Higher-grade finishes are usually smoother and, as a result, offer better corrosion and wear resistance.
- Aesthetic Considerations: Give primacy to the visual appeal of the product, like in the case of consumer electronics or luxury items: A0 and A01 type situations are favourable. For more functional parts, lower-grade finishes will do.
All these factors need to be analyzed carefully to derive the ideal polishing grade for your application in terms of cost and performance.
6) Conclusion
Now it is clear that flawless polish grade A0 versus functional polish A3 serves different levels of requirements. Never forget the important considerations: what industry is it for? What material will be used? What budget is available? With the right polishing technique, the requirements for long life expectations, favourable performance, and a pleasing appearance of the final product can be achieved. Knowing these parameters allows industries to meet their applications’ needs in regards to the desired level of finishing within budget.