Images of sandy coasts, calm waves, and cozy beach chairs frequently come to mind when we picture a leisurely day at the beach. But how does one make that piece of beach furniture that seems so essential but is so significant? The solution is found in combining modern technology with conventional comfort, especially when it comes to the production process's utilization of CNC (Computer Numerical Control) machinery.
The manufacturing sector has seen significant change in recent years, and CNC machines have been essential in raising productivity and accuracy. CNC machines are instruments that are operated by a computer and are capable of producing complex and well-made parts. The use of CNC technology in the manufacturing of beach chairs has revolutionized the possibilities for creation and manufacturing precision.
Beach chairs have always been connected to leisure and well-being. Their design emphasizes portability and convenience of use, and they are typically constructed with lightweight materials like wood or aluminum and include seating made of canvas or mesh. The chairs' ergonomic design enhances beachgoers' comfort by facilitating their ability to relax and take in the sun. But, how can we use CNC machines for precision crafting? What is the process to follow? Let’s discover it in full detail in this article. But, first, we will talk about the selection of materials.
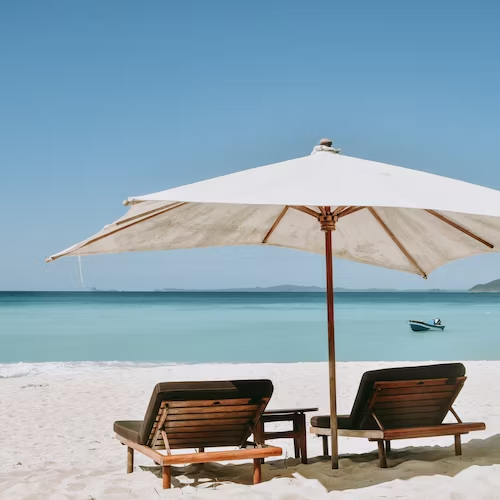
Photo by Sandy Ravaloniaina on Unsplash
Selection of Materials
To guarantee comfort, toughness, and resilience to the extreme weather conditions often found at the beach, selecting the proper materials for a beach chair is crucial. Here we will discuss the materials that are mostly used in beach chair manufacturing.
Material for the Frame:
Choosing the appropriate materials for a beach chair is essential to guarantee its longevity, comfort, and ability to withstand the severe weather conditions commonly seen at the shoreline. When choosing the materials for a beach chair, keep the following in mind:
Aluminum:
It is a common material for beach chair frames since it is strong, lightweight, and resistant to corrosion. It is rust-resistant, lightweight, and non-corrosive when exposed to saltwater.
Stainless Steel:
Despite being heavier than aluminum, stainless steel offers superior resistance against corrosion. It's a good option for beach chairs that need greater stability or may be used more frequently.
White Oak Hardwood:
This hardwood is prized for its toughness and strength. It's an excellent choice for outdoor applications because of its inherent durability against insects and rot. The wood may be formed and fashioned into strong frames that offer a beach chair the stability it needs.
The following describes the various ways that white wood can be used in beach chair elements:
A. Why oak is chosen
Strength, safety, durability, and beauty are all considered in the design and handcrafting of these exquisite beach chairs made of oak wood. Marine spar varnish is used to polish frames made of solid oak wood. These wood beach chairs will provide you with the best possible beach experience due to their sturdy brass hinges and rivets that can survive bad weather, even salty air!
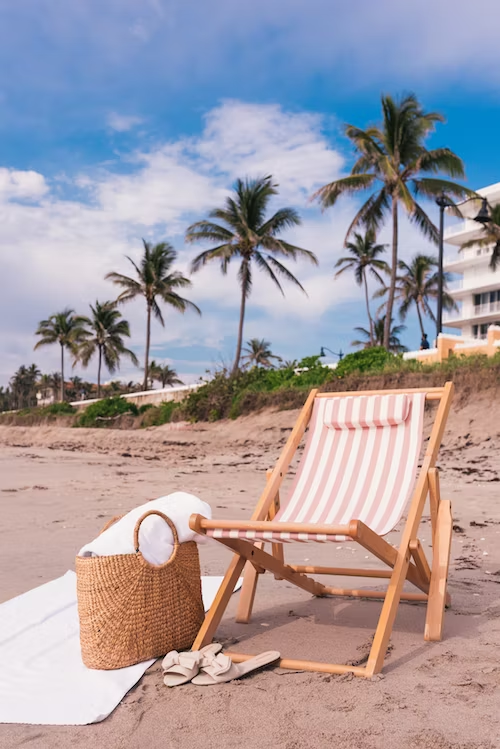
Photo by Arnel Hasanovic on Unsplash
B. Characteristics of oak wood
It is frequently preferred for various reasons:
Durability:
The strength and endurance of white oak are well-known. Because of its strong moisture resistance and tight grain structure, it is less likely to rot, distort, and degrade. Considering that beach chairs are subject to a variety of weather conditions, this is very crucial.
Resistance to Insect Infestations and Decay:
White oak is naturally resistant to both insect infestations and decay because of its chemical composition. This resilience is essential in situations when beach chairs come into contact with the dampness, sand, and salt found in coastal regions.
Stability:
White oak is less prone to shrink or swell in response to variations in humidity because it is dimensionally stable. For the beach chair to remain structurally sound over time, this stability is crucial.
Surface Finish:
White oak has a light color and an eye-catching grain pattern. It is quickly stained or treated to create the desired look. Due to this, it is a well-liked option for furniture where aesthetics count.
Sustainability:
White oak grows slowly, which adds to its dense and resilient qualities. It is frequently harvested from sustainable sources. In the woodworking sector, sustainable practices are becoming more and more significant.
C. Sustainability and Durability
For the following reasons, white oak is frequently regarded as a sturdy and sustainable hardwood:
Adaptability:
Although it grows more slowly than other hardwood species, white oak may regenerate. Replanting trees is a component of sustainable forestry practices, which aim to maintain the long-term stability of the forest ecosystem.
Managed Forests:
Where ethical logging is practiced, managed forests are a major supply of white oak. The goal of sustainable forestry practices is to strike a balance between the preservation of biodiversity and the health of the ecosystem and the extraction of wood.
Density:
One factor in white oak's durability is its density as a hardwood. Its resistance to wear, impact, and insect damage is attributed to its density.
Resistance to deterioration:
White oak is resistant to pest infestations and deterioration because it includes natural compounds like tannins. Its longevity is increased by this resistance, especially in outdoor environments where exposure to the elements is frequent.
CNC Machining Process
Beach chair manufacture relies heavily on CNC (Computer Numerical Control) technology, which provides accuracy, productivity, and flexibility in the process. The technique of CNC machining involves shaping stock material, such as metal, plastic, wood, foam, composite, etc., into unique parts and designs by manipulating machines and cutting tools with the use of computerized controls.
The essential principles of the CNC machining process remain substantially unchanged despite the process offering a variety of capabilities and activities. The following steps comprise the basic CNC machining process: The following explains how beach chair manufacture using CNC:
Detailed Steps of the CNC Process for the Beach Chair
Design Phase:
An intricate computer-aided design (CAD) model of the beach chair is created at the initial stage of the process. Every required measurement, angle, and design element is included in this model.
Programming for CAMs:
Computer-aided manufacturing, or CAM, the software is then used to convert the CAD model into machine-readable code. The CNC machine can make the appropriate chair components by following the instructions in this code, which tells it how to move and control its cutting tools.
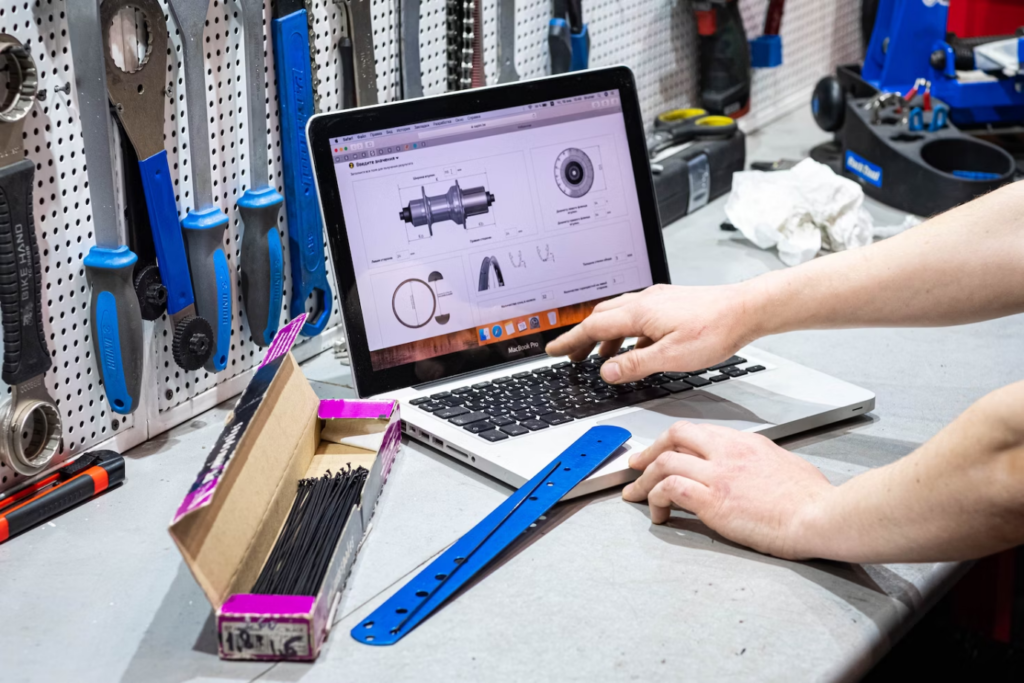
Photo by Anton Savinov on Unsplash
Selection and Preparation of Materials:
Superior wood, such as white oak, is frequently used in the construction of beach chairs. The wood is then roughly blanked, or cut into pieces that are just a little bit bigger than the final chair component proportions.
CNC Configuration:
Clamps or vacuum fixtures hold the rough blanks firmly in place on the CNC machine bed. The machine's control system is programmed using the CNC program that was created using CAM. Here are the basic steps of the CNC machining process.
Creating a CAD model
CAD file conversion to CNC program
Setting up the CNC device
Carrying out the machining process
Tool Adjustments:
Throughout the manufacturing process, the CNC machine may go through tool changes based on the programmed toolpaths. For tasks like drilling, finishing, and roughing, several cutting instruments are utilized.
Unfinished Machining:
Employing larger cutting instruments to swiftly eliminate the extra material and mold the basic structure of the chair components, the CNC machine begins with rough machining operations.
Completion Pass:
The finishing passes are subsequently completed using smaller, finer cutting tools. By refining the surfaces in this step, the CAD model's precise proportions and smooth finishes are achieved.
Engraving:
Intricate features and engraving are included in the design, and the CNC machine is programmed to drill holes for assembly. This process improves the beach chair's appearance and usefulness.
Sanding:
To guarantee a polished and smooth finish, the components are sanded after they have been machined. This process makes the finished product more aesthetically pleasing and comfortable.
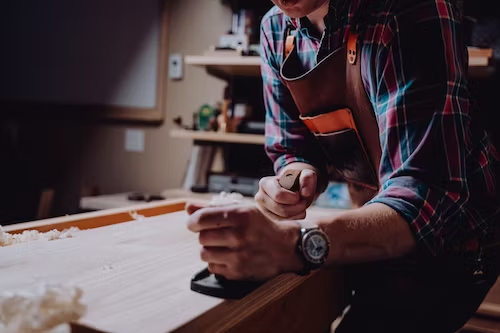
Photo by Bailey Alexander on Unsplash
Assembling:
The assembled beach chair is made up of machined parts. The chair's structural stability is enhanced by the precision with which each component fits together due to CNC machining.
Quality Assurance:
A quality assurance test is performed on the completed beach chairs to make sure they adhere to the design specifications. This entails examining the product for accuracy, fit, completion, and general quality.
B. Benefits of Using CNC for White Oak Wood
There are several advantages of using CNC (Computer Numerical Control) technology in woodworking, and these include improved manufacturing process precision, efficiency, and flexibility. The following are some major benefits of using CNC machining for white oak woodworking:
Accuracy & Precision:
The extreme precision with which CNC machines work guarantees that every bore, carve, and cut is carried out precisely as intended. It is difficult to regularly get this level of accuracy when using manual woodworking techniques.
Exquisite and Complicated Designs:
Complex and detailed designs that would be difficult or impossible to create manually may now be created due to CNC technology. This is especially useful for wood jobs that need complicated forms, engravings, or finely detailed carvings.
Reliability in Manufacturing:
CNC machines are remarkably consistent in producing many identical components. This is essential for preserving consistency and quality, particularly in massive manufacturing cycles.
Effectiveness and Time Reductions:
In a fraction of the time it would take to accomplish tasks using traditional woodworking methods, CNC machines can function swiftly. Faster turnaround times and higher output are the results of this efficiency.
Material Efficiency and Waste Mitigation:
CNC devices reduce waste by optimizing toolpaths and material usage. Efficiently arranging pieces on sheets of raw materials lowers expenses and promotes a more environmentally friendly manufacturing process.
Labor savings and automation:
Numerous operations are automated using CNC machines, which decreases the need for heavy physical labor. Professionals can concentrate on more complex or artistic aspects of woodworking while the CNC machine takes care of monotonous duties.
Iterative design and prototype design:
Iterative design procedures and quick prototyping are made easier by CNC technology. The software allows for quick design modifications, and the CNC machine can generate updated models without requiring a lot of restructuring.
Design and Measurements
A beach chair's design and measurement process takes into account both the chair's functionality and appearance. The general rules and factors for beach chair measurements and design are shown below:
General Layout:
Choose whether the beach chair is folding, reclining, conventional, or modern in style.
To guarantee comfort, take ergonomic design concepts into account. Select a design that complements the brand or the tastes of the target audience.
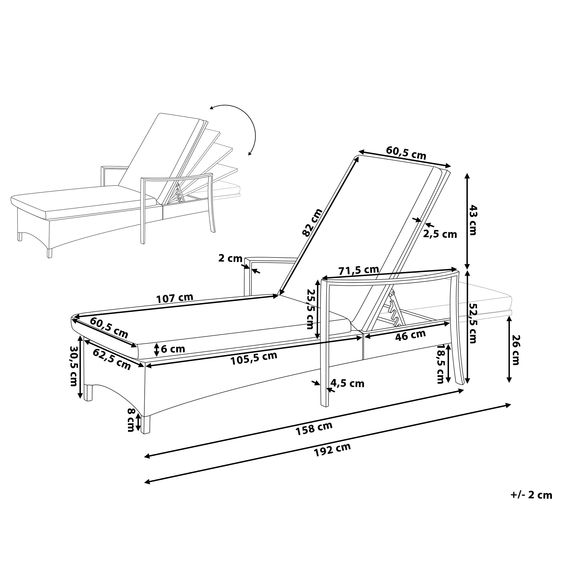
Material Selection:
Choose appropriate materials for the frame, such as metal or aluminum, or weather-resistant wood (such as teak, cedar, or white oak). Select a weatherproof fabric for the seat and backrest to provide longevity and resilience against the weather.
A. Importance of a well-thought-out design
A product's design greatly influences its appearance. An eye-catching beach chair enhances the overall perception of the brand in addition to drawing customers. A unified design can help establish brand identification and make the product recognizable.
Usability and Objective:
Functionality is directly impacted by the design of a product. When it comes to beach chairs, careful design takes into account the chair's intended usage, making sure it satisfies users' needs by offering comfort, stability, and ease.
User Comfort and Experience:
The user experience is given priority in a well-designed device, guaranteeing both comfort and functionality. This implies taking ergonomics into account to improve user comfort while using a beach chair.
Market Effectiveness:
A product with excellent design stands out in a crowded market. It is more probable that customers will select a beach chair that satisfies both their functional needs and visual preferences.
B. Measurements and dimensions for the beach chair
When creating a beach chair, particular proportions, and dimensions play a key role in guaranteeing comfort, functionality, and general usability. The following broad principles correspond to the main dimensions and measurements of a typical beach chair:
Dimensions:
Seat Height: For a comfortable seating position, the standard range is 12 to 18 inches (30 to 46 cm). Seat Width: A good seating space is between 18 and 24 inches (46 and 61 cm) wide.
Seat Depth: For sufficient support, measure between 18 and 24 inches (46 and 61 cm).
For back support, the backrest height should be between 24 and 32 inches (61 and 81 cm).
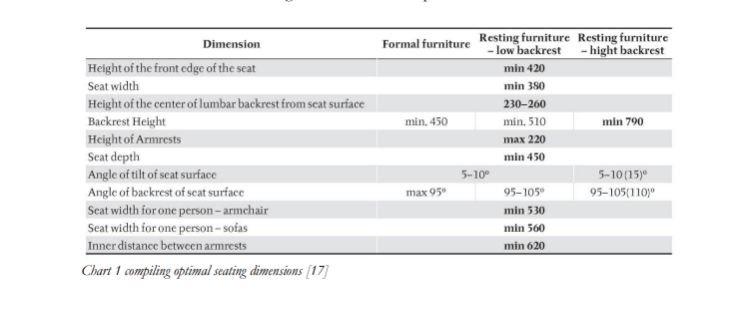
C. Ergonomics and comfort considerations:
For ergonomic comfort, take the body's natural curves into account. To make sure the chair offers enough lumbar support, evaluate models. A crucial factor in design safety. An intelligent design reduces the possibility of mishaps or harm resulting from using the product. This comprises stability, appropriate weight distribution, and structural integrity for a beach chair.
Joinery and Assembly
A beach chair's joinery and assembly are essential processes that guarantee its longevity, stability, and structural integrity. The following describes typical joinery techniques and assembly stages for building a wooden beach chair:
A. Joinery Techniques used in the chair
Joints with mortise and tenon:
It is used in attaching the backrest and seat structure to the legs. A strong joint is formed when the tenon, a projecting component, fits into the mortise, a similar hollow.
Joined Dowels:
Joining different parts together, like securing armrests to legs. To align and secure the two parts, holes are drilled into them and dowels are inserted.
Joined Dovetails:
Attaching other structural components, such as the seat frame. A safe and aesthetically pleasing junction is produced by interlocking wedge-shaped projections (tails and pins).
B. Ensuring Stability and Strength
When making beach chairs, stability and strength are essential for creating a high-quality product that satisfies customers and complies with safety regulations. The following are some crucial factors and procedures to follow when making beach chairs to attain stability and strength:
Engineering and Design:
Make use of engineering principles to create a sturdy and reliable framework. Take into account elements like load-bearing capacity, weight distribution, and the chair's general design. To increase strength and durability, add reinforcements at stress spots like joints and welds.

Welding Methods:
When the chair frame is composed of metal, employ premium welding procedures to ensure that the joints are robust and long-lasting. Make sure that the welds are uniform, smooth, and free of flaws that could reduce their strength.
Workers on the assembly line should adhere to protocols and perform routine quality assurance inspections.
Tests and User Input:
Get customer feedback to find any problems or areas where the beach chair's functioning and design need to be improved. To find out how well the chair works in actual use, do simulated usage scenarios or field testing.
Adherence to the Standards
Make sure the beach chair satisfies all applicable safety and quality requirements for outdoor furniture. Standards established by trade associations or government agencies may fall under this category.
Finishing and Surface Treatment
Beach chairs' surface treatment and finishing are important steps in the production process because they improve the product's weather resistance and durability while also adding to its visual appeal. When making beach chairs, the following factors should be taken into account for surface treatment and finishing:
A. Sanding and Smoothing the Chair
A wooden chair that is going to be surface-finished needs to be sanded and smoothed. Below is the in-depth description of the process:
Required Materials:
Sandpaper in a range of grades, from coarse to fine
Electric sander or sanding block Dust mask
safety eyewear
To prevent breathing in wood particles, work in an area with good ventilation or use a dust mask. Make sure there is no dust or debris on the chair.
B. Options for Finishing (stains, oils, varnishes)
For finishing wood, there are various choices, each with unique qualities and benefits. The type of wood, the intended purpose of the final product, and personal tastes all influence the finish selection. The following are some typical choices for wood finishing:
C. Protecting the Chair from Outdoor Elements
There are several finishing procedures to protect the chair from outdoor weather. Some of the finishing procedure is discussed here.
Varnish:
Polyurethane Varnish:
This long-lasting and protective finish is offered in both water- and oil-based formulas. It is impervious to abrasion, chemicals, and water.
Spar Varnish:
Specially made for outdoor use, spar varnish has ingredients that increase its flexibility and weather resistance. It is frequently utilized for outdoor furniture and maritime applications.
Oils:
Danish Oil:
A varnish and oil mixture, Danish oil provides deep penetration, water resistance, and a natural appearance. It gives an appearance of warmth and hand rubbing.
Linseed Oil:
Made from flaxseed, linseed oil brings out the natural color of the wood and imparts a little water resistance. Compared to other oils, it takes longer to dry.
stains
Oil-Based Stains:
These stains are made of dyes and pigments that have been diluted in oil. They offer some protection while bringing out the natural texture and color of the wood. Compared to water-based stains, oil-based stains take longer to dry.
Water-Based Stains:
Compared to oil-based stains, these stains are typically less hazardous and use water as their base. They smell less and dry more quickly. Oil-based stains have the potential to pierce wood more deeply than water-based stains.
Quality Control and Testing
To guarantee that beach chairs satisfy specified standards and specifications, quality control and testing are essential components of the manufacturing process. The following are some crucial factors for testing and quality assurance in the production of beach chairs:
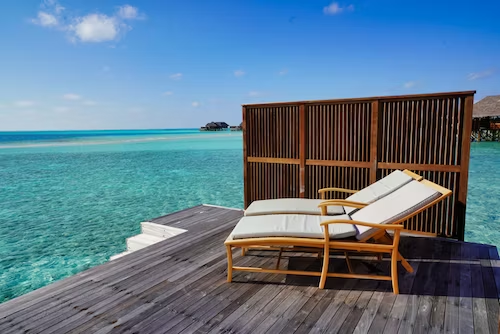
Photo by Datingjungle on Unsplash
A. Checking for Defects or Imperfections:
To find and fix any defects or blemishes, the complete beach chair—including the frame, fabric, and any extra parts—must be carefully inspected. Sharp edges, uneven surfaces, welding flaws, and cosmetic problems are examples of common faults. Maintaining the overall quality and aesthetics of the product is facilitated by identifying and resolving issues during the inspection phase.
Testing for stress to ensure strength and stability:
To evaluate the beach chair's strength and stability in various scenarios, stress tests are crucial. To ensure the chair can support the prescribed load without experiencing structural failure, this may entail adding weight to it. It is helpful to test the chair's resilience to different stressors, including transferring weight or rocking, to make sure it will remain stable under normal usage conditions. It's essential to avoid mishaps or harm to patrons using the beach chair.
Making Sure the Chair Complies with Safety Regulations
Adherence to safety regulations is crucial for the production process. This involves abiding by local, national, and international safety laws and guidelines. Aspects including the materials utilized, structural integrity, fire resistance, and other pertinent elements may be covered by safety regulations. In order to guarantee end users' safety, routine inspections, and testing protocols are put in place to verify that the beach chair satisfies or surpasses these requirements.
Environmental Considerations
Manufacturers have various options to reduce their ecological imprint when it comes to beach chair environmental impact. There are some important environmental factors to take into account when making beach chairs:
To minimize the impact on ecosystems and reduce waste, woodworking practices that are sustainable use eco-friendly techniques and materials.
A product's environmental impact is mostly determined by the materials used. When it comes to beach chairs, the choice of materials for the frame, fabric, and coatings can affect how environmentally friendly the item is overall.
Oak is a popular timber option because of its strength and resilience. Because oak furniture lasts a long time and requires fewer replacements, it can promote sustainability.
Conclusion
A new era of precision craftsmanship has emerged with the combination of white oak's timeless beauty with CNC machining, as demonstrated by the production of beach chairs that are both visually beautiful and long-lasting. Craftspeople can explore new design possibilities while preserving the endurance and purity of their creations because of this combination of technology and tradition.
In addition to being comfortable by the shore, white oak beach chairs made with precision through CNC machining serve as icons of the changing state of workmanship in the twenty-first century. If you have any thoughts about this article let us know by commenting.