Introduction
Current industrial rules necessitate the identification of parts in a way that can be read from a distance, which has led to a rise in the use of laser marking. Manufacturers were compelled to use time-honored techniques like engraving and screen printing to identify products in the marketplace. These methods were temporary at best, expensive at worst, and frequently resulted in defective components.
Laser marking, however, has made it possible for engineers and manufacturers to mark parts with numbers, images, or characters without lowering the standard of the finished product. This method uses concentrated laser beams to etch surfaces, leaving behind legible, undamaged markings that are easy to read.
Various processes, such as engraving, etching, foaming, carbon migration, etc., can be accomplished using laser marking because of the process's adaptability. The proper marking technique should be selected in accordance with the nature of the material and the standards you wish to achieve. Keep reading as we get into the specifics of this cutting-edge approach.
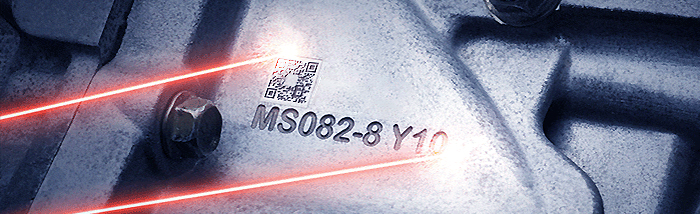
Evolution of laser marking
Albert Einstein pioneered laser technology in the early 1900s, and the first CO2 laser was developed in 1964. Peter Houldcroft of Cambridge's Welding Institute (TWI) developed some of the earliest commercial uses of laser material processing. Manufacturers of vehicles and aircraft components were the primary drivers of early "Laser Machining" applications.
Electrox created the very first commercial axial flow CO2 laser machine, which is now used as a primary component in many lasers marking systems, to enhance computer engravings. The computerization of laser marking is a product of the technological advances of the 1980s and 1990s. Since its introduction in 2001, fiber lasers have become increasingly powerful and contemporary.
Modern laser markers are quicker, more precise, and less harmful to the environment. Laser marking technologies have advanced to the point that they are both flexible and affordable, allowing for the creation of high-quality, long-lasting markings on the surfaces of parts. These technologies are more versatile in terms of the materials they can mark, as well as being quicker and smaller.
The improved power and adaptability of the systems allow for the creation of uniform markings across a wide range of products. As a result, their business objectives are met rapidly and at reduced costs.
What is laser marking?
Simply said, laser marking is the practice of making an indelible mark on a surface using a focused beam of light. Fiber, pulsed, continuous wave, green, or ultraviolet laser equipment is typically used for this procedure.
Steel, titanium, aluminum, copper, porcelain, plastic, glass, wood, paper, and cardboard can all be permanently marked with a laser, and the process may be mechanized and carried out at high speeds. Text (including serial numbers and part numbers), machine-readable data (such as barcodes, Unique ID codes, and 2D Data Matrix codes), and pictures can all be used to label components and final goods.
How does laser marking work?
The surface of a material can be marked with a laser by directing a beam of light to a specific spot on the surface. The qualities of the material as well as its appearance are both changed as a result of the beam's interaction with the surface of the substance. This concentrated beam focuses on only the designated region, which enables the laser marking machine to produce marks that are accurate, of high quality, and in high contrast. These marks are simple to read or scan and may be made on nearly any surface. Because of this property, laser marking is ideally suited for use in situations in which accuracy and durability are essential to achieving success.
When an atom is excited in such a way that it releases light particles, this is the beginning of a laser beam. This light has the capability of being focused and directed at an area that will be marked by a laser. The length of the wavelengths or the number of nanometers used to measure the energy that is released (NM). When the wavelength is increased, the power of the laser beam also increases.
For instance, a UV laser marker, which typically has a wavelength of somewhere around 355 NM, may mark heat-sensitive materials such as plastic and glass with lesser power than traditional lasers. UV laser markers and other machines that fall into the category of "cold laser" emit less energy than traditional lasers, making them excellent options for many organic or soft items. This is because they have a lower risk of burning the material. To mark more difficult materials, such as metal, a fiber laser, which operates at 1070 nanometers, delivers substantially more power than its traditional counterpart.
Laser marking requires less care and consumes no consumables in comparison to other non-permanent marking procedures like printing or labeling.
What are the types of laser marking techniques?
Several laser marking technologies suitable for various uses are currently available. There are advantages and disadvantages to each approach, and deciding which to use ultimately comes down to factors like cost, desired level of quality, and practicality. Okay, let's have a look at a few of these methods.
· Laser Engraving
In this method, laser beams are used to selectively ablate the surfaces of components. To do this, the substance will absorb the laser's heat, melt, and evaporate, leaving behind indentations. The substance reacts with air to change color, further distinguishing the mark.
In laser engraving, you won't need to worry about replacing any parts. Since it doesn't require any specialized inks or drill bits, it has relatively minimal operating expenses. Metals, polymers, and ceramics are just some of the many materials that laser works well with. Therefore, engineers use it for a wide variety of purposes.
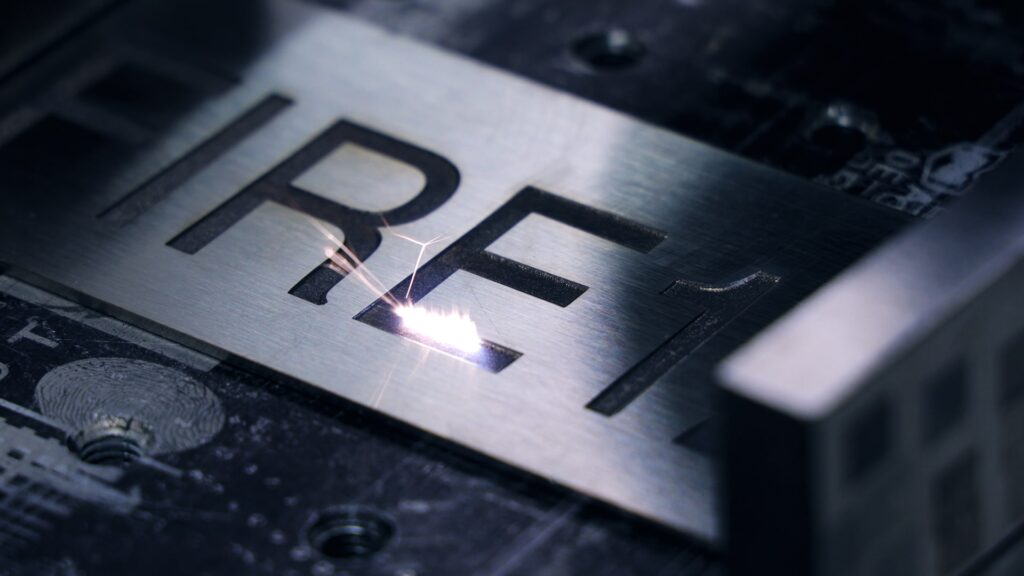
· Laser Etching
This very adaptable method uses heat to leave distinctive imprints on metal. When the laser beam hits a small spot, it raises the surface there. As a result, the surface will overheat, expand, and turn a uniform shade of black, gray, or white.
Serial numbers, data matrix codes, logos, and barcodes are just some of the permanent markings that may be made via etching. As an adaptable method, it works well with many different metals.
Related: Knowing the Variables that Affect the Quality of Laser Etching and Laser Engraving.
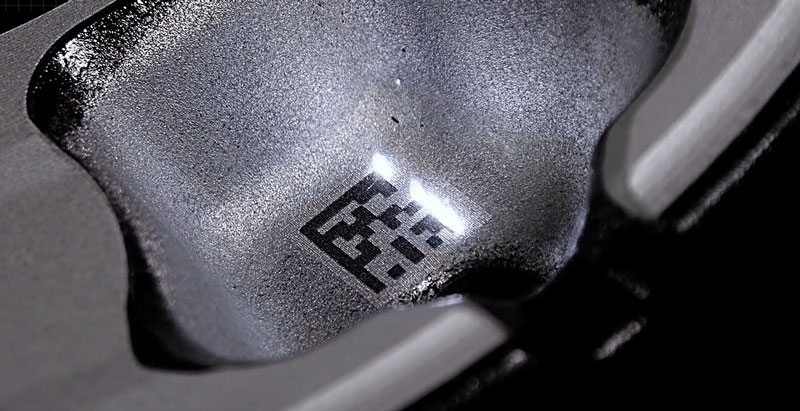
· Laser Annealing
Laser annealing involves making a mark on a substance by locally heating its surface with a focused laser beam. The beam's shallow depth of penetration (20-30 m) means that it has only a little effect on the material's outer layer. The concentrated heat alters the material's hue. Depending on the temperature of the heated layer, the marking could be black, red, yellow, or green.
Laser annealing produces indelible, scratch-proof marks. Ferrous metals and titanium are ideal for laser annealing. This means it has applications beyond the healthcare sector, including the automobile, food & beverage, and aerospace industries.
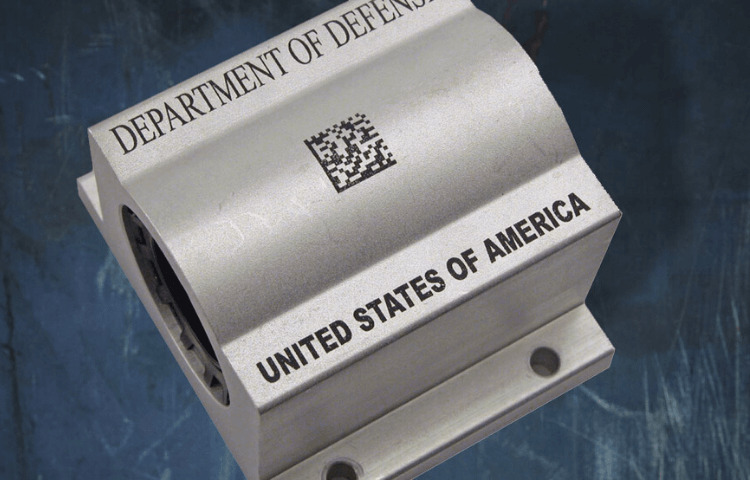
· Carbon Migration
The laser's thermal energy will melt the plastic, releasing oxygen and hydrogen gas. Because of this reaction, the marked region becomes darker, ranging from grey to blue-gray. Marking synthetic polymers and organic materials with carbonizing or carbon migration is always recommended.
You can use it on a wide variety of materials, including paper, wood, leather, plastic, and even some types of packaging. Darker things are less suited to the carbon migration process. The created grey mark will have less contrast than the surrounding material, making it harder to read.
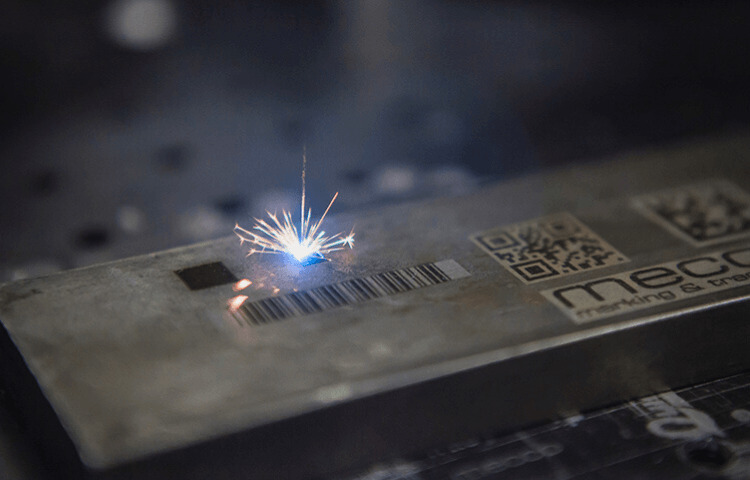
· Foaming
Foaming is better suited to producing light-colored marks than carbon migration is. Melting the material's surface with the laser causes it to release gas bubbles during the process. Oxidation of the gas results in a foaming that scatters light.
When working with components that are already dark in color, this is one of the more effective methods of marking. This is due to the stronger contrast between the mark and the rest of the component's surface, which is why it stands out. Furthermore, it works well as a marking tool for polymers.
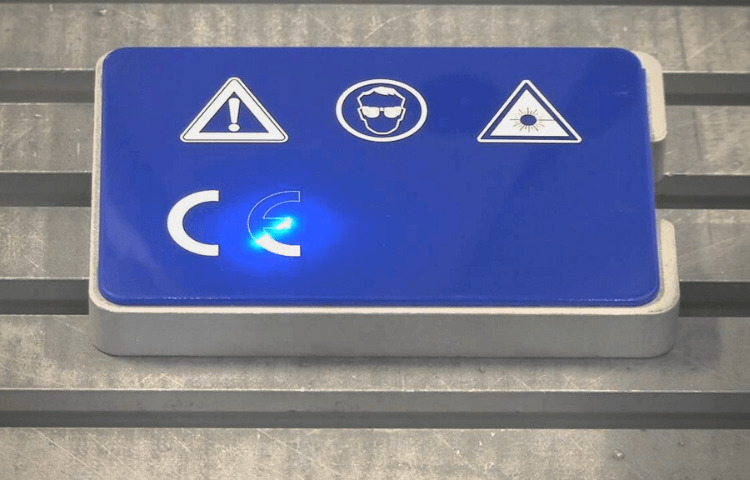
· Discoloration
Layers of the workpiece are cut away with a laser to reveal the layer beneath. In order to create a contrast, the detachable material evaporates after being heated by the laser. Because of this, it's important to use a top coat that stands out from the foundation.
Coated materials, such as anodized aluminum, benefit from this procedure since their markings are more visible and clear. Laminates, films, and foils are alternative materials that tolerate stains well. This method works wonderfully for identifying products on labels, in packing, and on accessories.
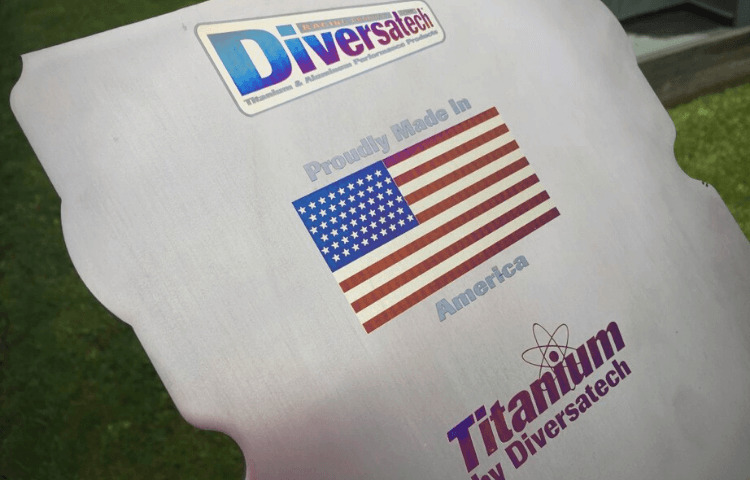
What are the various types of laser markers?
Depending on your needs, you can choose from a wide variety of laser marking equipment. These laser pointers are perfect for a variety of uses and substrates. We'll talk about the most popular laser markers here.
· CO2 Laser markers
These laser marking systems are typically sealed-tube devices with galvo-steered light beams. It's common practice to use CO2 laser markers for a wide variety of product identification markings, including logos, dates, and more. A wide variety of electronic products, as well as integrated circuits, food, and medical packaging, and electronic components, benefit from the use of these devices, which print serial numbers, logos, and barcodes.
The organic materials, such as papers, wood, and some plastic polymers, respond best to the wavelength of sealed CO2 lasers used for marking. They may be used on leather and glass, among other surfaces.
· Fiber Laser markers
These laser markers are among the most powerful currently available, which has contributed to their increased popularity in recent years. These solid-state lasers, with outputs of 20 to 50 watts, are used to increase the mining of the rare-earth element ytterbium. For identifying metals, this metal element's photons, with a wavelength of around 1,090 nm, are perfect.
To engrave or etch in three dimensions, use the fiber laser marking machine. When working with harder metals or when a more powerful system with a smaller spot size is required for more resolution, they provide superior results. These markers are perfect for marking small components in bulk due to their big lenses, good beam quality, and small spot sizes.
· Green laser markers
Green lasers produce light in the green region of the visible spectrum (532 nm) at a relatively low power level (five to ten watts). Marks can be made with them even on extremely shiny surfaces. Furthermore, they feature great precision and exceptional work ease, making them suitable for use with delicate substrates like silicon wafers. Higher absorption by a variety of materials and reduced heat output are hallmarks of these lasers. This makes them perfect for use in flexible plastics, electronic components, printed circuit boards, etc.
· Ultraviolet laser markers
For the purpose of part marking, UV lasers are built with a wavelength of 355 nm, which is extremely absorbent. Because of their high absorption rate, they are ideal for "cold marking," a process that doesn't subject the material to any heat stressors. UV lasers can leave permanent markings on materials including plastic, glass, and ceramic. Additionally, the high-quality laser can be used to micro-mark electrical components and medical devices.
· Nd: YAG Laser Markers
These laser pens are lightweight and portable. Their distinct ability to mark thin sheets of metal without warping or distorting the material has made them very popular. Because of this, it is used by manufacturers for micro markings on a variety of substrates such as aluminum, steel, and other plated metals.
What are the benefits of using a laser marker?
Project managers are now aware of the importance of branding thanks to the development of new marketing tactics. Therefore, laser marking has become an integral element of the production process, assisting with product tracking, reducing counterfeiting, enhancing quality, and more. Markings may be made quickly and precisely, which helps save both time and money.
In order to better appreciate the immense potential of this marking technology, take a look at the following advantages:
· High production speed
Using lasers and computers in laser marking allows for quicker deployment and greater efficiency. With this method, you can use cutting-edge computer software for graphic design while working on your own creations.
Conventional marking techniques necessitate specialized equipment, which lengthens the processing time. Laser marking devices, on the other hand, can be programmed to quickly label objects with a single command. This is an excellent choice if you want to reduce the time it takes to create a product, increase productivity, and cut costs.
· Eco-friendly Production Process
Various marking techniques make use of chemicals and inks to make their marks. These consumables are notorious for their high prices and the detrimental emissions they produce. Laser marking, on the other hand, requires zero consumables. As a result, it is a green method that saves resources and doesn't harm the environment.
This marking method is also non-contact, so it doesn't contaminate the material during processing. While certain printing methods can literally burn the material to the ground, laser marking leaves virtually little lasting damage because it does not actually penetrate the surface.
· Compatible with Most Materials
One can choose from a number of laser marking devices, each of which is capable of marking a wide range of materials. Marking organic materials such as paper, wood, and some plastic polymers yields the greatest results using CO2 lasers.
Like fiber lasers and Nd: YAG lasers.
Steel, aluminum alloys, stainless steel, etc. are all suitable for use with YAG lasers. Marking polymers, glass, and ceramics using a UV laser is possible.
· Consistent Repeatability
Within a mass production setting, laser marking may successfully imprint a design onto a huge number of identical products. This method of marking facilitates the simple incorporation of consistent markers into a manufacturing process. In addition, the reliability is stable, enabling for quicker turnaround times and aesthetically beautiful end results.
· Durability of Marks
Lasers can leave marks that last for a long time and stand out clearly. These permanent markings can endure the elements, as well as abrasion, heat, and acids. As a result, laser markings are the most dependable option for long-lasting marking required for accurate product tracing, as the mark will not fade over time.
· Low maintenance process
No physical touch is made during the laser marking process. Therefore, the laser marking system and the workpiece experience zero mechanical wear. This helps to reduce the amount of time spent on repairs and downtime. Dust buildup on the mirrors is easily cleaned with minimal effort.
What are the applications of laser marking?
Thanks to constantly improving technology, the number of scenarios where laser markings could be used has grown. That's why laser marking technologies are useful in so many different fields nowadays.
Labeling is a necessity for many types of manufactured and retail goods. Items like machine parts, ICs, keyboard buttons, food packaging, medical devices, and PCBs are all examples of this category. Labels with information such as model and serial numbers, QR codes, bar codes, part numbers, logos, dates, etc. can be generated with the aid of laser marking.
Quality control typically necessitates the availability of traceable information. Making permanent marking on a variety of components is facilitated by laser marking as well. Indicators on electronics, smart cards in car parts, and silicon wafers for photovoltaic cells are only a few examples. Potential issues can be immediately identified and addressed in this way.
Conclusion
Precision, durability, and quality markings may all be achieved through the use of laser marking, a procedure that is both flexible and adaptable. This environmentally friendly method is preferable to conventional marking methods since it guarantees rapid production, consistent repetition, and long-lasting marks with no aftercare. As a result, it is a superb option for the purposes you have in mind.