Have you ever wondered how plastic CNC Service works? Did you ever stop and ponder about all the parts and processes involved?
If so, then you've come to the right place!
Here we’ll dive into the intricate details of plastic CNC Service, from what it is to what machines and tools are used in production.
We’ll explore the basics and some of the more advanced techniques, helping you become an expert in no time!
What is Plastic CNC Service?
Plastic CNC service is the process of using computer numerically controlled (CNC) machines to shape and cut plastic materials into desired products. CNC machining is highly precise, allowing for the production of quality components and parts with minimal wastage.
It is used in a variety of industries, from aerospace engineering to the medical industry, making it an extremely versatile form of manufacturing. This type of machining has become popular with toy and model makers and hobbyists due to its affordability, accessibility, and flexibility.
Plastic CNC service involves heat-treating the material before machining it into its component shape or product form; high temperatures are used to soften the plastic so that it can be molded more easily into desired shapes and sizes.
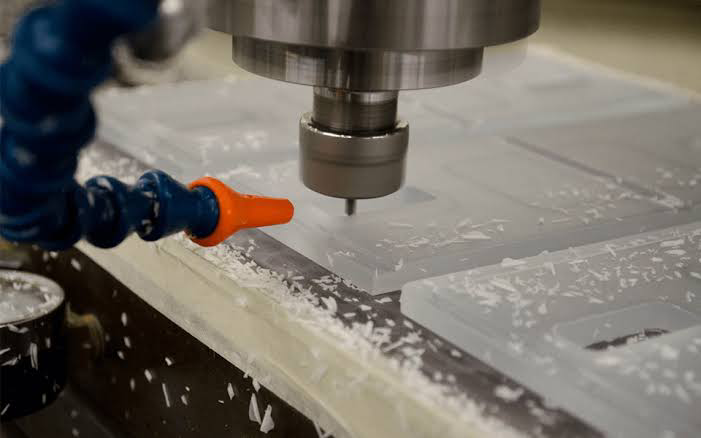
To achieve a polished finish, post-machining processes such as sanding, polishing, and coating may be employed so that the final product looks professional and attractive. Depending on customer specifications and requirements, customized components can also be created using CNC machines by varying the depth of cuts in specific areas or creating intricate patterns within an object.
CNC machined parts have many advantages over traditionally manufactured components; they have greater precision, superior dimensional accuracy, and longer working life expectancy due to tight control over heat levels during manufacturing processes.
In addition, they offer better aesthetic appeal thanks to their smooth surfaces, sharp angles, and uniform dimensions across all sides. With such great benefits, it’s no wonder CNC services are becoming increasingly popular in today’s manufacturing industry!
What Plastic Is Best For Machining?
CNC plastic machining often uses thermoplastic polymers. This is due to the fact that they keep their original characteristics after reforming and rebuilding during melting.
We have compiled a list of common CNC materials to help you see and make an informed decision about the plastic polymer you want to use. But here are some typical plastics that may be used for a wide range of things.
Delrin (POM)
Delrin is a very tough and stiff thermoplastic. It can perform well under high tensile stress, making it an excellent plastic CNC machining material. It can tolerate temperatures up to 12°C without breaking down. Hence it is considered heat resistant.
Nylon (Polyamide)
In the CNC plastic machining industry, nylon is used because of its high purity and semi-crystalline structure, which gives it superior resistance to heat, mechanical stress, and chemicals.
Nylon is a popular material for CNC machining because it is strong, lightweight, and dimensionally stable. It has the properties of a metal, as seen by the phrase "machining nylon is like machining brass." Tungsten carbide alloy CNC tools are recommended for usage with nylon material.
Acrylic
Acrylic is a good plastic for CNC because it is lightweight, has high tensile strength, is resistant to wear, and is stiff. Although there are a few limitations, it is very machineable. In CNC cutting, for instance, the cutting tool must be made of carbide and have a very sharp and aggressive cutting edge in order to produce a flawless surface.
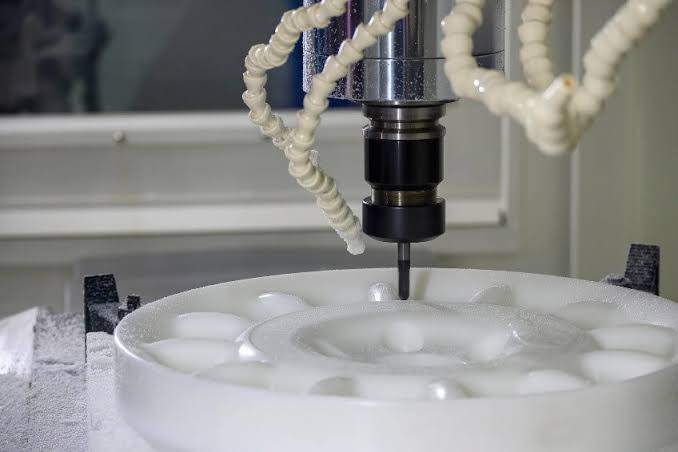
PTFE
Poly-tetrafluoro-ethylene (PTFE), more often known as Teflon, has a high tensile strength in addition to its higher resistance to heat, water, electricity, and chemicals. Due to its low weight and high elasticity, it is frequently used in CNC applications.
It's difficult to attain tight tolerances due to the material's high friction coefficient and tension creep qualities. Therefore, before machining, you or the quick prototyping service you choose should be aware of the consequences of its qualities and the necessary tools.
PEEK
Polyether ether ketone (PEEK) is a class of high-performance polymers with a very high melting point, good resistance to corrosion, and very good mechanical qualities. While PEEK is more commonly used in 3D printing, CNC machining is a great option due to the material's suitability, precision, and repeatability. Although PEEK is widely used for CNC machining, it is important to be familiar with its characteristics to minimize the risk of cracking caused by heat and stress.
UHMW
An additional plastic suitable for CNC machining, UHMW has great mechanical qualities, including high tensile strength and corrosion resistance. Due to its favorable characteristics, it is a preferred material for fast prototyping.
UHMW is a stable material, yet it can be difficult to machine. Machining remains the best choice since it is unable to shape the material. It is best to use a firm that has extensive prior knowledge dealing with the material.
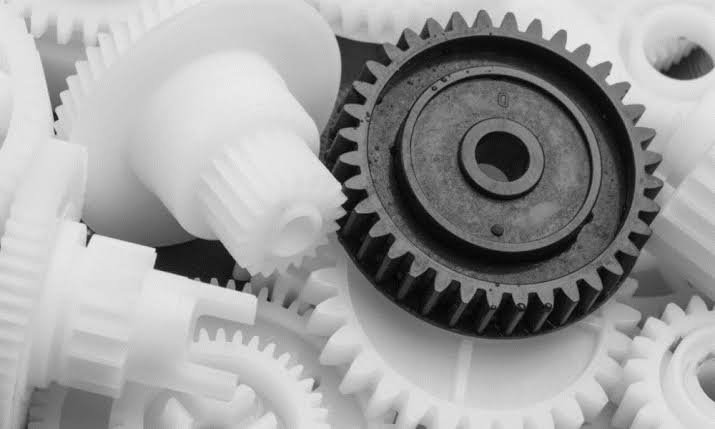
Advantages of Plastic CNC Machining
Plastic CNC machining offers strength, superb surface finish, better dimensional accuracy, and high-speed operations. These services can be employed for cutting hard or soft plastics that are difficult to machine with conventional manufacturing methods. Plastic CNC machining offers multiple advantages over other manufacturing processes.
Advantages of plastic CNC machining include:
Speed
Plastic CNC machining offers high-speed operations that can be used for the rapid production of parts without compromising on quality and precision. The process also allows complex design freedom that could not be achieved using traditional methods.
Precision
With precision plastic CNC machining, highly precise dimensional accuracy can be achieved with a tighter tolerance than other processes such as injection molding and casting. As a result, there are very few post-machining treatment requirements needed after production runs.
Quality
Using multi-axis machines, components with intricate shapes, faces, and angles can easily be achieved while maintaining precise dimensions within the tightest tolerance required by customers’ specifications. This ensures exceptional quality in every part produced by plastic CNC machining service providers.
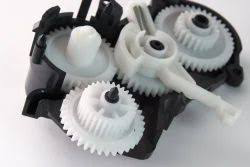
Versatility
Plastic CNC machining is suitable for producing diverse components, including rods, discs, blocks, and plates in any kind of hard or soft materials, which may have required multiple operations if done conventionally in the past.
Disadvantages of Plastic CNC Machining
Plastic CNC Machining is an efficient way to produce accurate and precise components in large quantities. However, there are a few disadvantages associated with this form of machining that you should be aware of before investing in this process.
Slower Process
First, plastic CNC machining can be a slower process than other manufacturing techniques, such as injection molding. This means that it may take longer to create the parts you need since the machine has to move its tool around the material more often than with other processes. This added time can result in longer turnaround times and higher costs associated with the project.
Uneven Surface Finish
Secondly, plastic CNC machining produces a surface finish that may not be as smooth or precise as injection molding or other processes. The cutting tool is constantly moving around different parts of the material which can create a less consistent surface finish than what could be achieved with injection molding or other processes.
If a higher level of precision is required for your part then plastic CNC machining might not be your best choice since there’s greater potential for imperfections in its finished product.
High Levels of Precision and Accuracy
Thirdly, plastic CNC machining requires high levels of precision and accuracy when cutting materials due to its reliance on specialized tools. Poorly maintained machinery and lack of operator experience can lead to accurate cuts and consistent surface finishes resulting in poor-quality parts that need to be then reworked or replaced, which adds additional costs to the project.
Noise and Heat
Finally, plastic CNC machining often produces high levels of noise and heat during operation which can pose safety risks for operators due to prolonged exposure. As such, it's important for businesses employing this process to adhere to relevant safety regulations regarding noise pollution and working conditions for employees operating these machines. Investing in additional ventilation systems, such as fans and dust collectors, can help reduce these risks by providing adequate levels of air circulation inside your workspace.
Plastic CNC Machining Process
Plastic CNC machining is a process that offers a wide range of custom capabilities for many industries, offering tight tolerances and intricate details for production parts. It is a subtractive manufacturing process in which parts are constructed by removing material from plastic blocks or sheets.
The materials that can be machined include thermoplastics such as acrylic, PEEK, and nylon, as well as thermoset plastics such as gypsum and MDF. The setup begins with loading the material into the machine’s work-holding device. CAD/CAM software is then used to direct the tool paths to program the machine for its specific task.
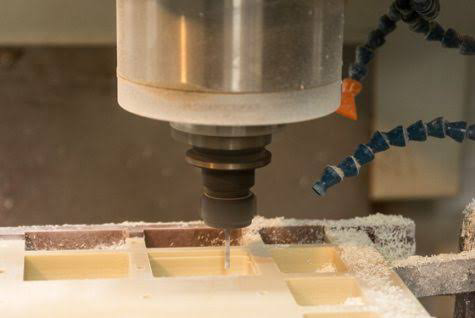
The CNC operator can typically create accurate parts up to ± 0.005 mm in dimension, depending on the size of the part and material used in production. Plastic CNC machining requires specialized tooling such as cutting tools and drill bits, which are analyzed by CAM software prior to running on a CNC machine, ensuring efficient chip load and accuracy.
Chips are constantly being generated while cutting, which must be removed periodically so they do not affect any surface finishes or dimensions of the parts being produced. Some common finishes available with plastic CNC machining include mirror faces, bead blasting, texturing, snubbing, and tumbling, which bring out lustrous finishes but require post-processing to achieve desired results.
Overall, plastic CNC machining offers a cost-effective solution for manufacturing complex components with tight tolerances that cannot be achieved with other prototyping or assembly processes making it ideal for production runs from prototype batches to large-scale operations depending on different application needs.
How To Achieve A Perfect Finish On Plastic Parts?
When working with CNC plastic machining, a flawless finish is achieved via careful technique and material knowledge. The following recommendations can help you avoid this (i.e., have a flawless finish) while manufacturing your plastic product.
- Cutting tools with intricate shapes should be avoided.
- Feed the material no faster than what is specified for that particular substance.
- Machining plastics requires the secure holding of the plastic substance. When materials are not properly clamped, vibration occurs, which in turn causes the plastic's finish to be subpar.
- It's also important to keep the cutting speed within the acceptable range; this range changes depending on the type of plastic you're using.
- An awareness of the various plastic characteristics is crucial to these considerations. Finishing methods like annealing, sandblasting, powder coating, etc. can further enhance the surface finish of any plastic product.
Cost of Plastic CNC Machining
CNC machining is a very cost-effective option for cutting and shaping plastic components with extreme accuracy and consistency. Depending on the type of plastic and the complexity of the component design, CNC services can cost anywhere from several cents for a small component to several hundred dollars for larger, more complex parts.
The most common factors that affect CNC machining costs are material selection, component size, tooling cost, tolerance/accuracy requirements, the complexity of shape/form, and production volumes.
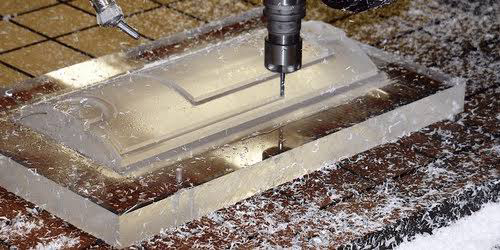
Material selection is also an important factor in price determination since different plastics have different properties which influence the processing time required to produce parts. Some easy-to-machine plastics, such as polyethylene and polyvinyl chloride, will generally have lower costs compared to harder materials like PEEK or Ultem.
Component size is an important consideration since bigger components require larger tooling sets which increase cycle times; this adds extra costs if tight tolerances or complex geometries must be achieved.
Tooling expenses help determine price points due to the equipment needed by CNC machines to shape plastic parts into specific geometries; special getters can be expensive if complex 3D shapes must be cut from a material block.
Tolerance requirements impose limits on how much material can be safely removed without making significant errors; tight tolerances demand expensive dental tools for accurate cuts that increase cycle times resulting in higher assembly costs.
Lastly, production volumes affect CNC machining charges when high quantity orders discount prices by allowing process consolidations that minimize the cost per unit of items produced.
Common Applications of Plastic CNC Machining
Plastic CNC machining provides a range of finishes, from ultra-smooth to textured, depending on the project's needs. CNC-machined plastic parts can also be molded for added depth, increased strength, and a more pleasing aesthetic.
Common applications for plastic CNC machining include:
- Medical components and devices
- Electrical components
- Consumer goods such as toys, sporting goods, and camping gear
- Point of purchase (POP) displays
- Vacuum forming molds
- Highly specialized prototypes
- Grills, fixtures, and trim/sealing products
- Valve seats and seals in the automotive industry
Frequently Asked Questions (FAQs)
Can a CNC machine cut plastic?
CNC devices are not limited to just making cuts and designs in packaging. One of its numerous secondary uses is in foam carving and plastic molding.
What is the best plastic for CNC?
Nylon 66 is robust and long-lasting enough for CNC machining in areas including automobiles and medical devices. This plastic has excellent mechanical properties and a high threshold for wear and tear. Plus, it is resistant to the deteriorating effects of oil and gasoline.
What plastic is easiest for the machine?
Acetal, PEEK, and PVC plastic materials have superior machining characteristics, plus they resist melting and chipping while offering good dimensional stability.
What is the hardest engineering plastic?
Polycarbonate is the strongest plastic available, with a tensile strength of over twenty times that of acrylic and two hundred times that of glass. Because of its high transparency, it is commonly employed in plastic tools that need seeing-through transparent components.
Which plastic is unbreakable?
There are three types of plastic that are impossible to break: polyvinyl chloride (PVC), polyethylene (PE), and polypropylene (PP).
How many types of plastic processing are there?
Plastics can be worked in a wide variety of ways, including machining, compression molding, transfer molding, injection molding, extrusion, rotational molding, blow molding, thermoforming, casting, forging, and foam molding.
What are the 4 classifications of plastic?
Plastic is typically categorized as having a base and side chains made of polymers. Plastic can be broken down into many subgroups the most prominent of which are acrylic, polyester, silicon, halogenated, and polyurethane plastics.
Conclusion
In conclusion, plastic CNC Service offers many benefits to businesses and individuals who need accurate, high-quality parts with quick turnaround times. The process is often more economical than traditional manufacturing techniques and can be completed faster with minimal downtime.
It offers a wide range of materials to choose from, enabling the customer to customize their part to the exact specification they need. Plastic CNC Service is a great way for automotive, medical device, electronics manufacturers, and many other industries to reduce costs while ensuring precision parts are created quickly and efficiently.
Contact us If you need any help selecting which plastic is best for CNC machining or need any services!