In the domain of machining parts manufacturer operation, "speeds and feeds" (or "feeds and speeds") refers to two distinct velocities: cutting speed and feed rate. They are frequently regarded as a pair due to their combined impact on cutting.
Because of its great accuracy and precision, computer numerical control (CNC) machining is among the most popular custom CNC manufacturing techniques today. Its success is mainly attributable to the relative motion between the workpiece and the cutting tool that is CNC-controlled.
Its movements can be categorized as cutting and feeding motions and both are used to quantify them.
But how does cutting speed differ from feed rate? Furthermore, how do these machining parameters affect the outcome of your manufacturing project? All of these queries are answered in this post. So, Let’s get started.
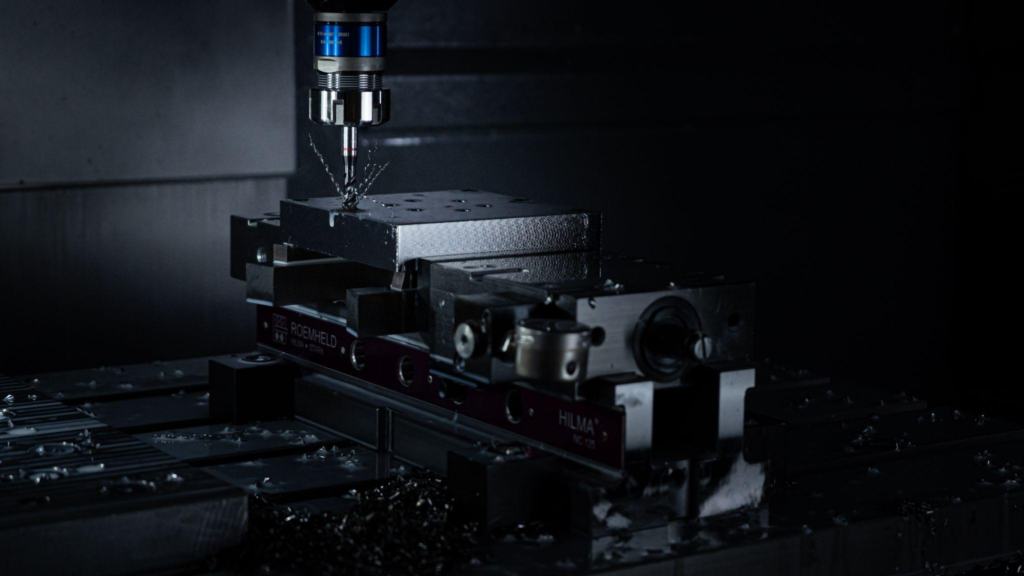
Photo by Daniel Smyth on Unsplash
How Do Feed and Speed Matter in Custom CNC Manufacturer
The primary regulating factors in metal cutting are depth of cut, feed rate, and cutting speed. Cutting tool-workpiece interaction, cutting forces, and surface quality are closely related.
The machinist must comprehend the significance of cutting speeds and feeds in order to operate any CNC milling machine services effectively. If the machines are not set at the right speed and feed for the workpiece, a lot of time might be lost.
Speed and feed both matter in machining parts manufacturing because they control the rate and amount of material removal during machining. The speeds and feeds may have a big impact on a tool's life.
If there is a minor mismatch between the feed rate and speed, the cutting tool will break immediately. To get improved surface roughness, the speeds and feeds are essential. Chatter marks will form on the material surface if the machine is operating at a high tool rate and spindle speed.
The cutting speed rises as the material's softness decreases. The cutting speed also rises as the cutting tool material grows stronger.
On softer materials (aluminum or plastic), where there is a lot of room for mistakes. Thus, the poor impacts of speeds and feeds are not noticeable. On harder materials (such as titanium or Inconel), however, where there is a smaller margin for error, the detrimental effects of speeds and feeds are evident.
Difference Between Feed Rate and Cutting Speed for Customized CNC Manufacturer
It is possible to confuse the two parameters because of their similar sorts of definitions. There are some characteristics also referred by some machinists as the distinction between speeds and feeds. The difference between feed rate and cutting speed is determined by a variety of practical concerns. For instance, these aspects include,
- Temperature:
Cutting temperature is an important component that can affect metrics like tool life and surface roughness, which can explain why there is a disparity between feed rate and cutting speed.
In comparison to cutting speed for feed rate, it has less of an impact on cutting temperature and tool life.
- Speed:
Cutting speed is a measurement of how quickly the tool actually cuts, and feed rate is a measurement of how quickly the tool passes through the material.
- Scallop marking:
The amount of scallop markings present on any portion is directly influenced by the feed rate. Therefore, scallop marks and surface roughness increase as the feed rate increases.
Cutting speed, however, has little impact on scallop markings, and as a result, no impact on surface finishes.
- Chip Direction:
The chip direction does not deviate from vertical in any direction due to the cutting speed. The feed rate will, however, nearly always have an impact on the actual chip flow direction.
- Generatrix and Directrix
The distinction between speeds and feeds is that the directrix is provided by the feed motion, whilst the generatrix is provided by the cutting speed.
A generatrix in geometry is a point or surface that, when moved along a predetermined section, produces a new shape. The directrix is the predetermined path along which the generatrix travels.
The primary objective of CNC milling machine services is to produce geometrical surfaces with superior precision and aesthetically acceptable finishes. Consequently, these two factors are necessary for machining parts manufacturing processes.
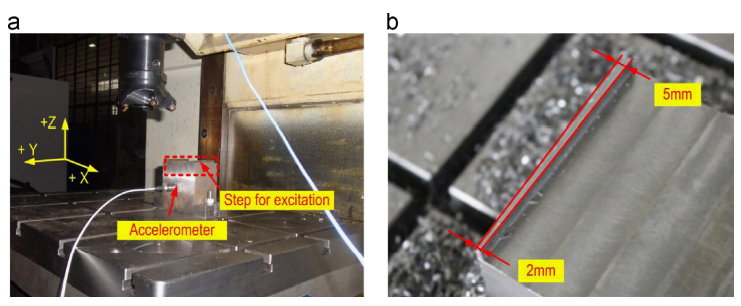
Cutting of small sample (a) test system(b) small width of the sample
How to Measure Feed Rate and Cutting Speed of machining Parts Fabrication
Techniques for choosing the best custom CNC manufacturer parameters are widely valued in the manufacturing sector because they have a major impact on component machining time, part surface quality, and tool life.
The part's material, the tool's size and material, the cutting force, and the depth of cut could all be used to establish the ideal feed rate.
There are two types of proposed methods for determining feed rates: online and off-line methods.
The online methods use force/torque sensors on tools to measure the cutting forces/torques when milling and modify the feed rate in accordance with the measured cutting forces/torques. On-line techniques are not commonly employed in industry, nevertheless, because the control system and sensors are relatively expensive.
On the other hand, the off-line procedures establish various feed rates at various locations and forecast cutting forces in accordance with cutting force models. The current off-line methods interpolate the experimental machining data to calculate the cutting force and estimate the ideal feed rate. The disadvantage of these methods is that the estimated cutting force is typically not reasonable and accurate and the interpolating surface is typically not smooth.
Thus, Prior to machining, the depth of cut and spindle rate is often calculated using machinist manuals, whereas the feed rate is typically determined subjectively by CNC milling machine service operators or programmers.
As a result, the feed rate is fixed at a conservative value, which results in longer machining times or lower tool lives because it is not optimal in terms of the machining conditions at each cutter spot.
All the factors that affect cutting speed and feed rate are depicted below. You'll observe that the feed rate and cutting speed are both based on the spindle speed. Additionally, two formulas are used to calculate the feed rate's final result. You must first identify the feed per tooth. The cutting tool's feed rate is then calculated using that value.
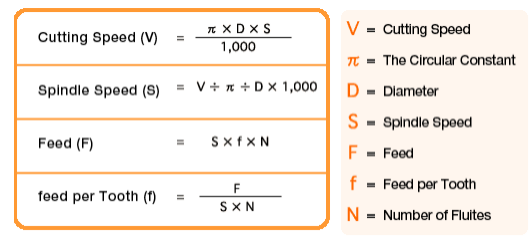
Factors that Impact Feed Rate of Custom CNC Suppliers
Feed rate is the relative speed at which the cutter is moved along the workpiece (also known as feed). In most cases, the units are inches per revolution (in/rev or ipr) or millimeters per revolution (mm/rev) for the distance of each spindle rotation.
There is a number of factors that must be considered while working on a custom CNC machining.
Surface Finishing:
As the feed rate rises, so does the surface roughness. The feed rate is therefore decreased to provide a clean surface finish.
Cut depth:
The chip may become thinner if the cut width is less than half the diameter. This results in production flaws. Feed rate and cut depth increases were accompanied by an increase in cutting forces. The feed rate needs to be raised to alleviate this problem.
TPI:
TPI, or threads per inch, is a unit of measurement related to feed rate. The range of thread pitch of the screws being used determines the feed rate.
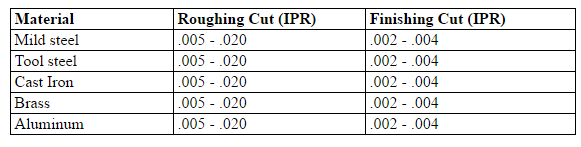
The feed rate for different materials
Factors that Impact Cutting Speed of Custom CNC Fabrication
The cutting speed is the speed difference (relative velocity) between the cutting tool and the surface of the workpiece it is operating on is also known as SFM (surface feet per minute), but is often known as surface speed or just speed. It is measured in terms of the length of the workpiece's surface divided by the speed of time, usually in terms of surface feet per minute (SFM) or meters per minute (m/min).
The number of parameters on cutting speed depends is mentioned below
Cutting Material:
A CNC milling machine can cut a variety of materials, including metals, wood, glass, and others. The cutting tool and the cutting speed are greatly influenced by the thickness and hardness of these materials. If the material is too soft, the cutting tool material will usually tend to swiftly and accurately cut the material. The cutting speed, however, will be slow for tough materials.
Cutting tool material:
The custom CNC supplier uses different kinds of tool materials. It is possible to employ both soft and hard materials. The best cutting speed is influenced by the cutting tool's strength. For example, a cutting tool made of a strong material can be used for cutting at a high speed, whereas a cutting tool made of soft material can be used for cutting at a low speed. Cutting tools for soft materials may wear out quickly at high speeds, much like in the later instance.
Tool's life
Tool life is essentially the time frame during which the cutting tool operates efficiently. The precision of the workpiece and the cutting speed are determined by the tool life.
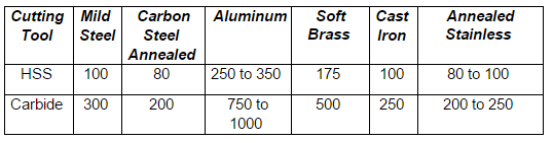
Cutting speed in RPM for recommended six materials
The same variables that the cutting speed impacts are likewise impacted by the feed rate. The sole distinction is the degree to which its effects are perceived. But the ultimate aesthetic quality (the surface finish of the machined part) of the machined object depends on the feed rate.
Conclusion
Only two factors—feed rate and cutting speed—can enhance the efficacy of your CNC machine parts manufacturing process. There are other additional things that might be involved.
In order to maximize the custom CNC manufacturing machinabilities, there are many factors to consider including tool life, power consumption, time, roughness, speeds, and feeds. Thus, to get high precision product machinist should have a good knowledge of feed rate and cutting speed.
BaiChuan Precision is a well-known supplier of CNC milling machines services globally. We not only have cutting-edge CNC machining technology but also have highly skilled engineers and CNC machinists who can complete your product precisely at the first time.
Contact us today if you're concerned about the cutting and feed rates of your customized CNC fabrication items. You will always receive the desired highest quality machined components.