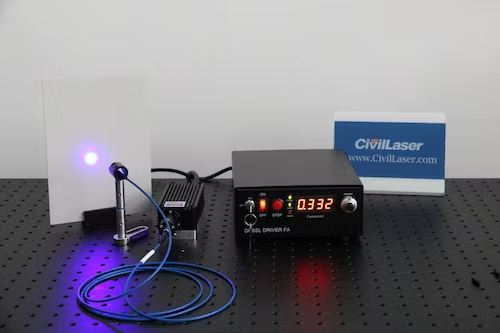
Photo by LaserWorld LaserBeam on Unsplash
The art of marking has evolved to identify essential products, marketing, and verification in the evolving era. To ensure longevity, accuracy, and visual appeal, the best marking technique must be chosen, whether it is for advertisements, commercial components, or customized treasures.
Modern techniques for material treatment include laser technologies. These techniques involve treating the workpiece material on a solid (or diod or liquid) basis with a highly energetic laser beam. Three methods stand out as top contenders among the variety of alternatives: such as laser marking, engraving, and etching.
These variable techniques made complex decisions because each approach has its own set of benefits and factors to take into account. Thus, This blog lays the groundwork for a thorough investigation of these marking methods, illuminating their fundamental ideas, practical uses, and salient distinctions.
The most crucial thing is why you are reading this post. What you will learn at the end of this blog? Guys In order to help you make an informed choice, we'll examine each of these approaches in detail in this article, explaining their advantages, disadvantages, and best uses.
1. Laser Marking
A. Definition and Process
Laser marking is a technique used to label or engrave materials using a focused laser beam. Since there is no direct interaction between the marking tool and the material being marked, laser marking is a precise and clean technique for leaving permanent impressions on many different surfaces.
1. How laser marking works
Interaction of Materials:
A laser beam that is focused onto the surface of a material interacts with the atoms or molecules there.
According to the material and laser parameters, this interaction causes the material to absorb the laser beam's energy, which can have a variety of effects.
Material Modification
A localized change in the material's surface properties, which can include color change, material loss, or a change in reflectivity, is brought on by the absorbed energy.
This modification leaves a noticeable mark on the material.
Interaction of Materials:
A laser beam that is focused onto the surface of a material interacts with the atoms or molecules there.
According to the material and laser parameters, this interaction causes the material to absorb the laser beam's energy, which can have a variety of effects.
Material Modification
A localized change occurs in a material's surface properties due to this absorbed energy, which can include color change, material loss, or a change in reflectivity. This modification leaves a noticeable mark on the surface.
Control and accuracy
Intricate drawings, text, or codes can be accurately marked using laser marking machines' precision control systems, which direct the laser beam.
Lasers Used for Laser Marking:
2. Lasers Used for Laser Marking:
Fiber Laser:
A fiber optic cable is used to transmit the laser beam to the marked surface. For marking metals, polymers, and some ceramics, they are frequently employed. They are well renowned for their effectiveness and great power output.
A CO2 laser:
The laser beam is produced by a gas combination in CO2 lasers. They are mostly utilized for organic materials that consume the CO2 laser's wavelength, such as wood, glass, plastic, and some kinds of metal.
Lasers with diode pumping in solid-state (DPSS):
DPSS lasers are pumped by diode lasers and use a crystal or rod of glass as the energy transfer medium. They are employed to label some metals, ceramics, and polymers.
B. Differences from Engraving and Etching
1. Depth of the mark
These processes differ in the depth at which the laser operates to create the desired pattern. Although laser marking is a phenomenon of the surface, etching operates at about 0.001", and laser engraving removes material at about 0.001"-0.125".
2. Surface Contact
Laser Marking:
During laser marking, there is just a small amount of interaction between the laser and the material's surface. Instead of removing material, it often induces a chemical or physical change in the material that results in a color shift or a minor surface alteration.
Etching:
Compared to laser marking, laser etching includes a deeper engagement with the material's surface. It creates a shallow, frequently exact groove or cavity on the surface by removing a tiny layer of material.
Engraving:
In terms of surface interaction, laser engraving is the most abrasive of the three procedures. To make a deep hollow or indentation, a sizable volume of material must be removed.
C. Applications
A variety of sectors employ accurate and adaptable laser marking technology for a variety of purposes. These are some typical industries and some of the specialized laser marking applications they use:
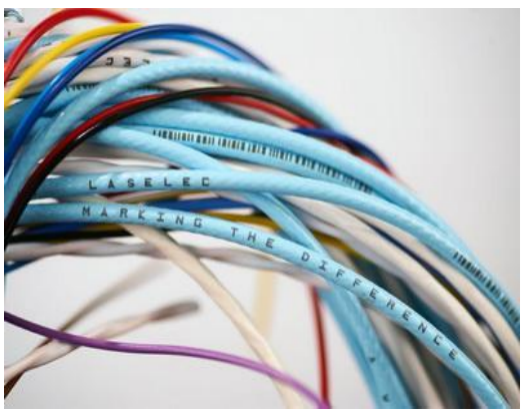
Laser marking on cables
Vehicle Industry:
Vehicle identification numbers (VINs) are marked for traceability.
branding and labeling of vehicle parts.
placing warning labels and safety information on automobiles.
Medical tools and devices:
For traceability, engraving serial numbers and lot codes.
labeling surgical tools for tracking and identifying purposes.
using UDI (Unique Device Identification) codes to ensure compliance with regulations.
Industry for Semiconductors and Electronics:
marking electrical components with logos, serial numbers, and barcodes.
using printed circuit boards (PCBs) to apply labels and identification.
Chips and wafers are engraved for identification.
Defence and aerospace:
Marking the serial numbers, part numbers, and other details on airplane parts. Putting labels in accordance with MIL-SPEC (Military Specifications).
tracking by engraving ammunition and weapons.
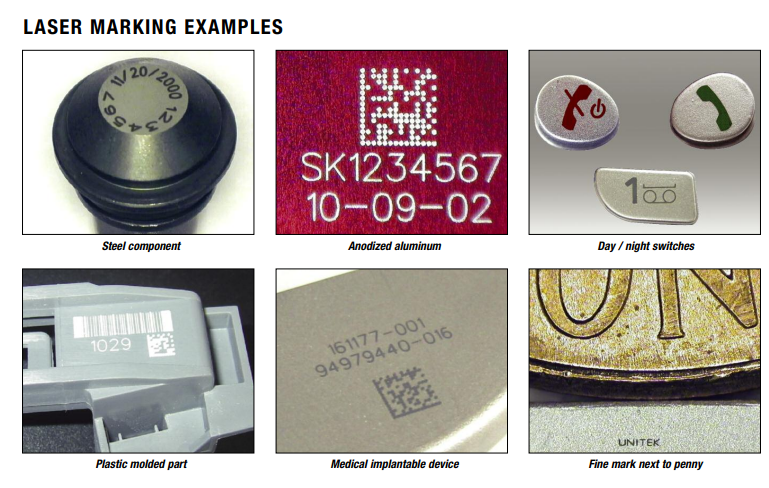
1. Engraving
Engraving is the technique of engraving a pattern or design onto a surface, usually one made of a hard substance like stone, glass, metal, or wood. It is a type of artistic or ornamental ornamentation that has been applied to numerous items for millennia to create elaborate and detailed designs.
There are various steps in the engraving process:
A. Definition and Process
The material melts or evaporates when engraved with a laser because of the laser radiation. This demands a lot of energy. The laser radiation's intensity must be greater than a predetermined threshold intensity. Materials with a high electrical conductivity have particularly high threshold intensities. A conical depression is produced by the beam profile and, when useful, thermal conduction into the base medium.

In this process, the laser beam emitted from a CO2 or fiber laser source is targeted on the desired material surface.
The intended design or marking is produced by the focussed laser beam removing material from the surface.
On the basis of a design, computer software regulates the direction of the laser head and the intensity of the laser beam.
Tools used in engraving
Forming grooves into a hard, flat surface allows for the incising of a design. This procedure is called engraving. The particular engraving tools are dependent on the engraving style and the substance that they're used on. There are many different engraving tools available. Some typical engraving tools are listed below for various engraving techniques: Burin, graver, scraper, and etching needle.
B. Differences from Laser Marking and Etching
Permanent markings can be made on a surface using engraving, laser marking, and etching, however, these techniques vary in terms of their procedures, uses, and outcomes. The following are the main distinctions between etching, laser marking, and engraving:
1. Depth and permanence of the mark
Deep, visible grooves are made in the material during engraving. Depending on the expertise of the engraver, engraving can be quite precise, enabling complex and elaborate designs.
2. Materials suitable for engraving
A variety of materials can be used with the adaptable engraving technique. Here are some typical materials that can be engraved: metal, wood, stone, plastic, and leather.
C. Applications
Engraving is frequently used to create intricate designs for decorative reasons on materials like metals, wood, glass, and stone. It's frequently utilized for things like awards, jewelry, and creative works.

Glass with laser engraved line
3. Etching
Etching is a technique used to carefully remove material from a surface to produce precise patterns or designs in various sectors, including metalworking, electronics, and printmaking. The intended design is left behind after the material is dissolved or abraded using chemicals or physical techniques.
A. Process
Etching is a chemical procedure that includes imprinting a design or mark on a material's surface using an acid or other corrosive agent. Usually, the material is covered with a layer of protection called resist, and then the etchant is applied to remove the exposed sections while maintaining the desired design intact. Here are the steps to follow in this process.
Getting the Surface Ready:
The substrate, which is the substance that will be etched, must first be carefully cleaned to get rid of any impurities like dust, oils, or oxides.
The use of masking material
Applying a masking substance—often referred to as a resist—to the surface. The regions that aren't meant to be etched are shielded by this substance. Wax, photoresist, or specialized etching tape are common masking supplies.
Chemical Etching Exposure
After that, an etching agent or solution is applied to the substrate that has been masked. This chemical dissolves or erodes the substance by reacting with the exposed surfaces.
Washing and Resist Removal:
The substrate undergoes a thorough washing to get rid of any etching agents that may still be on it after the desired depth of etching has been reached. The etched design is then often made visible by removing the resist substance.
Types of Etching Chemicals
There are basically four etching chemicals involved in this process.
Acid etching is the process of selectively removing material from a surface using acids. For etching, common acids include HCl, Nitric acid, Sulfuric Acid(H2SO4), and Ferric Chloride(FeCl3).
Alkaline etching
Plasma etching
Electrochemical etching
Photochemical etching
The material being etched, the level of detail that is wanted, and the particular application all have a role in the choice of etching technique and chemical. Each technique is employed in various fields and applications and has its own benefits.
B. Differences from Laser Marking and Engraving
Surface patterns, designs, or markings can be made by etching, laser marking, or laser engraving. They each use a different set of methods and technology, though, and each has advantages and uses of their own. The main variations between these procedures are as follows:
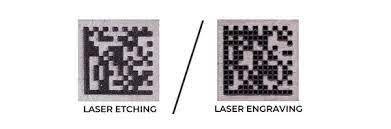
1. Depth of the mark and material removal
Depending on the etching procedure and chemicals employed, etching can produce shallow to deep patterns. Commonly used for metals, glass, ceramics, and occasionally polymers.
2. Precision and refined detail capabilities
Depending on the method employed, significant degrees of accuracy and precision can be achieved.
C. Applications
Etching may produce complex patterns, motifs, or textures on a variety of materials, including metal, glass, ceramics, and even some plastics. It is frequently employed in industries for both aesthetic and practical reasons.
1. Comparative analysis
Three different techniques—etching, laser engraving, and marking—are used to imprint patterns or designs on a variety of materials. Each technique has unique benefits, uses, and restrictions. Now, here is a comparison of these procedures:
Etching:
Applying a mask or resist material to a substrate, then exposing it to an etchant (chemical solution) that selectively eliminates material to generate the desired pattern, is the process of chemical etching.
Materials: Metals, glass, ceramics, and various polymers are frequently used.
Precision: Capable of achieving fine detail; however, depending on the material and etchant employed, the depth of the etching may change.
Speed: Compared to laser processes, it is often slower.
Complexity: Requires specialized chemicals and safety measures.
Cost: For large-scale production, the initial setup expenses might be rather significant.
Impact on the environment: management and disposal of chemicals.
Engraving
Process: To create a pattern or design, the material is removed from the surface using a strong laser.
Materials: Can be applied to a variety of materials, including leather, glass, wood, metals, and plastics.
Precision: High-level precision that can produce incredibly minute details.
Speed: This process is often quicker than chemical etching, though it might vary depending on the material and complexity of the pattern.
Process complexity: Low setup requirements and simple automation. However, modifications can be required for certain materials.
Cost: Initial equipment expenditures may be expensive, but due to lower consumable expenses, long-term running costs may be lower.
Environmental Impact: Chemical processes are typically thought to be less harmful to the environment.
Laser Marking:
Process: This process is similar to engraving, but this is for surface-marking rather than a deep-engraving emphasis.
Material Choice: Similar to laser engraving, this technique can be used on a variety of materials.
Precision: High levels of precision are possible, however, engraving often achieves greater depth.
Speed: Deep engraving takes longer to complete since less material is removed.
Complexity: It's not too difficult to automate and set up, similar to laser engraving.
Initial equipment expenses are comparable to engraving prices, but consumable costs could be lower.
Environmental Impact: In general, chemical etching is thought to be less environmentally friendly.
2. Choosing the right process
Selecting the appropriate Method for your desired material requires following the following parameters precisely.
Material Selection: Consider the substance you're dealing with because not all procedures work well with all materials.
Accuracy and Depth: Consider the degree of accuracy and depth needed for your application.
Volume and Speed: Take into account the needed manufacturing volume and speed. In general, laser processes move more quickly.
Environmental considerations: Laser procedures are often more environmentally friendly if the environmental effect is an issue.
Budget: Assess your spending plan for one-time setup fees and ongoing operational costs.
Regulatory Compliance: Verify that the approach you've selected conforms with any applicable safety or industry regulations.
3. Future Trends and Innovations
Upgrading Automation and Integration
Process automation for laser engraving, marking, and etching will likely keep going. To undertake complex jobs, may require more advanced robotic and computer vision systems.
Accelerated processing rates
Faster processing speeds could result from improvements in laser technology, which would increase the throughput and efficiency of marking and engraving activities.
Capability for several materials:
With advancements, lasers might be able to mark or engrave a wider variety of materials, including some that are typically thought to be difficult, like ceramics, glass, and some polymers.
3D laser Engraving and Marking
With more people using 3D laser marking and engraving, advances in laser technology may enable elaborate designs on challenging surfaces.
Integration of Machine Learning and AI
AI algorithms can be used to tailor laser settings for particular materials and purposes, resulting in more accurate and effective engraving and branding.
4. FAQ
Can any Design be Laser Marked, Etched, or Engraved?
In general, yes. Still, depending on the technique and the substance being utilized, the level of complexity and detail may change. Complex designs could need specialized tools and methods.
8. Does laser engraving last forever?
Permanent laser marks are usually thought of as unique. They are resistant to abrasion, substances, and the elements. The material and the laser settings employed can, however, affect the permanence.
Is there an Ideal Dimension for an Object that Can be Etched, Laser Marked, or Engraved?
According to the size and capabilities of the utilized equipment, there are indeed restrictions. Specialized equipment or many passes could be necessary for large things.
5. Conclusion
Choosing the best marking technique can be crucial in the sector of industrial and aesthetic purposes. whether you're doing labeling for branding purposes, or engraving elaborate designs on jewellery, the technique you choose will have a significant impact on the end product's quality, robustness, and visual appeal. These three methods are frequently used: laser marking, engraving, and etching.
The best marking method should be chosen based on the material, desired mark depth, level of detail, and production volume, among other considerations. Think carefully about these factors, and if you're unsure, seeking advice from a specialist in the area can be incredibly helpful. So, you may also get a consultation from BaiChuan. A leading CNC machining service in China.
Most importantly, you can make sure that your marks are not only practical but also aesthetically pleasing and durable by selecting the right approach. Do you have questions about this blog? Don’t forget to share your thoughts in the comment section below.