Introduction
There is a large variety of materials that are compatible with CNC milling technology, depending on the application for which your design will be used. It's time to choose the best material for your purposes, whether it be metal, plastic, or even wood, once you've decided to use CNC machining to create your product. The most popular CNC milling materials will be covered in the following article, along with an explanation of the applications that each material is most appropriate for.
The adaptability of CNC machining is one of its many benefits. This is due to the fact that precise CNC milling and turning can successfully generate final products from a very wide range of raw materials. This allows design engineers a wide range of alternatives when it comes to making commercial items and prototypes.
How To Choose The Right CNC Machining Materials?
Machining that is computer numerically controlled (CNC) is a method that is quick, effective, precise, and flexible. A wide variety of hard and soft technical materials, such as metals, polymers, semiconductors, and elastomers, are suitable with this production process. It is employed for both the creation of fully functional final products and for prototyping. The material used has a considerable impact on the outcome of a CNC machining project and the functionality of the generated product. This is why considerable consideration must be given to the material selection process in CNC manufacturing.
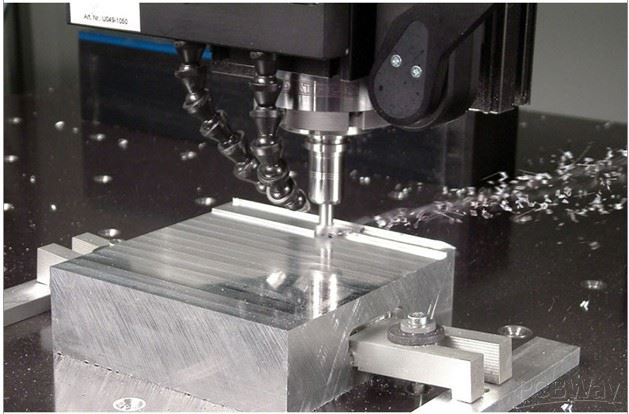
The appropriate material for a CNC machining project is determined by a number of needs and considerations. Do you, for instance, require a substance with superior mechanical qualities? But is a fast rate of production more important? The appropriateness of a material is frequently determined by taking into account a variety of elements. Although not all-inclusive, the following elements will provide a solid foundation when choosing materials for CNC machining.
Metals are typically utilized in applications that call for high strength, hardness, and thermal resistance. Plastics are versatile, lightweight materials that are employed for their electrical insulation and chemical resistance.
In our comparison of CNC materials, we place an emphasis on mechanical strength (represented as tensile yield strength), machinability (the ease of machining has an impact on CNC pricing), cost, hardness (mostly for metals), and temperature resistance (mainly for plastics).
CNC machining parts application
A flexible and economical manufacturing technology is CNC machining. A wide variety of materials are suitable with this procedure. As a result, CNC machining is beneficial for a variety of applications across a wide range of industries. This procedure is utilized in a variety of ways by producers and machinists. This includes using additional processes in conjunction with direct manufacturing procedures, indirect manufacturing processes, or both.
Industry in which the plastics are commonly used
· Medical Industry
For machinists and customers alike, the use of plastics for the manufacturing of parts in a variety of sectors is a no-brainer. Plastic is widely used in a variety of industries because of its low cost and simplicity of machining, including:
New equipment is becoming necessary as medicine evolves quickly. Certain polymers are better suitable for medical applications where safety and cleanliness are crucial due to t0heir special qualities. Additionally, the medical industry demands that its equipment be extremely pure. This necessitates routinely subjecting the machinery to high levels of sterilizing. As they can endure autoclaving repeatedly without degrading, several CNC plastic materials are ideal for this process. Imaging devices, sterilization trays, endoscopic probes, surgical tools, sterilization trays, etc. are some examples of medical equipment that employs plastic.
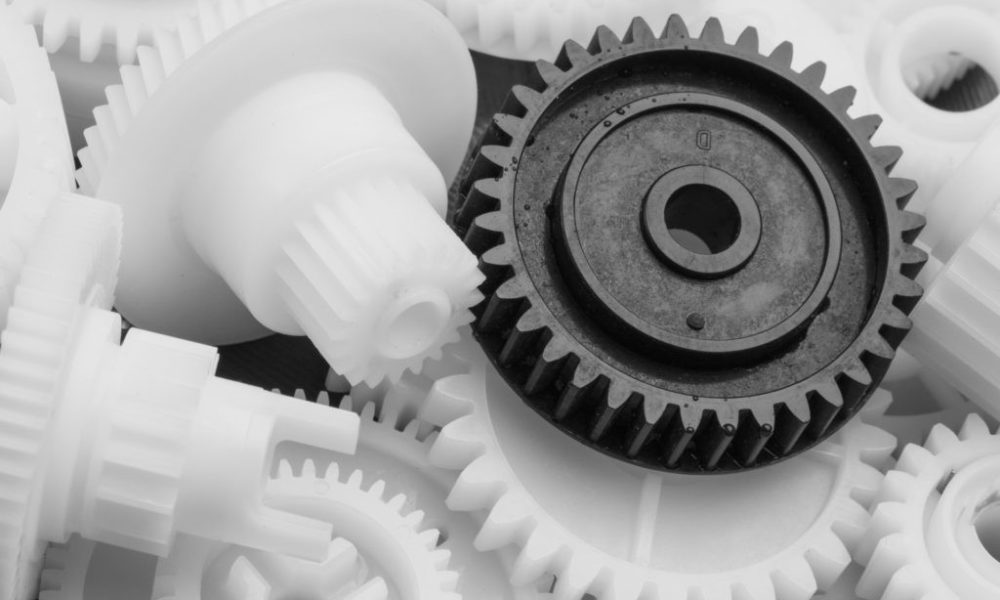
Industry in which the metals are commonly used
· Aerospace industry
CNC machining and the aerospace sector have a long history together. Metal aircraft parts are machined with the highest level of accuracy. For applications that are safety-critical, this is absolutely necessary. Additionally, there are many possibilities available to aerospace engineers thanks to the variety of technical metals suitable with CNC.
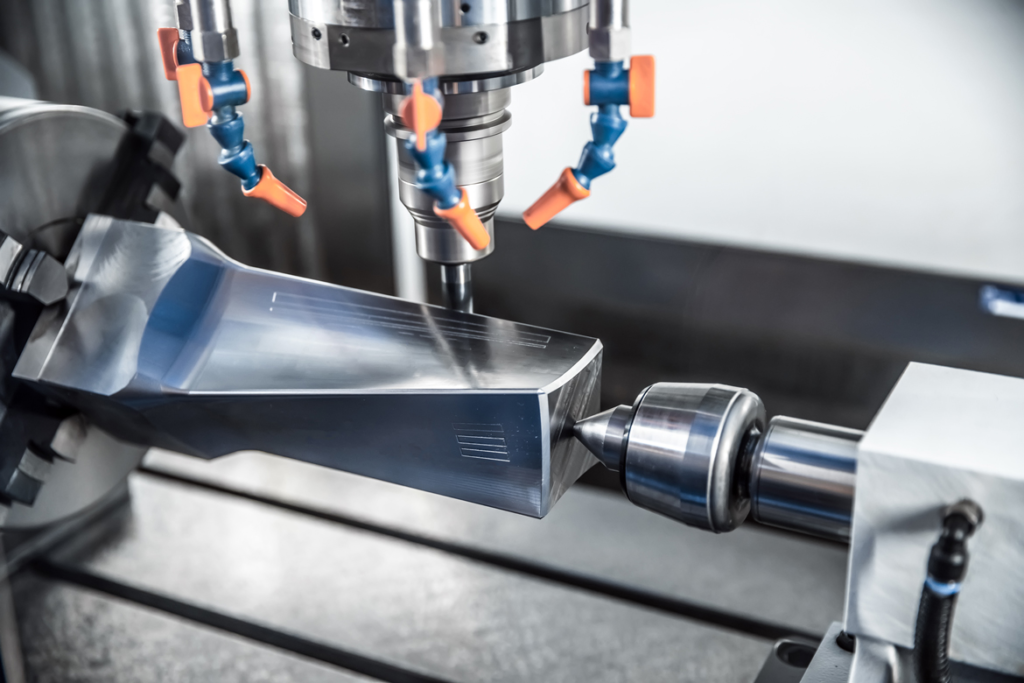
· Automotive industry
CNC milling machines are frequently used in the automotive sector for both production and prototyping. Extruded metal can be machined into a variety of components, including gearboxes, axels, valves, and cylinder blocks. Contrarily, CNC machinery is used to create components like dashboard panels.
Industry in which the wood is commonly used
Today's CNC industry uses wood extensively, but the two sectors that use it the most are the automobile and consumer electronics industries. In the automobile sector, wood is typically used to create the opulent interiors of vehicles, whereas in the electronics sector, wood is typically used to create the outer frame.
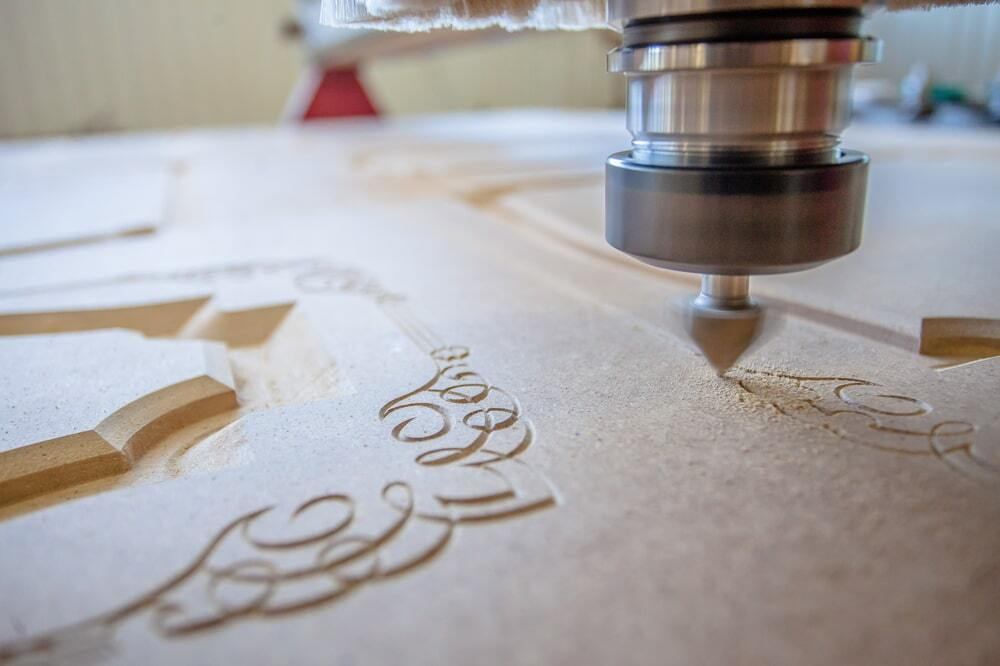
Dimensional Stability and Tolerance
When defining machining tolerances, you must take your material selection into account. The level of tolerance that can be achieved with various materials depends on the specific qualities of each material. These qualities include, among others:
- Hardness
Tight tolerances are more challenging to manufacture from softer materials. This is mostly because they are prone to dimension changes when the cutting tool contacts them. Therefore, when cutting these softer materials, you need to be more patient.
- Abrasiveness
Cutting tools typically have a difficult time with rough and coarse materials, and they may even wear out more quickly as a result. Due to fluctuations in the cutting tool's precision, these materials make it challenging to obtain specific tolerance. The technician typically needs to swap out the tool several times while cutting abrasive materials.
- Heat stability
Non-metals are primarily affected by this problem. During the machining process, these materials begin to lose their shape as heat builds up. This limits the processes you can apply to that specific substance.
Machinability
In actual use, employing machinability-friendly materials offers both immediate and long-term advantages. Using machinable materials can produce better products with tight tolerances, little deformation, and a smooth surface finish in the near future. Compared to parts created from difficult-to-machine materials, they can also be produced more quickly. Long-term use of machinable materials results in less tool wear and a longer tool life, which ultimately saves machine shops money.
So why don't machinists always use the materials that are easiest to work with? The issue is that, oftentimes, machinability is sacrificed for material performance, and vice versa. Engineers frequently have to choose between machinability and performance since strong materials are typically more difficult to cut than weak materials.
The scientific physical characteristics of the material group (what elements it is composed of) and the state of the particular work material are both factors that affect a material's capacity to be machined (how it has been made). While a material's physical characteristics are fixed, a workpiece's state might change significantly.
Cost
The most ideal material for a part may not always be the cheapest. The cost of purchasing such material substantially exceeds the budget for production. It becomes vital to consider additional inexpensive materials. To ascertain whether such a material is a workable low-cost substitute for the most appropriate material, considerable consideration must be given to functionality, strength, hardness, chemical tolerance, electrical characteristics, and other features. For instance, steel 1.4571 has strong machinability and great wear and corrosion resistance. Although it has double the wear resistance of steel 1.7131, it is also twice as expensive. Steel 1.7131 is a great substitute for steel 1.4571 in applications where resistance to wear is the main concern.
Given that CNC machining is a subtractive process—where the machine chips away at the workpiece to create the finished product—material cost is a crucial consideration when choosing CNC materials. As a result, the primary determinant of material choice is the project budget. Make sure the material you select has the needed qualities and falls within your budget.
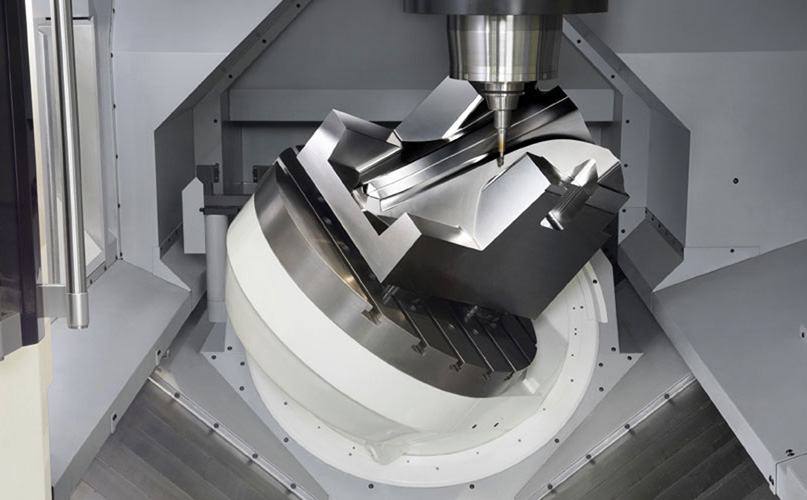
Common materials used in CNC milling
Metals are one of the most popular material types for CNC milling, and there is a wide variety to choose from. Let's examine the most popular options in general and the applications that each metal is best suited for.
· Aluminium
Aluminium is an excellent choice for both mechanical and aspect components, and is perhaps the most often utilised CNC milling material. Aluminum is often easier to process than other metals, making it the most practical material from an economic standpoint. When exposed to the environment, aluminium parts develop a protective layer that adds strength and corrosion resistance. CNC-milled aluminium is perfect for usage in the automotive, aerospace, medical, and consumer electronics industries due to its superior material properties. Aviation fittings, electronic housings, medical equipment, gears and shafts, and other specific uses are only a few examples.
· Steel
The various steel alloys that are offered for CNC milling services are primarily designed for superior machinability. Steel is often used for pieces that require improved formability and stronger welds, even though the particular material qualities vary depending on the alloy (1018, 1215, 12L14, etc. are some regularly used alloys). Commercial items, components that require strong welds, gears and shafts, as well as other high stress applications, are the greatest uses for this material, which vary based on the steel alloy.
· Stainless steel
Utilizing stainless steel alloys has several advantages, including the ability to heat treat them and provide corrosion resistance. Stainless steel has a wide range of possible uses for CNC milling, including medical equipment, electronics hardware, and other items requiring more formability and weldability. Additionally widely used in the
0automotive and aerospace industries are stainless steel alloys.
· Titanium
The high temperature melting point of titanium, which makes it a desirable material for many industries and uses, makes it a special substance. It is regarded as being resistant to corrosion and resistant to ductile, salt, and water. Titanium is a strong, durable material that is biocompatible, lightweight, and suitable for a variety of uses including jewelry, aircraft parts, and medical implants.
· Brass
Brass gives stability where strength sometimes lacks and is one of the simplest and most affordable metal to employ with CNC machining. Medical devices, consumer goods, and electrical hardware and contacts are a few examples of typical uses. Brass is used for applications in engineering, plumbing, steam work, even musical instruments since it has a low coefficient of friction and a high resistance to corrosion.
· Copper
Few metals provide the electric conductivity that copper does for CNC milling materials. High thermal conductivity properties facilitate shaping during CNC machining, and high corrosion resistance helps this material resist rust. Applications used frequently in the automotive sector include cooling systems, heat exchangers, as well as various engineering components like valves and radiators. It's crucial to understand though that copper isn't very strong against some substances, like acids, halogen sulphides, and ammonia solutions.
Conclusion
The material used affects practically every phase of the product life cycle, including prototype, full production, and the performance of the component in its final use. The proper material must be chosen in order to get an entirely optimal finished item.
As a result, choosing the right material is an essential step that must be carefully addressed before starting CNC machining operations. With the aforementioned factors in mind, it is simple to select the material with the greatest fit for the part from the list of options available.