What is Centerless Grinding?
In centerless grinding, the workpiece is held in place between two grinding wheels that rotate at different speeds while moving in the same direction. In order to lessen the force exerted to the workpiece, a grinding wheel revolves on a stationary shaft. At the point of contact, the grinding wheel typically grinds the workpiece by moving more quickly than it does.
The other moveable wheel is positioned to push against the workpiece laterally and often features a rough or rubber-bonded abrasive to catch the workpiece. The grinding effect is produced by varying the relative speeds of the two wheels, and the rotational speed of the grinding wheel is influenced by how quickly the workpiece is being stripped of material.
Grinding without a center involves utilizing a grinding wheel to remove material from a workpiece's outside diameter.
A working blade situated between the adjusting wheel and the grinding wheel is used to support the workpiece, which is situated on its outer diameter. While the grinding wheel removes material, the adjustment wheel propels the machined components.
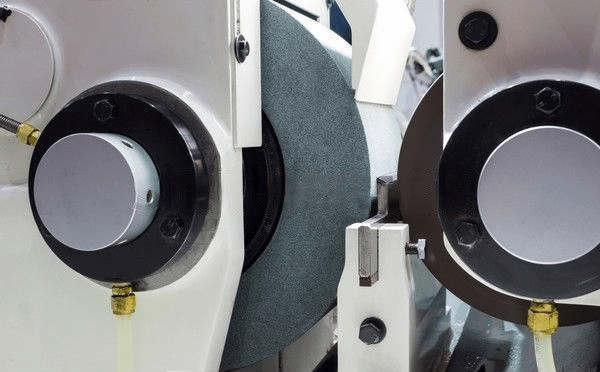
Differences between Centerless and Between Centers
I. Work-holding technique
The method used to hold the workpiece is the primary distinction between these two methods of grinding cylindrical forms. In centerless grinding, it is supported along its axial length, whereas in cylindrical grinding, it is maintained on its axis of rotation, "between centers."
Centers are perfectly ground cones that slide into identical grooves bored onto the workpiece's ends. By clamping the workpiece between a pair of opposing centers, the component is loaded into the machine.
Centers are not used in centerless grinding, as the word indicates. Instead, a regulating wheel that presses the workpiece against the grinding wheel holds it on a long, narrow axis. In centerless grinding, the workpiece is located by its outer diameter while grinding between centers keeps it on its centerline.
The workpiece need not be held between centers while grinding a cylindrical object. An alternative is to employ a collet or chuck jaws.
II. Workpiece Rotation
In centerless grinding, the workpiece is rotated by the grinding wheel, with the rotational speed being controlled by the regulating wheel. This offers the differential motion required for material removal.
In cylindrical grinding, the workpiece rotates in the opposite direction from the wheel. This is accomplished by using a chuck, which typically holds one of the centers, to drive rotation of the workpiece. A driving "dog" that is attached to the workpiece and is rotated in a circle by a pin on the chuck is used to turn the workpiece.
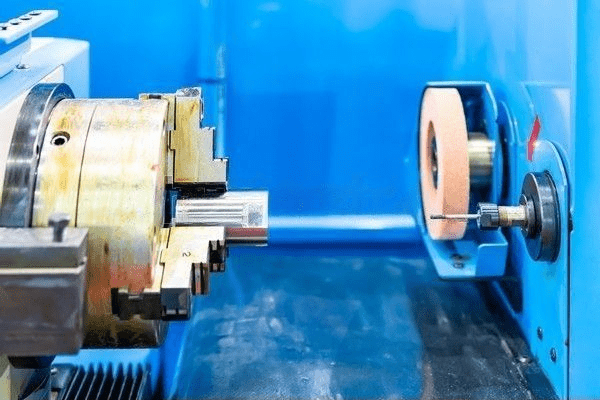
Workpiece on a chuck
Centerless grinding techniques
Centerless grinding comes in three different varieties. The primary distinction is how the workpiece is fed through the machine tool.
In-feed centerless grinding
The upgraded grinding wheel may be used to crush or grind the entire workpiece. The workpiece can have an independent outer diameter over its full length. Any profile may be generated using a plunger feed to perform feed centerless grinding. This is helpful if the workpiece has obstructions that prevent it from passing past the grinding wheel. Shoulders, heads, circles, etc. are examples of obstacles.
Relatively complicated geometries, including hourglass shapes, can be ground using feed centerless grinding. The workpiece must be manually put into the grinder and the adjustment wheel must be set in place before the procedure can begin. The workpiece cannot be passed axially through the machine tool due to the intricacy needed to correctly grind the form of the component and the shape of the grinding wheel.
Thru-feed Centerless Grinding
The workpiece is passed entirely through the grinding wheel in centerless feed-through grinding, entering from one side and exiting from the other. In simple grinding, the adjustment wheel is angled away from the grinding wheel plane to generate an axial force component, which forces the workpiece between the two grinding wheels. Because a separate feed mechanism is not needed, straight feed grinding is particularly efficient. It may only be utilized for components with straightforward cylindrical forms, though.
The workpiece for straight-through grinding can be bigger than the grinding wheel, and the machine can grind many workpieces simultaneously for a higher output.
End feed centerless grinding
The workpiece is axially fed into the machine tool along one side during end feed centerless grinding and rests on the end stop. Once the grinding process is complete, feed the workpiece out of the machine tool by feeding it in the opposite direction. The best applications for face feed grinding are tapered workpieces. For tapered workpieces, face feed grinding works well.
Benefits of centerless grinding
1. No deflection
The regulating wheel firmly supports the workpiece while pressing it against the grinding wheel's abrasive grains. Under the grinding cut and during the whole cut, it is securely secured. Deflection therefore has no place in the process. As an alternative to grinding between centers, this has also permitted heavier passes.
Preventive maintenance allows you to maximize output. The production of materials and the caliber of the end product will be significantly improved if you incorporate proper maintenance into your operation and maintain the appropriate tools and equipment. A rapid correction and routine machine inspection are essential to guaranteeing that you can avoid deflections while flawlessly fulfilling daily production volumes.
2. Extensive processing range
The centerless grinder is excellent for processing delicate workpieces and delicate materials since there isn't any additional pressure applied to either end of the workpiece.
Since these machines function with low tension, it is also possible to grind soft or delicate materials by supporting the workpiece linearly. To avoid the failure brought on by fixation, a fixed workpiece does not need to be prepared for the grinder. Smaller machines can also manage lengthy workpieces.
3. Short loading time
Compared to grinding between centers, the quick loading time enables a continuous operation. The workpiece does not require to be supported in the middle, as the name suggests. The "through-grinding" procedure is applied to the workpiece right away. To achieve the appropriate diameter tolerance and roundness of the bar material, the workpiece must simply be held in position and at the proper height by the work blade.
4. Quick processing reduces production time.
Due to their restricted width, conventional cylindrical grinders require numerous cuts to treat the same item. An astounding 200–300 components may be processed by the centerless grinder per minute (the exact number depends on the size of the part). The centerless grinder's incredible design makes it possible to operate hundreds of pieces without using any physical labor.
5. Capable of handling several parts
A centerless grinder is the tool you need if you want to process a lot of tiny cylindrical pieces since you don't have to reset each one individually. There's no need to worry if you need to process components with various diameters; the centerless grinder can handle varying diameters with a few simple adjustments.
6. Ability to grind brittle and deformed materials
There is no axial thrust applied on the workpiece during centerless grinding, allowing it to grind varied sizes and geometrical figures. Because of the lack of end pressure, the centerless grinder may grind lengthy portions of brittle materials and even deformed components.
7. Longer wheel life
The majority of centerless grinders have a maximum width and diameter both of 24 inches. With a series of grinding wheels, a 17-inch useable grinding wheel may be used to grind thousands of completed pieces. When the center error is removed, the component is in a "floating" state, which lowers tolls and increases the lifespan of the wheels.
8. Tight Tolerance
It is possible to maintain tighter dimensional tolerances using centerless grinding.
Uses Of Centerless Grinding
Centerless grinding may be used to create a huge variety of workpieces and materials. Typical illustrations consist of steel bar stock, needles, both ball and roller bearings, rings for bearing, glass rod, plastic rod, bottle corks, uranium rods, formed spools for valves, axles, stems for valves.
Many sectors, including automotive, aerospace, bearings, consumer goods, glass, medicine, tools, and molds, employ centerless grinding.
Many high-volume vehicle parts require heart grinding in order to be manufactured. These include control rods, camshafts, crankshafts, pistons, sleeves, and rollers.
Additionally, centerless grinding may produce components for the hydraulic and fluid control, medical, and aerospace sectors, in fact, for any application that demands cylindricality and cylindrical surface precision.
Also, centerless grinding is a technique for quickly cleaning up, roughing, and finishing. Workpieces can be shaped into straight or cylindric forms. Both internal and exterior cylindrical forms are possible for workpiece surfaces. Using barrel vibration feeders or other systems that sequentially employ pneumatics, hydraulics, or robotics, the operation is frequently mechanized. This implies that machinery can continue to produce with little oversight.
CNC machining parts China uses advanced CNC grinders to achieve centerless and cylindrical precision grinding. Many of the components that we have expertly machined over the years are displayed in our Product Gallery, which also includes centerless grinding as one of the finishing options. You can count on Kunshan Baichuan to meet your centerless grinding demands. Request an estimate or get started on your next project by contacting our staff.