Arc welding is the name given to a class of welding processes that melt and fuse metal together using an electric arc as the heat source. This method may or may not need pressure or filler metal to create a joint between the metals.
An electric arc is a discharge of electric current across a gap in a circuit, maintained by a thermally ionized column of gas known as plasma. To start the arc, the electrode is briefly touched to the workpiece and then swiftly withdrawn to a short distance, creating the arc. Temperatures beyond 5500°C (10,000°F) are produced by this arc, which is hot enough to melt any metal. Melted metal, consisting of the base metal and, if applicable, filler metal, gathers around the electrode tip. Filler metal is introduced throughout the process of most arc welding procedures in order to increase the volume and strength of the weld joint. The molten pool of weld solidifies and forms a strong bond as the electrode moves along the joint.
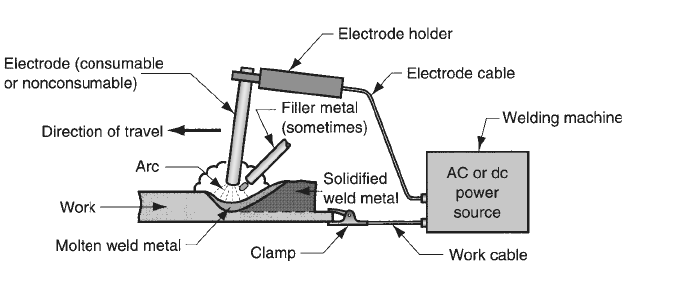
Welders can accomplish this manually or mechanically, using robotic, automatic, or machine welding machines, to move the electrode in relation to the workpiece. Manual arc welding is difficult in that the welder's ability and diligence have a major role in the quality of the weld joint. Arc time, sometimes known as arc-on time, is a common way to assess productivity in arc welding because it represents the percentage of working hours that are dedicated to arc welding activity.
Arc time can be computed with the following formula:
Arc time = (time arc is on) / (hours worked)
Since manual welding requires precise hand-eye coordination, arc time is usually 20% or less because welders must take regular breaks to prevent tiredness. In contrast, depending on the particular operation, arc time might grow to roughly 50% for machine, robotic, and automatic welding, boosting weld consistency and productivity.
General Technology of Arc Welding
Examining some of the broad technical challenges that relate to these processes is important before getting into the specific AW processes.
Electrodes
Electrodes in arc welding are classified into two main categories: consumable and non-consumable. Consumable electrodes provide the filler metal necessary for the weld. These are available as rods (also called sticks) and wires. In general, welding rods have diameters of no more than 9.5 mm (3/8 inch) and lengths ranging from 225 to 450 mm (9 to 18 inches). The occasional replacement of rods, which shortens the welder's arc time, is a drawback of employing them in production welding. However, there can be minimal disruptions when using consumable weld wire, which can be continually fed into the weld pool from spools. When the arc consumes wires and rods, more material is added to the weld junction.
Non-consumable electrodes don't melt; they are mainly composed of tungsten (and very rarely, carbon). Even while these electrodes are said to be non-consumable, they do eventually vaporize out, much like a cutting tool does. Any necessary filler metal must be provided separately when using non-consumable electrodes; this is usually done by feeding a wire into the weld pool.
Arc Shielding
When joining metals at high temperatures, oxygen, nitrogen, and hydrogen in the air can react chemically with the metals. These reactions may cause a significant deterioration of the weld joint's mechanical qualities. Because of this, almost all AW methods include a way to hide the arc from the surrounding air. Arc shielding is achieved by enveloping the molten weld pool, electrode tip, and arc with a layer of gas, flux, or both to prevent the weld metal from being exposed to air. Helium and argon are two inert gases that are frequently used as shields.
When using specific AW techniques to weld ferrous metals, carbon dioxide, and oxygen are typically utilized in conjunction with argon and/or helium to create an oxidizing environment and regulate the form of the weld. A substance called flux is used to dissolve undesired impurities and oxides and stop them from forming, making removal easier. The flux covers the welding process and shields the molten weld metal as it melts and turns into a liquid slag. After cooling, the slag hardens and needs to be scraped out using a chipping or brush. Typically, flux is designed to accomplish three more goals: (1) create a shield for the welding process; (2) maintain the arc; and (3) lessen spattering.
For every process, a different flux application mechanism is used. There are three different ways to apply flux: (1) pouring granular flux directly onto the welding operation; (2) covering the operation with a stick electrode coated in flux material, which melts during the welding process; and (3) using tubular electrodes, which have a core that contains the flux and releases it as the electrode wears down. We go into further detail about these methods in our explanations of the various AW procedures.
Power Source in Arc Welding
Arc welding uses both alternating current (AC) and direct current (DC). AC machines are often limited to the welding of ferrous metals; however, they are less expensive to buy and run. DC equipment is generally known for excellent arc control and may be utilized with good results on all metals.
Arc Welding Processes with Consumable Electrodes
Shielded Metal Arc Welding (SMAW)
The arc welding procedure known as shielded metal arc welding (SMAW) uses a consumable electrode made of a filler metal rod coated in chemicals to act as a shield and flux. Typically, the welding stick has dimensions of 2.5 to 9.5 mm in diameter and 225 to 450 mm in length. Since the composition of the filler metal used in the rod is typically quite similar to that of the base metal, it must be compatible with the metal to be welded. The coating is made up of powdered cellulose (wood and cotton powders), oxides, carbonates, and other materials combined with a silicate binder to hold everything together. Sometimes alloying components and more filler metal are added to the coating by adding metal powders.
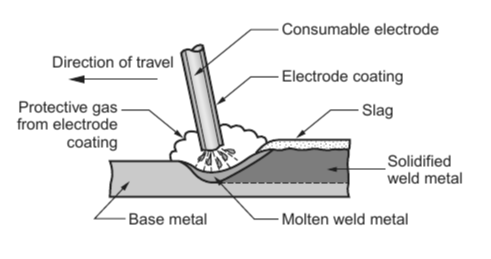
The coating is melted by the heat of the welding process, creating slag and a protective environment for the welding process. It also aids in controlling the rate at which the electrode melts and stabilizing the arc. When the welding stick is in use, its bare metal end—which is the one opposite the welding tip—is secured into an electrode holder that is wired to the power supply. An insulated handle on the holder allows a human welder to grasp and control it. SMAWs usually operate at voltages of 15 to 45 V and currents of 30 to 300 A. The metals being welded, the kind and length of the electrode, and the necessary depth of weld penetration all influence the choice of power parameters.
Manual labor is typically used for shielded metal arc welding. Pipelines, machinery constructions, shipbuilding, job shop fabrication, and repair work are examples of common applications. For thicker portions (over 5 mm/3/16 in), its increased power density makes it the favored method over oxyfuel welding. Being the most cost-effective and portable of all the AW techniques, SMAW is incredibly adaptable.
One drawback to using consumable electrode sticks in shielded metal arc welding as a manufacturing process is this. It is necessary to replace the sticks on a regular basis as they wear down. With this welding procedure, the arc time is shortened. The level that can be used at the moment is another restriction. Current levels must be kept within a safe range while starting a fresh welding stick because the electrode length fluctuates throughout operation and this length influences the resistance heating of the electrode. If this happens, the coating will overheat and melt prematurely. By employing a wire electrode that is continually fed, some alternative AW techniques get beyond the SMAW welding stick length restrictions.
Gas Metal Arc Welding (GMAW)
Gas Metal Arc Welding (GMAW) is a widely used welding process in which a consumable bare metal wire electrode is fed continuously through a welding gun. Gas is flooded into the arc to create shielding, which keeps the weld clean. Automatic feeding of the bare wire from a spool enables continuous operation and economical material use. The choice of wire diameter for GMAW typically depends on the required deposition rate and the thickness of the material to be welded and can range from 0.8 to 6.5 mm (1/32 to 1/4 in).
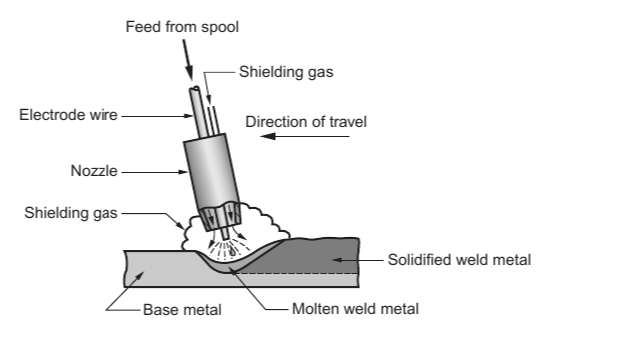
Shielding can be achieved using a variety of gases, including active gases like carbon dioxide and inert gases like argon and helium. The metal being welded, among other things, determines which of these gases should be used. While carbon dioxide is frequently used for welding low- and medium-carbon steels, inert gases are favored for welding aluminum alloys and stainless steels. GMAW is the best method for doing numerous welding passes on a single joint because it uses shielding gases to remove the requirement for manual slag cleaning and grinding.
In the late 1940s, argon was first utilized for welding aluminum using GMAW, which was formerly known as MIG (Metal Inert Gas) welding. The phrase CO2 welding originated when CO2 was used as a more cost-effective shielding gas on steel. Gas combinations, including CO2 and argon, and even oxygen and argon, were used in steel welding as welding techniques improved over time.
For a range of ferrous and nonferrous metals, this welding technique is preferred in fabrication activities. GMAW has a number of advantages over Stick Metal Arc Welding (SMAW). It reduces downtime and increases arc time when done manually by using continuous wire rather than welding sticks. Moreover, the continuous wire feed of GMAW enhances its suitability for automated welding procedures. Furthermore, there is less waste of filler metal because there are no electrode stubs left over, unlike stick welding. This results in higher material utilization.
GMAW is unique in that the process eliminates the need for flux, so slag removal is eliminated. Along with being more adaptable than SMAW, it also boasts better deposition rates. Because of these qualities, which provide efficiency, affordability, and versatility for a range of welding jobs, it is a favored option for numerous industrial applications.
Flux-Cored Arc Welding (FCAW)
Early in the 1950s, flux-cored arc welding (FCAW) was developed as a solution to the drawbacks of stick electrodes in shielded metal arc welding. FCAW uses flux-filled tubing, a continuous consumable electrode, and other materials including alloying elements and deoxidizers. This flexible tubular "wire" comes in coils and is meant to be fed continuously through the welding gun.
FCAW comes in two main types: self-shielded and gas-shielded. The self-shielded variant is not dependent on external shielding gases since it produces gases to protect the arc through flux within the core. Similar to gas metal arc welding (GMAW), the gas-shielded form was designed for welding steel and employs gases that are supplied outside. This type effectively combines parts of SMAW and GMAW by using carbon dioxide for mild steels or a combination of argon and carbon dioxide for stainless steels.
Similar to GMAW, FCAW has benefits such as continuous electrode feeding, which raises output. It produces excellent, smooth, and consistent welds when welding steel and stainless steel of different thicknesses. The method is favored in many industrial applications due to its efficiency and versatility.
As seen in the illustration below, FCAW can distinguish between the two types of processes by using optional shielding gasses.
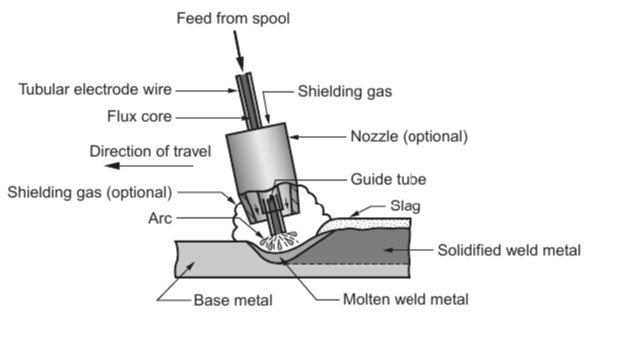
Electro-gas Welding (EGW)
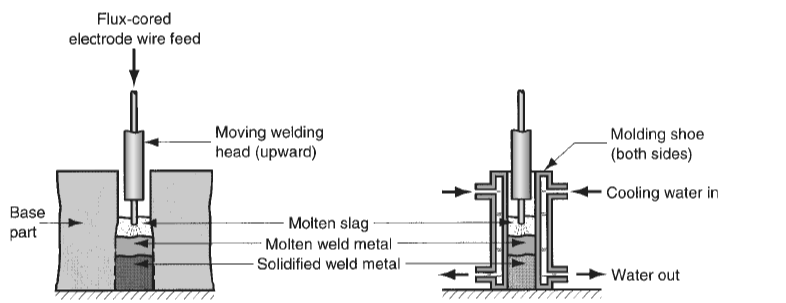
The AW procedure known as electro-gas welding (EGW) uses molding shoes to hold the molten metal in place together with a continuous consumable electrode (either flux-cored wire or bare wire with externally supplied shielding gases). Vertical butt welding is the main use of this technology. The procedure can be regarded as a specific application of self-shielded FCAW when the flux-cored electrode wire is used since no external gases are supplied. A unique instance of GMAW occurs when a bare electrode wire is utilized in conjunction with shielding gasses from an outside source. To avoid being added to the weld pool, the molding shoes are water cooled. In conjunction with the edges of the components undergoing welding, the shoes create a hollow akin to a mold that is gradually filled with molten metal from the electrode and base portions. A moving weld head that travels vertically upward completes the procedure automatically in one pass, filling the cavity.
The main industries that use electro-gas welding are shipbuilding and the construction of large storage tanks. These industries use steel (low- and medium-carbon, low-alloy, and certain stainless steels). EGW can handle stock thicknesses ranging from 12 to 75 mm. It can also be used for fillet and groove welds, always in a vertical orientation, in addition to butt welding. It is occasionally necessary to construct specially designed molding shoes for the associated joint shapes.
Submerged Arc Welding (SAW)
Submerged arc welding (SAW) is an arc-welding process that employs a continuous, consumable bare wire electrode, with arc shielding provided by a blanket of granular flux. An automated coil feeds the electrode wire into the arc. According to the figure below, the flux is deposited into the joint by gravity from a hopper just in front of the weld arc. The welding process is fully submerged in the blanket of granular flux, eliminating radiation, sparks, and splatter that is so dangerous in other AW techniques. As a result, the fairly bulky face shield needed for the other operations—safety glasses and protective gloves, of course—need not be worn by the welding operator in SAW.
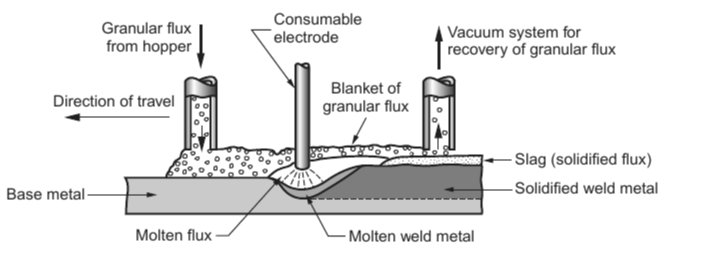
A glass-like slag is formed on top of the weld joint when the flux next to the arc melts and mixes with the molten metal to eliminate impurities. A superior weld joint with remarkable toughness and ductility is produced by the slag and unfused flux grains on top, which also act as good thermal insulation and atmospheric protection for the weld region. The weld area cools gradually as a result of this excellent protection. Welding residue that has not been fused can be retrieved and reused, as illustrated in the figure. Usually by hand, the solid slag covering the weld needs to be chipped away.
Submerged arc welding is frequently utilized in the manufacture of structural steel shapes, welding components for heavy machinery, and longitudinal and circumferential seams for large-diameter pipelines, tanks, and pressure vessels. Steel plates of a thickness of 25 mm (1.0 in) or more are frequently welded in these types of applications. High-carbon steels, tool steels, and the majority of nonferrous metals cannot be easily welded using SAW; only low-carbon, low-alloy, and stainless steels can. The pieces must always be oriented horizontally due to the granular flux's gravity feed, and a backup plate is frequently needed underneath the junction while welding.
Arc Welding Processes with Non-Consumable Electrodes
Gas Tungsten Arc Welding (GTAW/TIG)
Gas tungsten arc welding (GTAW) is an arc welding procedure that combines a non-consumable tungsten electrode and an inert gas to shield the arc. It is sometimes referred to as tungsten inert gas (TIG) welding, or WIG welding in Europe (with the "W" standing for Wolfram, the chemical symbol for tungsten). You can use this technique with or without a filler metal. In contrast to consumable electrode techniques, where filler metal is carried across the arc, it is introduced separately from a rod or wire and melted by the heat of the arc.
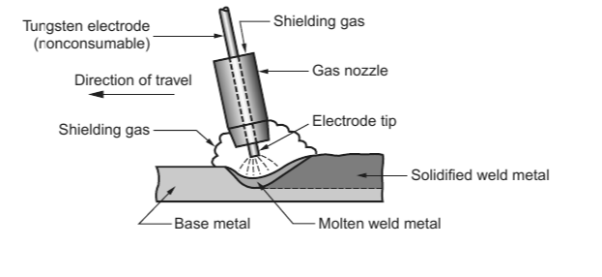
Tungsten's high melting point of 3410 degrees Celsius (6170 degrees Fahrenheit) makes it an excellent material for electrodes. Standard shielding gases consist of helium, argon, or a combination of these gas components. Almost any metal in a wide variety of stock thicknesses can be worked with using GTAW. It can also be applied to the connecting of different alloy combinations that are not the same. Stainless steel and aluminum are the materials it is most frequently used on.
It is challenging to use GTAW to weld cast irons, wrought irons, and naturally, tungsten. Except in situations involving tiny sections and the need for extremely high-quality welds, GTAW is often slower and more expensive than disposable electrode AW methods in steel welding applications. Filler metal is typically not used when TIG welding thin sheets to tight tolerances. For all types of joints, the procedure can be carried out manually, mechanically, or automatically. When performed properly, GTAW may produce high-quality welds with little to no weld spatter because no filler metal is transmitted across the arc and requires little to no post-weld cleaning because no flux is utilized.
Plasma Arc Welding (PAW)
Plasma arc welding (PAW) is an advanced variant of gas tungsten arc welding (GTAW), where a constricted plasma arc is directed at the welding area. In PAW, a tungsten electrode is encased in a specially designed nozzle that channels a high-velocity stream of inert gas, such as argon or argon–hydrogen mixtures, into the arc region to generate an intensely hot plasma arc stream. The gases used for arc shielding include argon, argon–hydrogen, and helium. Plasma arc welding can reach temperatures up to 17,000°C (30,000°F) or higher, sufficient to melt any known metal. The high temperatures in PAW, significantly higher than those in GTAW, are due to the constricted arc. Despite using lower power levels than GTAW, PAW achieves a highly concentrated plasma jet with a small diameter and high-power density.
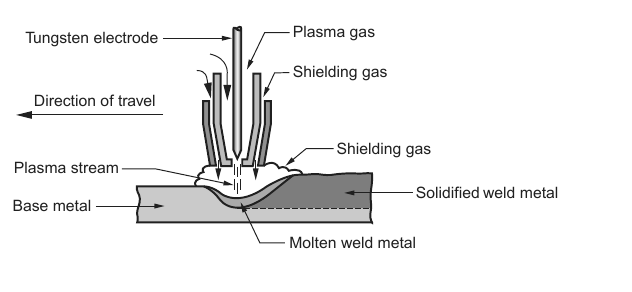
After being developed in the 1960s, plasma arc welding grew in popularity gradually. However, its use as a GTAW replacement has grown recently in a number of applications, including home appliances, metal cabinets, door and window frames, and automotive subassemblies. For the purpose of welding most metals from 0.02 to 6 mm (0.001 to 0.250 in.), the plasma arc welding (PAW) technique offers an extremely steady heat source. The PAW method produces higher enthalpy (heat content), better arc stability, higher energy concentration, and higher welding rates (than with GTAW) due to its superior penetration capabilities. These benefits put it ahead of other open arc welding techniques including SMAW, GMAW, and GTAW. It also creates more thorough joint penetration and smaller beads (a higher depth-to-width ratio) in the "keyhole" mode, which leads to less distortion.
The PAW technique allows for the possibility of three main welding variants. These varieties of arcs are needle, melt-in, and keyhole modes. Needle arc welding is particularly helpful for welding thin metals (0.02 to 1.5 mm [0.001 to 0.062 in.]). It gets its name from the lengthy, "needle-like" arc that is produced at low currents (1 to 25 A). This thickness range of manual welding is a significant change from earlier GTAW process techniques, which called for precisely robotic torch movement with the same fixturing. Nonetheless, the weld produced by either method is smooth and devoid of filler metal.
High current manual PAW is performed in the melt-in mode. This method is suitable for welding butt or lap joints on materials 0.8 to 3 mm (1/32 to 1/8 in.) thick and can be used to join a variety of materials, including titanium and other reactive metals, using helium as a shielding gas. Typically, the operating current does not exceed 100 A. The "keyhole" mode refers to a penetrating hole at the leading edge of the weld puddle, which then flows behind the keyhole to form the weld bead. This technique is applicable to most metals within the 2.4 to 6 mm (3/32 to 1/4 in.) thickness range and is a key differentiator between PAW and GTAW processes. The operating current for keyhole mode typically reaches up to 275 amperes.
However, welding lead, magnesium, bronze, and cast irons is a challenging task for PAW. Two other disadvantages that may make access difficult in some joint configurations are high equipment costs and a larger torch size than in other arc welding techniques.
Other Arc-Welding and Related Processes
Apart from the standard arc welding (AW) techniques, there exist a few specialty procedures that are noteworthy. Carbon Arc Welding (CAW) is one method that uses a non-consumable carbon electrode, specifically graphite. While CAW is historically significant as the original arc-welding technique, its current commercial value is negligible. It is still utilized, nevertheless, as a heat source for brazing, iron casting repair, and applying compounds that are resistant to wear on surfaces. Tungsten electrodes, which are utilized in procedures like Gas Tungsten Arc Welding (GTAW) and Plasma Arc Welding (PAW), have gradually supplanted graphite electrodes in welding.
Stud Welding (SW) is another specialized AW procedure used to weld studs or similar components to base parts. Figure below shows a typical SW operation where shielding is achieved by the use of a ceramic ferrule. First, the stud is inserted into a specialized weld gun, which regulates the power and timing of the steps as they are displayed in the sequence automatically. The worker merely needs to pull the trigger after aligning the gun correctly against the base work part that the stud will be fastened to. Applications for SW include heat radiation fins on equipment, threaded fasteners for connecting handles to cookware, and similar assembly scenarios. Stud welding typically offers advantages over manually arc-welded attachments, drilled and tapped holes, and rivets in high-production processes.
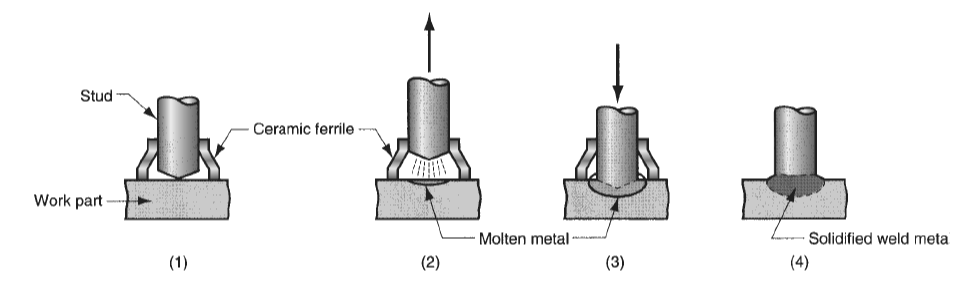
References
Groover, M.P., 2010. Fundamentals of Modern Manufacturing: Materials, Processes, and Systems. 4th ed. Hoboken, NJ: John Wiley & Sons, Inc.