Introduction
Cutting manufacturing costs is frequently the top issue when it comes to computer numerical control (CNC) machining, whether you're constructing a single prototype or a large-scale production run. Fortunately, design choices can help you save money. Simply following design for machinability standards can result in low-cost parts that meet functional design criteria.
This article is full of useful information to help you improve your design. First, let's look at what causes CNC machining costs to rise. Then, to help you save money on your project, we publish detailed guidelines with tried-and-true design tips.

How to Estimate CNC Machining Prices
The cost of CNC machining is determined by a number of factors, including the amount of time it takes to complete the project and the type of machine utilized, such as three- and five-axis machines. For their various types of machinery, CNC machining shops often set their own hourly rates. Five-axis CNC machines, for example, often cost more, although three-axis machines typically cost less.
Keep in mind that these are merely the operating costs of the CNC machines. These can be used as a starting point, but you should also include labor costs. In addition, there are a number of additional elements that might influence the pricing of CNC components, which we will discuss in the next section. Because prices vary, it's a good idea to consult with possible CNC shops before placing an order so you know how it will influence your budget.

Factors that affect CNC machining cost
· Costs of CNC Machine
The cost of machining varies depending on the machine type. 3 axis and multi-axis machines are the most common machinery used to manufacture parts utilizing CNC machining.
The cost of a machine is also determined by elements such as the equipment's size and weight, speed, power, and configuration.
CNC milling is more expensive than other types of machining procedures because it involves more complicated pieces. The cost of machining increases as the number of axes on the milling machines increases. In the instance of 5 axis machining, for example, it is more expensive than 3 axis machines.
· Quantity of the order
The quantity of parts in each order determines the total cost of CNC machining. This is the case since producing large orders is more expensive. Greater part numbers, on the other hand, usually imply lower extra unit costs. Larger orders, on the other hand, may increase production costs but lower the client's cost-per-part ratio. Small orders, on the other hand, are initially less expensive but may end up costing the client more money in the long run.
· Time for machining
The time it takes to complete the machining of each CNC machined product is also important in determining the CNC machining cost. The rule of thumb is that the more time spent machining, the higher the machining cost, which adds up to the basic setup cost.
Software like CAM, which requires a 3D CAD design model, may estimate the amount of time it will take to complete a job. Completing a project with a high level of complexity takes more time.
If manual labor is required to assemble, finish, or post-process the items, the additional cost is added to the labor cost. If the finished product is being delivered from the machine shop to a client at a separate site, the additional labor cost is also applied.
· Labor Cost
When compared to manual machining, one of the advantages of CNC machining is that it minimizes the number of laborers involved in the manufacturing process. The key labor expense is the professional designer who creates the 3D CAD design model for manufacturing, which grows in complexity as the desired product becomes more sophisticated.
Even if you are required to create additional pieces, the cost of machining each part remains the same. Then there's the cost of labor to operate the CNC machine, which goes up as the number of hours required to finish the machining of the part grows.
If manual labor is required to assemble, finish, or post-process the items, the additional cost is added to the labor cost. If the finished product is being delivered from the machine shop to a client at a separate site, the additional labor cost is also applied.
· Complexity of the process
The difficulty of each component varies. And, of course, the more complicated an item is to manufacture — involving more process activities, machines, and operators — the more it costs. The cost of machines and equipment is directly proportional to the cost of the item, and all machining operations add up.
The cost of a machine rises in proportion to its size and capability. Larger machines are more expensive and so have a greater load rate. They also increase complexity and risk, and they usually necessitate the use of a more skilled operator.
Work cells can be set up to conduct processes in parallel to maximize efficiency, knowing that process time increases cost. Multiple CNC machines are run in tandem by a cell operator, which reduces labor expenses. Similarly, value-added processes like pressure testing and assembly are frequently undertaken during the machining cycle to save total production time.
· Cost of the materials
The cost of materials is also crucial when estimating the cost of CNC machining. The cost of a CNC machine-made final product is determined by the materials used to create it. It's possible that you'll be asked to make anything out of plastic or metal.
Plastic or aluminum materials have a lower machining cost than stainless steel since they are less expensive and have a lower durability. To construct the 3D item, the material is taken from the solid blocks in the same way as it is done in CNC machines. As a result, the necessary raw material will be greater than the finished product's material.
The machinists purchase the materials in solid blocks and determine the product's cost per block. Aluminum, Stainless Steel, and Brass are the most widely utilized metals in CNC machining.
Aluminum is used in CNC machines by most machinists because of its low cost and high machinability.
Due of their poor machinability, stainless steel and brass are more expensive than aluminium. Because titanium alloy is the most expensive of all these metals, its machining cost will be the greatest because it may necessitate the use of specialised tools to produce the parts.
In the case of plastics, the cost of the bulk material is lower, the tools required are likewise lower, and the time necessary to process plastics such as Nylon, Delrin, and ABS is shorter.
· Design and Geometry
In many ways, part geometry has an impact on CNC cost. The greater the part's size, the more materials will be required in the manufacturing process, raising the cost. On the other side, the more complicated the part, the more difficult the machining process becomes, and the manufacturing cycle lengthens, increasing the cost. The part will be processed slower and may even need to be discarded if it has features that are easier to deal with. On the other hand, if the tool is difficult to finish or requires numerous operations to complete, the part will be processed slower and may even need to be discarded.
· Precision and tolerance
CNC machining with tight tolerances and great precision always has a higher price tag. Designers should provide drawings based on the manufacturing function since the part does not need to set up unique tight tolerances unless it is necessary in specific instances. Tight tolerances are normally reserved for parts that interact with other parts. Aside from that, tight tolerances are especially difficult to attain on your part's internal surfaces, and machining holes or cavities might result in burrs, which take extra effort to remove.
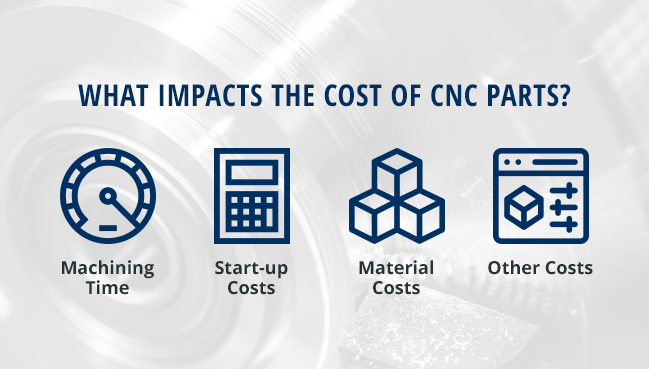
Tips To Save CNC Machining Cost
Changes in CNC machining time, start-up costs, materials costs, and other factors can all help you save money. You won't be able to adjust some product requirements, but taking efforts to guarantee your design is optimal will save you a lot of money. Here are some of our recommendations for cutting CNC machining costs.
· Internal Corners that are Rounded
Machines must come to a halt at sharp, 90-degree corners, rotate the part, and then restart the process. As you can expect, these extra stages add time to the machining process and frequently result in increased costs. CNC machining costs can be reduced by changing the interior corner patterns of your product.
If you change your design to include rounded corners, the machine will be able to produce your product continually, lowering your costs. Take it a step further by ensuring that the radius of your interior corners is at least 1/3 of the cavity's depth. Larger radii at the corners allow larger tools to cut them more efficiently, rather than requiring a small tool to travel over a smaller radius corner many times.
- Deep Pockets Should Be Avoided
Because attaining deep pockets necessitates removing a large amount of material, deep pockets can have a detrimental influence on CNC machining costs. Removing material takes time and may necessitate the use of a specialized instrument to achieve the desired depth.
Limit the depth of your design's pockets to four times the length. When it comes to cutting pockets, CNC tools have a limit — preferably, a depth of two to three times their diameter. Cutting the diameter up to four times is conceivable, but it will be more expensive
- Use tight tolerances in limited amounts
When you design a part with a tight tolerance, the cost goes up since the machining time goes up and you have to perform a human inspection. Unfortunately, precise tolerances on the inside surfaces of your product are particularly difficult to attain, as cutting holes and other cavities can cause burrs on the edges. Beyond the manual inspection, these burrs necessitate a deburring procedure. Deburring is a time-consuming and laborious technique that raises CNC machining costs.
If the design does not specify a tolerance, the usual tolerance of 0.010 thousandths or greater is utilized. This standard tolerance works well for many features, therefore any tight tolerances you have should be reconsidered, and you should only define tight tolerance when it's really necessary. If you have sophisticated design skills, you can further minimize the cost of CNC machining by taking advantage of the looser tolerances that come with them.
One more point on tolerances: the numbers that reflect your dimensions are crucial since they describe the amount of precision you need for your product. That level of accuracy determines which tool will be used to machine it in CNC machining. The more decimal places you add, the more complicated the instrument becomes, and the more expensive it becomes. Make sure your design doesn't have any needless decimal points.
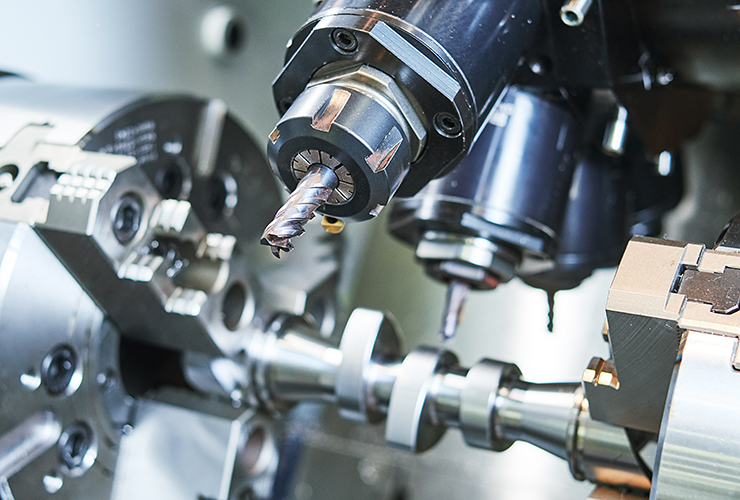
- Thin Walls should be expanded
Because thin walls are delicate, they take longer to machine. To avoid errors or cracks, thin walls are machined in many passes with shallow setting depths. The placement of holes and threads near the edge of the part is a common cause of thin walls. They should be strategically placed.
Thick walls provide more stability and are less expensive to machine. Design metal parts with walls thicker than 0.8 millimetres and plastic parts with walls thicker than 1.5 millimetres if weight isn't an issue.
- Thread Length Should Be Limited
Threads that are longer than 1.5 times the diameter of the hole may not strengthen the connection, and threads that are longer than necessary may incur additional expenditures due to the necessity of special tools to generate them.
When designing your component, specify a maximum length of three times the hole diameter to save money. Keep in mind that threads in blind holes should have a half-diameter unthreaded section at the end.
- Tapped Holes Should Be Optimized
When it comes to tapped holes, depth and tap size are the two aspects that influence cost. As previously stated, lengthening a thread past a point does not make the part any stronger. Going deeper than three times the hole diameter increases the chance of breaking the tap and adds time to the process, both of which can add to the cost. Small threads increase to expenses since they necessitate hand tapping, which takes time and is risky.
Limiting your depth to three times the hole diameter and using conventional tap sizes in your design instead will help you save money on CNC machining. For example, your design may call for 3-48 taps, but switching to a more common size of 4-40 taps could save you money. Also, threaded holes should be larger than 2-56 inches.
- Make Use of Standard Drill Sizes
CNC machines can use drill bits to manufacture holes fast and efficiently if you prepare ahead and make sure the holes in your product are standard size. Non-standard sizes, on the other hand, frequently necessitate the use of an end mill tool, which can add to the cost. The depth of the holes has an impact as well; while holes as deep as 10 times the diameter can be made, they are difficult to machine and will cost more.
If you have a hole diameter of up to 10 millimetres, plan it in 0.1 millimetre increments to save money on CNC machining. Use a 0.5-millimeter increment for everything over 10 millimetres. If you're working in inches, utilise fractions of an inch and refer to the fractional-inch drill bit sizes. Regardless of hole size, make sure the hole's length does not exceed four times the diameter.
- Multiple finishes should be avoided
The finish on your CNC machined object protects it from the elements while also improving its look. Regrettably, it also raises the price. Taking it a step further and requesting various finishes on a single product raises the price even further.
Consider going with the as-machined finish for the entire piece if you want to save money. Only request numerous finishes if you require them.
- Complex parts should be split
If your part has sophisticated geometries, rotating or repositioning is necessary, you'll most likely need a bespoke fixture, manual rotation, repositioning, or a multi-axis CNC system to machine it. All of this is not free.
If you can't reduce the complexity of your product any further, you might be able to save money on CNC machining by separating it into two or more independent machined sections that can be joined to create the part you need. You're more likely to save money if you break the part down into two or more geometries that can be machined in a single setup.
- Small Features with a High Aspect Ratio Should Be Avoided
Extreme width-to-depth ratio items are notoriously difficult to manufacture. Small features with a high width-to-height aspect ratio, for example, are difficult to machine because they are susceptible to vibrations. If something is difficult to mill, it raises the cost, as it does with many other aspects of machining.
Design all features with a width-to-height aspect ratio of less than four to save money on CNC machining, and consider attaching them to a wall or adding brace support to improve stiffness.
- Place a larger order
The unit price is heavily influenced by the amount of pieces you order. When it comes to figuring out how to save costs, economies of scale can be a useful tool. Increasing the quantity from one to 50 could result in a unit price reduction of more than 50%.
When you place your next order, consider ordering a larger amount.

- Maintain a Simple Approach
Many of these suggestions for lowering CNC machining expenses have a common theme: simplicity. When designing a complex product, you'll almost certainly need specific equipment or fixtures, several machine configurations, or special materials, all of which will cost you extra money.
Ask yourself the following questions when you submit your next order for a quote to help you save money on CNC machining:
- Have I used the Designing for Machinability principles to optimize my part? If you don't already know, learn how to optimize part design for CNC machining.
- Are all of my part's features required for it to function properly?
- Is it possible to break the part into multiple, simpler parts for machining and assembly?
- Is it possible to switch to a material that is easier to machine while still meeting my requirements?
F.A.Q
Q: How much does CNC machining cost?
If a higher quantity of a CNC-machined product is produced, it will be less expensive. For example, suppose you're requested to create a product with a $500 machine setup cost. One product's raw material costs ten dollars.
The one will have a total machining cost of 510 dollars. However, if you need to create 50 identical parts, the per-part cost will be $20. The cost will drop as the number of required parts increases because machine setup costs will not change.
Q: What are the best ways to cut CNC machining costs?
The cost of CNC operations can be reduced by improving the design without compromising the product's overall functioning. It can be accomplished by adding radius to the part's internal vertical edges, limiting the depth of the cavities, increasing the thickness of the walls, properly limiting the length of the threads, optimising the tapped holes, splitting complicated parts into simpler separate parts, selecting only essential surface finishes, and reducing the number of machine setups for operations.
Summary
Before attempting to reduce the cost of the CNC machining process, we must first determine all of the factors that influence the cost of the CNC machining process. Once that is completed, we examine all of the many components that may contribute to lowering the cost of the CNC machining process.
CNC machinists spend a large amount of time acquiring and improving their skills. They can operate a variety of equipment and construct products using a variety of materials and techniques. Their versatility allows the industrial industry to grow, but it can also make determining costs difficult.
As a result, it's vital to understand all of the factors that can influence your spending. Before deciding on a final design, consult a group of experts because inaccurate information on models can result in parts being made multiple times. You may be able to save money by modifying or eliminating processes along the road.