Are you confident in the structural integrity of your high vacuum equipment? A welding defect called undercut could be silently compromising its strength.
Welding undercut is a groove or depression along the edge of a weld, where the base metal melts away but isn't filled by the filler metal. This weakens the joint and can lead to cracks, corrosion, and even equipment failure.
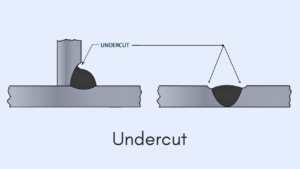
Don't let this hidden hazard jeopardize your operations. Let’s explore what welding undercut is, how it happens, and what you can do to prevent it from affecting your vacuum chambers and other critical components.
What is Welding Undercut?
Ever wondered why some welds seem to have a little "bite" taken out of the edge? That's likely an undercut, and it’s not a good sign.
Welding undercut is essentially a groove or notch that forms in the base metal next to the weld. It happens when the welding process melts the base metal, but the molten area isn't adequately filled in with filler metal. This leaves a depression that weakens the weld and makes it prone to failure.
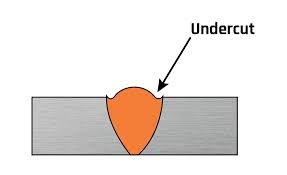
Think of it like this: you're building a wall with bricks (the weld), but you accidentally chip away some of the concrete foundation (the base metal) next to the wall. If you don't fill in those chips, you've created a weak spot. Undercut can occur as either an external or internal defect. External undercuts are visible on the surface and are easier to detect during inspection. Internal undercuts, on the other hand, are hidden within the weld itself and are much harder to spot, often requiring non-destructive testing methods like radiography or ultrasonic testing to identify them. Either way, if I find an undercut during my machining work, I know it's a serious issue that needs addressing to ensure the long-term reliability of your components.
How Does Undercut Occur? What Are the Common Causes?
So, what causes this unwanted groove to form in the first place? It's usually a combination of factors related to the welding process itself.
Undercut can occur due to excessive heat, which melts too much of the base metal. It can also be caused by moving too fast, not using enough filler metal, or holding the electrode at the wrong angle. Even a dampened electrode can lead to instability in the arc, resulting in undercut defects.
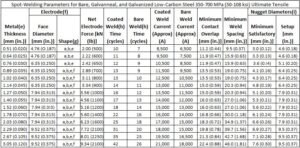
I've seen firsthand how different welding techniques and parameters can impact the final result. For instance, if the welding current or voltage is too high, it can overheat the base metal, causing it to melt faster than the filler metal can fill the gap. Similarly, an incorrect electrode angle can affect the distribution of heat and create uneven melting. The type of welding process also plays a role; undercut can occur in various methods like GMAW, GTAW, SMAW, and FCAW. The good news is that understanding these causes is the first step in preventing undercut and ensuring the quality of your welded components.
What Impact Does Undercut Have on Your Products?
Why is undercut such a big deal? Because it can seriously compromise the integrity and performance of your welded products.
The primary danger of undercutting is that it reduces the load-bearing capacity of the joint. The groove creates stress concentration points, making the weld more susceptible to cracks and fractures. This can lead to premature failure of the component, especially under dynamic loads or in corrosive environments.

Think about a vacuum chamber, where the integrity of the welds is critical for maintaining pressure and preventing leaks. An undercut can be a starting point for cracks that eventually propagate through the weld, leading to a catastrophic failure. Similarly, in sailboat parts or automotive components, where welds are subjected to constant stress and vibration, an undercut can significantly reduce their lifespan and reliability. That's why it's so important to address even small undercuts during the manufacturing process, to avoid potentially costly and dangerous consequences down the line.
How to Detect Welding Undercut? What Reliable Methods Are Available?
Okay, so how do you know if your welds have undercut? Fortunately, there are several methods available for detection, ranging from simple visual inspection to advanced non-destructive testing.
The easiest way to detect external undercut is by visual inspection. Look for a groove or depression along the edge of the weld. For internal undercuts, or when a more detailed assessment is needed, methods like radiographic (X-ray) or ultrasonic testing can be used to reveal hidden defects.
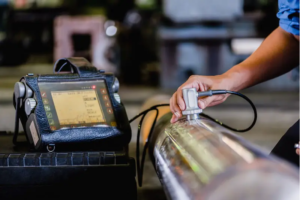
I always emphasize the importance of thorough inspection when we machine-weld parts. While a simple visual check can catch obvious external undercuts, it won't reveal any hidden internal defects. That's where non-destructive testing (NDT) comes in. Radiographic testing, for example, uses X-rays to create an image of the weld's internal structure, allowing us to identify any undercuts or other flaws that might be lurking beneath the surface. Ultrasonic testing, on the other hand, uses sound waves to detect defects based on how they reflect or refract the waves. By combining visual inspection with NDT methods, I can provide a comprehensive assessment of weld quality and ensure that your components meet the required standards.
How to Prevent Welding Undercut?
The best way to deal with undercut is to prevent it from happening in the first place. This requires careful control of the welding process and attention to detail.
To prevent undercut, use the correct welding parameters (current, voltage, travel speed), maintain a proper electrode angle, and ensure adequate filler metal deposition. Proper joint preparation, clean welding surfaces, and the right choice of electrode and shielding gas are also crucial.
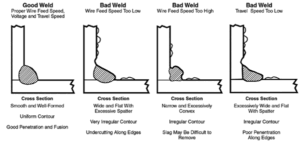
I've learned that preventing undercut is all about precision and control. It starts with selecting the right welding process and parameters for the specific material, thickness, and joint design. 7 2 For example, when welding thin sheets, it's essential to use lower heat input and faster travel speeds to avoid excessive melting and undercut. Similarly, the electrode angle should be carefully maintained to ensure uniform heat distribution and proper filler metal deposition. 7 And don't forget about proper joint preparation – cleaning the welding surfaces and ensuring a good fit-up can go a long way in preventing undercut and other defects.
Conclusion
Welding undercut is a serious defect that can compromise the structural integrity of your high vacuum equipment. By understanding the causes, implementing proper prevention techniques, and using reliable detection methods, you can minimize the risk of undercut and ensure the long-term performance of your critical components.