Are you confused regarding which service to choose? laser cutting versus CNC cutting? Don't Worry most businesses and manufacturing firms, when they decide to adopt advanced technology, are a little hesitant about which service is the most reliable, efficient, economical, and provides better finishing.
Both CNC and laser cutting are ideal for reliability, able to manufacture the most intricate components with little material wastage and mass production with dazzling finishing, but still, they have certain technical variations in operation, optimal performances, and in much more dimensions. A contract-based manufacturing method, CNC machining involves interacting with the workpiece to cut the material. It is perfect for cutting with extreme precision, particularly on curved and grooved surfaces.

On the other hand, laser cutting uses a high heated beam to cut the surfaces without any contact, and it is mostly used where we need to cut tough and high strength ratio material. As this process is a little bit more expensive than ordinary CNC cutting, it gives excellent surface finishing and high tolerance.
As both the processes have specific pros and cons so one should be well aware of its requirements to choose the best one, At Baichuan we have highly qualified and expert engineers and Machinist who are available around the clock to assist you, you can get in touch with us to get a consultation regarding your product requirements, we will assist you in guiding proper material, optimal technology, machining process and cad designs which will be ideal for you in quality, precision, and budget.
What Is CNC Cutting:
Computer numerical control machines are dedicated to producing various parts and complex designs of different materials and shapes. The process starts with designing a 3-D model of the required part with the help of modern designing software, like AutoCAD, solid works, or Creo. This has to be done by an expert engineering draftsman as dimensions and details are necessary for the next step which is to write its G-code.
The G-code of the part is generated by the CNC programmer, which is a command of CNC machining. After that, the process is set to go, and the machine interprets the design after a specific time.

CNC Cutting Tools:
As the CNC machining process is a contact base process, it needs specific tools for appropriate materials, tool decision mainly depends upon the material of the workpiece, its ductility, and hardness, secondly, the depths of grooves and cuts are also deciding factors in it. The tool directly affects the feed rate, spindle speed, and the chip size removed during contact friction, some properties which an ideal tool has for an appropriate contact and finishing.
- Thermal resistivity
- Highly resistive to wear and tear
- Chemically inert
- Must be harder stable and non-ductile.
Ceramics:
Ceramics are typically hard, low ductile, and nonreactive, that is why ceramic tools are mostly used for better surface finishing. They are mostly used when we have to deal with cast iron alloys.
Carbon Steel:
Carbon steel contains 0.9 % carbon and 1 % manganese and it is hardened up to 62 RC, that's why it is mostly used during working with aluminium sheets and woodworking, carbon steel shows low-temperature resistant properties, and it starts softening at 1800 degrees.
Cemented Carbide
Cemented carbide tools are made up of tantalum and tungsten with cobalt as a binder, they can bear temperatures up to 900 degrees. These tools are very hard and give an excellent surface finish.
High-Speed Steel (HSS):
HSS is mostly used to produce complex parts and grooves, like for automobiles, gears, dyes, taps, and reamers, they start softening at 600 degrees, and it is widely used in the machining process, they are mostly coated with some other material to improve their resistivity, and thermal conductivity.
Pros of using CNC Cutting:
As CNC cutting is whey cheaper than other machining processes, that is why most industries are equipped with CNC machines, which include, drilling, routing, milling, and boring processes. They can machine all types of metallic components and other materials as well, with a variety of designs and complexities.

Here are a few pros of using CNC cutting.
- CNC machines are operated through particular software, that's why they ensure minimum material wastage.
- Highly precise parts with complex designs can be obtained through CNC machines, as no human interaction is needed in its process so one can achieve high tolerance and precision.
- One can increase its feed rate to achieve mass production in less time.
- CNC machines are helpful in reducing power consumption so they are ideal for
Cost reduction.
Applications of CNC Cutting:
Most industries especially small units are preferring CNC cutting due to its low setup and working cost. In-depth grooves and 3D model structures are some things for which
CNC cutting is ideal. For those reasons, it found its applications in
- Automobile manufacturing
- Sheet metal working shops
- Dental industry.
- Die and moulding.
- Weapon industry.
- Agriculture tools and machinery.
What Is CNC Laser cutting?
CNC laser cutting uses a high-energy light beam to cut out the material, this high-energy beam is electronically programmed as per the required design, The system consists of CNC programmable machinery, an optical system, and an assistance gas, that helps in targeting the beam. CNC laser cutting is a contactless process, no physical interaction between workpiece and tool is present.
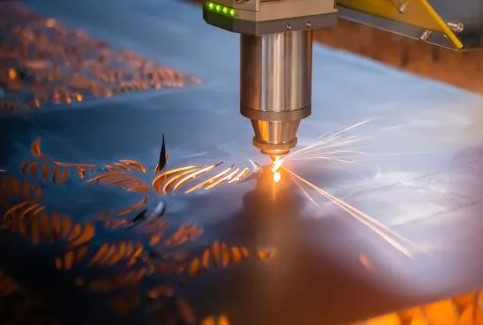
The process starts by coding the laser emitting jet as per desired dimensions, The laser beam is operated through a motion control system the high-temperature laser beam cut, melts, and vaporize the material to give a smooth surface finishing and a perfect shape of high precision.
How lens affects the Laser cut:
The lase cut, and its efficiency depends upon the strength of the laser beam, the diameter of the targeted spot, and the depth cut of the beam. For those conditions, the lens plays a lot of important roles, the Focal length and in-depth focus of the lens must be appropriate for the desired result.
The focal length is the distance from the center of the lens to its principal focus, and the depth of focus is the distance at which we achieve an appropriate cut. For an effective cut one has to reduce the focal length of the lens to achieve a small focus spot and in-depth cut.
The general requirement of cutting is as follows.
- Small focus spot for effective precision and tolerance.
- The long in-depth focus of the beam for effective cutting.
Sheet metal laser cutting types:
Depending upon the working procedure and laser type, the CNC laser machines come in three different variants.
CO2 Laser:
This type of CNC cutting is used for working with thicker metals, especially for wood working and engravings. The Laser beam is produced by passing electricity through a pipe containing carbon dioxide, helium, and nitrogen.
- These laser beams are most suitable for cutting thicker sheets.
- Through a flying optics system, one can rotate a laser beam to the x-y axis for various angle cuttings.
Fiber Laser:
Laser diodes are used to produce a fiber laser beam, the beam is then transferred through optical fiber, from where it gets strength and efficiency is increased multiple times, The high-power beam is then focused on the workpiece with the help of the optical glasses, like a concave lens. Fiberglass is whey better than ordinary CO2 resonators in multiple ways.
- Conventional CO2 resonator has multiple moving parts, for its various operations like gas circulation, and light-generating beam, whereas in fiberglass beam we don’t have to bother for all these. So, its maintenance cost is reduced as compared to the CO2 resonator.
- Fiberglass beams are most suitable for cutting reflective material sheets, as these sheets may damage the machinery in other techniques, due to reflection caused by them, so fiber is suitable for cutting, brass, aluminium, and copper sheets.
THE ND:
It is also known as the YAG laser, it is the most powerful laser cutting technique, it used ND-Yag crystals to amplify the power of the beam, and it is used for highly precise drilling, cutting, boring, and engraving. Due to its high price tag, it is not commonly used.
Pros of Laser Cutting
Precision & high accuracy: Laser cutting is known for its high precision and accuracy, The highly targeted laser beam can produce the finest cuts with great surface finishing, The laser can produce up to 0.005 inches cut which produces the finest details.
Low Power Consumption: with fewer moving parts and no pre-machining and after-machining processes, laser cutting is ideal for low power consumption, which reduces the overall manufacturing cost.
Less wastage: Laser cutting uses a targeted beam for cutting, so it causes less wastage and reduces the overall cost.
Bulk production: Most industries need bulk production within the minimum time, laser cutting has excellent cost-effectiveness in bulk production, as it doesn't require any pre-machining process like clumping and after machining like surface finishing so it produces the target without any interruption.
Lower Maintenance and Repair Costs: Laser-cutting machinery has fewer moving parts so its maintenance cost is a little bit cheaper as compared to ordinary CNC machines.
Applications Of Laser Cutting:
Precision, low lead time, less wastage, low power consumption, ability to design most complex parts, and thicker parts are something that makes laser cutting quite popular these days. Several manufacturing industries are preferring some of them listed.
- Automobile
- Aerospace
- Die, mould, and tooling industry ● Medical industry.
- Ceramic industry
- Jewellery manufacturing
- Architectural, household products.

Differences between CNC Cutting and Laser Cutting:
Intricate Designs:
Intricate designs and complex geometries are ideal for laser cutting, it gives smooth surface finishing along with highly precise grooves and corners, The laser beam can cut up to 0.01 mm radius cut, while CNC cutting is only restricted to 0.5mm/0.08 inches radius cut. Moreover, laser cutting also reduces material wastage which affects the overall cost directly.
High speed:
High speed and bulk production is something which is the necessity of the modern world, high precision, excellent surface finishing, and smooth edges, surely reduce the after-machining cost and time, Furthermore no need for clamping and after-matching formalities in laser cutting make it an ideal and quickest machining process.
Processing Cost:
NO after machining processes, low material wastage, and no clamping with high precision and tolerance make the laser beam effective for industries, but still set up and machining cost of laser cutting is a little bit high than ordinary CNC cutting.
Surface fining:
Accidental markings, poor finishing, and material wastage are something one has to face during CNC cutting, on the other hand, laser cutting is free from any marks, or after machining services, that’s why laser beams are mostly used in those industries where one has to focus on quality and precision, like in aerospace and shipbuilding and automobile industries.

Nowadays most industries prefer to use Laser cutting, due to its time-saving and bulk production benefits, and high precision benefit, but still, laser cutting can only be used in specific industries due to its setup and machinery cost. Most local industries still use CNC cutting. CNC cutting has its benefits, as it is ideal for high thickness and deepest grooves, and it is ideal for the production of 3D model structures where one needs 3d curves and grooves, Moreover CNC machines are more durable and they have a good life span than laser cutting machines.
Both the process have their pros and cons, if you are still confused about whom to choose and which service is best for your particular case, you can contact us any time. At Baichuan our experienced engineers and machinist are always available to assist you. We are the leading CNC and laser cutting service provider in China, having millions of satisfied customers all over the globe.