Every defective mechanical part creates potential danger. In our facility, we've seen catastrophic failures that could have been prevented with proper inspection methods like penetrant testing.
Penetrant testing is a non-destructive testing method that reveals surface defects invisible to the naked eye. By applying liquid penetrants to parts, waiting for absorption into cracks, and then applying developers, even microscopic flaws become clearly visible, ensuring part integrity and safety.

Penetrant testing process showing fluorescent dye highlighting surface defects
When we first implemented penetrant testing in our CNC machining operations, the results were eye-opening. Components that appeared flawless under visual inspection revealed hidden defects that could have led to premature failures. This inspection technique has become indispensable for ensuring safety across numerous industries.
Why is Penetrant Testing Critical for Quality Control of Mechanical Parts?
After a major customer returned a batch of precision parts, we discovered the hard way that invisible defects can cost more than just money. Surface cracks had developed during machining, but went undetected without proper testing.
Penetrant testing detects microscopic flaws by exploiting capillary action, where liquid penetrant seeps into surface discontinuities. After applying a developer, these flaws become highly visible, even those as small as 0.001 inches in length. This method works with virtually any non-porous material, including metals, ceramics, and certain polymers.
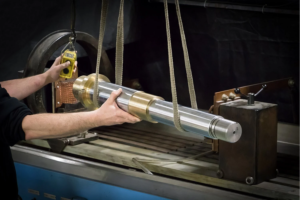
CNC machined components undergoing penetrant testing inspection
Dive deeper into penetrant testing, and you'll discover it's more than just a quality control measure—it's preventative medicine for your mechanical components. In our machining operations, we've integrated it as a critical checkpoint before parts move to final assembly or shipment.
The process itself follows a systematic protocol: first, thorough cleaning removes contaminants that could mask defects. Next, we apply the penetrant solution—either visible dye (typically bright red) for standard inspections or fluorescent dye for enhanced detection capabilities under UV light. After allowing sufficient dwell time (typically 10-30 minutes), excess penetrant is carefully removed, and developer is applied to draw the penetrant from defects, creating visible indications.
For critical components like vacuum chambers that we produce, we often use fluorescent penetrants, which provide superior sensitivity. Under UV light, even the smallest defects glow brightly against the dark background, allowing our inspectors to detect flaws that could compromise vacuum integrity. This level of detection is impossible with visual inspection alone and provides crucial quality assurance for high-stakes applications.
Penetrant Type | Best Application | Detection Capability | Cost Factor |
---|---|---|---|
Visible Dye | General inspection, field work | Good (>0.001") | Low |
Fluorescent | Critical components, precision parts | Excellent (>0.0005") | Medium |
Water-Washable | Environmental concerns, bulk processing | Good | Medium |
Post-Emulsifiable | The highest sensitivity needs | Superior | High |
How to Choose the Right Penetrant Testing Solution for Your Industry?
When a medical device manufacturer approached us about machining critical components, they were concerned about microfractures. Traditional inspection methods weren't sufficient, and failures could mean life or death for patients.
Selecting the right penetrant testing solution depends on your specific industry requirements, material types, and defect sensitivity needs. For aerospace or medical components, fluorescent penetrants with Level 4 sensitivity (highest) are often mandatory, while automotive parts might only require Level 2 or 3 sensitivity with visible dye penetrants.
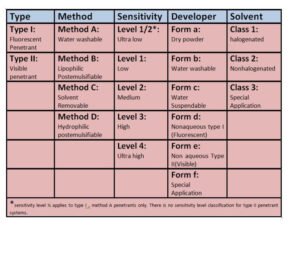
Comparison of penetrant testing methods for different industrial applications
The penetrant testing landscape offers various options tailored to specific industry needs, something we've learned through years of providing precision machining services. For our automotive clients, we often recommend water-washable penetrants that balance detection capability with processing efficiency and environmental considerations. Meanwhile, our aerospace customers typically require post-emulsifiable fluorescent penetrants that offer the highest sensitivity levels.
Material compatibility is another crucial consideration. When testing aluminum components for sailboats, we select penetrants specifically formulated to avoid chemical attack on sensitive alloys. With high-value stainless steel vacuum chamber components, we use methods that won't leave residues that could compromise vacuum integrity.
The testing environment also dictates your choice. In our controlled factory setting, we can utilize sophisticated systems with automated processing lines and UV inspection chambers. However, when we need to conduct field inspections at customer sites, we opt for portable visible dye kits that require minimal equipment but still provide reliable results.
Industry | Recommended Penetrant Type | Sensitivity Level | Key Considerations |
---|---|---|---|
Aerospace | Fluorescent, Post-Emulsifiable | Level 3-4 | Highest defect detection, regulatory compliance |
Automotive | Visible or Fluorescent, Water-Washable | Level 2-3 | Production volume, cost efficiency |
Medical | Fluorescent, Low-Residue | Level 3-4 | Biocompatibility, cleanliness |
Marine | Visible, Water-Washable | Level 2-3 | Corrosion resistance, field application |
Semiconductor | Fluorescent, Ultra-Low Sulfur/Halogen | Level 3-4 | Contamination prevention, precision |
Have Your Competitors Already Adopted This Advanced Inspection Technology?
When we lost a major contract to a competitor, we investigated why. The answer was unsettling: they guaranteed defect-free parts through comprehensive penetrant testing while we relied on sampling and visual inspection.
Industry surveys indicate that over 85% of medium to large precision machining operations now employ penetrant testing as standard practice. Companies without this capability increasingly find themselves excluded from high-value contracts in aerospace, medical, and defense sectors where zero-defect requirements are non-negotiable.
Modern CNC machining facility with integrated penetrant testing station
The widespread adoption of penetrant testing has created a clear competitive divide in the precision manufacturing industry. From our perspective as a Chinese CNC machining facility competing globally, we've observed this technology transition from being a differentiator to becoming an entry-level requirement for certain market segments.
Five years ago, when we first invested in our comprehensive penetrant testing capability, less than 50% of our regional competitors offered this service. Today, virtually all serious contenders in high-precision manufacturing have some form of penetrant testing capability. However, the sophistication of these systems varies dramatically, creating different competitive tiers.
Basic operations typically offer simple visible dye testing with manual processing, sufficient for non-critical components. Mid-tier competitors have adopted fluorescent penetrant systems with semi-automated processing lines. The market leaders—where we position ourselves—maintain fully automated systems with computerized documentation, traceability, and statistical process control integration.
This technology adoption curve extends across industries. In automotive manufacturing, penetrant testing has become standard for critical safety components like steering and brake systems. For semiconductor equipment parts we produce, customers now routinely specify penetrant testing protocols in their purchase requirements, often with detailed procedures that must be followed precisely.
Competitive Position | Penetrant Testing Capability | Market Access | Client Perception |
---|---|---|---|
Market Leader | Automated fluorescent systems with digital documentation | All sectors, including aerospace, medical | Premium quality provider |
Mid-Market | Semi-automated fluorescent systems | Most industrial sectors | Quality-conscious supplier |
Basic Provider | Manual visible dye process | Limited to less critical applications | Budget option |
No Capability | Visual inspection only | Increasingly restricted to non-critical parts | Perceived quality risk |
What Specific Economic Returns Can Investment in Penetrant Testing Bring You?
After a costly recall due to failed components, we calculated the true price of inadequate testing. The direct costs were considerable, but the damage to our reputation nearly sank our business division.
Implementing penetrant testing typically reduces defect escape rates by 75-95% compared to visual inspection alone. For a mid-sized manufacturing operation, this can translate to annual savings of $50,000-$200,000 in rework, warranty claims, and recall costs, while opening access to premium contracts with higher profit margins.
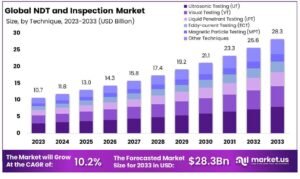
Economic impact analysis of penetrant testing on manufacturing operations
The economic case for penetrant testing extends far beyond simple defect prevention—it fundamentally transforms your business positioning and profitability structure. When we upgraded our penetrant testing capabilities last year, we conducted a comprehensive cost-benefit analysis that revealed multiple layers of economic return.
The most immediate benefit came from defect detection at the earliest possible stage. Finding flaws before additional machining operations prevents wasting expensive machine time on parts that would ultimately be scrapped. For complex vacuum chamber components that undergo multiple machining operations, this early detection saved us approximately $85,000 in the first year alone.
Customer retention and contract expansion represented an even larger economic impact. By guaranteeing certified penetrant testing results, we secured a three-year contract with a premium medical equipment manufacturer that had previously distributed their orders among multiple suppliers. The increased business volume improved our operational efficiency through economies of scale, reducing per-unit costs by approximately 12%.
The ability to charge premium prices for verified quality represents another significant economic advantage. Our parts that undergo certified penetrant testing command prices 15-20% higher than similar parts without this verification, reflecting the reduced risk and higher value to customers. This premium pricing structure has increased our overall profit margin by approximately 8% across tested product lines.
Economic Benefit | Typical First-Year Return | Long-Term Value |
---|---|---|
Reduced scrap/rework | $30,000-$100,000 | Consistent production efficiency |
Warranty claim reduction | $20,000-$80,000 | Enhanced brand reputation |
Access to premium contracts | $50,000-$500,000 | Stable business growth |
Premium pricing opportunity | 10-20% increased margins | Market differentiation |
Reduced liability risk | Variable (potential savings of millions) | Business stability and insurability |
Conclusion
Penetrant testing isn't just another quality control method—it's essential insurance for your mechanical parts and business reputation. By implementing this proven technology, you'll detect invisible threats, meet industry standards, and ultimately deliver superior products to your customers.