Imagine making parts, only to find they break easily. What if a car part fails, causing an accident? Material testing helps avoid these disasters.
Material testing is all about checking if materials are strong and safe. For CNC machining, this is super important because we want to make sure the parts we create meet specific standards and will last.
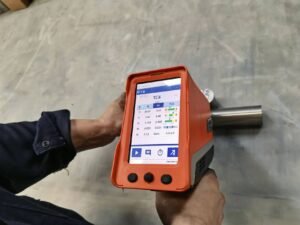
So, material testing matters a lot in CNC machining. Let's dive into why.
What Material Properties Do We Test in CNC Machining?
Ever wonder what makes one metal different from another? If you're thinking about how to ensure your CNC machined parts meet design specifications, you might also wonder if you're testing for the right qualities.
We test many things, such as how strong the material is, how hard it is, and how well it handles stress. These tests tell us if the material is right for the job.
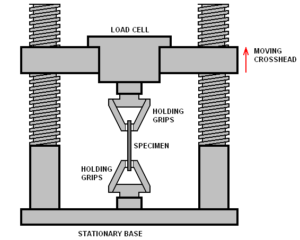
When it comes to CNC machining, we focus on several key material properties to ensure the final product meets the required specifications. Here’s a breakdown of what we test and why it matters:
Property | Description | Importance of CNC Machining |
---|---|---|
Tensile Strength | Measures how much stress a material can withstand before breaking when pulled. | Critical for parts that will be under tension or pulling forces, such as bolts or cables. Ensures the part can handle the load without failing. |
Yield Strength | Indicates the amount of stress a material can endure before it starts to deform permanently. | Important for parts that need to maintain their shape under stress, like gears or structural components. Helps prevent bending or deformation during use. |
Hardness | Measures a material's resistance to localized plastic deformation caused by indentation or scratching. | Essential for parts that need to resist wear and abrasion, such as cutting tools or bearings. Ensures a longer lifespan and consistent performance. |
Fatigue Strength | Determines a material's ability to withstand repeated cycles of stress without failing. | Crucial for parts subjected to cyclical loading, such as connecting rods in engines or suspension components. Prevents unexpected failures due to fatigue cracks. |
Impact Strength | Measures a material's resistance to sudden, high-energy impacts. | Important for parts that may experience sudden shocks or impacts, such as safety guards or housings. Ensures the part can absorb energy without shattering. |
Knowing these properties helps us choose the right material. This way, we can make sure our CNC parts work well and last long.
Why is Material Testing Crucial for High-Precision CNC Parts?
Imagine building a complex machine and using unreliable parts. That would be a disaster. Material testing gives us peace of mind.
Material testing makes sure that every part meets the exact standards we need. This is super important for high-precision CNC parts, where even small mistakes can cause big problems.
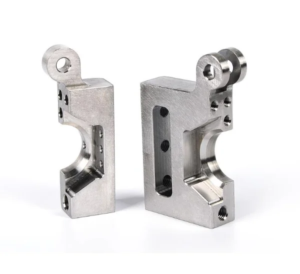
Precision CNC parts
For high-precision CNC parts, material testing isn't just a good idea; it's essential. Here's why:
- Ensuring Accuracy: CNC machining is all about precision. If the material doesn't behave as expected, the final part won't meet the required dimensions. Material testing verifies that the material properties align with the design specifications, guaranteeing accuracy.
- Preventing Failures: High-precision parts often operate under demanding conditions. Without proper material testing, there's a risk of premature failure, leading to costly downtime and potential safety hazards. Testing identifies weaknesses and ensures the material can withstand the intended stress.
- Maintaining Consistency: Batch-to-batch variations in material properties can affect the performance of CNC parts. Material testing helps maintain consistency by verifying that each batch meets the required standards.
- Meeting Industry Standards: Many industries have strict regulations regarding material properties. Material testing ensures compliance with these standards, avoiding legal and financial repercussions.
- Optimizing Performance: Understanding the material's properties allows us to optimize the machining process. This can lead to improved efficiency, reduced waste, and enhanced part performance.
So, you see, material testing is not an option, but a must-have for high-precision CNC parts.
What Are the Different Types of Material Testing Methods?
Have you ever wondered how we check if metal is strong enough? Different tests show us different things about a material.
There are many ways to test materials, like pulling them apart (tensile testing) or hitting them (impact testing). Each test helps us understand how the material will act under different conditions.
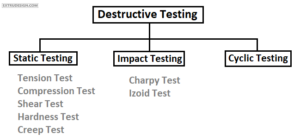
Material testing methods can be broadly classified into destructive and non-destructive techniques. Here’s an overview of some common methods used in CNC machining:
Destructive Testing:
- Tensile Testing: This test measures a material's resistance to being pulled apart. A sample is subjected to a controlled tension until it fails, providing data on tensile strength, yield strength, and elongation.
- Hardness Testing: This test measures a material's resistance to indentation. Common methods include Rockwell, Vickers, and Brinell hardness tests.
- Impact Testing: This test measures a material's ability to withstand sudden impacts. A standard specimen is struck with a known force, and the energy absorbed is measured.
- Fatigue Testing: This test measures a material's ability to withstand repeated cycles of stress. A sample is subjected to cyclic loading until it fails, providing data on fatigue life.
Non-Destructive Testing (NDT):
- Visual Inspection: A basic but important method involving a thorough visual examination of the material for surface defects.
- Ultrasonic Testing: This method uses high-frequency sound waves to detect internal flaws in the material.
- Radiographic Testing: This method uses X-rays or gamma rays to inspect the internal structure of the material.
- Magnetic Particle Testing: This method is used to detect surface and near-surface flaws in ferromagnetic materials.
- Dye Penetrant Testing: This method is used to detect surface cracks and other discontinuities by applying a dye to the material's surface.
Each testing method provides valuable insights into material properties. We use these insights to make sure our CNC parts are safe and effective.
How Do We Ensure Material Quality in Our CNC Machining Processes?
Imagine starting a project with the wrong materials. It would waste time and money. We need to be careful about quality.
We make sure materials are good by testing them before, during, and after machining. This helps us catch any problems early and make sure the final product is top-notch.
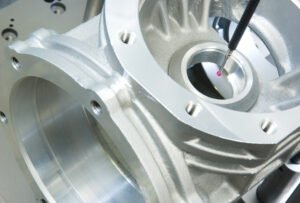
Quality control in CNC machining
Ensuring material quality in CNC machining is a multi-faceted process that involves several key steps:
- Material Selection: We carefully select materials based on the specific requirements of the part. This includes considering factors like strength, hardness, corrosion resistance, and machinability.
- Supplier Qualification: We work with trusted suppliers who can provide materials that meet our strict quality standards. We assess their quality control processes and track their performance over time.
- Incoming Inspection: We inspect all incoming materials to verify that they meet the specified requirements. This includes visual inspection, dimensional checks, and material testing.
- Process Control: We monitor the CNC machining process closely to ensure that it is stable and consistent. This includes controlling factors like cutting speed, feed rate, and coolant flow.
- In-Process Inspection: We perform inspections during the machining process to catch any defects early on. This includes dimensional checks, surface finish inspections, and visual examinations.
- Final Inspection: We conduct a final inspection of the finished part to verify that it meets all requirements. This includes dimensional checks, material testing, and functional testing.
These steps help us maintain high standards. They make sure our CNC parts are reliable and meet our customers' needs.
Which Industries Benefit Most from Material Testing in CNC Machining?
Think about industries where safety is super important. Material testing is critical in these fields.
Industries like aerospace, automotive, and medical rely heavily on material testing. They need to ensure that their parts are safe, reliable, and perform as expected.
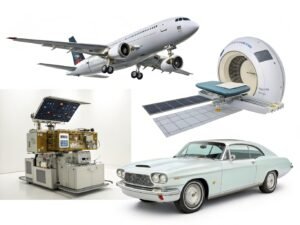
Aerospace, automotive, and medical industries
Material testing in CNC machining is crucial for various industries, each with its specific needs and challenges:
- Aerospace: In aerospace, the stakes are incredibly high. Material testing ensures that aircraft components can withstand extreme conditions, such as high altitudes, temperature variations, and stress. The tests help prevent failures that could have catastrophic consequences.
- Automotive: The automotive industry relies on material testing to ensure the safety and reliability of vehicles. From engine parts to suspension components, material testing helps identify potential weaknesses and ensure that parts can withstand the rigors of daily use.
- Medical: In the medical field, precision and reliability are paramount. Material testing is used to ensure that medical devices and implants are biocompatible, strong, and durable. This helps prevent infections, failures, and other complications.
- Industrial Machinery: Heavy machinery operates under extreme conditions and is subject to constant wear and tear. Material testing helps ensure that these machines can withstand the demands of their applications, preventing breakdowns and downtime.
- Energy: The energy sector, including oil and gas, relies on material testing to ensure the safety and reliability of equipment used in harsh environments. This helps prevent leaks, explosions, and other disasters.
Material testing supports safety and reliability in these important industries.
What Standards Govern Material Testing for CNC Machined Parts?
Imagine a world without rules. Material testing needs rules to be consistent.
Standards like ISO 9001 and ASTM International set the rules for material testing. Following these standards ensures that testing is done correctly and that results are reliable.
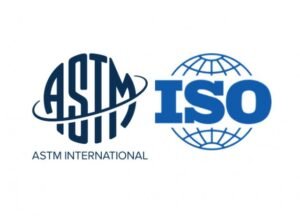
ISO 9001 and ASTM International
Material testing for CNC machined parts is governed by a range of international standards that ensure consistency, accuracy, and reliability. Here’s a look at some key standards:
- ISO 9001: This international standard specifies requirements for a quality management system (QMS). It helps organizations consistently provide products and services that meet customer and regulatory requirements.
- ASTM International: ASTM develops and publishes technical standards for a wide range of materials, products, systems, and services. These standards cover testing methods, specifications, and practices.
- EN Standards: European Norms (EN) are standards adopted by the European Committee for Standardization (CEN). They cover a wide range of industries and products, including material testing for CNC machined parts.
- MIL-STD: Military Standards (MIL-STD) are used by the U.S. Department of Defense to ensure the quality and reliability of products and materials used in military applications.
These standards help standardize material testing. They give customers confidence in the quality of CNC-machined parts.
How Much Does Material Testing Cost? A CNC Machining Perspective
Thinking about testing costs? It's an important part of making good products.
The cost of material testing depends on the type of test and how many tests you need. While it adds to the cost, it's an investment in quality and prevents bigger problems later.

Cost of material testing in CNC machining
From a CNC machining perspective, the cost of material testing is a critical consideration. Several factors influence the overall cost:
- Type of Test: Different testing methods have varying costs. Simple tests like visual inspection are relatively inexpensive, while more complex tests like tensile testing and fatigue testing are more costly.
- Sample Size: The number of samples required for testing affects the cost. Larger sample sizes provide more reliable results but also increase testing expenses.
- Testing Facility: The choice of testing facility can impact costs. Independent testing labs may charge more than in-house facilities, but they offer unbiased results.
- Industry Standards: Compliance with specific industry standards may require additional testing, which can add to the overall cost.
- Equipment and Labor: The cost of equipment and skilled labor needed to perform the tests also contributes to the overall expense.
We work to balance cost and quality. We test to prevent future problems.
What Mistakes Should Be Avoided When Choosing Materials for CNC Machining?
Choosing the wrong material can cause big problems. Knowing what to avoid is essential.
Avoid choosing materials that are too weak, too soft, or not right for the environment. Doing your research and testing materials can save you headaches later.
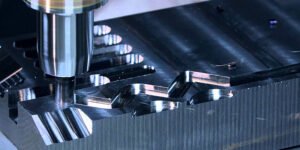
Common mistakes in choosing materials for CNC machining
Selecting the right material for CNC machining is crucial for ensuring the success of a project. Here are some common mistakes to avoid:
- Ignoring the Application: Failing to consider the end-use of the part is a major mistake. Materials should be chosen based on the specific requirements of the application, such as load, temperature, and environment.
- Overlooking Machinability: Some materials are more difficult to machine than others. Choosing a material that is hard to machine can increase production costs and lead to poor surface finishes.
- Ignoring Material Properties: Neglecting to consider key material properties like strength, hardness, and corrosion resistance can lead to premature failure.
- Failing to Test: Not testing the material before machining can result in unexpected problems. Material testing helps verify that the material meets the required specifications.
- Focusing Solely on Cost: Choosing the cheapest material without considering its suitability for the application can be a costly mistake in the long run.
- Not Considering Environmental Factors: Ignoring environmental factors like temperature, humidity, and exposure to chemicals can lead to corrosion and degradation of the material.
Avoiding these mistakes can lead to better outcomes.
Conclusion
Material testing is super important in CNC machining. It helps make sure parts are strong, safe, and reliable, and helps avoid big problems.